- お役立ち記事
- Visualization and reduction techniques for raw material costs practiced by purchasing departments
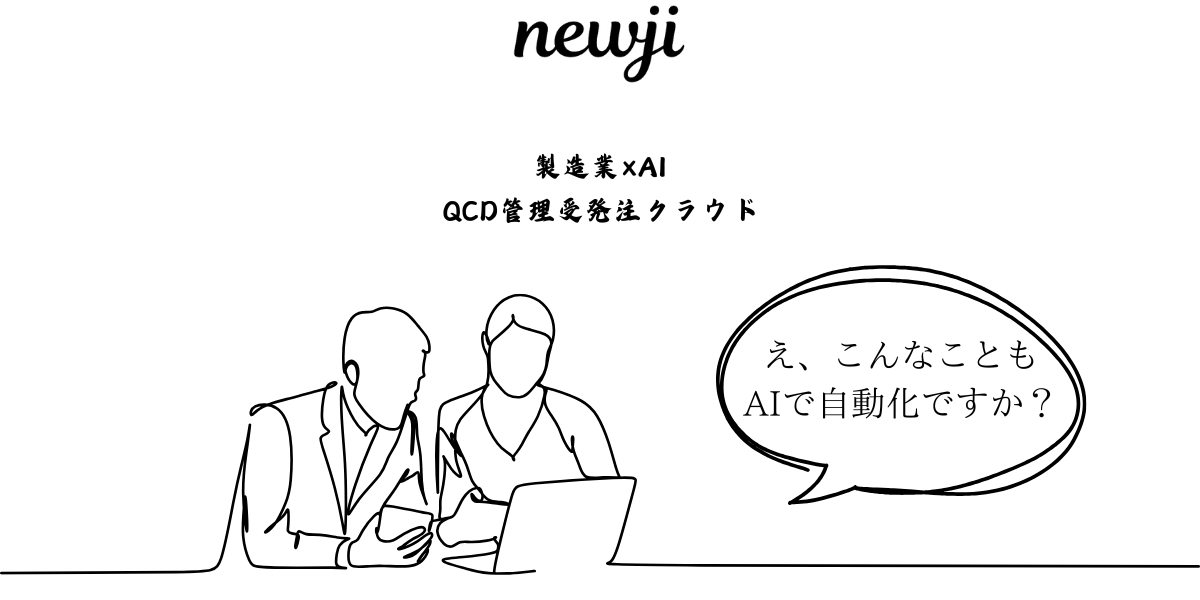
Visualization and reduction techniques for raw material costs practiced by purchasing departments
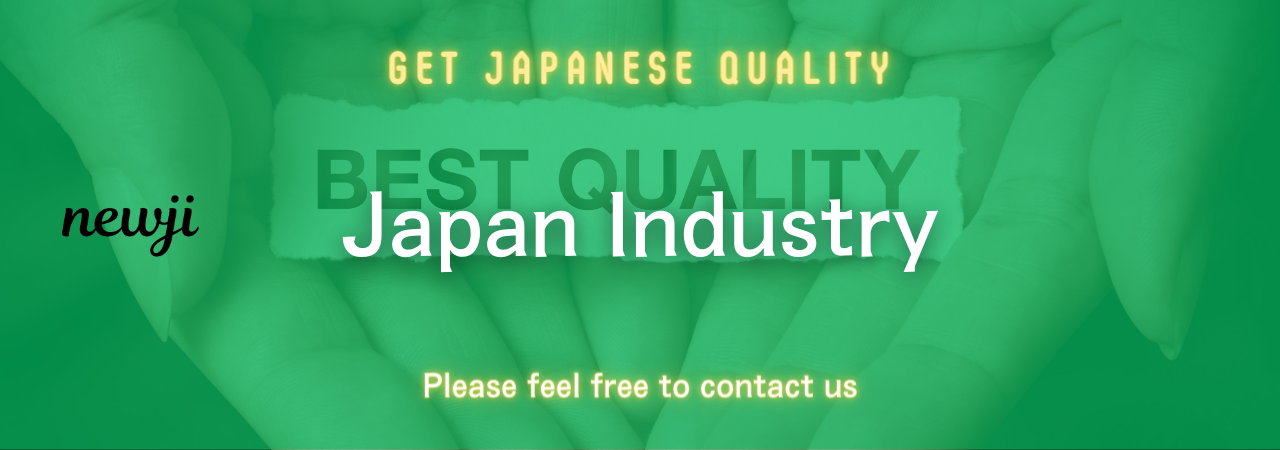
目次
Understanding Raw Material Costs
Purchasing departments in businesses across various industries face the constant challenge of managing raw material costs.
These costs can fluctuate due to a number of factors such as market demand, supply chain disruptions, and global economic conditions.
Proper visualization and reduction strategies are paramount to effectively manage these expenses.
In this article, we’ll explore techniques that purchasing departments can employ to control and reduce raw material costs while ensuring operational efficiency.
The Importance of Visualization in Cost Management
Visualization in the context of cost management involves presenting data in a way that makes it easier to understand and analyze.
For purchasing departments, having a clear view of raw material costs is essential for making informed decisions.
Visual tools like charts, graphs, and dashboards allow managers to see patterns, trends, and anomalies in their sourcing expenses.
With visualization tools, purchasing managers can quickly identify which materials are contributing most to the cost and which prices are fluctuating.
Utilizing Software for Data Visualization
The use of visualization software tools like Tableau, Power BI, or Excel can transform complex datasets into meaningful insights.
These tools help in developing customized dashboards that track the price movements of materials, compare costs across suppliers, and project future expenses.
They also enable the integration of real-time data feeds, ensuring that decisions are based on the most current information.
Benefits of Data Visualization
The primary benefit of visualizing data is the ability to identify cost drivers.
By clearly seeing which materials are the most expensive or volatile, purchasing managers can prioritize efforts to negotiate better prices or find alternative sources.
Additionally, visualization aids in tracking the impact of cost-reduction initiatives over time, helping departments to measure success and make data-driven decisions.
Effective Cost Reduction Techniques
Once the raw material costs are clearly understood, the next step is to employ techniques to reduce these costs.
There are several strategies purchasing departments can leverage to achieve cost reductions without compromising quality.
Supplier Negotiations
Effective negotiation with suppliers is critical for managing raw material costs.
Establishing long-term relationships can lead to favorable pricing agreements.
Additionally, purchasing managers should be prepared to negotiate terms such as payment schedules, bulk discounts, or loyalty incentives that can lead to cost reductions.
Alternative Sourcing
Exploring alternative suppliers or materials can also drive down costs.
By diversifying the supply base, purchasing departments can reduce dependency on single suppliers, which often leads to better pricing leverage.
Evaluating substitute materials or parts which offer similar performance at a lower cost can also yield significant savings.
Collaborative Approach
Collaboration with engineering, production, and other departments can also lead to innovative cost-saving strategies.
Collective cross-departmental efforts can uncover inefficiencies and propose ways to redesign products to use less expensive or less material-intensive options.
Volume Consolidation
Consolidating purchases to leverage volume discounts is a proven method to achieve cost savings.
Combining orders across locations or divisions can enhance the company’s negotiating power with suppliers, leading to bulk purchase discounts.
Implementing a Cost Monitoring System
An effective cost monitoring system is crucial for proactive management of raw material expenses.
Regular monitoring helps in rapidly identifying any deviation from expected costs, allowing the department to act promptly.
Regular Cost Analysis
Implement regular cost analysis schedules to track fluctuations in material prices and consumption trends.
This can be achieved by setting up automated alerts or building regular reporting processes to ensure consistency and accuracy.
Benchmarking
Benchmarking raw material costs against industry standards gives a clear picture of where the business stands in terms of competitiveness.
This involves comparing your material costs with those of similar companies and identifying areas for improvement.
Budgeting and Forecasting
Accurate budgeting and forecasting are essential to prepare for future raw material needs.
Using historical data and trend analysis, purchasing departments can better predict future costs and adjust their strategies accordingly.
This proactive approach reduces the likelihood of unexpected expenses impacting the business.
The Role of Technology in Cost Management
Technology plays a vital role in modernizing the approach to raw material cost management.
Automation, artificial intelligence (AI), and blockchain are some of the technologies that can be leveraged to ensure more efficient and transparent procurement processes.
Automation
Automating purchase orders, invoice processing, and inventory management can reduce administrative costs and enhance accuracy.
This allows purchasing teams to focus on strategic sourcing initiatives rather than manual tasks.
Artificial Intelligence and Predictive Analytics
AI can be used to analyze large datasets, identify patterns, and predict cost trends.
Predictive analytics assists purchasing departments in anticipating price increases or stock shortages, allowing for timely action.
Blockchain for Supply Chain Transparency
Blockchain technology can enhance supply chain transparency by providing verifiable and tamper-proof records of transactions.
This helps in building trust with suppliers and ensuring that procurement processes are ethical and efficient.
Conclusion
Managing raw material costs effectively is a critical function of purchasing departments.
Through visualization, cost reduction techniques, and the adoption of technology, businesses can better control these expenses.
By continuously monitoring and analyzing costs, purchasing teams can make informed decisions that contribute to the company’s bottom line.
Implementing these strategies equates to not only reducing expenses but also optimizing the value derived from every dollar spent on raw materials.
資料ダウンロード
QCD調達購買管理クラウド「newji」は、調達購買部門で必要なQCD管理全てを備えた、現場特化型兼クラウド型の今世紀最高の購買管理システムとなります。
ユーザー登録
調達購買業務の効率化だけでなく、システムを導入することで、コスト削減や製品・資材のステータス可視化のほか、属人化していた購買情報の共有化による内部不正防止や統制にも役立ちます。
NEWJI DX
製造業に特化したデジタルトランスフォーメーション(DX)の実現を目指す請負開発型のコンサルティングサービスです。AI、iPaaS、および先端の技術を駆使して、製造プロセスの効率化、業務効率化、チームワーク強化、コスト削減、品質向上を実現します。このサービスは、製造業の課題を深く理解し、それに対する最適なデジタルソリューションを提供することで、企業が持続的な成長とイノベーションを達成できるようサポートします。
オンライン講座
製造業、主に購買・調達部門にお勤めの方々に向けた情報を配信しております。
新任の方やベテランの方、管理職を対象とした幅広いコンテンツをご用意しております。
お問い合わせ
コストダウンが利益に直結する術だと理解していても、なかなか前に進めることができない状況。そんな時は、newjiのコストダウン自動化機能で大きく利益貢献しよう!
(Β版非公開)