- お役立ち記事
- Utilizing Wearable Devices in Procurement and Purchasing Departments of Manufacturing: Monitoring Work and Enhancing Safety
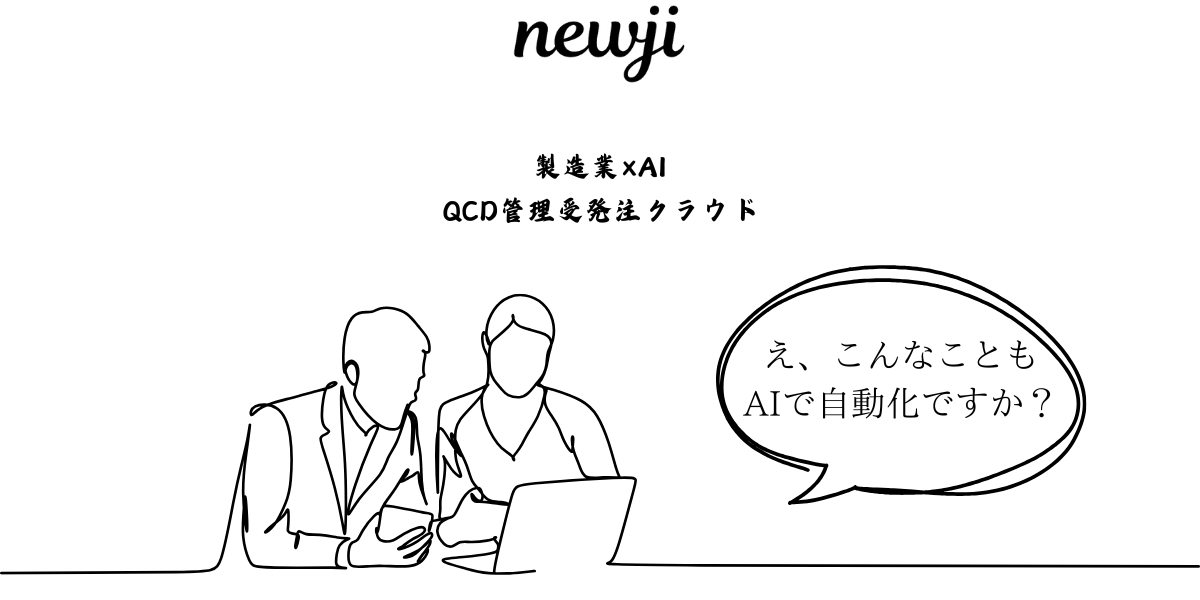
Utilizing Wearable Devices in Procurement and Purchasing Departments of Manufacturing: Monitoring Work and Enhancing Safety
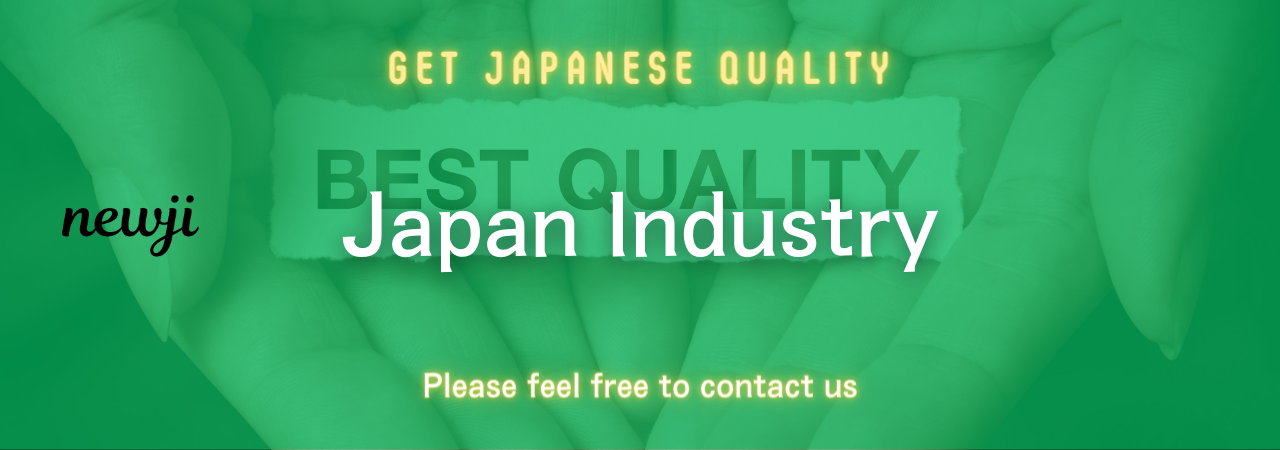
Wearable devices are becoming increasingly popular in various industries, including manufacturing.
In procurement and purchasing departments, these devices offer numerous benefits by monitoring work and enhancing safety.
Let’s explore how wearable technology can transform these departments, making them more efficient, safer, and smarter.
目次
Understanding Wearable Devices
Wearable devices are electronic gadgets that can be worn on the body.
They include smartwatches, fitness trackers, smart glasses, and location-based devices.
These tools gather data on the wearer’s physical activities, health metrics, and environmental conditions.
In the context of manufacturing procurement and purchasing, they perform specific functions to monitor work and promote safety.
Monitoring Work in Real-Time
One of the critical advantages of wearable devices in procurement is real-time monitoring.
Smartwatches and fitness trackers, for instance, can monitor employees’ movements and physical activities throughout the day.
This constant monitoring helps supervisors understand how efficiently tasks are being carried out on the shop floor.
By keeping track of activities, these devices ensure that workers are staying on task and working efficiently.
Any deviations from the daily tasks can be quickly noticed and addressed.
Enhanced Productivity
Wearable devices also contribute to productivity by providing real-time feedback to workers.
If a procurement officer is taking longer than usual to complete a task, a wearable device can alert them.
This immediate feedback helps workers stay on track and meet their deadlines.
Moreover, data collected over time can be analyzed to identify areas of improvement in workflows.
Managers can then take necessary actions to optimize these processes, ultimately boosting productivity.
Location Tracking
Location-based wearable devices allow for precise tracking of employees across the manufacturing floor.
This feature is particularly useful in large manufacturing facilities, where procurement and purchasing officers often need to move around.
With wearables, supervisors can track their location and ensure they are working in the correct areas.
In case of an emergency, knowing the precise location of employees can be crucial for prompt assistance.
Enhancing Safety In the Workplace
Safety is a paramount concern in any manufacturing setting.
Wearable devices bring several safety benefits to procurement and purchasing departments.
By closely monitoring workers’ health and the environment, these devices help mitigate risks and prevent accidents.
Health Monitoring
Many wearable devices come equipped with sensors that track vital signs such as heart rate, body temperature, and respiratory rate.
In a high-stress manufacturing environment, monitoring these health metrics is essential.
If a worker’s vital signs indicate they are under stress or unwell, supervisors can take immediate action to provide the necessary support.
This proactive approach to health monitoring can prevent incidents such as fatigue-related accidents.
Environmental Monitoring
Wearable devices can also track environmental conditions on the shop floor.
Factors such as air quality, temperature, and noise levels can significantly impact worker safety and comfort.
By monitoring these conditions, wearables help ensure that the work environment remains within safe limits.
If any parameters exceed these limits, immediate actions can be taken to rectify the situation, thus preventing potential hazards.
Emergency Alerts
In addition to health and environmental monitoring, wearable devices can send emergency alerts in critical situations.
For example, if a worker slips or falls, the device can immediately send an alert to supervisors with the exact location of the accident.
This enables quick response and assistance to the injured worker.
Such alerts can be lifesaving in severe accidents where every second counts.
Streamlining Procurement Processes
Beyond monitoring and safety, wearable devices can streamline various procurement processes in manufacturing.
They facilitate better communication, improve inventory tracking, and enhance decision-making.
Improved Communication
Smartwatches and other wearable devices enable instant communication between team members.
Procurement officers can send and receive messages without needing to access their phones or computers.
This seamless communication ensures that important information is shared promptly, and decisions are made quickly.
Better communication leads to more efficient procurement processes and reduces the chances of errors.
Enhanced Inventory Management
Wearables can also assist in inventory management.
By integrating wearable technology with inventory software, procurement officers can easily track stock levels and manage inventory in real-time.
For example, smart glasses with augmented reality capabilities can display vital inventory information directly in the user’s field of vision.
Such integration reduces manual errors and helps maintain accurate inventory records.
Data-Driven Decision Making
The data collected by wearable devices provides valuable insights into various aspects of procurement and purchasing.
By analyzing this data, managers can make informed decisions to enhance efficiency and safety.
For instance, data on workers’ productivity can help identify training needs, while health metrics can inform wellness programs.
The ability to make data-driven decisions ensures continuous improvement in procurement processes.
Challenges and Considerations
While wearable devices offer tremendous benefits, their implementation in procurement and purchasing departments comes with some challenges.
Addressing these considerations is crucial for successful adoption.
Privacy Concerns
One of the primary concerns with wearable devices is worker privacy.
Constant monitoring of physical activities and health metrics may be perceived as intrusive.
It is essential to communicate clearly with employees about how data will be used and to ensure that privacy is respected.
Establishing transparent policies and obtaining consent can alleviate privacy concerns.
Integration with Existing Systems
Integrating wearable devices with existing procurement and inventory management systems can be complex.
It is crucial to ensure that wearables seamlessly work with other tools and software.
Collaborating with technology providers and conducting thorough testing can help achieve effective integration.
Cost Considerations
Equipping an entire department with wearable devices can be costly.
It is important to weigh the benefits against the initial investment and ongoing maintenance costs.
However, the long-term advantages of enhanced productivity, safety, and efficiency often justify the expense.
The Future of Wearable Devices in Manufacturing Procurement
The adoption of wearable devices in procurement and purchasing departments is likely to grow as technology continues to advance.
With ongoing innovations, wearables will become even more versatile and powerful.
They will play a crucial role in creating smarter and safer manufacturing environments.
In the future, we can expect wearables to integrate with other emerging technologies, such as the Internet of Things (IoT) and artificial intelligence.
This integration will further enhance their capabilities and transform procurement processes.
Wearable devices offer numerous benefits for monitoring work and enhancing safety in manufacturing procurement and purchasing departments.
By leveraging real-time data, wearables contribute to increased productivity and better decision-making.
They also improve safety by monitoring health and environmental conditions and sending emergency alerts.
Despite some challenges, the long-term advantages make wearable technology a valuable investment for manufacturing companies.
Embracing these devices can pave the way for a more efficient, safe, and innovative future in procurement and purchasing.
資料ダウンロード
QCD調達購買管理クラウド「newji」は、調達購買部門で必要なQCD管理全てを備えた、現場特化型兼クラウド型の今世紀最高の購買管理システムとなります。
ユーザー登録
調達購買業務の効率化だけでなく、システムを導入することで、コスト削減や製品・資材のステータス可視化のほか、属人化していた購買情報の共有化による内部不正防止や統制にも役立ちます。
NEWJI DX
製造業に特化したデジタルトランスフォーメーション(DX)の実現を目指す請負開発型のコンサルティングサービスです。AI、iPaaS、および先端の技術を駆使して、製造プロセスの効率化、業務効率化、チームワーク強化、コスト削減、品質向上を実現します。このサービスは、製造業の課題を深く理解し、それに対する最適なデジタルソリューションを提供することで、企業が持続的な成長とイノベーションを達成できるようサポートします。
オンライン講座
製造業、主に購買・調達部門にお勤めの方々に向けた情報を配信しております。
新任の方やベテランの方、管理職を対象とした幅広いコンテンツをご用意しております。
お問い合わせ
コストダウンが利益に直結する術だと理解していても、なかなか前に進めることができない状況。そんな時は、newjiのコストダウン自動化機能で大きく利益貢献しよう!
(Β版非公開)