- お役立ち記事
- Wetsuit Manufacturing Process and Waterproofing Techniques
月間76,176名の
製造業ご担当者様が閲覧しています*
*2025年3月31日現在のGoogle Analyticsのデータより
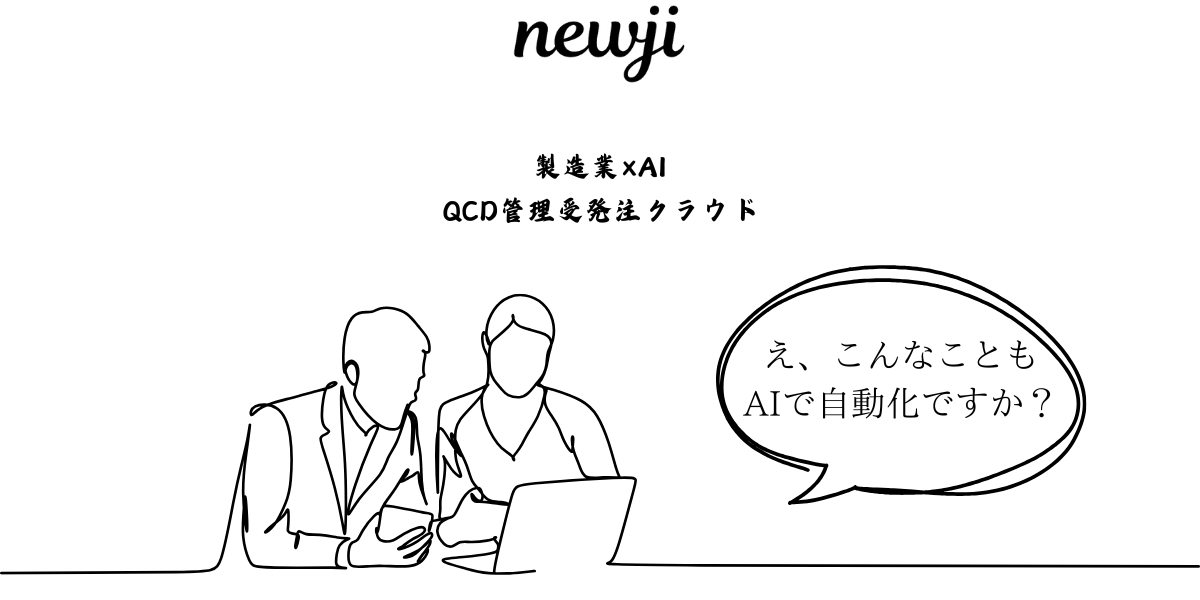
Wetsuit Manufacturing Process and Waterproofing Techniques
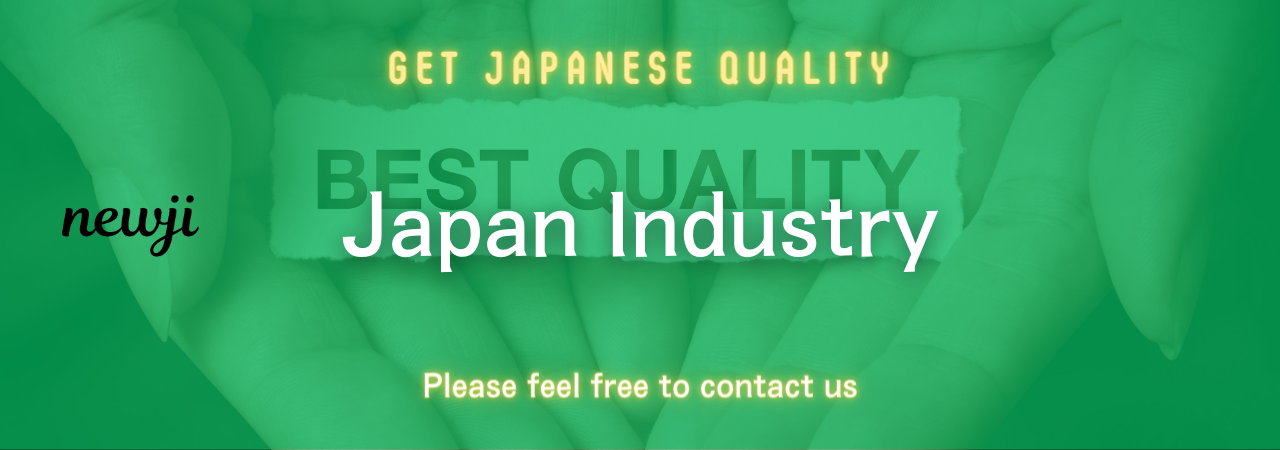
目次
Understanding the Basics of Wetsuit Manufacturing
When it comes to watersports, wetsuits play a crucial role in ensuring comfort and safety.
But have you ever wondered how these suits are made?
The wetsuit manufacturing process is intricate and requires a blend of technology and craftsmanship.
The primary material used in wetsuit production is neoprene.
Neoprene is a type of synthetic rubber that provides excellent insulation and flexibility.
It’s the core element that keeps surfers and divers warm in cold waters.
The Role of Neoprene in Wetsuits
The manufacturing journey begins with the production of neoprene sheets.
These are made by mixing and curing a combination of chemicals, creating a flexible and durable material.
Neoprene comes in various thicknesses, depending on the intended use of the wetsuit.
Once neoprene sheets are ready, they are laminated with nylon or polyester fabrics.
This lamination process enhances the suit’s strength and flexibility, making it more comfortable for prolonged use in water.
Cutting and Assembling the Wetsuit
Once the neoprene is laminated, the next step is cutting it into panels that will form the wetsuit.
These panels are meticulously cut according to specific patterns tailored for various sizes and designs.
Precision is key during this stage to ensure the suit fits perfectly.
After cutting, the panels are assembled through gluing and stitching.
Special waterproof glue is used to bond the seams of the panels.
This step is critical as it provides the primary waterproofing function.
The seams are then stitched with a technique known as blind stitching.
This method involves passing the needle through only part of the neoprene, maintaining the material’s integrity and preventing water from seeping through.
Types of Stitches Used
In wetsuit construction, the type of stitch used can significantly affect both comfort and durability.
The three most common stitches are flatlock, overlock, and blind stitch.
– **Flatlock Stitching**: Best for warm water suits, flatlock stitching involves overlapping the neoprene and stitching across both pieces.
While strong, it allows some water to seep through, so it’s typically used in suits meant for warmer climates.
– **Overlock Stitching**: This is less common in high-end wetsuits but works for economical suits.
The edges are rolled together and sewn, which can cause discomfort and isn’t as waterproof as other methods.
– **Blind Stitching**: For colder environments, blind stitching is preferred.
It’s both waterproof and durable, using a type of needle that doesn’t fully penetrate the neoprene, thus preventing leakage.
Waterproofing Techniques in Wetsuit Manufacturing
A key aspect of wetsuit design is ensuring the suit is as waterproof as possible.
Several techniques are employed to achieve this.
Seam Sealing
Apart from stitching, seam sealing adds an extra layer of waterproofing.
This involves applying a layer of liquid rubber or tape over the seams.
Liquid rubber seals the external surfaces, while tape adds a physical barrier to prevent water from entering.
Special Zippers
Another crucial component is the zipper.
Traditional zippers can be a point of water ingress, so many wetsuits employ specialized waterproof zippers.
These are often placed on the back of the suit and include a flap underneath, acting as a barrier against water.
Neck, Wrist, and Ankle Seals
Wetsuit design also includes seals at the neck, wrists, and ankles.
These seals are often made of smooth-skin neoprene, which clings to the skin and prevents water from flushing into the suit.
By minimizing the entry points for water, these seals are vital for maintaining warmth and comfort.
Advanced Features in Modern Wetsuits
As technology advances, so do the features in modern wetsuits.
Some newer designs offer added layers for thermal retention or anti-bacterial linings for hygiene.
These innovations enhance the overall experience, catering to both professional athletes and recreational swimmers.
Thermal Linings
Many high-end wetsuits now feature thermal linings that reflect body heat back, improving warmth without adding bulk.
These linings can make a crucial difference in colder waters, extending the duration one can comfortably stay submerged.
Environmental Considerations
In recent years, environmental concerns have led to the development of eco-friendly wetsuits.
Manufacturers are increasingly using limestone-based neoprene instead of petroleum-based varieties.
This switch reduces the carbon footprint of production, appealing to eco-conscious consumers.
Conclusion
Overall, the wetsuit manufacturing process involves a combination of materials and techniques aimed at maximizing comfort, durability, and waterproofing.
From the selection of neoprene to the final assembly and sealing, each step is critical.
With advancements in technology and an increasing focus on sustainability, the future of wetsuit design looks promising.
These versatile pieces of equipment keep us warm and safe in cold waters, enabling us to enjoy aquatic adventures to their fullest.
Whether surfing on the waves or exploring the depths of the ocean, a properly manufactured wetsuit is a quintessential component for anyone venturing into the water.
資料ダウンロード
QCD管理受発注クラウド「newji」は、受発注部門で必要なQCD管理全てを備えた、現場特化型兼クラウド型の今世紀最高の受発注管理システムとなります。
ユーザー登録
受発注業務の効率化だけでなく、システムを導入することで、コスト削減や製品・資材のステータス可視化のほか、属人化していた受発注情報の共有化による内部不正防止や統制にも役立ちます。
NEWJI DX
製造業に特化したデジタルトランスフォーメーション(DX)の実現を目指す請負開発型のコンサルティングサービスです。AI、iPaaS、および先端の技術を駆使して、製造プロセスの効率化、業務効率化、チームワーク強化、コスト削減、品質向上を実現します。このサービスは、製造業の課題を深く理解し、それに対する最適なデジタルソリューションを提供することで、企業が持続的な成長とイノベーションを達成できるようサポートします。
製造業ニュース解説
製造業、主に購買・調達部門にお勤めの方々に向けた情報を配信しております。
新任の方やベテランの方、管理職を対象とした幅広いコンテンツをご用意しております。
お問い合わせ
コストダウンが利益に直結する術だと理解していても、なかなか前に進めることができない状況。そんな時は、newjiのコストダウン自動化機能で大きく利益貢献しよう!
(β版非公開)