- お役立ち記事
- Vibration Control Design and Precision Control for Semiconductor Exposure Equipment
月間77,185名の
製造業ご担当者様が閲覧しています*
*2025年2月28日現在のGoogle Analyticsのデータより
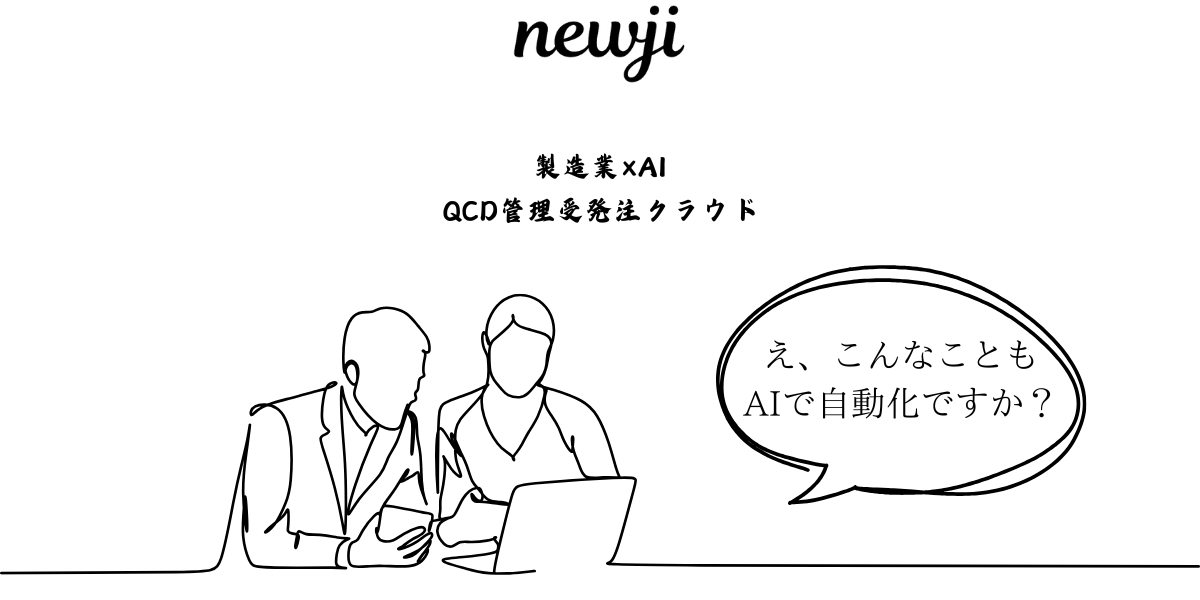
Vibration Control Design and Precision Control for Semiconductor Exposure Equipment
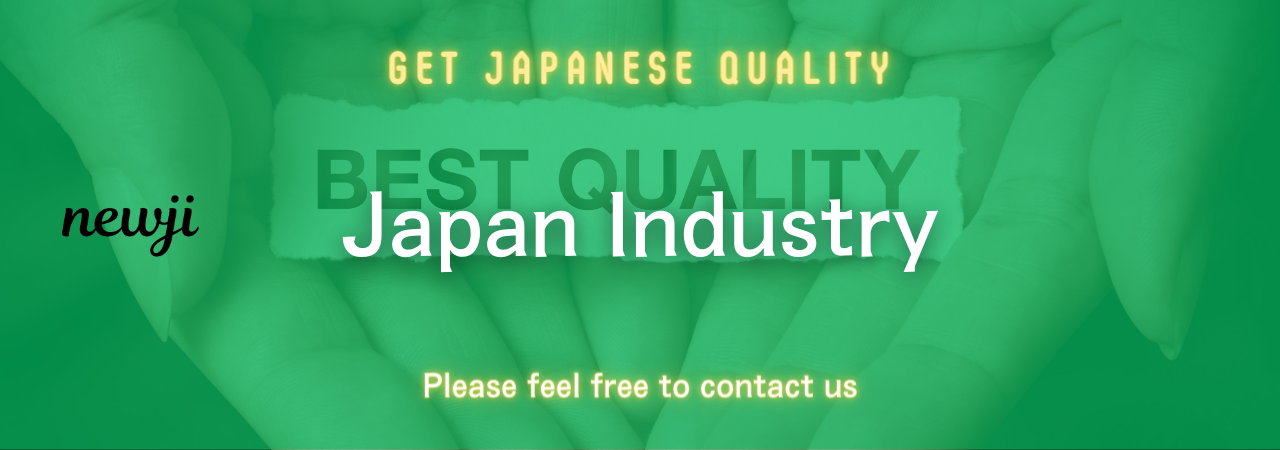
The semiconductor industry plays a critical role in modern technology, enabling the development of advanced electronic devices that power everything from smartphones to supercomputers.
One of the key components in semiconductor manufacturing is exposure equipment.
These sophisticated machines are responsible for accurately transferring circuit patterns onto silicon wafers.
To ensure precision and reliability, vibration control and precise control are paramount.
目次
Understanding Semiconductor Exposure Equipment
Semiconductor exposure equipment, commonly known as lithography machines, utilize a complex process to project circuit patterns onto silicon wafers.
This projection must be executed with extreme precision, often at nanometer scales.
Even the slightest vibration or misalignment can result in defects, which affect the performance and yield of the semiconductor devices.
The Importance of Vibration Control
Vibration control is essential for the optimal functioning of semiconductor exposure equipment.
Vibrations can originate from various sources, including the machinery itself, environmental factors, and human activity.
Uncontrolled vibrations can lead to disturbances that hamper the exposure process, potentially rendering entire batches of wafers unusable.
Sources of Vibration
There are numerous sources of vibration that can impact the performance of lithography machines.
One primary source is the mechanical components of the machine.
Motors, actuators, and other moving parts inherently produce vibrations.
Environmental factors such as building vibrations, acoustic noise, and ground tremors also contribute to the challenge.
Additionally, human activities like footsteps or nearby construction work can introduce vibrations into the system.
Strategies for Vibration Control
To address the issue of vibrations, several strategies can be employed.
First and foremost, the design of the exposure equipment must incorporate vibration-damping mechanisms.
This can include the use of isolation mounts, which help to absorb and dissipate vibrations.
Additionally, advanced materials that are less prone to vibration can be utilized in the construction of the machine.
Another effective strategy is the implementation of active vibration control systems.
These systems utilize sensors to detect and measure vibrations in real time.
The data is then processed, and counteracting forces are applied to neutralize the vibrations.
This ensures that the machine remains stable, even in the presence of external disturbances.
Moreover, environmental control measures can be adopted to minimize the impact of external vibrations.
This can involve isolating the exposure equipment from sources of noise and tremors, such as constructing dedicated, vibration-insulated rooms.
Implementing policies to limit human activity around sensitive equipment during critical operations is also beneficial.
Precision Control in Lithography Machines
In addition to vibration control, precision control mechanisms are crucial for the functionality of semiconductor exposure equipment.
The accuracy required in lithography machines demands control systems that can precisely manage the positioning and movement of various components.
Mechanisms for Precision Control
One of the core components of precision control in lithography machines is the alignment system.
This system ensures that the wafer is correctly positioned relative to the projected circuit pattern.
Misalignment at the nanometer scale can result in defective chips.
To this end, advanced optical sensors and feedback loops are implemented to achieve and maintain alignment accuracy.
Another important aspect of precision control is the regulation of the light source used for exposure.
The intensity, wavelength, and coherence of the light must be meticulously controlled.
Fluctuations in these parameters can lead to inconsistencies in the projected pattern, thereby compromising the quality of the semiconductor devices.
Additionally, the movement and positioning of the wafer stage, which holds the silicon wafer, must be precisely controlled.
State-of-the-art motor systems, often utilizing linear motors and magnetic levitation, enable smooth and accurate positioning.
Sophisticated software algorithms are employed to manage these systems, ensuring coordinated and precise movements.
Challenges in Precision Control
Despite advancements, precision control in lithography machines is not without challenges.
One significant challenge is thermal expansion.
The heat generated during the exposure process can cause components to expand and contract, leading to misalignments and inaccuracies.
To mitigate this, temperature control systems are integrated to maintain a stable thermal environment.
Materials with low thermal expansion coefficients are also preferred in the construction of critical components.
Furthermore, the miniaturization trend in semiconductor manufacturing poses additional challenges.
As device features shrink, the margin for error becomes exceedingly small.
This necessitates the continual development of more sophisticated control systems that can operate at exceptionally high levels of precision.
The Synergy of Vibration and Precision Control
While vibration control and precision control are distinct areas, they are closely interrelated.
Effective vibration control contributes to precision by providing a stable platform for the delicate operations of lithography machines.
Conversely, precise control mechanisms ensure that the system can promptly and accurately respond to any perturbations, including those related to vibrations.
Benefits of Integrated Control Solutions
An integrated approach that combines vibration control and precision control yields significant benefits.
It enhances the overall reliability and performance of semiconductor exposure equipment, leading to higher yields and reduced defect rates.
This is especially important as the demand for high-quality semiconductor devices continues to grow.
Moreover, by maintaining tighter control over the exposure process, manufacturers can push the boundaries of miniaturization and complexity in semiconductor devices.
This drives innovation and enables the development of more powerful and efficient electronic systems.
Conclusion
In the sophisticated world of semiconductor manufacturing, the importance of vibration control and precision control in exposure equipment cannot be overstated.
These critical mechanisms ensure that lithography machines operate with the necessary accuracy and reliability to produce high-quality semiconductor devices.
By understanding the sources of vibrations, employing effective control strategies, and integrating advanced precision mechanisms, manufacturers can achieve greater levels of performance and innovation.
In the ever-evolving realm of technology, such advancements provide a solid foundation for the continued progress and development of the semiconductor industry.
資料ダウンロード
QCD管理受発注クラウド「newji」は、受発注部門で必要なQCD管理全てを備えた、現場特化型兼クラウド型の今世紀最高の受発注管理システムとなります。
ユーザー登録
受発注業務の効率化だけでなく、システムを導入することで、コスト削減や製品・資材のステータス可視化のほか、属人化していた受発注情報の共有化による内部不正防止や統制にも役立ちます。
NEWJI DX
製造業に特化したデジタルトランスフォーメーション(DX)の実現を目指す請負開発型のコンサルティングサービスです。AI、iPaaS、および先端の技術を駆使して、製造プロセスの効率化、業務効率化、チームワーク強化、コスト削減、品質向上を実現します。このサービスは、製造業の課題を深く理解し、それに対する最適なデジタルソリューションを提供することで、企業が持続的な成長とイノベーションを達成できるようサポートします。
製造業ニュース解説
製造業、主に購買・調達部門にお勤めの方々に向けた情報を配信しております。
新任の方やベテランの方、管理職を対象とした幅広いコンテンツをご用意しております。
お問い合わせ
コストダウンが利益に直結する術だと理解していても、なかなか前に進めることができない状況。そんな時は、newjiのコストダウン自動化機能で大きく利益貢献しよう!
(β版非公開)