- お役立ち記事
- Vibration Control in Mechanical Systems with Feedforward Techniques
月間76,176名の
製造業ご担当者様が閲覧しています*
*2025年3月31日現在のGoogle Analyticsのデータより
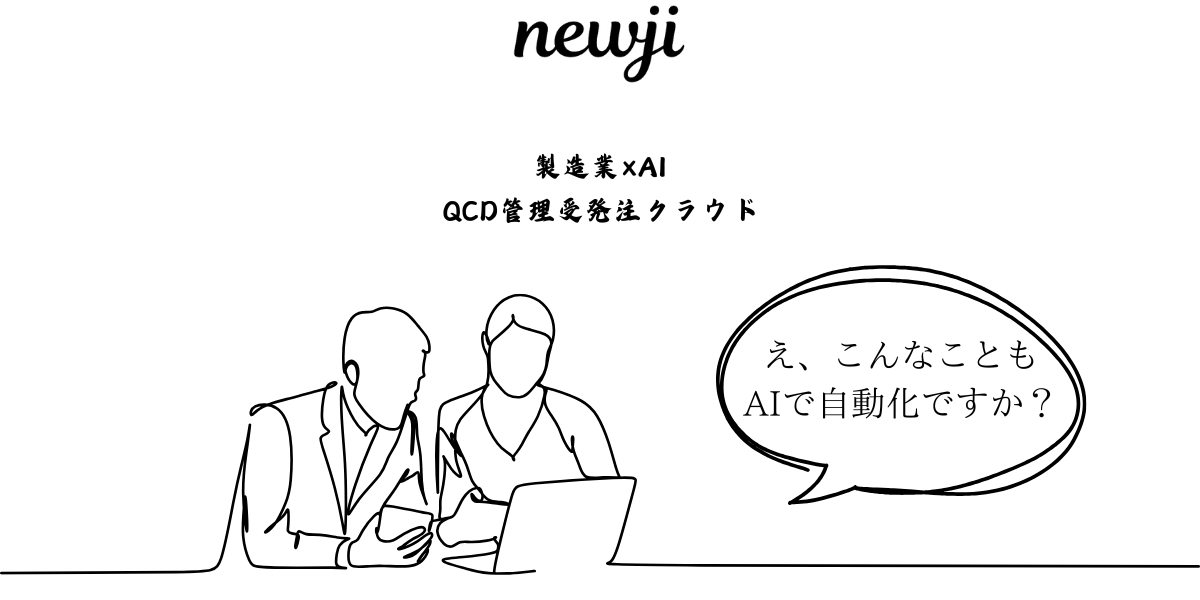
Vibration Control in Mechanical Systems with Feedforward Techniques
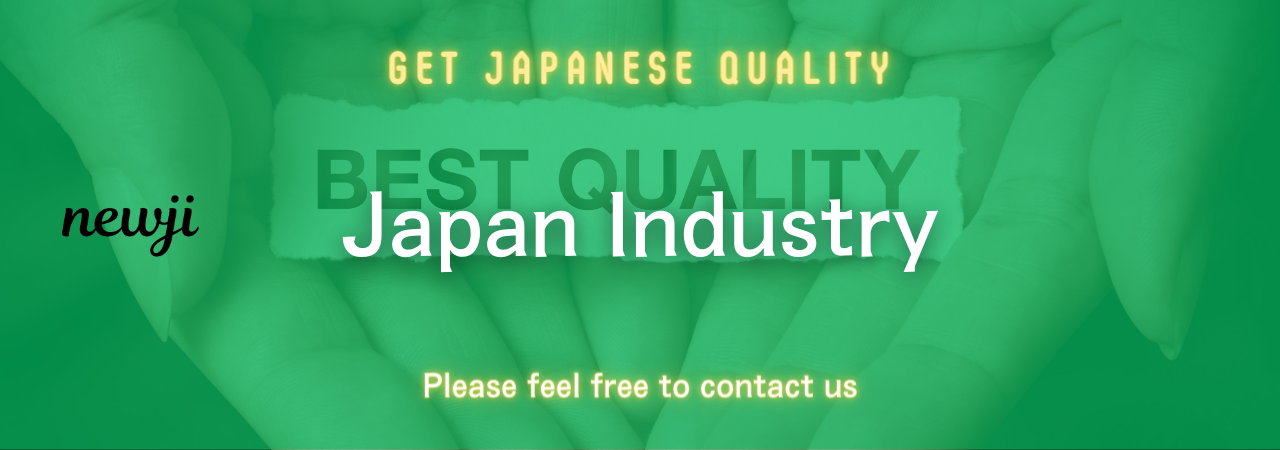
目次
Understanding Vibration Control in Mechanical Systems
Mechanical systems are fundamental components in various industries, ranging from automotive to aerospace, manufacturing to construction.
One crucial aspect in these systems is vibration control.
Vibration is an inevitable occurrence in mechanical systems due to moving parts, external forces, or environmental impacts.
However, excessive vibration can lead to noise, wear and tear, reduced efficiency, or even failure of the mechanical system.
To mitigate these issues, vibration control techniques are implemented.
Among the various methods, feedforward vibration control techniques have proven to be effective in managing vibrations before they affect the system negatively.
In this article, we will explore how feedforward techniques contribute to vibration control in mechanical systems.
What is Feedforward Vibration Control?
Feedforward control is a proactive strategy in system control that anticipates disturbances and compensates for them before they affect the system.
Unlike feedback control, which reacts to errors after they occur, feedforward control predicts disturbances by using a model of the system or incorporating sensor data.
In the realm of vibration control, feedforward techniques aim to suppress unwanted vibrations by applying corrective actions derived from models or sensors ahead of time.
These techniques reduce the need for reactive measures and can lead to improved stability and performance in mechanical systems.
Key Principles of Feedforward Techniques
Feedforward control relies on inputs and system modeling to achieve its goals.
Here are the key principles that define feedforward techniques in vibration control:
System Modeling
To implement feedforward vibration control, an accurate model of the mechanical system is imperative.
This model represents the behavior of the system, including the vibrational characteristics and dynamics.
Through modeling, it becomes possible to predict how the system responds to different inputs and disturbances.
Disturbance Prediction
Feedforward techniques require anticipating disturbances that may cause vibrations.
This can be achieved by detecting external forces, changes in system parameters, or environmental changes.
Predicting disturbances allows the control system to determine how they will potentially impact the system’s performance.
Corrective Actions
Once disturbances are predicted, feedforward control determines corrective actions that should be applied to counteract these disturbances.
This could involve adjusting the forces, altering system parameters, or applying opposing vibrations to cancel out the effects.
The control actions are implemented even before the disturbances have an impact, maintaining the system’s stability and efficiency.
Applications of Feedforward Vibration Control
Feedforward vibration control techniques are widely applied in various industries to address performance issues and enhance system operation.
Here are a few examples of their applications:
Automotive Systems
In the automotive industry, feedforward vibration control is used to improve ride quality and reduce noise.
Suspension systems are equipped with sensors and models to predict road vibrations.
Corrective forces are applied to the suspension components to absorb shocks and minimize vibrations, resulting in a smoother ride for passengers.
Aerospace Engineering
Aircraft and spacecraft are susceptible to vibrations due to aerodynamic forces and engine operations.
To ensure safety and reliability, aerospace engineers utilize feedforward techniques to predict and mitigate these vibrations.
This enhances the structural integrity and reduces the possibility of failure during missions or flights.
Manufacturing Equipment
Precision manufacturing equipment, like CNC machines, can be affected by vibrations that impact the quality of the final product.
Feedforward control techniques help to counteract these vibrations by anticipating tool and workpiece interactions.
This results in reduced errors, better surface finishes, and extended equipment lifespan.
Advantages of Using Feedforward Techniques
Employing feedforward vibration control techniques offers numerous benefits, including:
Proactive Approach
Rather than reacting to disturbances, feedforward techniques enable a proactive approach to vibration control.
By anticipating disturbances, corrective actions are implemented in advance, preventing unwanted impacts on the system.
Improved System Performance
The application of feedforward control often leads to an overall improvement in system performance.
Systems operate more efficiently, with reduced wear and tear and extended lifespan due to diminished vibrations.
Enhanced Stability
Feedforward techniques contribute to enhanced stability in mechanical systems by minimizing the effect of disturbances.
Stable systems are less prone to failures, ensuring reliability across different applications.
Challenges and Considerations
While feedforward vibration control offers significant advantages, its implementation comes with certain challenges and considerations:
Accurate System Modeling
To effectively employ feedforward techniques, the system model must be precise.
Inaccurate models can lead to improper corrective actions, potentially exacerbating the issue instead of mitigating it.
Real-Time Data Processing
Successful implementation of feedforward control requires real-time processing of data.
Delays in data acquisition, processing, or application of corrective actions can reduce the effectiveness of the control system.
Complexity and Cost
Implementing feedforward systems can be complex and costly, particularly in systems where disturbances are highly variable.
The need for advanced sensors, computational power, and intricate algorithms might raise the overall cost of the control system.
Conclusion
Feedforward vibration control techniques serve as a vital tool in managing vibrations proactively in mechanical systems.
By anticipating and counteracting disturbances before they impact the system, feedforward control ensures stability, enhances performance, and reduces the likelihood of system failure.
While there are challenges in implementing these techniques, the advantages they offer make them a valuable addition to industries where vibration control is crucial for success.
Understanding and applying feedforward vibration control techniques can lead to more efficient, reliable, and robust mechanical systems across various applications.
資料ダウンロード
QCD管理受発注クラウド「newji」は、受発注部門で必要なQCD管理全てを備えた、現場特化型兼クラウド型の今世紀最高の受発注管理システムとなります。
ユーザー登録
受発注業務の効率化だけでなく、システムを導入することで、コスト削減や製品・資材のステータス可視化のほか、属人化していた受発注情報の共有化による内部不正防止や統制にも役立ちます。
NEWJI DX
製造業に特化したデジタルトランスフォーメーション(DX)の実現を目指す請負開発型のコンサルティングサービスです。AI、iPaaS、および先端の技術を駆使して、製造プロセスの効率化、業務効率化、チームワーク強化、コスト削減、品質向上を実現します。このサービスは、製造業の課題を深く理解し、それに対する最適なデジタルソリューションを提供することで、企業が持続的な成長とイノベーションを達成できるようサポートします。
製造業ニュース解説
製造業、主に購買・調達部門にお勤めの方々に向けた情報を配信しております。
新任の方やベテランの方、管理職を対象とした幅広いコンテンツをご用意しております。
お問い合わせ
コストダウンが利益に直結する術だと理解していても、なかなか前に進めることができない状況。そんな時は、newjiのコストダウン自動化機能で大きく利益貢献しよう!
(β版非公開)