- お役立ち記事
- Web winding tension control technology and troubleshooting
月間76,176名の
製造業ご担当者様が閲覧しています*
*2025年3月31日現在のGoogle Analyticsのデータより
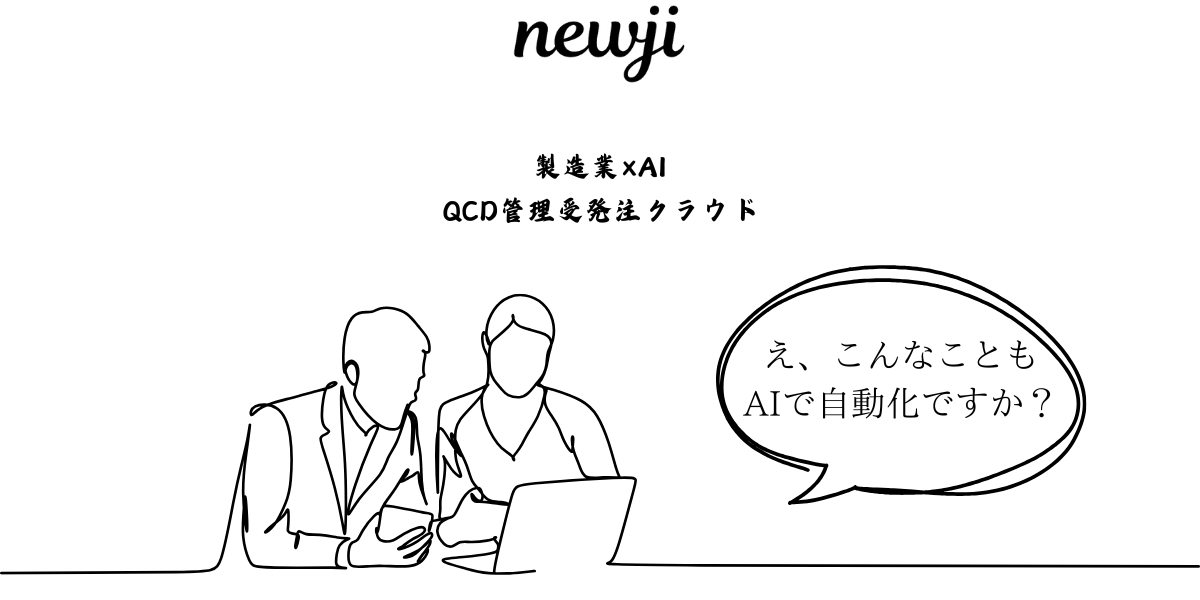
Web winding tension control technology and troubleshooting
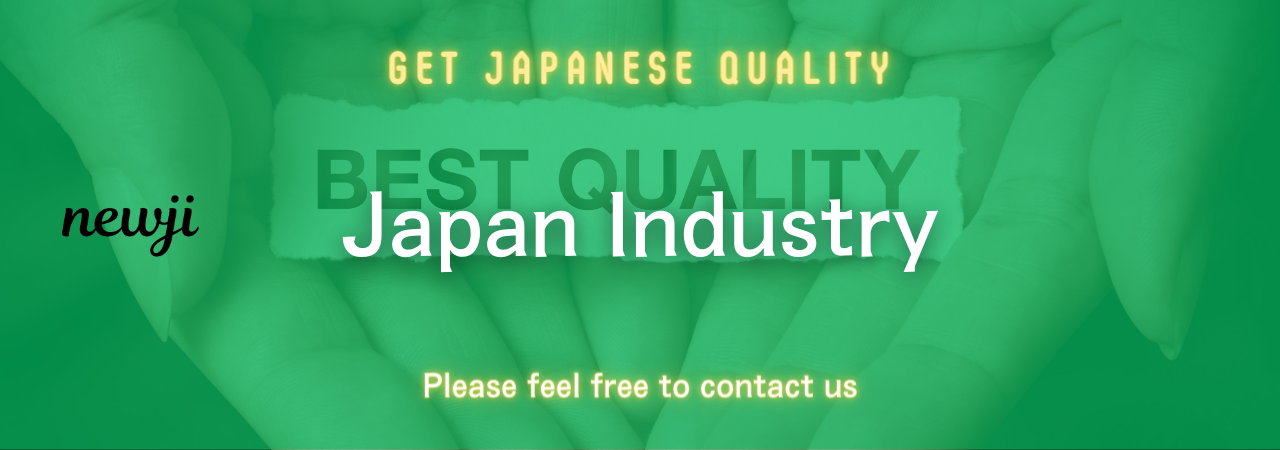
目次
Understanding Web Winding Tension Control
Web winding tension control is an essential aspect of manufacturing processes that involve materials such as paper, film, or foil wound onto rolls.
By managing the tension, manufacturers ensure the quality and consistency of the final product.
Without proper tension control, issues like wrinkles, creases, or even tears can occur, leading to material waste and additional costs.
Why Tension Control Matters
The primary goal of web winding tension control is to maintain a consistent tension throughout the winding process.
When tension is consistent, it prevents defects and ensures the rolled material is neither too tight nor too loose.
This balance is crucial because too much tension can stretch or tear the material, while too little can cause slackness, leading to wrinkles or uneven winding.
In manufacturing, tension control plays a critical role in aligning materials properly.
Improper tension can result in misalignment, especially in laminated products or materials that require precise overlapping.
By maintaining the right tension, manufacturers can reduce downtime caused by adjustments and repairs.
Components of Tension Control Systems
Tension control systems typically consist of several key components designed to regulate and monitor tension levels throughout the winding process.
These components work in tandem to achieve desired tension parameters.
Sensors and Load Cells
Sensors and load cells are critical for real-time feedback on tension levels.
They measure the tension applied on the web and send signals to the controller, ensuring adjustments can be made immediately.
Different types of sensors, such as ultrasonic or infrared, might be used depending on the material and process requirements.
Controllers
Controllers process the data received from sensors and adjust operational parameters accordingly.
They act as the brain of the tension control system, utilizing this information to maintain optimal tension.
Controllers can be programmed for specific material types and thicknesses, allowing for versatile applications in various industries.
Actuators
Actuators are responsible for making physical changes based on controller instructions.
They adjust elements like brakes, drives, or motors to increase or decrease tension.
Effective actuators are essential for prompt responses to any tension fluctuations detected by sensors.
Types of Tension Control Techniques
There are several techniques used in web winding tension control, each suited to different types of materials and production requirements.
Open Loop Tension Control
Open loop tension control does not rely on feedback from the tension being applied to the web.
Instead, it uses preset parameters to maintain consistent tension.
This method is generally suitable for materials with consistent properties, where little variation in thickness or elasticity is expected.
Closed Loop Tension Control
Closed loop tension control, in contrast, uses continuous feedback from sensors to adjust tension dynamically.
It is suitable for materials that may vary in properties during the process.
This method ensures precision in applications where material quality is variable or where high-quality end products are required.
Torque-Based Tension Control
Torque-based tension control uses the driving torque to regulate tension.
It adjusts the speed of winding or unwinding based on the torque required to maintain tension.
This method is widely used in applications where material properties might change, requiring precise tension adjustments.
Common Problems and Solutions
Despite the importance of tension control, several issues can arise during the winding process.
Understanding common problems and their solutions helps in maintaining smooth operations and ensuring product quality.
Wrinkles and Creases
Wrinkles and creases are among the most common problems caused by poor tension control.
They typically occur due to inconsistent tension or material misalignment.
To address this, ensure that sensors and controllers are properly calibrated and functioning.
Regular maintenance of the tension control system helps in preventing these issues.
Excessive Material Tension
Excessive tension can lead to material breakage or elongation.
Adjusting the controller settings to lower tension levels or employing a closed loop system can help in moderating tension appropriately.
It’s also crucial to regularly check sensors and actuators for proper functioning.
Inconsistent Roll Diameter
Inconsistent roll diameter is often a result of varying tension throughout the winding process.
Maintaining a consistent tension profile by using advanced controllers can prevent this.
Additionally, ensuring that the material is fed into the machine evenly and under the correct tension will help maintain uniform roll diameter.
Tips for Effective Tension Control
Achieving optimal web winding tension control involves both understanding system components and adopting best practices in operation.
Regular System Checks
Regularly checking and calibrating the tension control system ensures that all components are functioning correctly.
Monitor sensors, controllers, and actuators to prevent unexpected failures.
Customized Settings
Utilize customized settings based on specific material characteristics.
Program controllers to adapt to different materials, thicknesses, and production speeds to enhance tension control efficiency.
Employee Training
Train operators on the significance of tension control and how to employ system components effectively.
They should understand how to make real-time adjustments and recognize issues early, preventing defects and material waste.
By mastering web winding tension control technology, manufacturers can optimize their production processes, improve product quality, and reduce overall costs.
Understanding the intricacies of tension control is integral in the pursuit of superior manufacturing efficiency and product excellence.
資料ダウンロード
QCD管理受発注クラウド「newji」は、受発注部門で必要なQCD管理全てを備えた、現場特化型兼クラウド型の今世紀最高の受発注管理システムとなります。
ユーザー登録
受発注業務の効率化だけでなく、システムを導入することで、コスト削減や製品・資材のステータス可視化のほか、属人化していた受発注情報の共有化による内部不正防止や統制にも役立ちます。
NEWJI DX
製造業に特化したデジタルトランスフォーメーション(DX)の実現を目指す請負開発型のコンサルティングサービスです。AI、iPaaS、および先端の技術を駆使して、製造プロセスの効率化、業務効率化、チームワーク強化、コスト削減、品質向上を実現します。このサービスは、製造業の課題を深く理解し、それに対する最適なデジタルソリューションを提供することで、企業が持続的な成長とイノベーションを達成できるようサポートします。
製造業ニュース解説
製造業、主に購買・調達部門にお勤めの方々に向けた情報を配信しております。
新任の方やベテランの方、管理職を対象とした幅広いコンテンツをご用意しております。
お問い合わせ
コストダウンが利益に直結する術だと理解していても、なかなか前に進めることができない状況。そんな時は、newjiのコストダウン自動化機能で大きく利益貢献しよう!
(β版非公開)