- お役立ち記事
- Vibration control technology for mechanical systems using feedforward control and its application through simulation
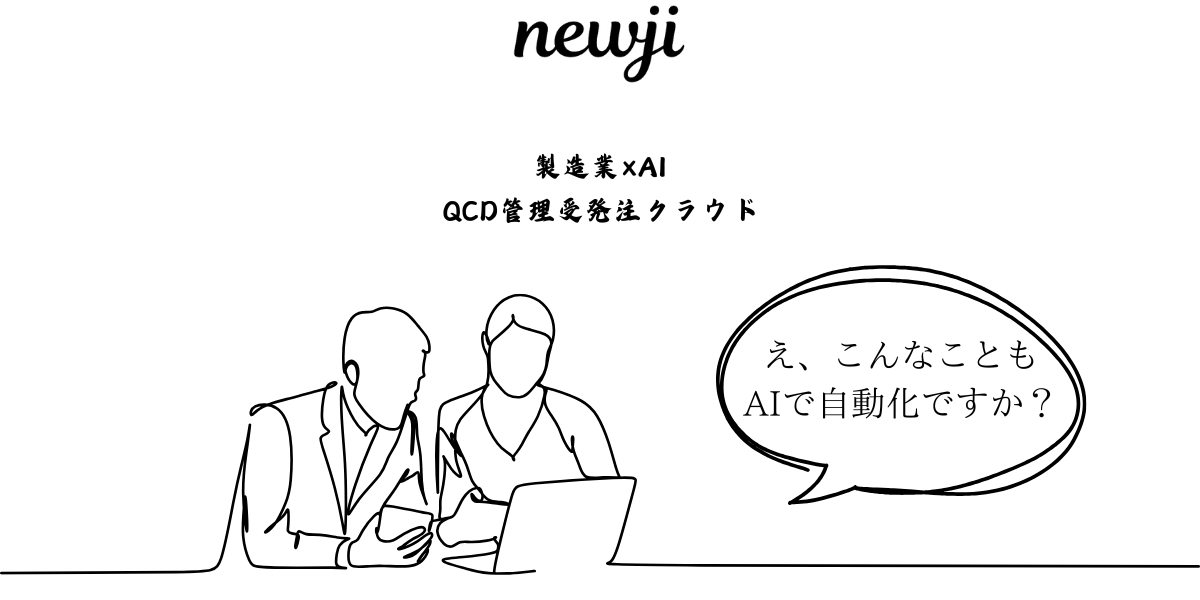
Vibration control technology for mechanical systems using feedforward control and its application through simulation
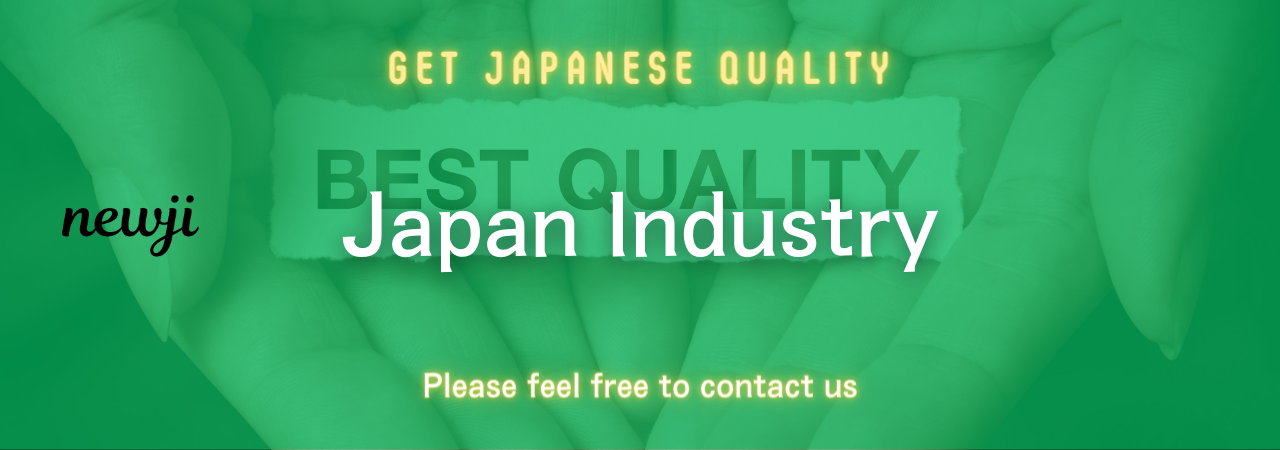
目次
Understanding Vibration Control in Mechanical Systems
Vibration control is essential in mechanical systems to ensure stability, safety, and efficiency.
Uncontrolled vibrations can lead to wear and tear, noise, and even system failures.
To address these challenges, engineers use various techniques, one of which is feedforward control.
Feedforward control is a proactive way to manage vibrations by anticipating potential disturbances.
Unlike feedback control, which reacts to deviations after they occur, feedforward control acts before the system is affected.
This preemptive approach can significantly enhance system stability and performance.
The Basics of Feedforward Control
Feedforward control works by predicting disturbances and adjusting the system accordingly.
It requires accurate modeling of the mechanical system and a clear understanding of potential disturbances.
Once these factors are identified, the control system can implement corrective actions proactively.
For instance, in a manufacturing setting, machinery vibrations caused by external factors like uneven ground or motor imbalances can be predicted.
By understanding these factors, feedforward control can initiate corrective measures to minimize the impact before it affects production quality.
Components of a Feedforward Control System
A feedforward control system typically involves three main components:
1. Sensors
Sensors detect incoming disturbances or conditions that may lead to vibrations.
They provide real-time data to the control system, enabling it to make informed decisions.
2. Actuators
Actuators are responsible for implementing the control actions decided by the system.
They adjust system parameters to counteract or minimize the predicted disturbances.
3. Control Algorithms
These are the mathematical models and algorithms that analyze sensor data, identify potential disturbances, and dictate the necessary actions.
Benefits of Using Feedforward Control in Vibration Management
Feedforward control offers several advantages for managing vibrations in mechanical systems.
1. Proactive Disturbance Mitigation
Since feedforward control anticipates disturbances, it reduces the reactive measures needed to stabilize the system, leading to a quicker response and fewer disruptions.
2. Enhanced System Performance
By reducing unexpected vibrations, the system can operate more smoothly, leading to increased efficiency and lower maintenance costs.
3. Improved Safety and Reliability
Minimizing vibrations through proactive control enhances the safety and reliability of mechanical systems, vital in industries where equipment failure could lead to catastrophic consequences.
Real-World Applications of Feedforward Vibration Control
Feedforward vibration control is utilized across various sectors, including manufacturing, automotive, and aerospace industries.
Manufacturing
In manufacturing, precision is critical.
Feedforward control can enhance the accuracy of cutting, grinding, and milling machines by minimizing vibrations that lead to errors.
Automotive
In the automotive industry, feedforward control helps manage vibrations in engine mounts, suspension systems, and other vehicle components.
This improves ride comfort and vehicle longevity.
Aerospace
In aerospace applications, controlling vibrations is essential for aircraft safety and comfort.
Feedforward control systems are employed in flight control surfaces and other critical components to ensure smooth operation.
Simulation: A Powerful Tool for Developing Feedforward Control
Simulations play a crucial role in developing and testing feedforward control systems.
They allow engineers to model mechanical systems, predict disturbances, and test control strategies in a virtual environment.
Why Use Simulation?
1. Risk Reduction
Simulations provide a safe environment to test various control strategies without risking damage to actual machinery.
2. Cost Efficiency
By identifying the most effective control strategies through simulations, companies can save on costs associated with trial-and-error testing on physical equipment.
3. Speed and Flexibility
Simulations enable quicker iterations and adjustments to control algorithms, speeding up the development process and allowing for rapid testing of different scenarios.
Case Study: Simulating Feedforward Control in a Manufacturing Plant
Consider a manufacturing plant with a high-speed conveyor system.
Frequent vibrations from the machinery lead to product misalignment and production delays.
Using simulation, engineers model the conveyor system and simulate various operational conditions.
Predictive algorithms within the simulation identify potential vibration sources.
Engineers then design feedforward control strategies to mitigate these vibrations before they occur.
Once validated in the simulation, the optimized control strategies are implemented in the real conveyor system.
The result is a significant reduction in vibrations, improving product alignment and overall production efficiency.
Challenges and Future Prospects
While feedforward control offers significant benefits, it also faces challenges.
1. Accurate System Modeling
The effectiveness of feedforward control relies on accurate system modeling and prediction of disturbances.
Inaccurate models can lead to ineffective control strategies.
2. Complexity
Implementing feedforward control systems can be complex, requiring expertise in system dynamics and control theory.
Despite these challenges, advancements in sensor technology, computational power, and machine learning algorithms continue to enhance the efficacy and accessibility of feedforward control.
The future of feedforward control technology holds promise for more widespread adoption across industries, leading to enhanced stability, efficiency, and safety in mechanical systems globally.
資料ダウンロード
QCD調達購買管理クラウド「newji」は、調達購買部門で必要なQCD管理全てを備えた、現場特化型兼クラウド型の今世紀最高の購買管理システムとなります。
ユーザー登録
調達購買業務の効率化だけでなく、システムを導入することで、コスト削減や製品・資材のステータス可視化のほか、属人化していた購買情報の共有化による内部不正防止や統制にも役立ちます。
NEWJI DX
製造業に特化したデジタルトランスフォーメーション(DX)の実現を目指す請負開発型のコンサルティングサービスです。AI、iPaaS、および先端の技術を駆使して、製造プロセスの効率化、業務効率化、チームワーク強化、コスト削減、品質向上を実現します。このサービスは、製造業の課題を深く理解し、それに対する最適なデジタルソリューションを提供することで、企業が持続的な成長とイノベーションを達成できるようサポートします。
オンライン講座
製造業、主に購買・調達部門にお勤めの方々に向けた情報を配信しております。
新任の方やベテランの方、管理職を対象とした幅広いコンテンツをご用意しております。
お問い合わせ
コストダウンが利益に直結する術だと理解していても、なかなか前に進めることができない状況。そんな時は、newjiのコストダウン自動化機能で大きく利益貢献しよう!
(Β版非公開)