- お役立ち記事
- We quantify the client’s feeling of using the actual machine and thoroughly explain specific measures for improving parts and how to implement them based on the initial evaluation.
月間76,176名の
製造業ご担当者様が閲覧しています*
*2025年3月31日現在のGoogle Analyticsのデータより
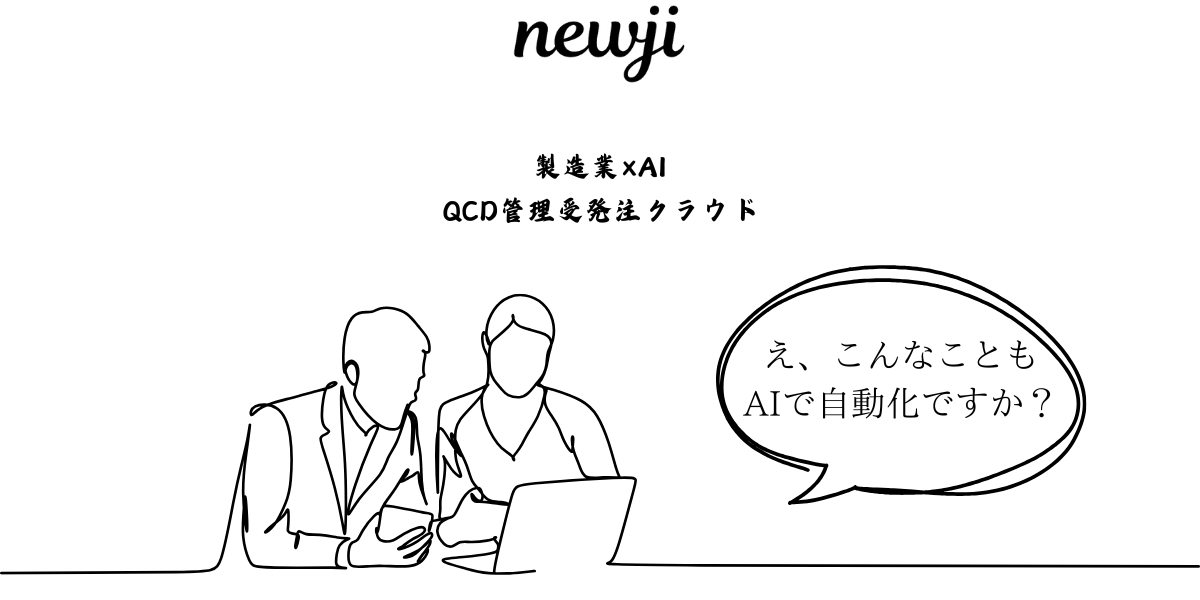
We quantify the client’s feeling of using the actual machine and thoroughly explain specific measures for improving parts and how to implement them based on the initial evaluation.
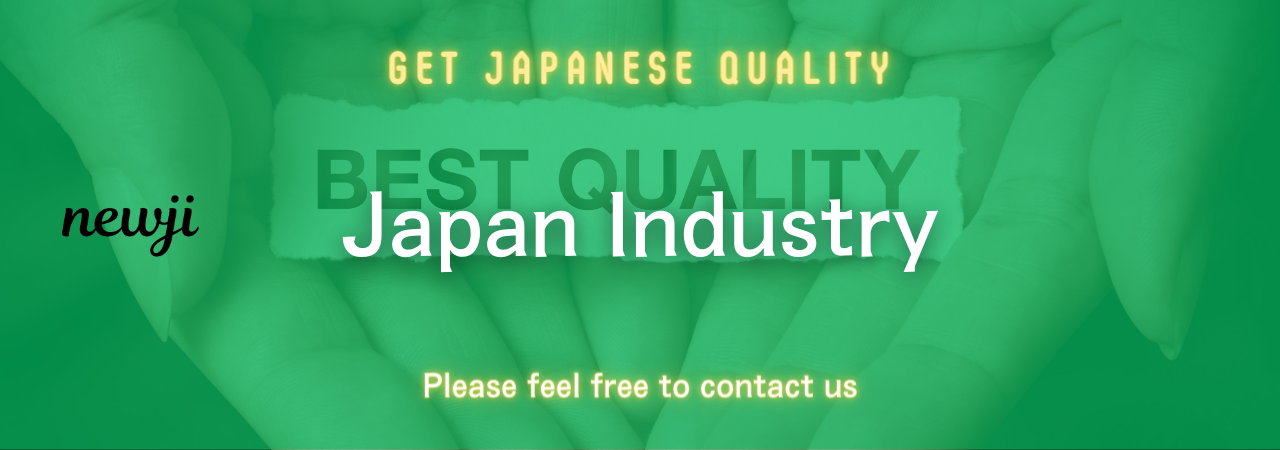
目次
Understanding Client Feedback on the Actual Machine
When a client uses an actual machine, their experience can be quite informative.
Quantifying their feelings and impressions is essential for improving the machine’s performance and functionality.
In this discussion, we delve into how you can extract valuable insights from client feedback to make informed improvements.
Initial Client Evaluation
The first step in understanding client feedback is through an initial evaluation.
This process usually involves collecting data on the client’s first impression and overall satisfaction with the machine.
Conducting surveys or interviews shortly after their use can capture their genuine reactions.
In these evaluations, it’s vital to focus on specific aspects such as ease of use, efficiency, and reliability.
For instance, asking about the machine’s speed or how straightforward it was to operate can yield actionable feedback.
Encouraging detailed responses ensures that each comment can help guide enhancement projects.
Quantifying Client Feedback
Once you have gathered feedback, it’s time to quantify it.
Quantifying involves categorizing responses and turning qualitative data into quantitative metrics.
This might include translating comments like “The machine was slow” into a measurable performance attribute.
Analytical tools can assist in this process by evaluating sentiment and identifying key themes.
Using scales or scores, like a 1 to 5 rating, can also simplify various client feelings into understandable data points.
Software solutions are available to automate these analytics, smoothing the transition from raw feedback to structured input.
Identifying Areas for Improvement
With quantified feedback in hand, the next step is pinpointing specific parts of the machine that require attention.
Analyzing which aspects received negative or below-average scores can highlight potential weaknesses.
For example, if clients noted frequent breakdowns or malfunctions, it might signal the need to enhance durability.
Similarly, if complicated interfaces are common complaints, simplifying the design could make the machine more user-friendly.
It’s important to prioritize these areas based on impact and feasibility.
Not all improvements can be tackled at once, so focus on those that promise the highest return on investment first.
Implementing Specific Improvements
After identifying areas for improvement, strategize the implementation of these changes.
This process often involves collaboration between various teams including engineering, design, and marketing.
Start by defining clear objectives for each improvement.
For instance, if enhancing durability is the goal, set a target for the machinery’s lifespan.
Design teams can then work on material alterations or structural adjustments to meet these targets.
Prototyping and testing are integral to this phase.
By developing prototypes, you can test out modifications before wide-scale implementation.
These tests should focus on whether the changes effectively resolve the identified issues without introducing new problems.
Measuring Post-Improvement Success
Once improvements are implemented, the work is not over.
It’s essential to measure the success of these changes to ensure they meet the desired outcomes.
Conduct follow-up evaluations with clients to gather their reactions to the improved machine.
Compare the new feedback data to the initial evaluation to assess progress in critical areas.
Look at whether there is a noticeable shift in ratings for ease of use, speed, or satisfaction.
Utilize customer reviews and ratings to reflect broader sentiment beyond direct client feedback.
Monitoring these can provide ongoing insights and help maintain continuous improvement efforts.
Continuous Feedback Loop
Improving a machine isn’t a one-time affair but a continuous process.
Establishing a feedback loop where ongoing client evaluations feed back into regular updates ensures the machine stays relevant and effective.
Maintain an open channel for feedback through surveys or customer support interactions.
Regularly engage with clients to understand evolving needs or emerging challenges they face.
Being proactive in soliciting feedback not only shows customers that their input is valued but also positions your product at the forefront of innovation by keeping pace with current demands.
Conclusion
Quantifying client feedback from their use of the actual machine plays a pivotal role in elevating performance and customer satisfaction.
From initial evaluation through to the implementation of improvements and measurement of success, each step in the process demands careful consideration and execution.
By maintaining a robust feedback loop, businesses can ensure that their machines not only meet current customer expectations but also adapt to future challenges.
Listening actively to clients and responding decisively is the cornerstone of sustained growth and development.
資料ダウンロード
QCD管理受発注クラウド「newji」は、受発注部門で必要なQCD管理全てを備えた、現場特化型兼クラウド型の今世紀最高の受発注管理システムとなります。
ユーザー登録
受発注業務の効率化だけでなく、システムを導入することで、コスト削減や製品・資材のステータス可視化のほか、属人化していた受発注情報の共有化による内部不正防止や統制にも役立ちます。
NEWJI DX
製造業に特化したデジタルトランスフォーメーション(DX)の実現を目指す請負開発型のコンサルティングサービスです。AI、iPaaS、および先端の技術を駆使して、製造プロセスの効率化、業務効率化、チームワーク強化、コスト削減、品質向上を実現します。このサービスは、製造業の課題を深く理解し、それに対する最適なデジタルソリューションを提供することで、企業が持続的な成長とイノベーションを達成できるようサポートします。
製造業ニュース解説
製造業、主に購買・調達部門にお勤めの方々に向けた情報を配信しております。
新任の方やベテランの方、管理職を対象とした幅広いコンテンツをご用意しております。
お問い合わせ
コストダウンが利益に直結する術だと理解していても、なかなか前に進めることができない状況。そんな時は、newjiのコストダウン自動化機能で大きく利益貢献しよう!
(β版非公開)