- お役立ち記事
- Wireless battery charger manufacturing process and key points for overseas expansion
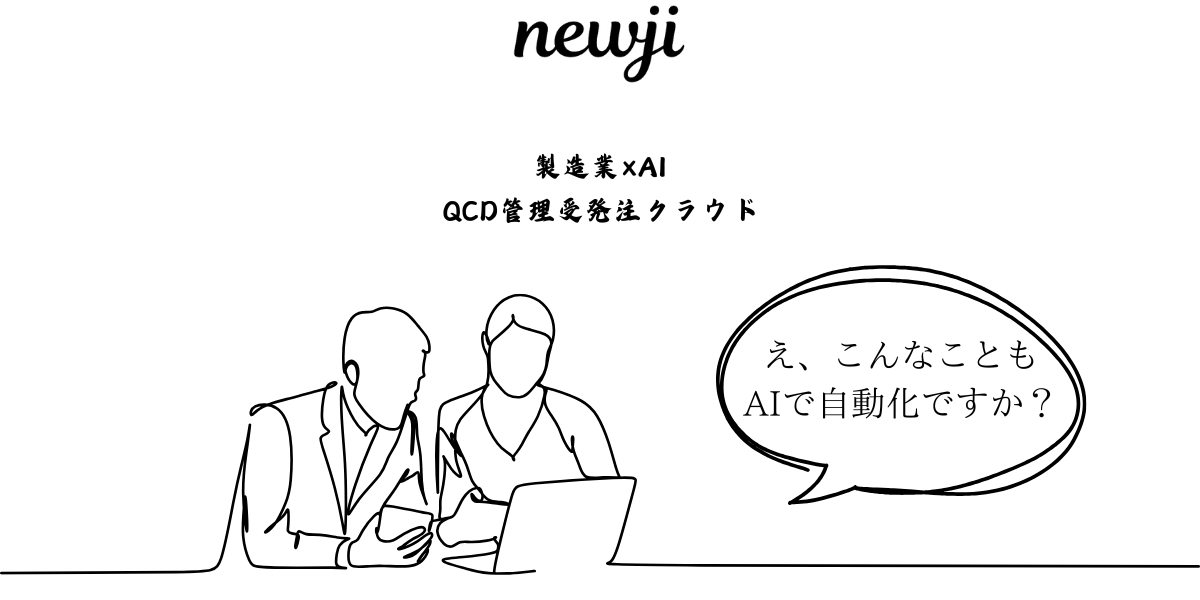
Wireless battery charger manufacturing process and key points for overseas expansion
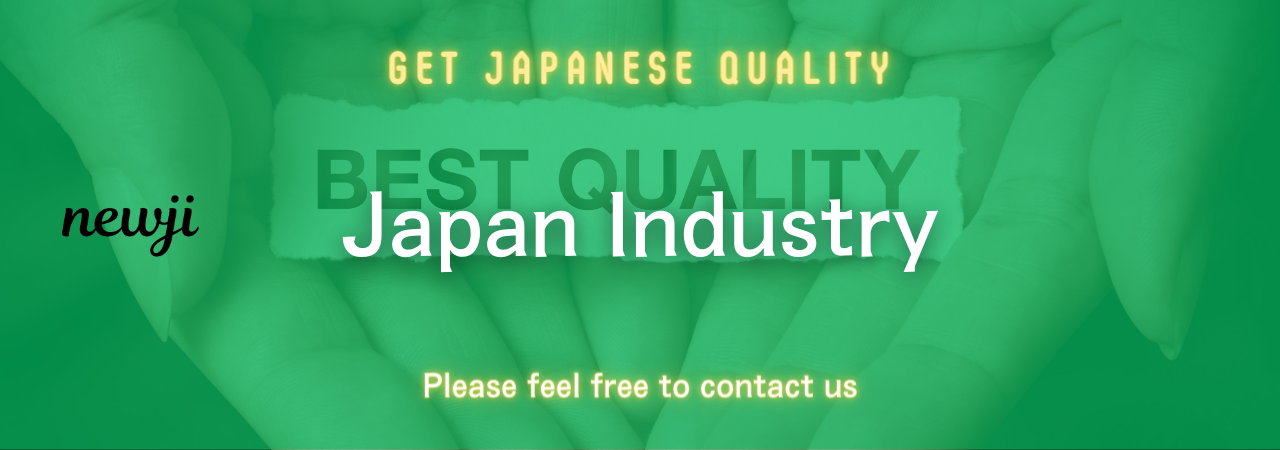
目次
Understanding the Wireless Battery Charger Manufacturing Process
The manufacturing process of wireless battery chargers involves several meticulously planned steps, ensuring that the end product is efficient, reliable, and consumer-safe.
Creating such innovative technology requires careful consideration of design, materials, and testing procedures.
Let’s delve into the key stages of manufacturing wireless battery chargers to understand this intricate process better.
Design and Prototyping
Every successful product begins with a thoughtful design.
For a wireless battery charger, designers focus on creating a product that is not just functional but also appealing to the consumer.
The design phase includes determining the ideal size, shape, and materials that will provide durability and effectiveness.
Once a design concept is finalized, the next step is prototyping.
Prototypes allow manufacturers to test the functionality of the design and make necessary adjustments before mass production begins.
Prototyping is crucial to identify potential issues in the design or materials that could compromise the charger’s performance.
Material Selection
Choosing the right materials is critical for manufacturing wireless battery chargers.
Materials must be durable enough to withstand regular use while maintaining the ability to conduct electricity effectively.
The most common materials used include various plastics for the casing, copper coils for induction, and magnets for aligning the charger with the device.
Manufacturers must ensure these materials conform to international safety standards, particularly when planning to export to different global markets.
Component Manufacturing
Wireless chargers comprise several key components, each needing precision manufacturing.
The inductive coil is one of the most critical components, as it’s responsible for transferring energy from the charger to the device wirelessly.
Manufacturing these coils involves winding copper wire into precise coils that can effectively transmit energy without overheating.
Other components, such as the circuit board that controls power flow, must also be manufactured to exact specifications to ensure reliability and safety.
Assembly Line Production
After manufacturing individual components, the next step is the assembly process.
This phase involves putting together all the parts, such as encasing the coil within the protective plastic housing and attaching the circuit boards and power connectors.
Automation often plays a significant role in assembly lines to ensure consistency and efficiency in production.
However, manual inspections are still necessary to ensure each charger operates correctly.
Quality control checks are integral at this stage, testing each unit for functionality and safety before proceeding to packaging.
Quality Assurance and Testing
Quality assurance is a vital part of manufacturing wireless battery chargers.
Before reaching consumers, each charger undergoes rigorous testing to ensure that it meets performance standards.
Testers evaluate factors such as charging efficiency, compatibility with various devices, and resistance to overcharging or overheating.
Manufacturers must also ensure the devices comply with local and international regulatory standards.
Meeting these standards is especially important when exporting to different countries with varying guidelines for electronic products.
Key Points for Overseas Expansion
Expanding into international markets is a significant step for manufacturers of wireless battery chargers.
However, it requires strategic planning and consideration of several key factors to be successful.
Understanding Global Regulations
One of the most crucial aspects of expanding overseas is understanding and complying with different countries’ regulations and standards.
Each country may have unique guidelines for electronics, covering areas such as safety certifications, electromagnetic compatibility, and energy efficiency requirements.
Manufacturers should work closely with regulatory experts to ensure their products meet these standards to facilitate smooth entry into new markets.
Adapting Products to Market Preferences
Consumer preferences can vary greatly across different regions.
Manufacturers should conduct thorough market research to understand the specific needs and expectations of consumers in each targeted region.
Some countries might prefer more compact charger designs, while others may prioritize faster charging speeds.
Adapting products to fit these preferences can significantly enhance market acceptance and success.
Establishing Local Partnerships
Partnering with local firms can provide critical insights and resources to successfully penetrate new markets.
Local partners can assist in navigating regulatory landscapes, understanding cultural nuances, and developing effective distribution networks.
These collaborations can also help in tailoring marketing strategies that resonate with local consumers, improving brand recognition and trust.
Logistics and Distribution
Efficient logistics and distribution are essential for successful international expansion.
Manufacturers must establish reliable supply chains and distribution channels to ensure their products reach consumers in good condition and in a timely manner.
Considering factors such as shipping costs and local customs procedures is important to minimize potential delays and additional expenses.
Continuous Innovation
Finally, continuous innovation is key to maintaining a competitive edge in the global market.
Staying at the forefront of wireless charging technology not only helps in retaining existing customers but also attracts new ones.
Manufacturers should invest in research and development to create cutting-edge features and improvements that respond to changing consumer demands and technological advancements.
In conclusion, the manufacturing process of wireless battery chargers is a complex operation that requires precise execution at every stage.
Understanding and planning for overseas expansion involve navigating regulations, adapting to market preferences, building local partnerships, ensuring efficient logistics, and committing to continuous innovation.
By considering these factors, manufacturers can successfully expand their reach in the global market, offering effective and cutting-edge wireless charging solutions to consumers worldwide.
資料ダウンロード
QCD調達購買管理クラウド「newji」は、調達購買部門で必要なQCD管理全てを備えた、現場特化型兼クラウド型の今世紀最高の購買管理システムとなります。
ユーザー登録
調達購買業務の効率化だけでなく、システムを導入することで、コスト削減や製品・資材のステータス可視化のほか、属人化していた購買情報の共有化による内部不正防止や統制にも役立ちます。
NEWJI DX
製造業に特化したデジタルトランスフォーメーション(DX)の実現を目指す請負開発型のコンサルティングサービスです。AI、iPaaS、および先端の技術を駆使して、製造プロセスの効率化、業務効率化、チームワーク強化、コスト削減、品質向上を実現します。このサービスは、製造業の課題を深く理解し、それに対する最適なデジタルソリューションを提供することで、企業が持続的な成長とイノベーションを達成できるようサポートします。
オンライン講座
製造業、主に購買・調達部門にお勤めの方々に向けた情報を配信しております。
新任の方やベテランの方、管理職を対象とした幅広いコンテンツをご用意しております。
お問い合わせ
コストダウンが利益に直結する術だと理解していても、なかなか前に進めることができない状況。そんな時は、newjiのコストダウン自動化機能で大きく利益貢献しよう!
(Β版非公開)