- お役立ち記事
- Work Chain Manufacturing Process and Durability Strengthening
Work Chain Manufacturing Process and Durability Strengthening
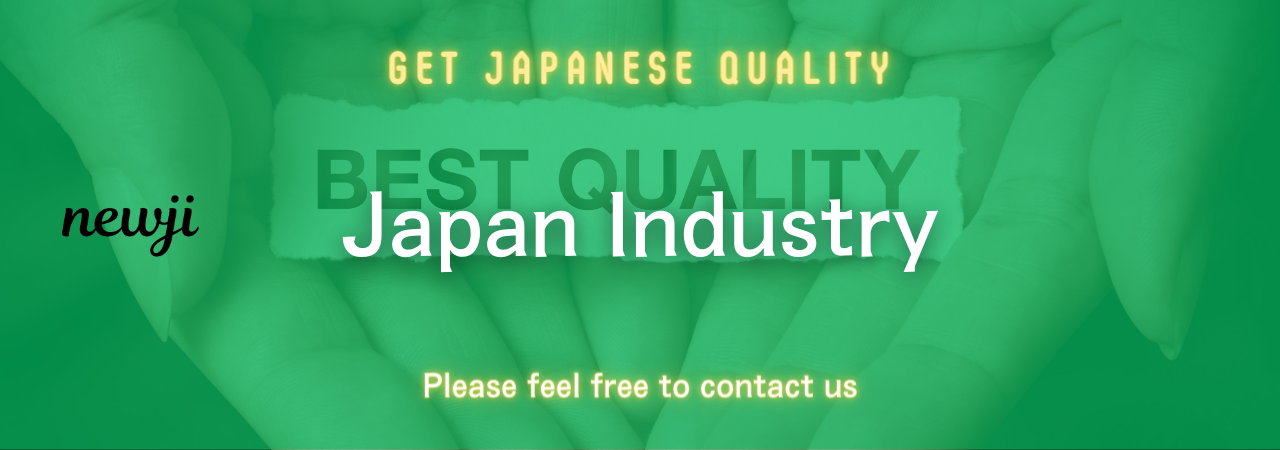
The process of manufacturing a work chain involves several detailed and precise steps meant to ensure the final product is both durable and efficient.
Chains are used in various industries, from construction to transportation, so their reliability is critical.
To comprehend how a work chain is manufactured and its durability strengthened, let us delve into the process step by step.
目次
Raw Material Selection
The first step in manufacturing a work chain is selecting high-quality raw materials.
Typically, chains are made from steel due to its tensile strength and durability.
The steel used is often carbon steel, alloy steel, or stainless steel, depending on the specific application and required properties.
Once the appropriate steel type is identified, it is sourced from trusted suppliers to ensure consistent quality.
Cutting and Shaping
After procuring the raw material, the steel is cut into smaller pieces called billets.
These billets are then heated to a high temperature to make them malleable.
Once heated, the billets are shaped into the desired link forms using specialized molds.
This step, known as forging, ensures that each chain link conforms to precise dimensions and specifications.
Forging Process
Forging is an effective method to shape steel because it aligns the grain structure, significantly enhancing the chain’s strength.
The heated billets are placed within the mold, and immense pressure is applied to form the links.
After forging, the links are left to cool, often in a controlled environment, so they retain their strength while avoiding unwanted stresses in the metal.
Heat Treatment
Heat treatment is a crucial phase in the manufacturing process.
This step involves heating the forged chain links to a specific temperature and then rapidly cooling them, a technique known as quenching.
This process increases the hardness and strength of the steel, making the chain more durable and resistant to wear.
Tempering
Following the quenching process, the links are tempered.
Tempering is a heat treatment method applied to reduce brittleness in the metal.
The links are reheated to a lower temperature than used in quenching and held there for a specific period before cooling slowly.
This step provides a balance between hardness and toughness, ensuring that the chain is both strong and flexible enough to withstand heavy loads and shocks.
Assembling the Chain
Once the links are heat-treated, the next step is assembly.
Assembly involves joining the individual links to form a continuous chain.
This process can be done manually or using automated machinery.
Ensuring that each link is securely joined is vital for the chain’s overall strength.
Specialized equipment may be used to apply the correct joining force, while careful inspection ensures the integrity of each connection.
Welding
In some cases, welding is used to strengthen the joints further.
Each link is welded closed to prevent any openings that could weaken the chain.
The welding process requires precision and skill, as improper welding can compromise the chain’s durability.
Surface Treatment
After assembly, the chain undergoes surface treatment processes to enhance its resistance to environmental factors like corrosion.
Surface treatments include galvanizing, coating, or painting the chain with protective layers.
For instance, galvanizing involves coating the chain with a layer of zinc, which offers excellent corrosion resistance.
Other treatments might include powder coating or applying anti-corrosive paints.
Inspection and Quality Control
The manufactured chain undergoes rigorous inspection and quality control testing to ensure it meets the required standards.
This step involves checking the dimensions, tensile strength, and overall durability of the chain.
Advanced testing methods, such as x-ray inspections and magnetic particle testing, might be used to detect any internal or surface defects that could weaken the chain.
Durability Strengthening Techniques
To further enhance the chain’s durability, manufacturers might use additional techniques like peening, shot blasting, or applying advanced coatings.
These methods aim to increase the chain’s lifespan and ensure it performs reliably under heavy-duty conditions.
Shot Peening
Shot peening involves bombarding the chain with small spherical media, which creates compressive stress layers on the surface of the links.
This process increases fatigue resistance and prevents premature failure, making the chain more robust over its operational life.
Load Testing
Lastly, finished chains undergo rigorous load testing to simulate real-world conditions.
The chains are subjected to various loads greater than their intended working limits to ensure they can handle extreme stress without breaking.
This testing guarantees that each chain can perform reliably and safely when deployed in demanding environments.
Conclusion
The manufacturing process of a work chain is intricate and involves several critical steps to ensure the final product is durable and reliable.
From the initial selection of high-quality raw materials to the final load testing, each phase is crucial in achieving the desired strength and performance.
By adhering to stringent manufacturing protocols and employing advanced durability strengthening techniques, manufacturers can produce robust work chains capable of withstanding the rigors of heavy use across various industries.
資料ダウンロード
QCD調達購買管理クラウド「newji」は、調達購買部門で必要なQCD管理全てを備えた、現場特化型兼クラウド型の今世紀最高の購買管理システムとなります。
ユーザー登録
調達購買業務の効率化だけでなく、システムを導入することで、コスト削減や製品・資材のステータス可視化のほか、属人化していた購買情報の共有化による内部不正防止や統制にも役立ちます。
NEWJI DX
製造業に特化したデジタルトランスフォーメーション(DX)の実現を目指す請負開発型のコンサルティングサービスです。AI、iPaaS、および先端の技術を駆使して、製造プロセスの効率化、業務効率化、チームワーク強化、コスト削減、品質向上を実現します。このサービスは、製造業の課題を深く理解し、それに対する最適なデジタルソリューションを提供することで、企業が持続的な成長とイノベーションを達成できるようサポートします。
オンライン講座
製造業、主に購買・調達部門にお勤めの方々に向けた情報を配信しております。
新任の方やベテランの方、管理職を対象とした幅広いコンテンツをご用意しております。
お問い合わせ
コストダウンが利益に直結する術だと理解していても、なかなか前に進めることができない状況。そんな時は、newjiのコストダウン自動化機能で大きく利益貢献しよう!
(Β版非公開)