- お役立ち記事
- Wafer Manufacturing Technology and Its Industrial Applications
月間76,176名の
製造業ご担当者様が閲覧しています*
*2025年3月31日現在のGoogle Analyticsのデータより
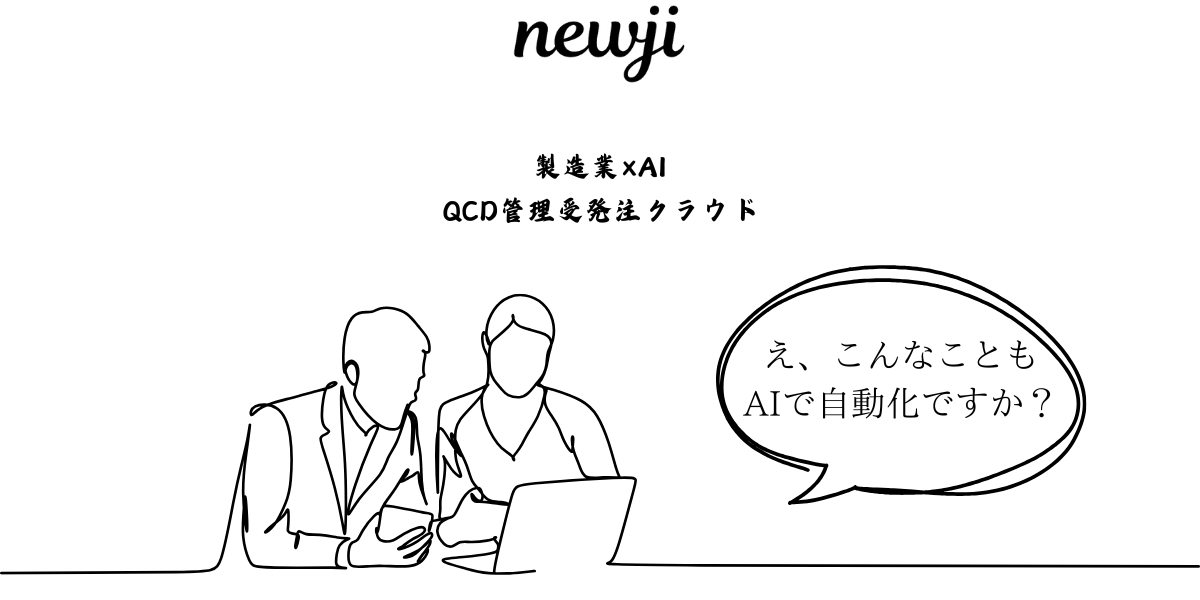
Wafer Manufacturing Technology and Its Industrial Applications
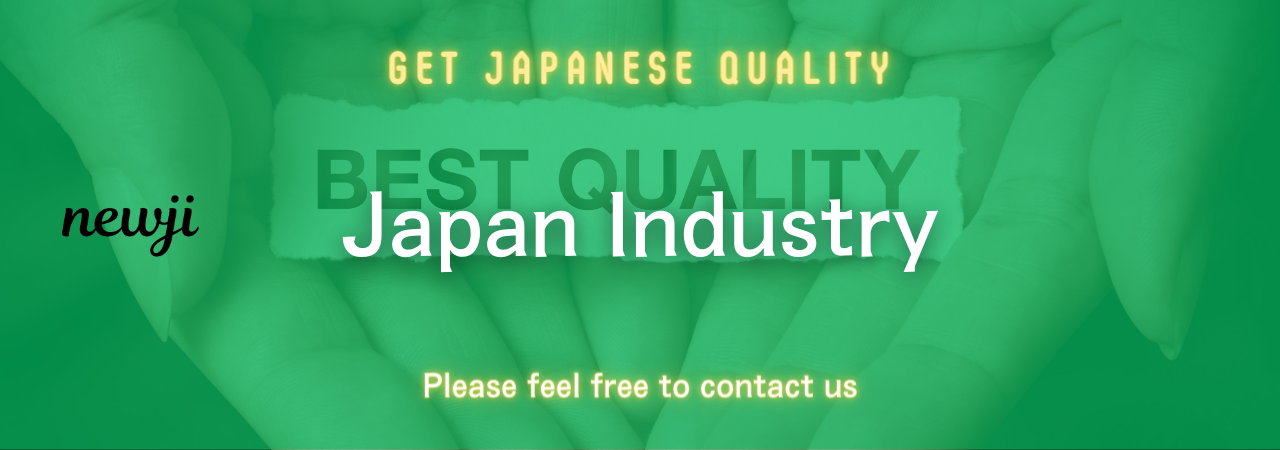
Wafer manufacturing technology is a crucial component in the production of various electronic devices, including semiconductors and integrated circuits (ICs).
This sophisticated process has propelled advancements in many industries, from telecommunications to consumer electronics.
Understanding how wafers are manufactured and their multiple industrial applications is essential for grasping the technological progress shaping our world.
目次
What is Wafer Manufacturing?
Wafer manufacturing involves the creation of thin slices of semiconductor material, typically silicon, known as wafers.
These wafers serve as the foundational substrate for fabricating microelectronic devices.
The process starts with refined silicon, which is then crystallized into a cylindrical ingot.
This ingot is sliced into thin discs or wafers, polished to a mirror-like smoothness, and then processed to create various electronic components.
The Silicon Ingot
The journey of wafer manufacturing begins with purified silicon, usually extracted from sand or quartz.
This pure silicon is melted in a crucible at high temperatures to create a molten state.
From this, a seed crystal is carefully introduced and slowly drawn upward, forming a large cylindrical crystal known as an ingot.
Slicing and Polishing
Once the silicon ingot is formed, it is mechanically sliced into thin discs.
These initial wafers are typically rough and uneven.
Therefore, each wafer undergoes lapping and polishing to achieve the required thickness and a flawless surface.
This polished surface is vital for the subsequent layering of electronic components.
Photolithography and Etching
After slicing and polishing, wafers are ready for photolithography and etching, which are crucial steps in defining intricate circuit patterns.
Photolithography
Photolithography is akin to traditional photography.
A light-sensitive photoresist layer is applied to the wafer’s surface.
Using a photomask, the wafer is exposed to light.
The exposed areas undergo chemical changes, creating a pattern which will be developed using etching techniques.
Etching
Etching removes selected portions of the wafer’s surface to create the required circuit patterns.
This can be done through either wet etching, involving liquid chemicals, or dry etching, which uses gases or plasma.
The patterns carved out via etching form the complex pathways necessary for semiconductor functionality.
Layer Deposition Techniques
To build functioning electronic devices, multiple layers of various materials need to be deposited on the wafer.
Physical Vapor Deposition (PVD)
PVD is a technique where material is vaporized in a vacuum and then condensed onto the wafer’s surface.
This process results in thin film layers of metals or insulators.
PVD is essential for creating conductive pathways and insulating layers within the wafer.
Chemical Vapor Deposition (CVD)
CVD involves depositing a material onto the wafer by means of chemical reactions from gas-phase precursors.
This method is particularly useful for depositing insulating or semiconductor layers, contributing to the device’s overall functionality.
Testing and Dicing
Once the wafer has undergone photolithography, etching, and layer deposition, it needs to be tested for quality assurance before being cut into individual units.
Electrical Testing
Each wafer is subjected to rigorous electrical testing to verify the functionality of the microelectronic circuits.
Probes test the connectivity and performance characteristics of each circuit, allowing manufacturers to identify defective units.
Dicing
After passing quality tests, the wafer is then diced into individual dies or chips.
These are the final electronic components that will be packaged and integrated into various electronic devices.
The precision in dicing ensures that each chip remains intact and functional.
Industrial Applications of Wafer Technology
Wafer manufacturing technology has catalyzed innovation across multiple industries, creating a foundation for modern electronics.
Consumer Electronics
From smartphones to televisions, consumer electronics rely heavily on silicon wafers for their performance.
The intricate circuits enabled by wafers are fundamental to the functioning of processors, memory chips, and various other components that make up these devices.
Telecommunications
Telecommunication networks depend on semiconductors for signal processing and data transmission.
Silicon wafers are integral to the development of these communication devices, ensuring reliability and efficiency in data handling.
Automotive Industry
Modern vehicles are equipped with numerous electronic systems that enhance performance and safety.
From engine control units (ECUs) to advanced driver-assistance systems (ADAS), wafers play a critical role in automotive technology.
Medical Devices
The medical sector has also seen significant advancements due to wafer technology.
Devices like MRI machines, pacemakers, and various diagnostic tools incorporate semiconductor components that improve their efficiency and effectiveness.
The Future of Wafer Manufacturing
The continuous development in wafer manufacturing technology promises even greater advancements in the future.
Miniaturization
As the demand for smaller, more powerful devices grows, wafer technology is advancing towards creating smaller, more efficient circuits.
Innovations in photolithography and materials science are paving the way for further miniaturization.
3D Integration
3D integration involves stacking multiple layers of circuits vertically, enhancing performance and reducing the footprint of electronic components.
This approach is particularly promising for high-performance computing and data storage applications.
Materials Beyond Silicon
While silicon remains the dominant material, research is ongoing into alternative materials like gallium nitride (GaN) and silicon carbide (SiC).
These materials offer superior performance for certain applications, particularly where high power and efficiency are required.
In conclusion, wafer manufacturing technology is integral to the production of modern electronic devices.
Its development has fueled advancements across numerous industries, facilitating progress in telecommunications, consumer electronics, automotive sectors, and beyond.
As technology continues to evolve, we can expect further innovations in wafer manufacturing, propelling us towards an even more interconnected and efficient future.
資料ダウンロード
QCD管理受発注クラウド「newji」は、受発注部門で必要なQCD管理全てを備えた、現場特化型兼クラウド型の今世紀最高の受発注管理システムとなります。
ユーザー登録
受発注業務の効率化だけでなく、システムを導入することで、コスト削減や製品・資材のステータス可視化のほか、属人化していた受発注情報の共有化による内部不正防止や統制にも役立ちます。
NEWJI DX
製造業に特化したデジタルトランスフォーメーション(DX)の実現を目指す請負開発型のコンサルティングサービスです。AI、iPaaS、および先端の技術を駆使して、製造プロセスの効率化、業務効率化、チームワーク強化、コスト削減、品質向上を実現します。このサービスは、製造業の課題を深く理解し、それに対する最適なデジタルソリューションを提供することで、企業が持続的な成長とイノベーションを達成できるようサポートします。
製造業ニュース解説
製造業、主に購買・調達部門にお勤めの方々に向けた情報を配信しております。
新任の方やベテランの方、管理職を対象とした幅広いコンテンツをご用意しております。
お問い合わせ
コストダウンが利益に直結する術だと理解していても、なかなか前に進めることができない状況。そんな時は、newjiのコストダウン自動化機能で大きく利益貢献しよう!
(β版非公開)