- お役立ち記事
- What is the standard process for purchasing departments to assess the stability of material supply?
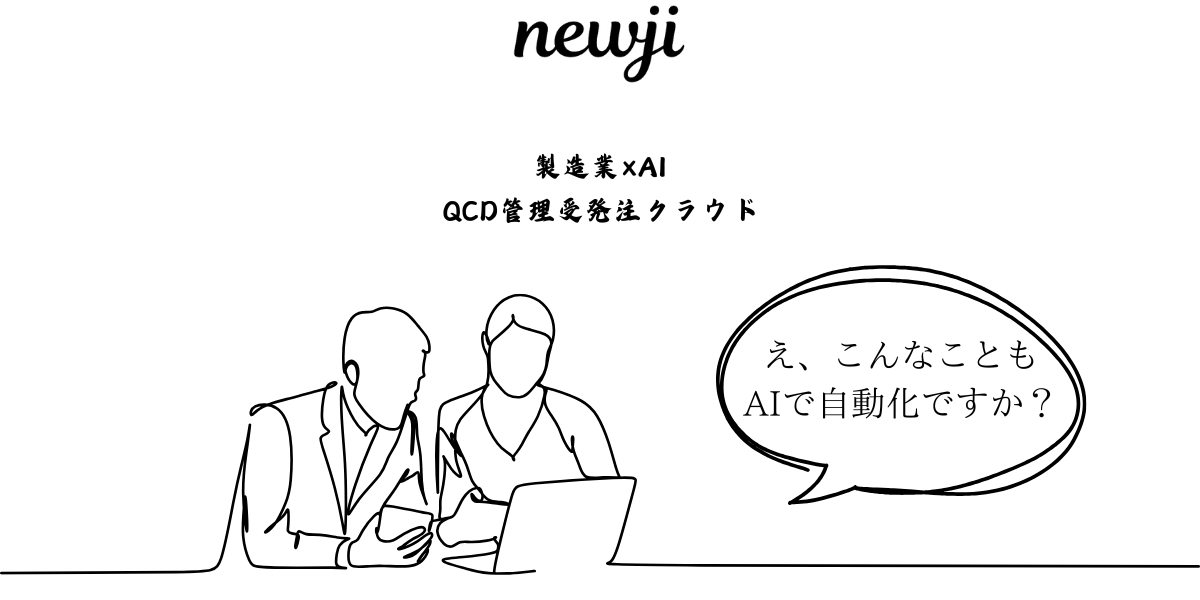
What is the standard process for purchasing departments to assess the stability of material supply?
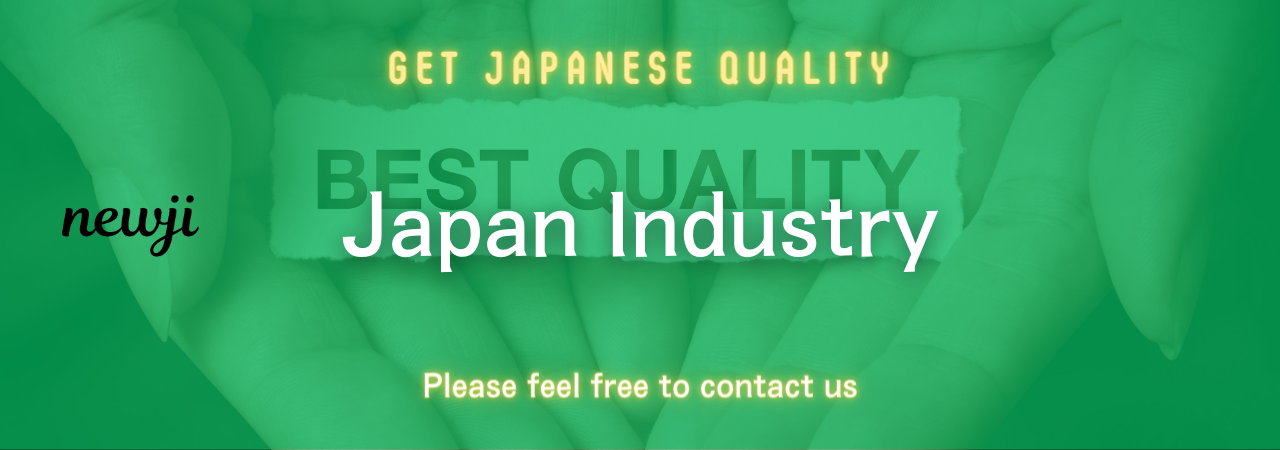
目次
Understanding the Purchasing Process in a Company
When it comes to running a successful business, maintaining a steady and reliable supply of materials is crucial.
This responsibility primarily falls on the purchasing department, which plays a vital role in assessing and ensuring the stability of material supply.
To help businesses maintain an efficient flow of resources, it is necessary to understand the standard processes these departments use.
Identifying Material Requirements
The first step in the purchasing process begins with identifying what the company requires.
Purchasing departments need to be aware of the materials necessary for production.
This involves collaborating with other departments such as production, research and development, and even sales to forecast material needs.
Having an accurate estimation reduces the chances of overstocking or shortages.
Supplier Identification and Evaluation
Once the material requirements are known, the next step is identifying potential suppliers.
A comprehensive evaluation is undertaken to determine which suppliers are capable of meeting the business’s needs.
Factors such as quality, cost, reliability, and delivery times are considered.
The department may request samples and conduct site visits to evaluate the supplier’s capacity and processes.
Establishing Supplier Relationships
A critical aspect of material supply stability is developing strong relationships with suppliers.
The purchasing department often negotiates terms and conditions that benefit both parties.
Having good supplier relationships can be advantageous in times of supply chain disruptions, ensuring preferential treatment or prioritization.
Price Negotiation
Negotiating the price is another vital step in the purchasing process.
The goal is to secure materials at the best possible price without compromising quality.
This involves negotiation skills and understanding market trends and material costs.
By keeping abreast of market conditions, purchasing departments maximize cost-efficiency, contributing to overall profitability.
Contract Management
After negotiating terms, formal contracts are drawn to define the supplier relationship.
Contracts cover all agreed-upon terms, including delivery schedules, quality standards, quantities, and payment conditions.
Clear documentation helps prevent misunderstandings and provides a reference point for future disputes or audits.
Monitoring and Evaluation
Continuously monitoring supplier performance is essential for ensuring the stability of material supply.
Purchasing departments evaluate their suppliers regularly based on agreed criteria like timeliness, adherence to quality, and response to issues.
This evaluation helps identify potential risks early and take proactive measures to mitigate them.
Risk Management
The purchasing department must also develop contingency plans and risk management strategies.
This involves identifying potential risks in the supply chain, such as geopolitical issues, fluctuating market prices, or natural disasters.
Having alternative suppliers or buffer stock can help maintain stability in material supplies during crises.
Inventory Management
Efficient inventory management is integral to maintaining a stable supply.
Purchasing departments collaborate with inventory teams to monitor stock levels and forecast demand accurately.
This helps prevent overstocking, which ties up capital, and understocking, which can halt production.
Supplier Audits and Quality Assurance
Conducting regular audits and quality checks on suppliers is important for maintaining material supply standards.
Purchasing departments establish quality protocols and ensure compliance through routine inspections and testing.
By doing so, they safeguard the company’s reputation and maintain product quality.
Technology and Automation
Modern purchasing departments leverage technology to streamline operations and improve decision-making.
Automation tools help manage large volumes of data, optimize procurement processes, and enhance supplier communication.
Using software for tracking orders, forecasting demand, and managing supplier relationships can lead to more efficient and stable supply chains.
Conclusion
The standard process for purchasing departments to assess the stability of material supply is multifaceted and involves careful strategy and proactive measures.
From understanding material needs and selecting suppliers to managing contracts and inventory, each step contributes to overall supply chain efficiency.
By adopting a comprehensive approach that includes risk management and technology integration, purchasing departments can ensure a robust and stable supply of materials, thereby supporting the organization’s goals and growth.
資料ダウンロード
QCD調達購買管理クラウド「newji」は、調達購買部門で必要なQCD管理全てを備えた、現場特化型兼クラウド型の今世紀最高の購買管理システムとなります。
ユーザー登録
調達購買業務の効率化だけでなく、システムを導入することで、コスト削減や製品・資材のステータス可視化のほか、属人化していた購買情報の共有化による内部不正防止や統制にも役立ちます。
NEWJI DX
製造業に特化したデジタルトランスフォーメーション(DX)の実現を目指す請負開発型のコンサルティングサービスです。AI、iPaaS、および先端の技術を駆使して、製造プロセスの効率化、業務効率化、チームワーク強化、コスト削減、品質向上を実現します。このサービスは、製造業の課題を深く理解し、それに対する最適なデジタルソリューションを提供することで、企業が持続的な成長とイノベーションを達成できるようサポートします。
オンライン講座
製造業、主に購買・調達部門にお勤めの方々に向けた情報を配信しております。
新任の方やベテランの方、管理職を対象とした幅広いコンテンツをご用意しております。
お問い合わせ
コストダウンが利益に直結する術だと理解していても、なかなか前に進めることができない状況。そんな時は、newjiのコストダウン自動化機能で大きく利益貢献しよう!
(Β版非公開)