- お役立ち記事
- Winding methods and material selection that maintain stability and durability are important for new employees in the electromagnetic coil manufacturing industry.
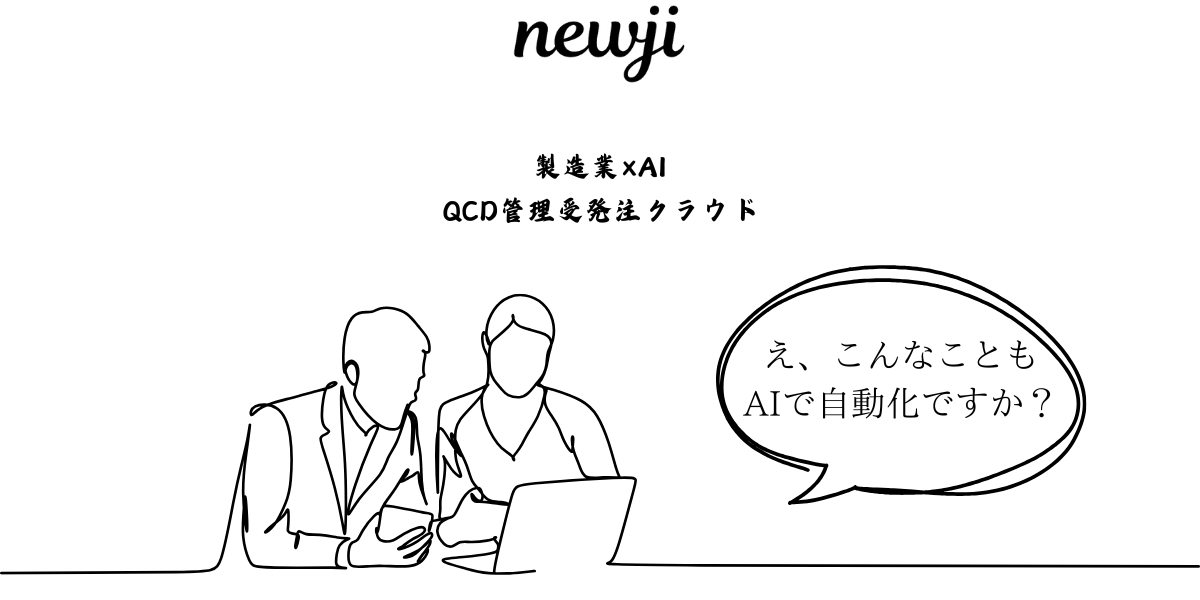
Winding methods and material selection that maintain stability and durability are important for new employees in the electromagnetic coil manufacturing industry.
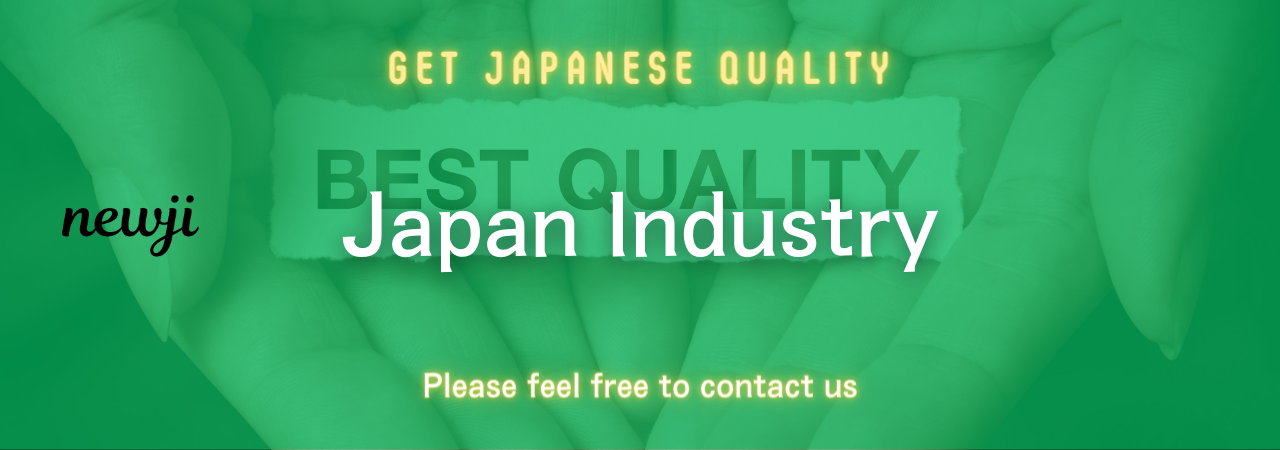
目次
Introduction to Electromagnetic Coils
New employees in the electromagnetic coil manufacturing industry quickly learn that creating stable and durable electromagnetic coils is crucial to their success.
Understanding the fundamentals of winding methods and selecting the right materials is essential in producing high-quality coils.
These coils are used in various applications, from electric motors to transformers, and the reliability of these devices often hinges on the manufacturing quality of the coils themselves.
Why Winding Methods Matter
The winding process is at the heart of electromagnetic coil manufacture.
Winding involves wrapping wire around a core or spool to create coils that can generate or receive electromagnetic fields.
Different winding methods can significantly impact the coil’s performance, affecting parameters like inductance, resistance, and capacitance.
Choosing the appropriate winding method is crucial as it determines the efficiency and functionality of the finished coil.
Common Winding Techniques
Some common winding techniques include:
1. **Single-Layer Winding**: This is the most basic method, where wire is wound in a single layer on a core. It’s simple but limits the coil’s inductance and capacity.
2. **Multi-Layer Winding**: Layers of wire are stacked to reach specific performance requirements. While it can enhance coil capability, it also demands careful attention to winding tension and insulation.
3. **Toroidal Winding**: Used in transformers and reactors to minimize magnetic flux leakage. The core is donut-shaped, necessitating meticulous winding to maintain efficiency.
4. **Random Winding**: Common in mass production, wires are wound without a specific pattern. This requires less time but usually results in lower-performance coils.
Material Selection for Coil Stability
Material selection is a critical part of coil manufacturing that impacts its durability and stability.
The right materials can extend a coil’s lifespan, enhance its efficiency, and adapt its function to the application at hand.
Conductive Materials
The wire used in an electromagnetic coil is typically made of conductive materials like copper or aluminum.
Copper is favored for its excellent conductivity and thermal properties, making it ideal for most applications.
Aluminum, while less conductive than copper, is lighter and less expensive, making it suitable for large-scale applications where weight is a concern.
Insulation Materials
Insulation is key to preventing short circuits and ensuring safety.
The choice of insulation depends on the coil’s operating environment and temperature.
Common insulating materials include:
– **Polyimide Film**: Known for its thermal resistance, making it suitable for high-temperature applications.
– **Polyester Film**: Often used due to its cost-effectiveness and good insulating properties.
– **Glass Fiber**: Used in high-voltage applications due to its excellent insulating capability.
Core Materials
The core of a coil, usually made from ferromagnetic materials, is vital for directing the magnetic field.
Materials like silicon steel and ferrite are commonly used for their magnetic properties and ability to reduce energy losses.
Maintaining Coil Stability and Durability
To maintain coil stability and durability, manufacturers must pay close attention to both the winding process and the materials selected.
It’s essential to ensure that wires are wound evenly, without excessive tension that could cause breakage.
Precision in winding and material selection directly correlates with the overall stability and lifespan of the coil.
Quality Control in Coil Manufacturing
Implementing rigorous quality control checks at various stages of production helps guarantee coil performance and reliability.
Testing for electrical parameters, mechanical stress, and thermal performance is vital in identifying potential issues early in the manufacturing process.
Technological Innovations and Future Trends
Innovations in coil manufacturing, such as automated winding machines and advanced materials, are driving improvements in coil performance.
Automation enables precise winding, reducing human error and increasing production speed.
In addition, research into new materials, such as superconductors, is paving the way for coils that offer unprecedented efficiency and durability.
Conclusion
For new employees entering the electromagnetic coil manufacturing industry, understanding winding methods and material selection is fundamental.
These principles underpin the creation of coils that are stable, durable, and efficient, meeting the diverse needs of modern technology.
With the right knowledge and skills, anyone can contribute significantly to producing high-quality electromagnetic components that play a pivotal role in countless applications worldwide.
資料ダウンロード
QCD調達購買管理クラウド「newji」は、調達購買部門で必要なQCD管理全てを備えた、現場特化型兼クラウド型の今世紀最高の購買管理システムとなります。
ユーザー登録
調達購買業務の効率化だけでなく、システムを導入することで、コスト削減や製品・資材のステータス可視化のほか、属人化していた購買情報の共有化による内部不正防止や統制にも役立ちます。
NEWJI DX
製造業に特化したデジタルトランスフォーメーション(DX)の実現を目指す請負開発型のコンサルティングサービスです。AI、iPaaS、および先端の技術を駆使して、製造プロセスの効率化、業務効率化、チームワーク強化、コスト削減、品質向上を実現します。このサービスは、製造業の課題を深く理解し、それに対する最適なデジタルソリューションを提供することで、企業が持続的な成長とイノベーションを達成できるようサポートします。
オンライン講座
製造業、主に購買・調達部門にお勤めの方々に向けた情報を配信しております。
新任の方やベテランの方、管理職を対象とした幅広いコンテンツをご用意しております。
お問い合わせ
コストダウンが利益に直結する術だと理解していても、なかなか前に進めることができない状況。そんな時は、newjiのコストダウン自動化機能で大きく利益貢献しよう!
(Β版非公開)