- お役立ち記事
- Welding technology for prototype parts and measures to improve joint strength
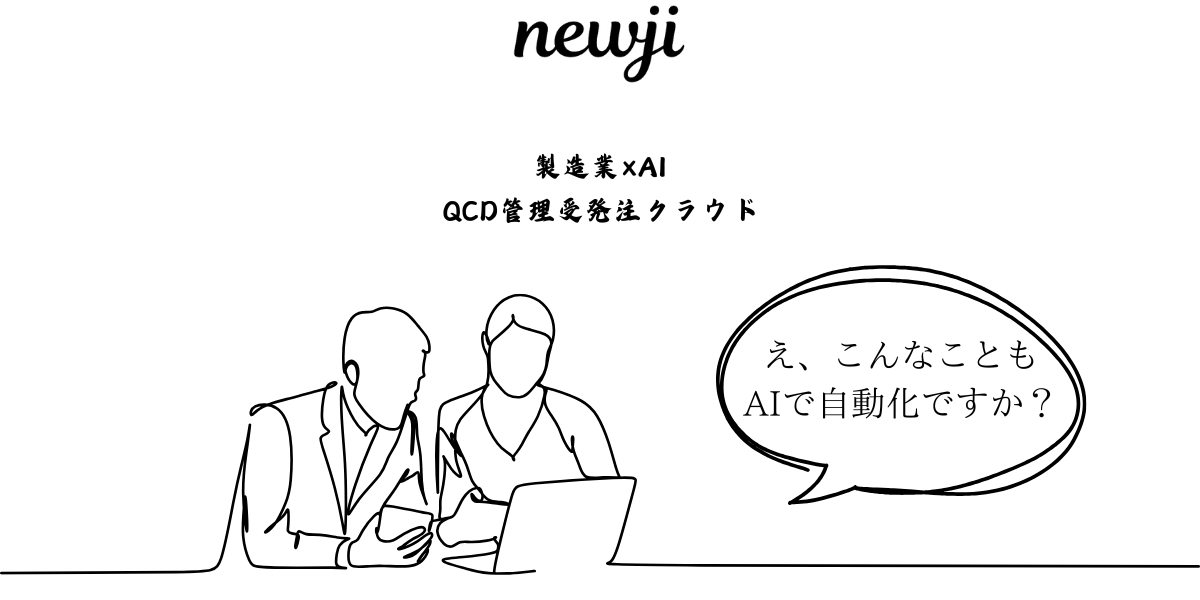
Welding technology for prototype parts and measures to improve joint strength
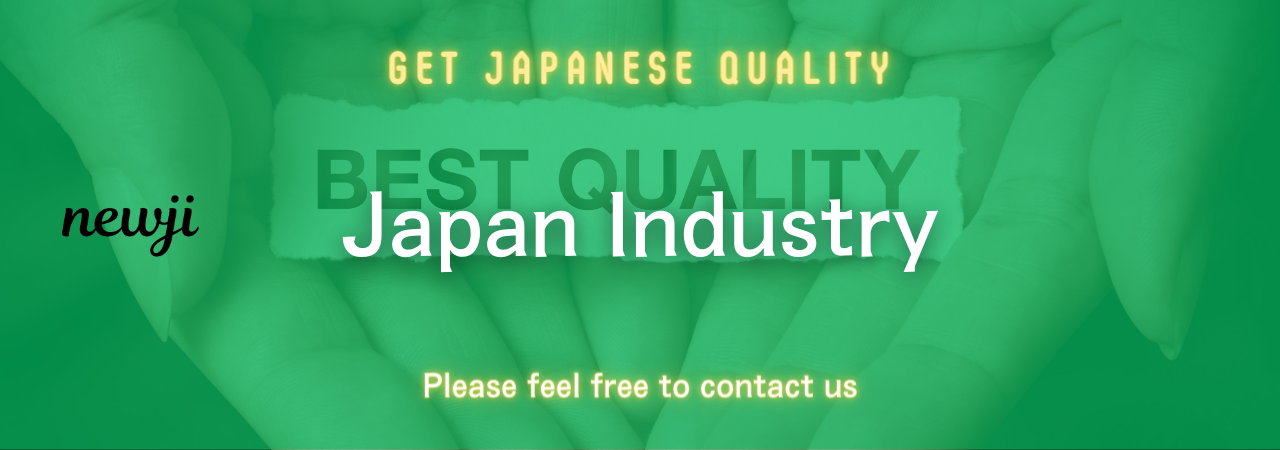
目次
Understanding Welding Technology for Prototype Parts
When it comes to creating prototype parts, selecting the right welding technology is crucial.
A prototype is a preliminary model of a product, used to evaluate design, test functionality, and refine ideas.
Welding, a fundamental process for joining materials, plays an essential role in creating durable and functional prototypes.
This article will explore the various welding technologies used for prototype parts and discuss strategies to improve joint strength.
Common Welding Technologies
Several welding technologies are largely used to create prototype parts.
Each has its own advantages and drawbacks, making it essential to select the right type based on specific requirements.
Here are some of the most common welding methods:
– **Arc Welding**:
This is a versatile technique that involves using an electric arc to create heat, which melts the metal at the joint.
Methods such as Shielded Metal Arc Welding (SMAW), Gas Metal Arc Welding (GMAW), and Tungsten Inert Gas (TIG) welding fall into this category.
Arc welding is suitable for various metals, including steel, aluminum, and copper, making it popular for prototypes.
– **Laser Beam Welding**:
Laser Beam Welding (LBW) is excellent for precise and small-scale prototype parts.
This technique uses a focused laser beam to join workpieces.
The high precision and speed of LBW make it suitable for intricate and delicate prototypes, primarily in the automotive and aerospace industries.
– **Resistance Welding**:
This process involves joining metals through resistance caused by the flow of electric current through the contact points.
Spot welding and seam welding are subtypes of resistance welding.
Due to its speed and efficiency, this technique is often used in the mass production of prototype parts.
– **Friction Stir Welding (FSW)**:
In FSW, the metallurgical phase of materials changes through frictional heat generated by a rotating tool.
This welding method is ideal for materials that are difficult to weld by fusion methods, such as aluminum alloys, and is commonly used in transportation and aerospace sectors.
Factors Affecting Joint Strength
The strength of a welded joint is vital to the performance of a prototype part.
Several factors influence joint strength, and understanding these can lead to more robust prototype designs:
– **Material Type**:
Different materials have different properties; hence, the choice of material impacts joint strength.
Certain metals weld together more easily than others.
For instance, aluminum requires precise control of welding parameters compared to steel.
– **Welding Design and Technique**:
The design of the joint, including its shape and the angle of the weld, plays a significant role in joint strength.
A well-planned design assignment often anticipates stress points and incorporates features to reduce them.
– **Weld Quality**:
The quality of the weld itself, which includes factors like penetration, bead appearance, and the presence of defects, directly affects the joint’s strength.
Ensuring consistent welding quality is vital, typically requiring skilled technicians or automated systems.
– **Environmental Conditions**:
Welding environments influence the joint’s durability.
Welding in controlled environments minimizes contaminants that could weaken the weld.
Exposure to extreme temperatures or corrosive environments post-welding also affects joint strength.
Measures to Improve Joint Strength
Improving joint strength ensures the reliability and longevity of prototype parts.
Here are some strategies to enhance weld quality and joint durability:
– **Pre-Welding Preparation**:
Proper preparation of materials and surfaces before welding is essential.
Clean surfaces free from rust, oil, and dirt, as these can lead to poor quality welds.
Proper fit-up preparation, including beveling and adjusting material alignment, ensures even distribution of weld material.
– **Controlled Welding Parameters**:
Adjusting welding parameters such as heat input, weld speed, and current can vastly improve joint strength.
For instance, in TIG welding, controlling the arc length and maintaining a consistent travel speed can prevent overheating and ensure deeper penetration.
– **Use of Filler Materials**:
Selecting appropriate filler materials that are compatible with the base materials can reinforce the joint.
Filler metals often come with additives or coatings that enhance weld properties.
– **Post-Welding Treatments**:
Post-weld heat treatment (PWHT) can relieve stress and reduce residual stresses in the weld area, helping in achieving stronger joints.
Employing techniques like peening or shot blasting post-welding also improves fatigue resistance.
– **Incorporating Advanced Techniques**:
Advanced methods such as Ultrasonic Additive Manufacturing (UAM) combine printing with bonding, promoting stronger joints in metal prototypes.
Exploring state-of-the-art welding technologies often results in better joint quality and overall performance.
Conclusion
Selecting the right welding technology and improving the joint strength significantly affects the success of prototype development.
Each welding method has unique features tailored to different material types, designs, and application needs.
With improved joint strength, prototypes perform better, affecting the final product’s reliability and quality.
Incorporating diligent preparation, precise control, and innovative techniques ensures that welded joints are not just robust, but optimal.
By understanding these elements, manufacturers can create high-quality prototypes that withstand functional testing and provide valuable insights for the final product development phase.
Investing in advanced welding technologies and refining joint-strengthening strategies ultimately leads to more successful product innovations.
資料ダウンロード
QCD調達購買管理クラウド「newji」は、調達購買部門で必要なQCD管理全てを備えた、現場特化型兼クラウド型の今世紀最高の購買管理システムとなります。
ユーザー登録
調達購買業務の効率化だけでなく、システムを導入することで、コスト削減や製品・資材のステータス可視化のほか、属人化していた購買情報の共有化による内部不正防止や統制にも役立ちます。
NEWJI DX
製造業に特化したデジタルトランスフォーメーション(DX)の実現を目指す請負開発型のコンサルティングサービスです。AI、iPaaS、および先端の技術を駆使して、製造プロセスの効率化、業務効率化、チームワーク強化、コスト削減、品質向上を実現します。このサービスは、製造業の課題を深く理解し、それに対する最適なデジタルソリューションを提供することで、企業が持続的な成長とイノベーションを達成できるようサポートします。
オンライン講座
製造業、主に購買・調達部門にお勤めの方々に向けた情報を配信しております。
新任の方やベテランの方、管理職を対象とした幅広いコンテンツをご用意しております。
お問い合わせ
コストダウンが利益に直結する術だと理解していても、なかなか前に進めることができない状況。そんな時は、newjiのコストダウン自動化機能で大きく利益貢献しよう!
(Β版非公開)