- お役立ち記事
- Vibration Testing and Evaluation Standards in Production Equipment
月間76,176名の
製造業ご担当者様が閲覧しています*
*2025年3月31日現在のGoogle Analyticsのデータより
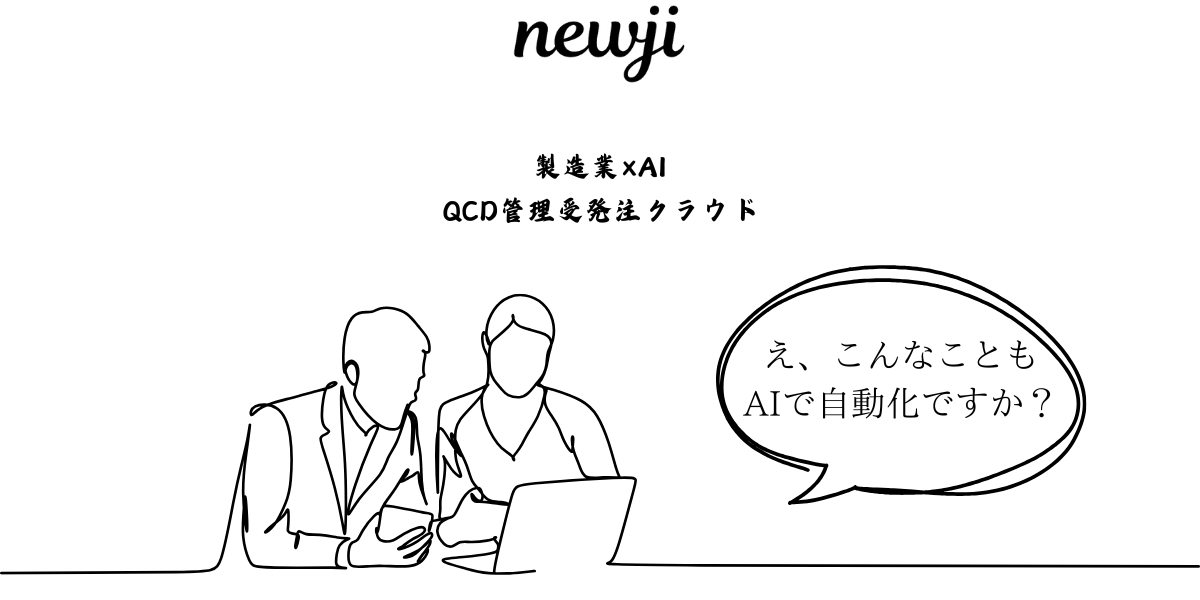
Vibration Testing and Evaluation Standards in Production Equipment
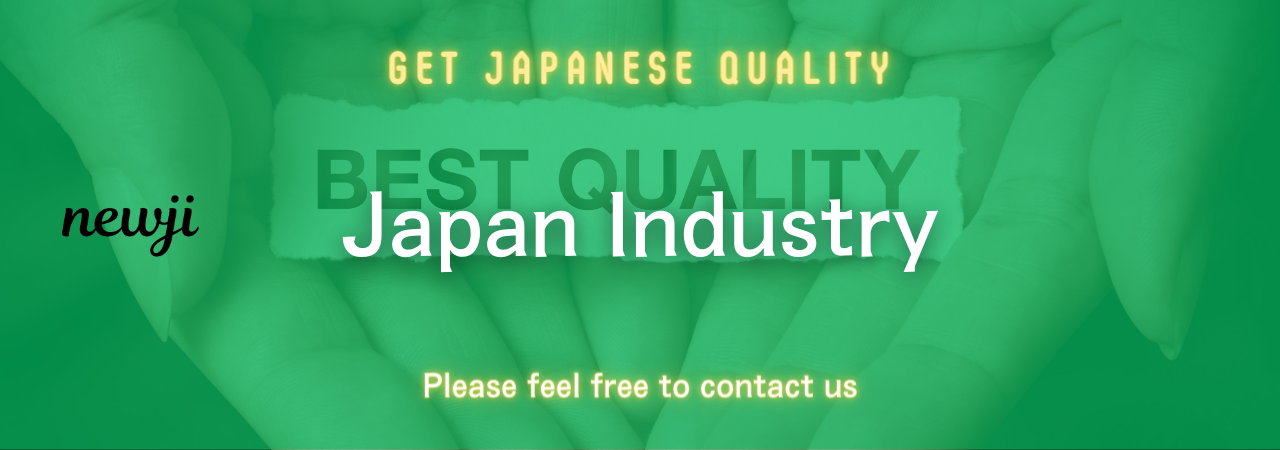
目次
Understanding Vibration Testing in Production Equipment
In the world of manufacturing, ensuring that production equipment operates smoothly and efficiently is crucial.
One of the essential ways to achieve this is through vibration testing.
Vibration testing is a method used to assess the vibrations that occur in machinery and equipment during operation.
This process helps in identifying potential issues that could lead to equipment failure, reducing downtime, and improving overall productivity.
Vibration can occur due to several factors such as mechanical imbalances, alignment issues, or external influences like seismic activity.
Regular vibration testing and evaluation allow manufacturers to monitor machinery health and take corrective actions before minor issues turn into major problems.
The Importance of Vibration Testing
Vibration testing is important for several reasons.
Firstly, it aids in quality control by ensuring that the production equipment meets industry standards.
Equipment that vibrates excessively can lead to poor-quality products, increased wear and tear, or even equipment failure.
Through vibration testing, manufacturers can maintain high quality and consistency in their products.
Secondly, vibration testing plays a crucial role in safety.
Excessive vibrations in machinery can be hazardous, potentially leading to accidents or equipment malfunction.
Routine testing and evaluation help in identifying these risks and mitigating them accordingly.
Lastly, vibration testing contributes significantly to cost savings.
Identifying and fixing vibration issues early can save a company from costly repairs and downtime.
By optimizing the performance of machinery, companies can extend the lifespan of their equipment and reduce operational costs.
Types of Vibration Testing Methods
There are several methods of vibration testing, each serving different purposes depending on the type of equipment and the specific issues it may face.
Operational Deflection Shape (ODS) Analysis
ODS analysis involves measuring the vibration of equipment while it is in operation.
This method helps visualize the movement of the equipment and identify areas that may need further inspection or repairs.
ODS is particularly useful for identifying dynamic behaviors related to operational imbalances or misalignments.
Frequency Analysis
Frequency analysis is a common vibration testing method that involves measuring the frequency of vibrations in equipment components.
By analyzing these frequencies, technicians can determine if there are any anomalies indicating mechanical issues such as worn-out bearings or loose parts.
Time Waveform Analysis
Time waveform analysis involves capturing the vibration signal over a designated period.
This method is beneficial in understanding the exact nature and cause of vibrations.
It provides detailed information that frequency analysis alone may not reveal, such as transient events or intermittent abnormalities.
Resonant Frequency Testing
Resonant frequency testing is used to identify the natural frequency of a piece of equipment or structure.
Understanding this frequency is vital because resonance can cause severe damage if not managed properly.
This testing helps manufacturers design equipment that avoids operation at natural frequencies, reducing the risk of resonance-related issues.
Vibration Evaluation Standards
Vibration evaluation standards are integral in providing guidelines for acceptable vibration levels in production equipment.
These standards help manufacturers maintain uniformity in quality and ensure safety.
ISO 10816
ISO 10816 is one of the most widely recognized standards for evaluating mechanical vibration in rotating and reciprocating machinery.
It provides guidelines on vibration severity in relation to equipment types and operational conditions.
This standard categorizes machinery into different classes and specifies acceptable vibration limits for each class.
ANSI S2.1
The American National Standards Institute (ANSI) provides standards like ANSI S2.1, focused on mechanical vibration and shock measurements.
This standard outlines the methods for measuring vibration in different types of equipment and provides criteria for evaluating the results.
It is particularly valuable for industries where precise vibration measurements are critical.
IEC 60034-14
IEC 60034-14 is an international standard that deals with the vibration limits of electrical motors.
This standard specifies the permissible vibration levels for motors of different sizes and operational conditions.
It helps manufacturers and engineers ensure that electrical motors operate within safe and efficient vibration parameters.
Implementing and Following Vibration Standards
Compliance with vibration evaluation standards is essential for manufacturers aiming to enhance operational efficiency and safety.
Implementing these standards involves regular monitoring and testing of production equipment.
Routine Maintenance
Regular maintenance should include vibration testing as a part of standard operating procedures.
This approach helps in early detection of potential issues, ensuring timely intervention and preventing costly breakdowns.
Training and Awareness
Training personnel to understand and interpret vibration data is crucial.
Skilled technicians can make informed decisions based on test results, enabling proactive maintenance and troubleshooting.
Advanced Monitoring Systems
The use of advanced monitoring systems and technologies can provide continuous and real-time data on equipment vibration.
IoT-enabled sensors and smart diagnostic tools can alert operators to changes in vibration patterns instantly, facilitating quicker response times.
By adhering to industry standards and implementing comprehensive vibration testing regimes, manufacturers can safeguard their equipment, enhance product quality, and boost production efficiency.
Understanding and managing vibrations in production equipment is a critical factor in achieving operational excellence in the manufacturing sector.
資料ダウンロード
QCD管理受発注クラウド「newji」は、受発注部門で必要なQCD管理全てを備えた、現場特化型兼クラウド型の今世紀最高の受発注管理システムとなります。
ユーザー登録
受発注業務の効率化だけでなく、システムを導入することで、コスト削減や製品・資材のステータス可視化のほか、属人化していた受発注情報の共有化による内部不正防止や統制にも役立ちます。
NEWJI DX
製造業に特化したデジタルトランスフォーメーション(DX)の実現を目指す請負開発型のコンサルティングサービスです。AI、iPaaS、および先端の技術を駆使して、製造プロセスの効率化、業務効率化、チームワーク強化、コスト削減、品質向上を実現します。このサービスは、製造業の課題を深く理解し、それに対する最適なデジタルソリューションを提供することで、企業が持続的な成長とイノベーションを達成できるようサポートします。
製造業ニュース解説
製造業、主に購買・調達部門にお勤めの方々に向けた情報を配信しております。
新任の方やベテランの方、管理職を対象とした幅広いコンテンツをご用意しております。
お問い合わせ
コストダウンが利益に直結する術だと理解していても、なかなか前に進めることができない状況。そんな時は、newjiのコストダウン自動化機能で大きく利益貢献しよう!
(β版非公開)