- お役立ち記事
- Various fracture phenomena, fracture surface analysis (fractography) technology
月間76,176名の
製造業ご担当者様が閲覧しています*
*2025年3月31日現在のGoogle Analyticsのデータより
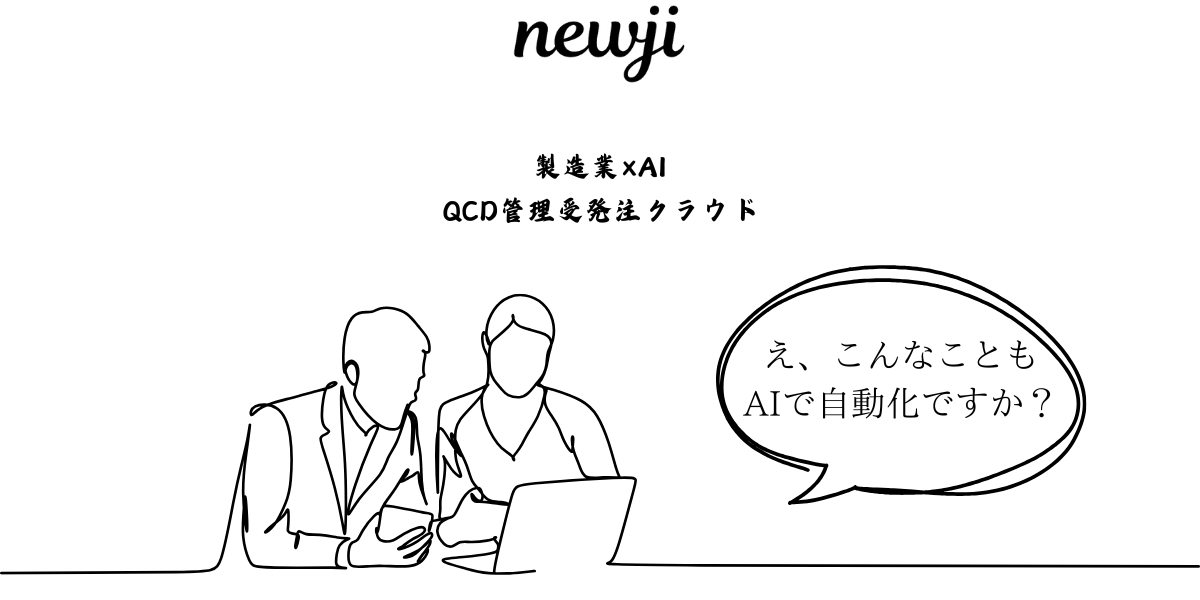
Various fracture phenomena, fracture surface analysis (fractography) technology
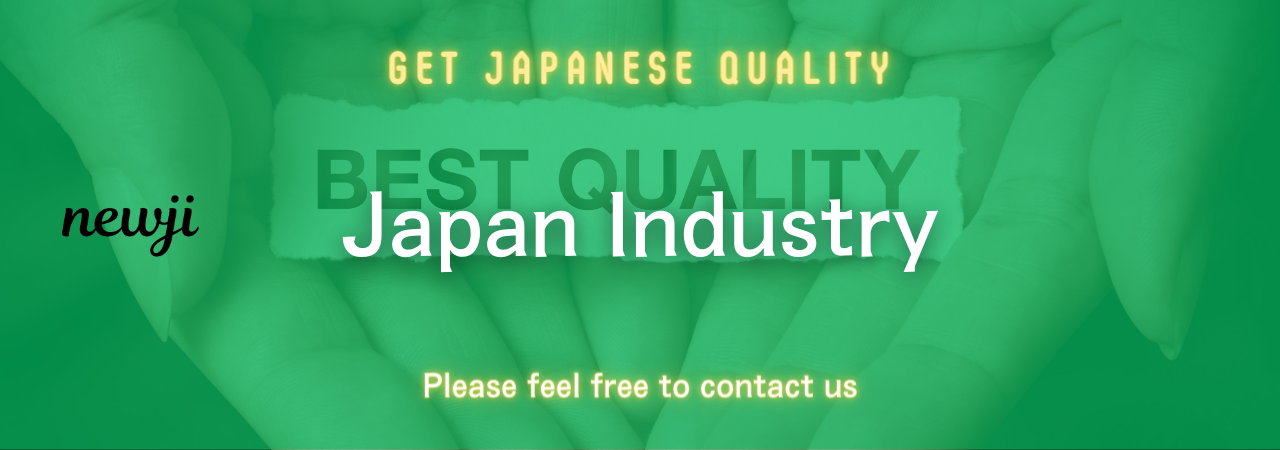
目次
Understanding Fracture Phenomena
Fractures are a universal phenomenon occurring across various fields, from engineering to geology and biology.
A fracture refers to the separation or breaking of a material into two or more pieces under the influence of stress.
Understanding fracture phenomena is crucial in preventing failures in structures, enhancing material strength, and ensuring safety in applications.
In scientific terms, analyzing fractures involves evaluating the forces and conditions that lead to a material’s failure.
When materials experience stress beyond their yield point, they tend to crack, and this cracking is essentially a fracture.
Fracture phenomena can be broadly classified into two categories: ductile and brittle fractures.
Ductile fractures occur when materials deform plastically before breaking, allowing time for detection and prevention.
On the other hand, brittle fractures happen suddenly without much prior deformation, making them dangerous.
Types of Fracture Surfaces
Examining fracture surfaces provides insights into the nature and circumstances of the fracture event.
The surface topography of a fractured material often reveals its mechanical history.
Three primary types of fracture surfaces include ductile fracture surfaces, brittle fracture surfaces, and fatigue fracture surfaces.
Ductile Fracture Surfaces
Ductile fracture surfaces display features that indicate significant plastic deformation before fracturing.
These surfaces often appear rough and irregular, with dimples that form as voids coalesce and grow under tension.
Ductile fractures are typical in metals, where visible necking and significant elongation precede failure.
The presence of dimpled surfaces suggests that the load was gradually increased until failure, offering clues about the material’s ductility.
Brittle Fracture Surfaces
Brittle fracture surfaces are typically flat and smooth, indicating a lack of plastic deformation.
The absence of surface irregularities suggests a rapid crack propagation through the material.
As a result, brittle fractures often occur with little to no warning, posing significant risks in structural applications.
The surface may display features like cleavage facets or river patterns, providing valuable information about the brittle nature of the fracture event.
Fatigue Fracture Surfaces
Fatigue fracture surfaces exhibit features that indicate repeated or cyclic loading that gradually leads to failure.
These surfaces display a characteristic pattern of striations or concentric ridges, indicating crack propagation over time.
The presence of fatigue striations is a testament to the progressive nature of fatigue fractures, which are prevalent in components subjected to cyclic stress.
Fractography: The Art of Fracture Surface Analysis
Fractography is a specialized field within material science dedicated to the study and analysis of fracture surfaces.
It combines both visual and microscopic techniques to interpret the causes and progression of fractures.
Fractography not only identifies the fracture type but also helps determine the root cause by revealing details invisible to the naked eye.
Macroscopic Examination
Macroscopic examination involves analyzing the fracture surface with unaided eyes or low magnification tools.
Large-scale features like overall shape, color variations, and crack initiation points are identified.
This step provides an initial assessment of the fracture type, offering insight into potential stress factors influencing the fracture event.
Microscopic Examination
Microscopic examination delves deeper into the fracture surface, using tools like scanning electron microscopes (SEM).
This analysis reveals finer details, including microvoids, grain boundaries, and secondary cracks.
By examining these features, engineers and scientists can determine the precise mechanisms of fracture, be it due to material defects or environmental factors.
Applications of Fractography
Fractography plays a pivotal role in various industries, from aerospace to automotive and construction.
In the aerospace industry, analyzing fracture surfaces from failed components can prevent future accidents by identifying material flaws or assembly errors.
In automotive applications, understanding fatigue fractures in engine components can lead to improved designs and enhanced longevity.
Likewise, in construction, identifying fracture origins in concrete or steel can bolster structural integrity.
Future Directions in Fracture Analysis
As technology advances, so does the field of fracture analysis.
New methodologies and tools are emerging, offering more detailed and accurate insights into fracture phenomena.
One such innovation is the use of digital image correlation (DIC), a technique that captures real-time strain data during material testing.
Artificial intelligence and machine learning are also being integrated into fractography, offering automated pattern recognition and predictive capabilities.
These technologies can potentially revolutionize the way fracture surfaces are analyzed, increasing efficiency and accuracy.
Understanding fracture phenomena and employing cutting-edge fractography techniques not only prevents catastrophic failures but also enhances the reliability of materials employed in critical applications.
This knowledge extends across industries, promising safer, more durable products for the future.
資料ダウンロード
QCD管理受発注クラウド「newji」は、受発注部門で必要なQCD管理全てを備えた、現場特化型兼クラウド型の今世紀最高の受発注管理システムとなります。
ユーザー登録
受発注業務の効率化だけでなく、システムを導入することで、コスト削減や製品・資材のステータス可視化のほか、属人化していた受発注情報の共有化による内部不正防止や統制にも役立ちます。
NEWJI DX
製造業に特化したデジタルトランスフォーメーション(DX)の実現を目指す請負開発型のコンサルティングサービスです。AI、iPaaS、および先端の技術を駆使して、製造プロセスの効率化、業務効率化、チームワーク強化、コスト削減、品質向上を実現します。このサービスは、製造業の課題を深く理解し、それに対する最適なデジタルソリューションを提供することで、企業が持続的な成長とイノベーションを達成できるようサポートします。
製造業ニュース解説
製造業、主に購買・調達部門にお勤めの方々に向けた情報を配信しております。
新任の方やベテランの方、管理職を対象とした幅広いコンテンツをご用意しております。
お問い合わせ
コストダウンが利益に直結する術だと理解していても、なかなか前に進めることができない状況。そんな時は、newjiのコストダウン自動化機能で大きく利益貢献しよう!
(β版非公開)