- お役立ち記事
- What purchasing departments should know about how to reduce logistics costs by optimizing transportation methods
月間76,176名の
製造業ご担当者様が閲覧しています*
*2025年3月31日現在のGoogle Analyticsのデータより
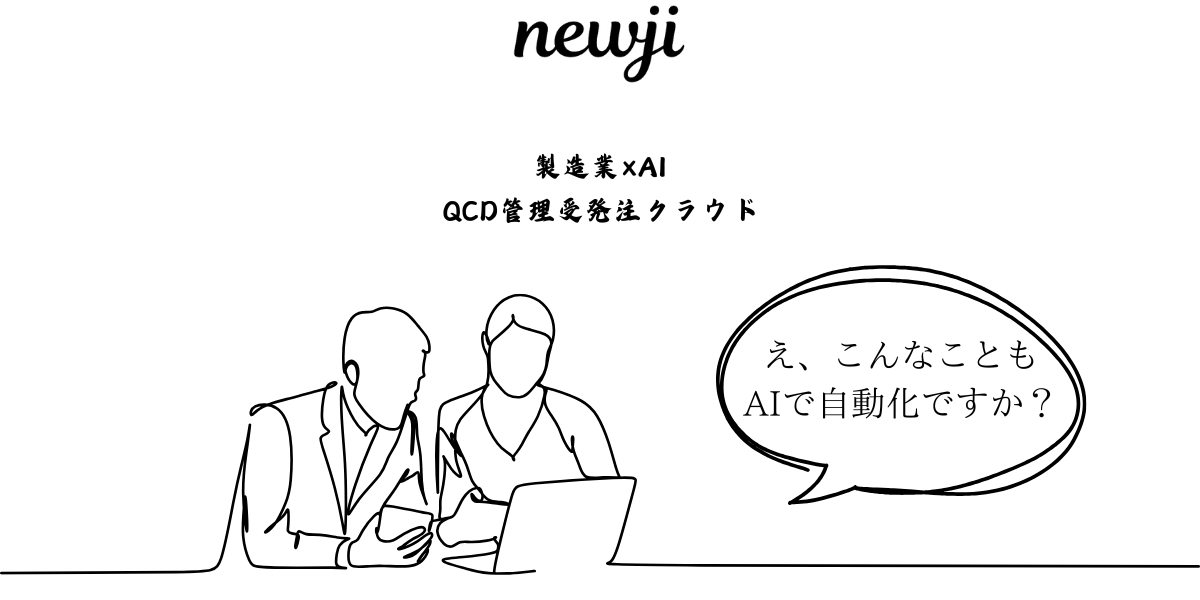
What purchasing departments should know about how to reduce logistics costs by optimizing transportation methods
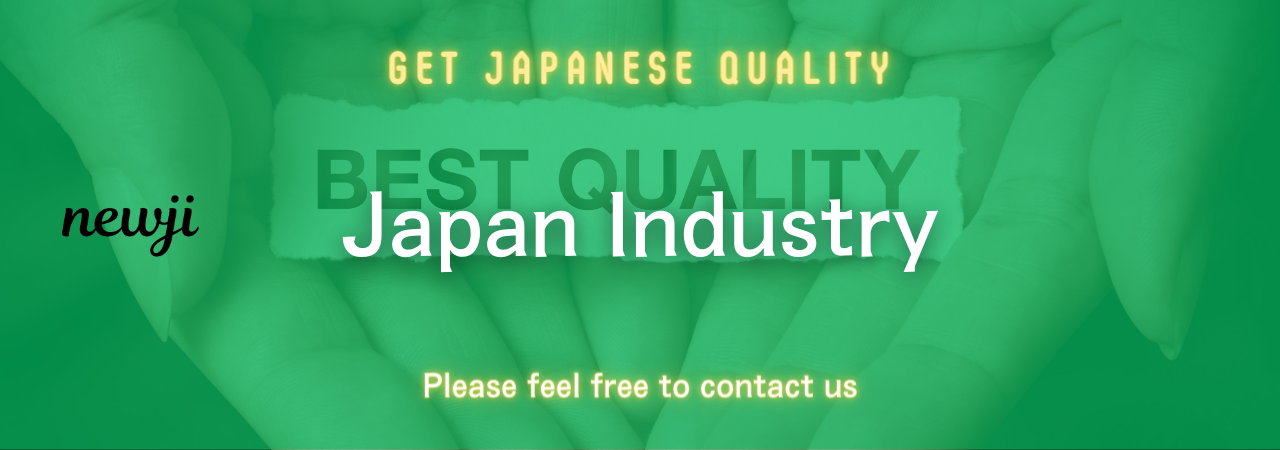
目次
Understanding Logistics Costs
Logistics costs are a significant component of a company’s overall expenditure.
For purchasing departments, these costs can often seem like an insurmountable challenge.
Yet, with an informed approach and strategic planning, they can be streamlined effectively.
The first step to reducing logistics costs is understanding the components that contribute to these expenses.
These can include transportation, warehousing, inventory management, and administrative costs.
Transportation expenses stand out as one of the most substantial parts of logistics costs.
Thus, a targeted focus on optimizing transportation methods can lead to considerable savings for the company.
The Importance of Optimizing Transportation Methods
Optimizing transportation methods is essential, as it directly affects the cost-efficiency of your logistics.
Smart logistics management prioritizes reducing excessive costs while maintaining or improving service quality.
Efficient transportation processes not only save money but also enhance customer satisfaction by ensuring timely deliveries.
Purchasing departments need to evaluate their transportation networks regularly to find opportunities for optimization.
This process involves analyzing routes, delivery modes, load sizes, and scheduling.
Evaluate Your Transportation Options
Transportation modes vary depending on the nature of the goods being shipped and the delivery timeline.
Common options include truck, rail, air, and sea transport.
Each mode has its advantages and limitations.
Truck transport is flexible and ideal for short distances, while rail can handle heavier loads over longer distances at a lower cost.
Air transport, although costly, is suitable for urgent shipments, and sea transport is best for large volumes with longer timelines.
Determining the best transportation mode requires a careful assessment of cost versus urgency and the nature of the shipment.
Consider Multimodal Transport Solutions
Multimodal transport integrates different transportation modes within a single contract, optimizing logistics for cost and speed.
By leveraging the strengths of various transport types, companies can optimize delivery routes and reduce costs.
For example, a combination of sea and rail transport can offer cost-effective long-haul solutions with a balance of time and expense.
Evaluating multimodal solutions helps purchasing departments to develop flexible and resilient transportation strategies.
Consolidate Shipments to Boost Efficiency
Consolidating shipments is an effective strategy to optimize transportation costs.
By grouping smaller shipments into a single larger load, companies can reduce the frequency of dispatches, lowering fuel and labor costs.
This approach also maximizes the use of available space and resources, reducing wastage.
Purchasing departments should coordinate closely with suppliers and partners to consolidate shipments effectively.
This collaboration ensures that shipments are combined without compromising delivery timelines or service quality.
Leverage Technology for Route Optimization
Technology plays a critical role in optimizing transportation routes.
Using software for route planning can help identify the most efficient paths, reducing distance, time, and fuel consumption.
Advanced logistics platforms offer data-driven insights that help purchasing departments make informed decisions about route selections.
Furthermore, real-time tracking and analytics tools enable proactive management of logistical issues.
This agility helps in maintaining the delivery schedule and improving overall efficiency.
Negotiate with Carriers and Establish Strategic Partnerships
Establishing strong relationships with carriers can lead to better negotiation outcomes for transportation costs.
Purchasing departments should regularly evaluate carrier performance and review contracts to ensure cost-effectiveness.
Negotiating better terms based on performance matrices can secure lower rates and improve service standards.
Forming strategic partnerships with reliable carriers enhances the company’s ability to handle logistical challenges seamlessly.
These partnerships often result in beneficial long-term agreements, including discounts and priority services.
Implement a Vendor-Managed Inventory (VMI) System
Vendor-managed inventory is an inventory control system wherein the supplier manages the inventory levels for the purchaser.
Implementing VMI can reduce overhead and logistics costs by transferring some supply chain responsibilities to the vendor.
This system allows for better inventory management, reduces stockouts, and improves order fulfilment.
Collaborating with vendors to implement VMI ensures that inventory levels align more closely with customer demand and production needs.
Embrace Sustainable Practices
Sustainability is becoming a necessity in logistics, reducing costs and improving the company’s environmental footprint.
Sustainable practices, such as optimizing vehicle load factors, maintaining proper tire pressure, and using alternative fuels, can significantly reduce transportation costs.
Additionally, using eco-friendly packaging materials can decrease weight and disposal costs.
Companies that prioritize sustainability often witness improved brand reputation and customer loyalty, which can indirectly impact logistics costs favorably.
Regularly Review and Adjust Logistics Strategies
The final step for purchasing departments is the continuous review and adjustment of logistics strategies.
Market conditions, fuel prices, and technological advancements can influence logistics efficiency.
Therefore, regular assessments and adjustments ensure that the logistics strategies remain cost-efficient and relevant.
Engaging in regular audits helps identify areas of improvement and allows for proactive management of any issues.
By staying informed and adaptable, purchasing departments can continue to find new methods to minimize logistics costs effectively.
Optimizing transportation methods is not a one-time task but a continuous process, essential for reducing costs and maintaining a competitive edge.
資料ダウンロード
QCD管理受発注クラウド「newji」は、受発注部門で必要なQCD管理全てを備えた、現場特化型兼クラウド型の今世紀最高の受発注管理システムとなります。
ユーザー登録
受発注業務の効率化だけでなく、システムを導入することで、コスト削減や製品・資材のステータス可視化のほか、属人化していた受発注情報の共有化による内部不正防止や統制にも役立ちます。
NEWJI DX
製造業に特化したデジタルトランスフォーメーション(DX)の実現を目指す請負開発型のコンサルティングサービスです。AI、iPaaS、および先端の技術を駆使して、製造プロセスの効率化、業務効率化、チームワーク強化、コスト削減、品質向上を実現します。このサービスは、製造業の課題を深く理解し、それに対する最適なデジタルソリューションを提供することで、企業が持続的な成長とイノベーションを達成できるようサポートします。
製造業ニュース解説
製造業、主に購買・調達部門にお勤めの方々に向けた情報を配信しております。
新任の方やベテランの方、管理職を対象とした幅広いコンテンツをご用意しております。
お問い合わせ
コストダウンが利益に直結する術だと理解していても、なかなか前に進めることができない状況。そんな時は、newjiのコストダウン自動化機能で大きく利益貢献しよう!
(β版非公開)