- お役立ち記事
- Weaving Innovation: How the Digital Thread Transforms Japanese Manufacturing
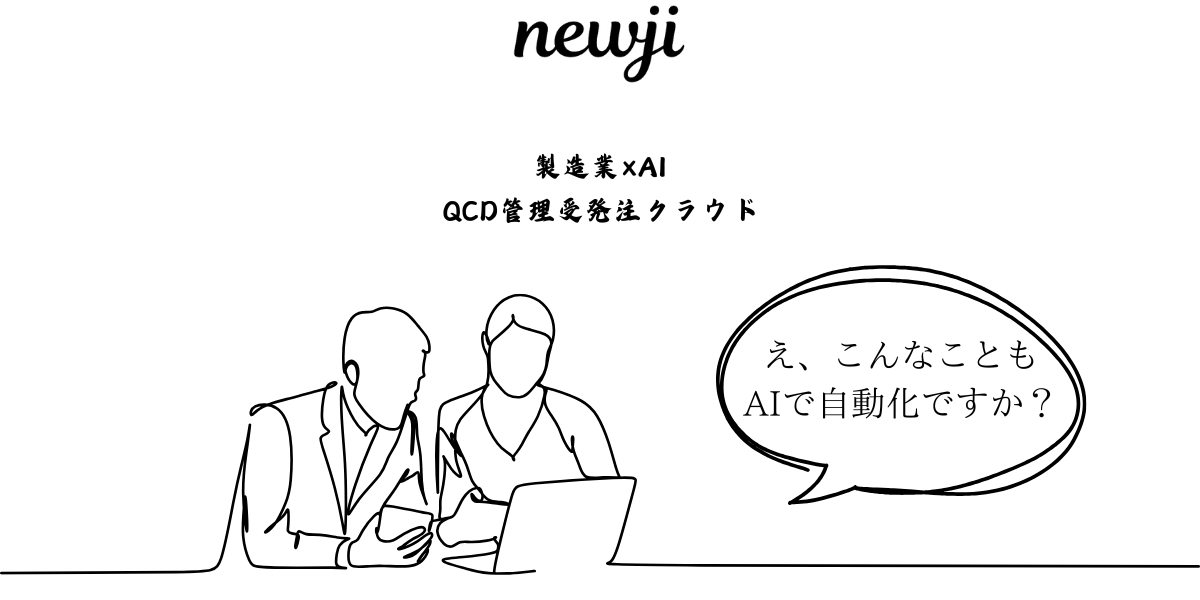
Weaving Innovation: How the Digital Thread Transforms Japanese Manufacturing
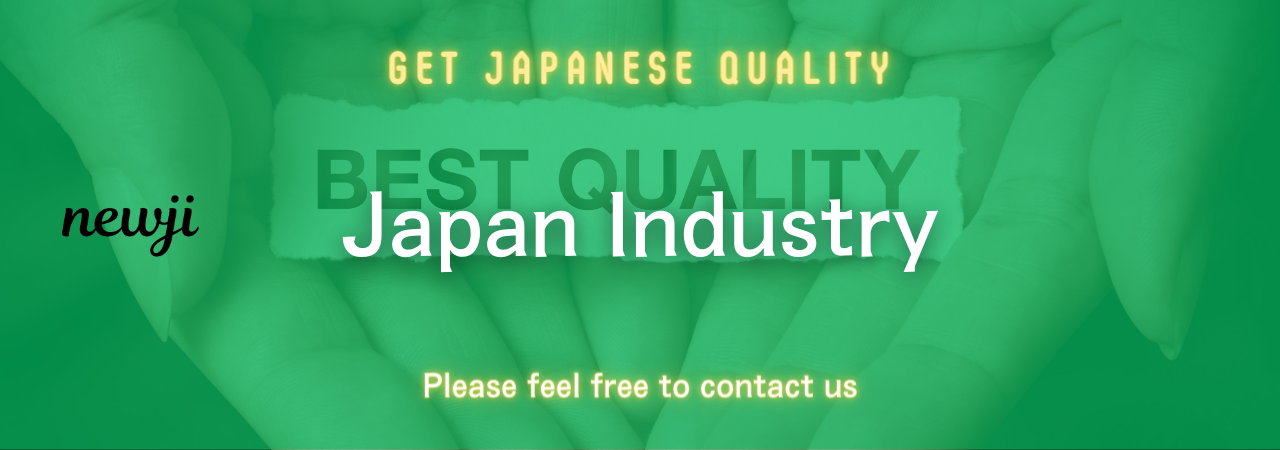
目次
Introduction to the Digital Thread in Japanese Manufacturing
The manufacturing landscape is undergoing a significant transformation driven by digitalization. Among the most impactful innovations is the concept of the digital thread, a framework that integrates data and processes across the entire lifecycle of a product. In Japanese manufacturing, renowned for its precision and efficiency, the digital thread is weaving innovation into every aspect of production. This transformation not only enhances operational efficiency but also redefines procurement and purchasing strategies, supplier relationships, and overall market competitiveness.
Understanding the Digital Thread
The digital thread refers to a seamless flow of data that connects all stages of a product’s lifecycle, from initial design and engineering to production, maintenance, and end-of-life disposal. It provides a continuous stream of information that ensures consistency, traceability, and real-time collaboration across different departments and stakeholders.
Components of the Digital Thread
The digital thread comprises several key components:
– **Data Integration:** Centralizing data from various sources such as CAD models, production plans, and quality control systems.
– **Real-Time Analytics:** Utilizing data analytics to monitor and optimize processes continuously.
– **Collaborative Platforms:** Enabling seamless communication and collaboration among different teams and suppliers.
– **Automation Tools:** Implementing automation in manufacturing processes to enhance efficiency and reduce human error.
Benefits of the Digital Thread
Implementing a digital thread offers numerous advantages:
– **Enhanced Efficiency:** Streamlining processes reduces waste and increases productivity.
– **Improved Quality Control:** Real-time monitoring allows for immediate identification and correction of defects.
– **Greater Agility:** Companies can quickly adapt to market changes and customer demands.
– **Cost Savings:** Optimized processes and reduced downtime lead to significant cost reductions.
Digital Thread in Japanese Manufacturing
Japan’s manufacturing sector is renowned for its commitment to quality and continuous improvement. The adoption of the digital thread is a natural progression in maintaining this reputation while embracing modern technological advancements.
Integration with Lean Manufacturing
Many Japanese manufacturers have long embraced lean manufacturing principles, focusing on minimizing waste and maximizing value. The digital thread complements these principles by providing the data and tools necessary to identify inefficiencies and implement continuous improvements.
Cultural Alignment
The emphasis on teamwork and precision in Japanese corporate culture aligns well with the collaborative nature of the digital thread. This cultural synergy facilitates smoother implementation and more effective utilization of digital tools and processes.
Impact on Procurement and Purchasing
The digital thread significantly influences procurement and purchasing strategies, particularly when dealing with Japanese suppliers known for their high standards and reliability.
Enhanced Supplier Collaboration
With the digital thread, procurement teams can collaborate more effectively with suppliers. Real-time data sharing ensures transparency, allowing for better coordination and faster response times to changing demands or issues.
Improved Demand Forecasting
Access to comprehensive data through the digital thread enables more accurate demand forecasting. This precision helps in maintaining optimal inventory levels, reducing holding costs, and minimizing stockouts or overstock situations.
Streamlined Procurement Processes
Automating procurement processes through the digital thread reduces manual intervention, decreasing the likelihood of errors and speeding up transaction times. This efficiency is particularly beneficial when managing multiple suppliers and large volumes of transactions.
Advantages of Implementing the Digital Thread
Adopting the digital thread offers several significant benefits to Japanese manufacturers and their procurement departments.
Enhanced Traceability
The digital thread provides end-to-end traceability of products, materials, and components. This traceability is crucial for quality control, regulatory compliance, and addressing issues such as recalls or defects swiftly and effectively.
Increased Operational Transparency
Transparency across all stages of production and procurement processes fosters trust among stakeholders. It allows for better decision-making based on accurate and timely information.
Optimized Supply Chain Management
The integration of data across the supply chain enables better coordination and optimization. Manufacturers can identify bottlenecks, predict disruptions, and implement strategies to mitigate risks, ensuring a more resilient supply chain.
Challenges and Disadvantages
While the digital thread offers numerous advantages, its implementation also presents challenges that must be addressed to ensure successful adoption.
High Initial Investment
Implementing a digital thread requires significant upfront investment in technology, infrastructure, and training. This cost can be a barrier, especially for smaller manufacturers or those with limited budgets.
Data Security Concerns
The increased connectivity and data sharing inherent in the digital thread raise concerns about data security and privacy. Manufacturers must implement robust cybersecurity measures to protect sensitive information from breaches and unauthorized access.
Resistance to Change
Adopting new technologies often meets resistance from employees accustomed to traditional processes. Overcoming this resistance requires effective change management strategies, including training and clear communication of the benefits.
Supplier Negotiation Techniques in the Digital Era
Effective negotiation with Japanese suppliers is crucial for maintaining strong relationships and securing favorable terms. The digital thread enhances these negotiations by providing comprehensive data and insights.
Leveraging Data for Negotiations
Access to detailed production data and performance metrics allows procurement teams to negotiate based on factual evidence rather than assumptions. This approach fosters transparency and mutual trust between parties.
Collaborative Decision-Making
The digital thread facilitates a more collaborative approach to decision-making. By involving suppliers in the planning and optimization processes, both parties can work together to achieve common goals, such as reducing costs or improving quality.
Flexibility and Responsiveness
Real-time data enables procurement teams to respond quickly to changes in demand or supply conditions. This responsiveness allows for more dynamic negotiations, accommodating the needs of both the manufacturer and the supplier.
Market Conditions and the Digital Thread
The global manufacturing market is increasingly competitive and dynamic. The digital thread equips Japanese manufacturers to navigate these conditions effectively.
Global Supply Chain Complexity
As supply chains become more global and complex, managing them efficiently becomes challenging. The digital thread provides a centralized framework for overseeing and optimizing supply chain activities, ensuring smoother operations despite geographical and logistical complexities.
Demand for Customization
Customers increasingly demand customized products tailored to their specific needs. The digital thread enables manufacturers to offer personalized solutions by integrating design, production, and procurement processes seamlessly.
Sustainability and Regulatory Compliance
Sustainability is becoming a critical consideration in manufacturing. The digital thread aids in tracking environmental impact, ensuring compliance with regulations, and implementing sustainable practices throughout the product lifecycle.
Best Practices for Implementing the Digital Thread
Successful implementation of the digital thread requires careful planning and adherence to best practices to maximize benefits and mitigate challenges.
Comprehensive Planning and Strategy
Developing a clear strategy that outlines goals, required technologies, and implementation timelines is essential. This plan should align with the overall business objectives and consider the specific needs of the procurement and manufacturing departments.
Investing in the Right Technology
Selecting appropriate technologies that integrate seamlessly with existing systems is crucial. This includes choosing robust data management platforms, analytics tools, and collaborative software that support the digital thread framework.
Training and Development
Providing adequate training to employees ensures they are equipped to use new technologies and processes effectively. Continuous development programs help in maintaining a skilled workforce capable of leveraging the digital thread to its full potential.
Fostering a Culture of Collaboration
Encouraging a collaborative culture across all departments and with suppliers enhances the effectiveness of the digital thread. Open communication, shared objectives, and mutual respect are fundamental to successful collaboration.
Ensuring Data Quality and Integrity
Accurate and reliable data is the backbone of the digital thread. Implementing strict data governance policies and regular audits ensures data quality and integrity, which are critical for informed decision-making and operational efficiency.
Case Studies: Digital Thread in Action
Examining real-world examples of Japanese manufacturers that have successfully implemented the digital thread provides valuable insights into its practical applications and benefits.
Case Study 1: Toyota’s Integrated Production System
Toyota, a leader in manufacturing excellence, has integrated the digital thread into its production system. By connecting design, production, and supply chain data, Toyota has achieved remarkable efficiency and quality standards. Real-time data monitoring allows for immediate adjustments, minimizing waste and ensuring consistent product quality.
Case Study 2: Sony’s Product Lifecycle Management
Sony has leveraged the digital thread to enhance its product lifecycle management. From initial concept through to after-sales service, the seamless flow of information has enabled Sony to innovate rapidly, respond to market changes, and maintain high customer satisfaction levels.
Case Study 3: Panasonic’s Smart Factory Initiatives
Panasonic’s smart factories utilize the digital thread to automate processes and integrate various manufacturing stages. This integration has resulted in increased production speed, reduced errors, and improved flexibility in manufacturing operations, allowing Panasonic to meet diverse customer requirements efficiently.
Future Trends in Digital Thread and Japanese Manufacturing
The digital thread continues to evolve, shaping the future of Japanese manufacturing in several key areas.
Artificial Intelligence and Machine Learning
Integrating AI and machine learning with the digital thread can further enhance data analysis and decision-making processes. Predictive analytics can anticipate maintenance needs, optimize production schedules, and personalize customer experiences.
Internet of Things (IoT) Integration
The incorporation of IoT devices into the digital thread provides even more granular data from the production floor. This connectivity enhances real-time monitoring, automates data collection, and enables more sophisticated control over manufacturing processes.
Advanced Cybersecurity Measures
As the digital thread becomes more pervasive, ensuring robust cybersecurity measures will be paramount. Future developments will focus on enhancing data protection protocols to safeguard sensitive information against evolving cyber threats.
Conclusion
The digital thread is revolutionizing Japanese manufacturing by integrating data and processes across the entire product lifecycle. This transformation enhances efficiency, quality control, and supplier collaboration, positioning Japanese manufacturers to thrive in a competitive global market. While challenges such as high initial investments and data security concerns exist, adopting best practices and leveraging technology effectively can mitigate these issues. As the digital thread continues to evolve with advancements in AI, IoT, and cybersecurity, its impact on Japanese manufacturing will only grow, weaving a future of innovation and excellence.
資料ダウンロード
QCD調達購買管理クラウド「newji」は、調達購買部門で必要なQCD管理全てを備えた、現場特化型兼クラウド型の今世紀最高の購買管理システムとなります。
ユーザー登録
調達購買業務の効率化だけでなく、システムを導入することで、コスト削減や製品・資材のステータス可視化のほか、属人化していた購買情報の共有化による内部不正防止や統制にも役立ちます。
NEWJI DX
製造業に特化したデジタルトランスフォーメーション(DX)の実現を目指す請負開発型のコンサルティングサービスです。AI、iPaaS、および先端の技術を駆使して、製造プロセスの効率化、業務効率化、チームワーク強化、コスト削減、品質向上を実現します。このサービスは、製造業の課題を深く理解し、それに対する最適なデジタルソリューションを提供することで、企業が持続的な成長とイノベーションを達成できるようサポートします。
オンライン講座
製造業、主に購買・調達部門にお勤めの方々に向けた情報を配信しております。
新任の方やベテランの方、管理職を対象とした幅広いコンテンツをご用意しております。
お問い合わせ
コストダウンが利益に直結する術だと理解していても、なかなか前に進めることができない状況。そんな時は、newjiのコストダウン自動化機能で大きく利益貢献しよう!
(Β版非公開)