- お役立ち記事
- Vibration strength design and optimization of turbomachinery blades and impellers and troubleshooting
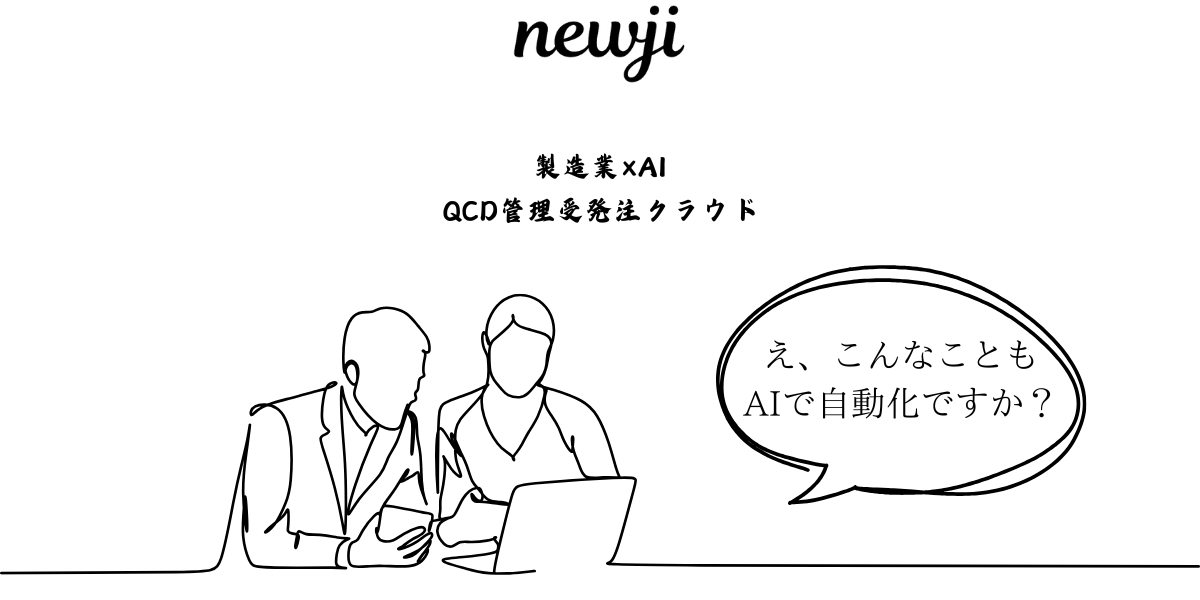
Vibration strength design and optimization of turbomachinery blades and impellers and troubleshooting
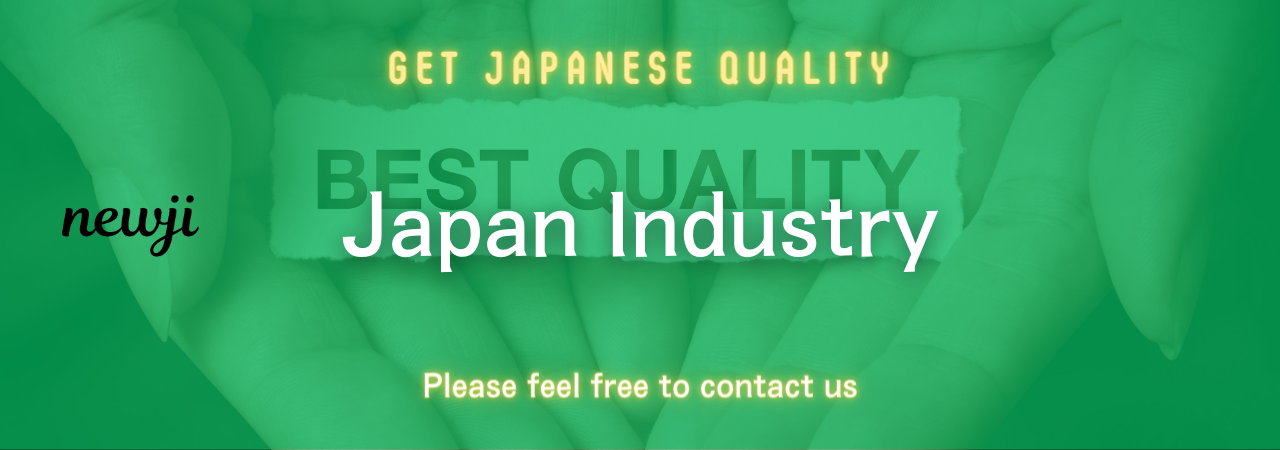
目次
Understanding Vibration in Turbomachinery
Vibration is a critical aspect that must be carefully managed in the design and operation of turbomachinery, which includes both blades and impellers.
These components are integral to the efficiency and functionality of engines, pumps, and compressors.
Understanding the causes and impacts of vibration can help in optimizing performance and preventing failures.
Turbomachinery blades and impellers are subject to various forces that can induce vibration.
These forces can arise from aerodynamic, mechanical, or thermal sources.
Aerodynamic forces might be due to irregular airflow or pressure changes.
Mechanical forces can result from the imbalances in rotating components, while thermal effects may stem from temperature variances that cause expansion or contraction.
When these vibrations become too intense, they can lead to fatigue failure, resulting in substantial operational setbacks or even safety risks.
The Role of Blade Design
The design of turbomachinery blades plays a pivotal role in vibration strength.
Engineers must consider various factors such as material selection, geometry, and stress distribution.
Optimizing these factors helps in enhancing the durability and efficiency of the blades.
Material selection is crucial as it affects how blades dampen vibrations.
Strong and lightweight materials, such as titanium alloys or composites, are commonly used due to their high fatigue resistance.
In addition, the geometry of blades, including their shape and thickness, significantly influences how they handle forces.
A well-designed blade reduces turbulence and facilitates smooth airflow, minimizing aerodynamic-induced vibrations.
Stress distribution within the blades also demands careful attention.
Using computational tools, engineers can simulate how stress is distributed across blades under operational conditions.
By adjusting the design based on these simulations, they can ensure that stress concentrations are minimized, reducing the chances of vibrations leading to material fatigue.
Impeller Optimization Techniques
Impellers are another key component that needs optimization for vibration strength.
These rotating devices work to increase the pressure and flow of fluids, making them susceptible to vibration issues.
Balancing is one of the fundamental techniques to mitigate vibrations in impellers.
Any imbalance in the rotor can lead to excessive vibrations, contributing to mechanical wear and damage.
Precise manufacturing and machining processes ensure that the mass distribution of the impeller is uniform, thereby reducing the potential for imbalances.
The use of advanced computational fluid dynamics (CFD) tools aids in optimizing impeller designs.
These tools allow engineers to simulate and analyze the flow patterns within the impeller, identifying possible sources of turbulence or pressure fluctuations.
By refining the design based on CFD results, engineers can enhance the impeller’s aerodynamic performance and minimize vibration-induced stresses.
Another vital approach is to conduct comprehensive dynamic analysis.
Such analysis helps in identifying the natural frequency of impellers, which is crucial in avoiding resonant vibrations during operation.
By ensuring that the impeller’s operational frequency does not match its natural frequency, the risk of excessive vibrations is significantly reduced.
Troubleshooting Vibration Issues
Despite taking preventive measures, turbomachinery may still experience vibration-related issues during its lifespan.
Effective troubleshooting is essential in identifying the root cause and implementing corrective actions.
Regular monitoring and inspection are the first steps in troubleshooting.
Utilizing vibration analysis tools can help in detecting abnormal vibration patterns early.
These tools analyze the frequency, amplitude, and phase of vibrations, providing insights into potential issues such as bearing wear, rotor imbalances, or aerodynamic instabilities.
It is also crucial to consider operational conditions.
Changes in operating parameters, such as speed or load, can affect the vibration behavior of turbomachinery.
Reviewing these conditions helps in determining whether the vibration issue is linked to external factors rather than internal flaws.
When inspecting for mechanical issues, focusing on the integrity of mounting fixtures and connections is vital.
Loose fittings or worn-out parts can exacerbate vibrations, contributing to more significant mechanical problems.
In some cases, retrofitting or upgrading certain components may be necessary.
This could involve replacing worn-out parts with newer, vibration-resistant materials or implementing advanced damping technologies.
Long-Term Strategies for Vibration Management
Managing vibration in turbomachinery is not a one-time task but an ongoing process.
Implementing long-term strategies helps in sustaining optimized performance and extending the lifespan of both blades and impellers.
Routine maintenance schedules ensure that all components are functioning correctly and are free from defects that could cause vibrations.
Keeping a log of maintenance records also aids in tracking the history of vibration issues, helping in predictive maintenance planning.
Investment in advanced monitoring systems is another strategic approach.
Modern turbomachinery often incorporates sensors that continuously monitor vibration levels.
These systems can provide real-time data, allowing for quick response to any deviations and preventing potential failures.
Continuous research and development play a significant role in vibration management.
Stay abreast of the latest advances in materials, design techniques, and computational tools.
This knowledge can be applied to improve existing designs or develop new solutions that further reduce the risk of vibrations.
Conclusion
Vibration strength design and optimization in turbomachinery are crucial for ensuring efficiency, safety, and longevity.
Understanding the causes of vibration, optimizing designs through advanced tools, and employing effective troubleshooting and maintenance strategies are all integral parts of managing these challenges.
By prioritizing vibration management, industries can improve performance and reduce the risk of costly failures, ensuring that turbomachinery continues to operate smoothly and reliably.
資料ダウンロード
QCD調達購買管理クラウド「newji」は、調達購買部門で必要なQCD管理全てを備えた、現場特化型兼クラウド型の今世紀最高の購買管理システムとなります。
ユーザー登録
調達購買業務の効率化だけでなく、システムを導入することで、コスト削減や製品・資材のステータス可視化のほか、属人化していた購買情報の共有化による内部不正防止や統制にも役立ちます。
NEWJI DX
製造業に特化したデジタルトランスフォーメーション(DX)の実現を目指す請負開発型のコンサルティングサービスです。AI、iPaaS、および先端の技術を駆使して、製造プロセスの効率化、業務効率化、チームワーク強化、コスト削減、品質向上を実現します。このサービスは、製造業の課題を深く理解し、それに対する最適なデジタルソリューションを提供することで、企業が持続的な成長とイノベーションを達成できるようサポートします。
オンライン講座
製造業、主に購買・調達部門にお勤めの方々に向けた情報を配信しております。
新任の方やベテランの方、管理職を対象とした幅広いコンテンツをご用意しております。
お問い合わせ
コストダウンが利益に直結する術だと理解していても、なかなか前に進めることができない状況。そんな時は、newjiのコストダウン自動化機能で大きく利益貢献しよう!
(Β版非公開)