- お役立ち記事
- What is a Production Management System? Explaining the Benefits for SMEs in Manufacturing
What is a Production Management System? Explaining the Benefits for SMEs in Manufacturing
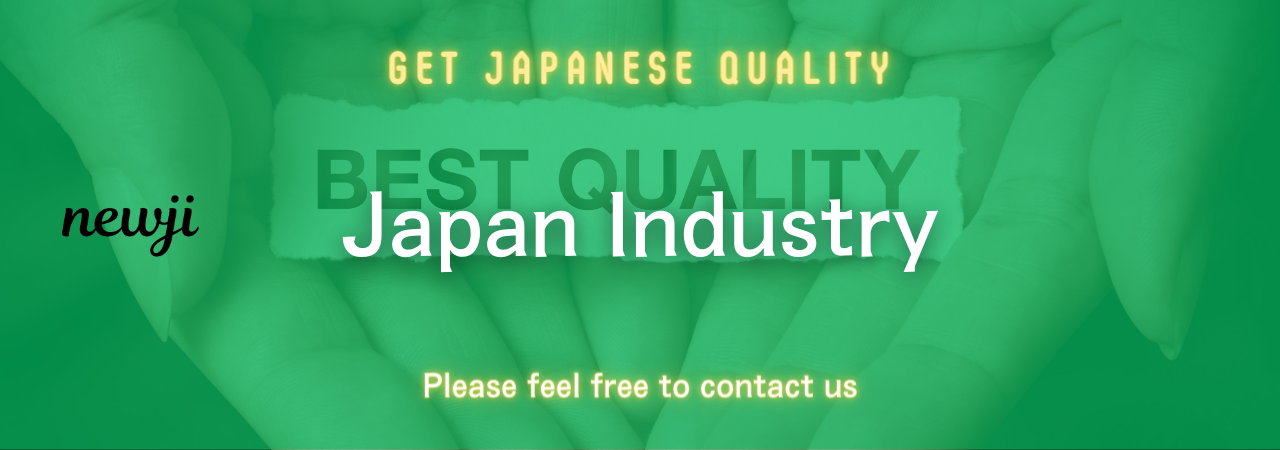
In today’s fast-paced manufacturing environment, small to medium-sized enterprises (SMEs) must maintain high efficiency and stay competitive.
One significant way to achieve this is through the implementation of a production management system.
So, what exactly is a production management system, and how can it benefit SMEs in the manufacturing sector?
Let’s take a closer look.
目次
Understanding Production Management Systems
A production management system is a framework that helps businesses plan, control, and monitor their production processes.
Think of it as a central hub that streamlines operations, ensuring everything runs smoothly from raw material procurement to the final delivery of products.
Whether you’re managing inventory levels, scheduling production runs, or tracking work-in-progress, a production management system integrates all these aspects into one cohesive platform.
Core Components of a Production Management System
Several key components make up an effective production management system.
Let’s explore them:
1. Inventory Management
Inventory management is a fundamental aspect of a production management system. It allows businesses to keep track of raw materials, work-in-progress items, and finished goods.
By accurately managing inventory levels, SMEs can reduce costs and avoid stockouts or overstocking issues.
2. Production Planning and Scheduling
Efficient production planning and scheduling ensure that manufacturing processes run smoothly.
This component helps allocate resources, set production targets, and maintain optimal workflow.
With an effective planning system, SMEs can minimize downtime and meet customer demands more efficiently.
3. Quality Control
Maintaining high-quality standards is crucial for any manufacturing business.
A good production management system includes quality control measures to detect and address defects early in the production process.
By ensuring consistent quality, SMEs can enhance customer satisfaction and reduce waste.
4. Real-Time Monitoring
Real-time monitoring provides instant visibility into production activities.
This feature allows managers to oversee operations, identify bottlenecks, and make informed decisions.
With real-time data, SMEs can respond quickly to changes and optimize production efficiency.
5. Reporting and Analytics
Detailed reporting and analytics enable businesses to track performance and identify areas for improvement.
A robust production management system provides insights into key metrics, such as production costs, lead times, and overall equipment effectiveness (OEE).
Armed with this information, SMEs can make data-driven decisions to drive growth and profitability.
Benefits of a Production Management System for SMEs
Implementing a production management system can bring numerous benefits to SMEs in the manufacturing sector.
Here are some of the most significant advantages:
Increased Efficiency
A well-implemented production management system streamlines processes and eliminates inefficiencies.
By automating routine tasks, businesses can focus on high-value activities, leading to increased productivity and faster production cycles.
Cost Reduction
Effective inventory management and optimized production scheduling can significantly reduce operational costs.
By minimizing waste and controlling expenses, SMEs can improve their bottom line and maintain a competitive edge.
Enhanced Quality
Consistent quality control measures ensure that products meet the required standards.
With fewer defects and rework, SMEs can build a reputation for reliability and earn customer trust.
Better Decision Making
Access to real-time data and comprehensive reports enables informed decision-making.
Managers can quickly identify issues, evaluate performance, and implement strategic improvements.
This proactive approach leads to better overall business performance.
Improved Customer Satisfaction
Meeting customer demands consistently and delivering high-quality products on time increases customer satisfaction.
With a production management system in place, SMEs can build stronger relationships with their clients and foster loyalty.
Choosing the Right Production Management System
Selecting the right production management system is crucial for reaping these benefits.
Here are some factors to consider when choosing a system for your SME:
Scalability
Ensure that the system can grow with your business.
A scalable solution will accommodate increasing production volumes and support expanding operations.
Ease of Use
The system should be user-friendly and easy to implement.
Look for intuitive interfaces and comprehensive training resources to ensure a smooth transition.
Integration Capabilities
Choose a system that can seamlessly integrate with your existing software and tools.
Compatibility with ERP, CRM, and other applications will enhance overall efficiency and reduce data silos.
Customization Options
Every business has unique requirements.
A customizable production management system allows you to tailor the solution to meet your specific needs and preferences.
Support and Maintenance
Reliable support and regular maintenance are essential for the long-term success of your production management system.
Evaluate the vendor’s reputation and service offerings to ensure you’ll receive the necessary assistance.
Conclusion
A production management system can transform the way SMEs in the manufacturing sector operate.
By integrating critical components such as inventory management, production planning, quality control, real-time monitoring, and reporting, these systems drive efficiency and cost savings.
The benefits are clear: increased productivity, reduced costs, enhanced quality, better decision-making, and improved customer satisfaction.
When selecting a system, consider factors like scalability, ease of use, integration capabilities, customization options, and support.
By choosing the right production management system, SMEs can position themselves for long-term success and stay competitive in the ever-evolving manufacturing landscape.
資料ダウンロード
QCD調達購買管理クラウド「newji」は、調達購買部門で必要なQCD管理全てを備えた、現場特化型兼クラウド型の今世紀最高の購買管理システムとなります。
ユーザー登録
調達購買業務の効率化だけでなく、システムを導入することで、コスト削減や製品・資材のステータス可視化のほか、属人化していた購買情報の共有化による内部不正防止や統制にも役立ちます。
NEWJI DX
製造業に特化したデジタルトランスフォーメーション(DX)の実現を目指す請負開発型のコンサルティングサービスです。AI、iPaaS、および先端の技術を駆使して、製造プロセスの効率化、業務効率化、チームワーク強化、コスト削減、品質向上を実現します。このサービスは、製造業の課題を深く理解し、それに対する最適なデジタルソリューションを提供することで、企業が持続的な成長とイノベーションを達成できるようサポートします。
オンライン講座
製造業、主に購買・調達部門にお勤めの方々に向けた情報を配信しております。
新任の方やベテランの方、管理職を対象とした幅広いコンテンツをご用意しております。
お問い合わせ
コストダウンが利益に直結する術だと理解していても、なかなか前に進めることができない状況。そんな時は、newjiのコストダウン自動化機能で大きく利益貢献しよう!
(Β版非公開)