- お役立ち記事
- Why-why analysis of bugs and horizontal deployment methods
Why-why analysis of bugs and horizontal deployment methods
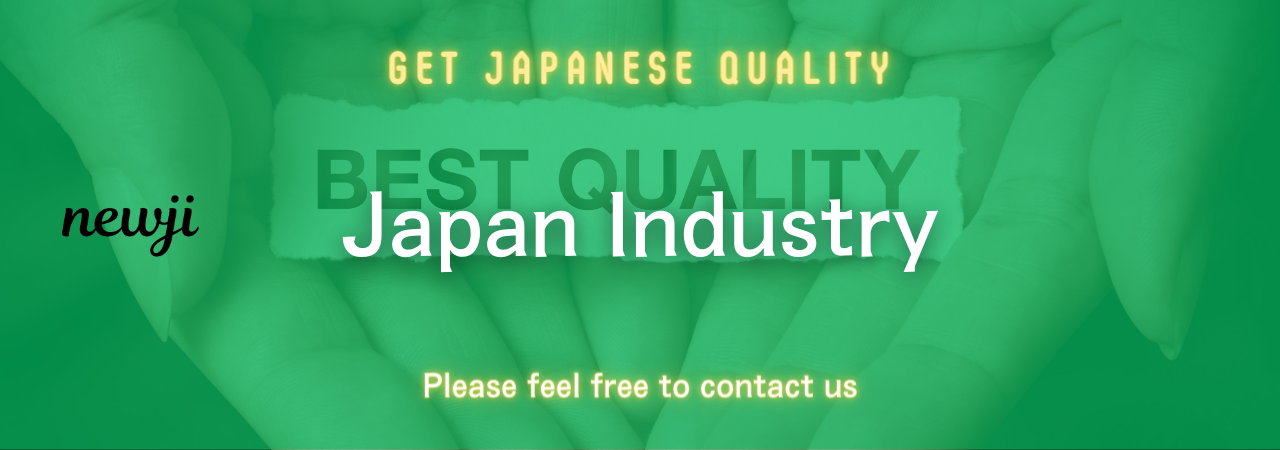
目次
Understanding the Why-Why Analysis
The Why-Why Analysis is a problem-solving tool used to discover the root causes of an issue by asking “why” multiple times.
This method helps to dig deeper into a problem, rather than addressing only its symptoms.
Originating from the Lean Manufacturing principles, the Why-Why Analysis has been a go-to method for organizations aiming to improve their processes and product quality.
Employing the Why-Why Analysis can provide clarity and help teams identify underlying issues, allowing them to devise effective solutions.
When examining bugs, this analysis provides a structured way to understand the origins and prevent them from recurring.
The goal is to construct a cause-and-effect chain that leads back to the problem’s source.
Step-by-step Guide to Performing Why-Why Analysis
1. **Identify the Problem:**
Start by clearly stating the issue at hand.
Ensure that everyone involved has a common understanding of the problem.
2. **Ask the First Why:**
Ask why the problem occurs.
Try to reach an answer that’s factual rather than opinion-based.
3. **Ask the Second Why:**
With the initial answer, ask why that situation exists.
It’s crucial to challenge assumptions and rely on data if possible.
4. **Repeat:**
Continue asking “why” until you’ve drilled down five times or until you’ve reached a root cause or no further logical explanation exists.
Sometimes, fewer questions are needed, while in other cases, more probing is necessary.
5. **Verify:**
After identifying what you believe is the root cause, verify it by considering the likelihood that it really is the base of the problem.
Benefits of Why-Why Analysis in Bug Identification
Performing a Why-Why Analysis on bugs allows teams to move past surface-level fixes and towards systemic solutions.
It prevents the recurrence of issues, helping to maintain product integrity and user satisfaction.
When applied effectively, it saves time and resources in the long run, reducing the likelihood of binge-fixing efforts in future software releases.
Organizations also benefit from a collaborative approach.
When team members work together on this analysis, shared insights often lead to a comprehensive understanding of issues.
This fosters more productive discussions and innovative solutions.
Challenges and Considerations
Despite its benefits, there are challenges associated with Why-Why Analysis.
For one, it requires an environment where team members feel safe to express ideas and hypotheses without judgment.
Organizations must cultivate this open environment to leverage the full potential of the Why-Why process.
Another consideration is ensuring that asking “why” doesn’t turn into a blaming exercise.
The focus should always be on the process, not individual faults.
Additionally, sometimes a problem can arise from various interconnected factors, complicating the analysis.
Horizontal Deployment Methods
Once root causes are discovered, the next step is implementing solutions, which is where horizontal deployment methods come into play.
Horizontal deployment involves disseminating solutions and improvements across different teams, departments, or even entire organizations.
It’s about spreading successful practices beyond the origin of the problem-solving activity.
Effective Horizontal Deployment Strategies
1. **Documentation of Solutions:**
Clearly document the findings of the Why-Why Analysis and the subsequent solutions.
This will serve as a guide for others facing similar issues.
2. **Cross-Departmental Communication:**
Encourage sharing of insights and learnings between teams.
Regular meetings or workshops can facilitate this exchange of knowledge.
3. **Pilot Programs:**
Before full deployment, test the solution in a controlled setting.
This minimizes risks and provides data to refine the approach before wider application.
4. **Feedback Loops:**
Establish mechanisms for ongoing feedback once the solution is implemented.
This ensures continuous improvement and adaptation to new challenges.
5. **Standardization:**
If a solution proves effective, work towards developing a standard operating procedure that can be applied consistently across different areas.
Conclusion
A robust Why-Why Analysis coupled with effective horizontal deployment methods can make a substantial difference in managing bugs and improving processes.
By systematically identifying and addressing root causes, teams can shift from reactive problem management to proactive improvement strategies.
Through horizontal deployment, organizations expand the impact of their solutions and enhance overall productivity and quality.
This approach fosters a culture of continuous improvement, equipping organizations to face challenges with confidence and resilience.
With every analysis and deployment, not only do processes improve, but team collaboration and insights deepen, propelling the organization toward sustainable success.
資料ダウンロード
QCD調達購買管理クラウド「newji」は、調達購買部門で必要なQCD管理全てを備えた、現場特化型兼クラウド型の今世紀最高の購買管理システムとなります。
ユーザー登録
調達購買業務の効率化だけでなく、システムを導入することで、コスト削減や製品・資材のステータス可視化のほか、属人化していた購買情報の共有化による内部不正防止や統制にも役立ちます。
NEWJI DX
製造業に特化したデジタルトランスフォーメーション(DX)の実現を目指す請負開発型のコンサルティングサービスです。AI、iPaaS、および先端の技術を駆使して、製造プロセスの効率化、業務効率化、チームワーク強化、コスト削減、品質向上を実現します。このサービスは、製造業の課題を深く理解し、それに対する最適なデジタルソリューションを提供することで、企業が持続的な成長とイノベーションを達成できるようサポートします。
オンライン講座
製造業、主に購買・調達部門にお勤めの方々に向けた情報を配信しております。
新任の方やベテランの方、管理職を対象とした幅広いコンテンツをご用意しております。
お問い合わせ
コストダウンが利益に直結する術だと理解していても、なかなか前に進めることができない状況。そんな時は、newjiのコストダウン自動化機能で大きく利益貢献しよう!
(Β版非公開)