- お役立ち記事
- Vibration Testing and Management Methods in General Machinery
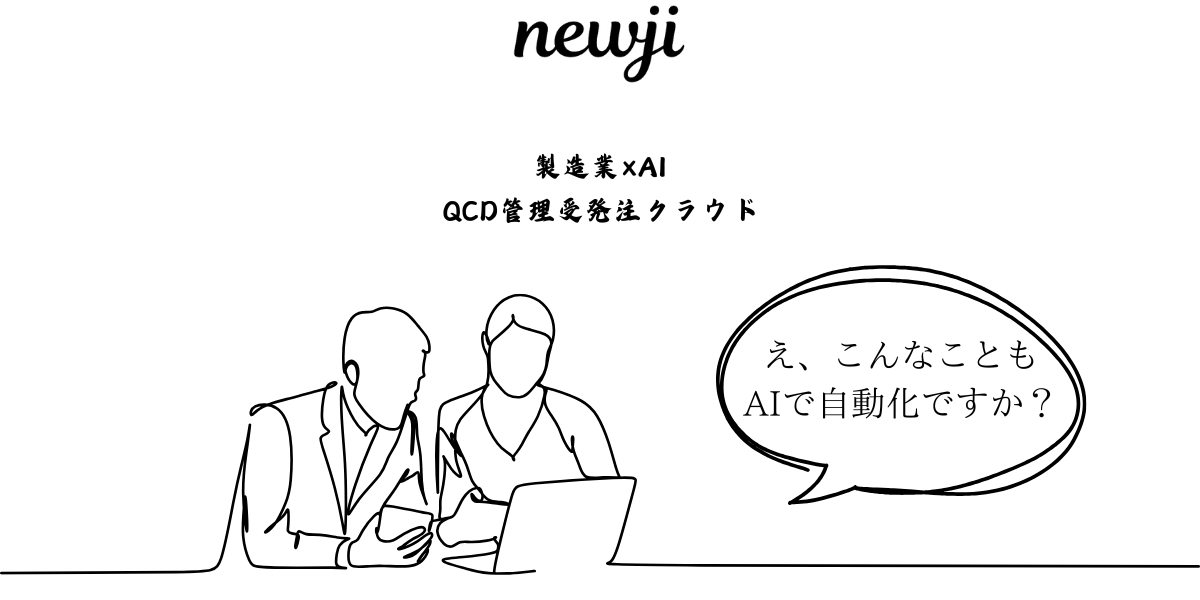
Vibration Testing and Management Methods in General Machinery
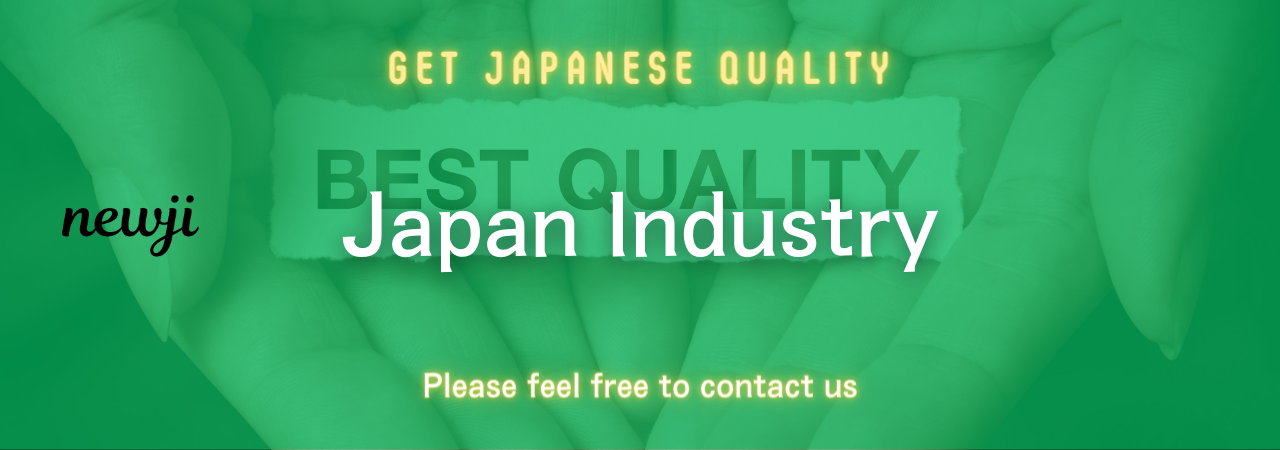
目次
Introduction to Vibration Testing
Vibration testing is a critical process in the field of engineering and machinery maintenance.
It involves evaluating the behavior of machinery under various simulated conditions to ensure its performance and durability.
Vibration testing helps identify potential weaknesses in machinery, which can lead to failures or malfunctions if not addressed in time.
Machines in steady operation naturally produce vibrations.
However, excessive or abnormal vibrations can indicate problems, such as imbalances or defects in the components.
This is where vibration testing becomes pivotal.
By understanding the vibratory behavior, engineers can predict the lifespan of machinery and make necessary adjustments to maintain efficiency and safety.
Why is Vibration Testing Important?
There are several reasons why vibration testing is essential in the general machinery sector.
Firstly, it helps ensure machinery reliability.
By detecting abnormal vibrations early, technicians can prevent unexpected breakdowns, saving both time and resources.
Secondly, it improves safety.
Abnormal vibrations can lead to catastrophic failures, which may endanger workers and compromise operational safety.
By monitoring and addressing vibration issues, companies can maintain a safer working environment.
Lastly, vibration testing enhances the operational efficiency of machinery.
When machines operate smoothly, they consume less energy, run more efficiently, and have a longer lifespan.
This contributes to the overall productivity and profitability of the business.
Methods of Vibration Testing
There are several methods of vibration testing, each serving unique applications and needs.
Some of the most common types include:
1. Sinusoidal Vibration Testing
Sinusoidal vibration testing, often referred to as sine testing, involves subjecting a machine to a range of sinusoidal vibrations.
This form of testing is used to simulate real-life conditions that a machine might encounter.
It is ideal for detecting resonant frequencies, where natural structural vibrations align with external forces, causing amplification.
2. Random Vibration Testing
Random vibration testing subjects machinery to a range of frequencies simultaneously.
This process simulates a more realistic environment because machines often experience multiple frequencies during normal operation.
Random testing is particularly useful for identifying weaknesses in newly designed equipment or components.
3. Shock Vibration Testing
Shock vibration testing assesses a machine’s ability to withstand sudden and extreme forces.
It is essential for equipment expected to endure impacts during their operation, such as vehicles or field machinery.
Through this testing, engineers can validate that the equipment can absorb shocks without sustaining damage.
4. Operational Vibration Testing
Operational testing allows engineers to evaluate machinery under normal working conditions.
It differs from other tests by examining the equipment while it is fully operational, capturing real-time data on how it performs in actual scenarios.
This form of testing helps in identifying real-world issues that might not appear under controlled environments.
Vibration Management in General Machinery
Effective vibration management is vital for the longevity and reliability of machinery.
Once abnormal vibrations have been detected, several management techniques can be applied to address these issues.
1. Balancing
Balancing is a straightforward yet effective method to manage excessive vibrations.
Imbalances in rotating parts are a common cause of vibrations.
Weight adjustments or corrections can bring balance and reduce vibration levels, enhancing the machine’s performance.
2. Isolation
Vibration isolation involves using specialized supports or mounts that dampen vibrations.
It prevents vibrational energy from being transmitted between components or to the machine’s surroundings.
By isolating parts that generate excessive vibration, the overall impact on the machine is minimized.
3. Damping
Damping refers to the process of absorbing or dissipating vibrational energy to minimize its effects.
Materials like rubber or specific composites are often used to coat or encase vibrating components, limiting displacement and reducing noise.
4. Regular Maintenance
Routine maintenance is crucial to controlling machinery vibrations.
Scheduled inspections and maintenance allow for early detection and correction of potential issues.
Replacing worn-out parts, lubricating the moving components, and realigning misaligned elements can significantly reduce vibrations.
Conclusion
Vibration testing and management are integral components of machinery maintenance and engineering.
By understanding the vibrational behavior of machinery and implementing appropriate management strategies, companies can enhance the reliability, safety, and efficiency of their equipment.
Proactive measures through regular testing and maintenance ensure machinery operates at its best, reducing the risk of failures and extending their operational life.
In an industry where downtime can result in significant financial loss, prioritizing vibration testing and management is not just a maintenance task—it’s a business imperative.
資料ダウンロード
QCD調達購買管理クラウド「newji」は、調達購買部門で必要なQCD管理全てを備えた、現場特化型兼クラウド型の今世紀最高の購買管理システムとなります。
ユーザー登録
調達購買業務の効率化だけでなく、システムを導入することで、コスト削減や製品・資材のステータス可視化のほか、属人化していた購買情報の共有化による内部不正防止や統制にも役立ちます。
NEWJI DX
製造業に特化したデジタルトランスフォーメーション(DX)の実現を目指す請負開発型のコンサルティングサービスです。AI、iPaaS、および先端の技術を駆使して、製造プロセスの効率化、業務効率化、チームワーク強化、コスト削減、品質向上を実現します。このサービスは、製造業の課題を深く理解し、それに対する最適なデジタルソリューションを提供することで、企業が持続的な成長とイノベーションを達成できるようサポートします。
オンライン講座
製造業、主に購買・調達部門にお勤めの方々に向けた情報を配信しております。
新任の方やベテランの方、管理職を対象とした幅広いコンテンツをご用意しております。
お問い合わせ
コストダウンが利益に直結する術だと理解していても、なかなか前に進めることができない状況。そんな時は、newjiのコストダウン自動化機能で大きく利益貢献しよう!
(Β版非公開)