- お役立ち記事
- Workflow construction method for improving purchasing processes in the building materials industry
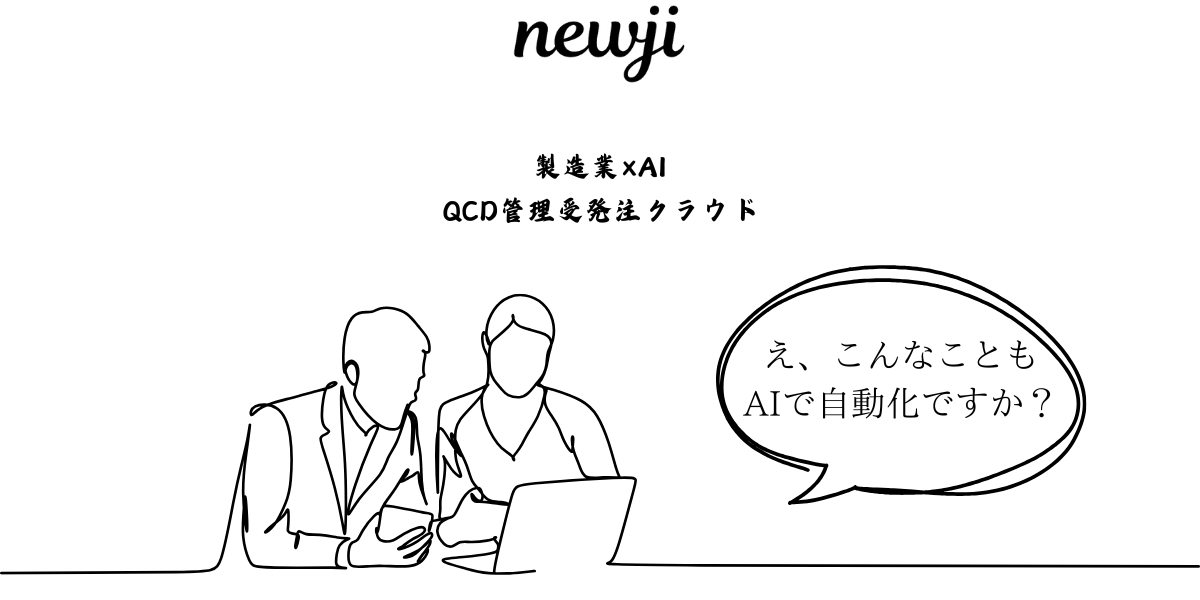
Workflow construction method for improving purchasing processes in the building materials industry
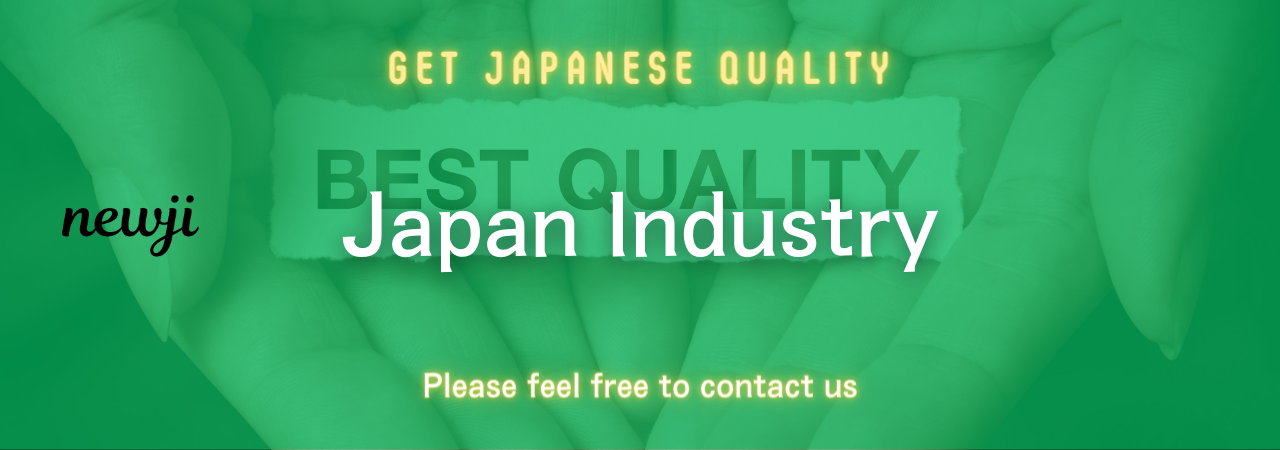
目次
Understanding the Importance of Workflow in Purchasing Processes
In the building materials industry, efficiency and organization are essential for maintaining competitive advantage and operational success.
One critical area requiring attention is the purchasing process.
When managed well, this can lead to cost savings, improved productivity, and better supplier relationships.
But how does one achieve this?
The answer lies in constructing a well-defined workflow.
Purchasing workflows in the building materials sector bring structure to the procurement of supplies and materials.
This process involves various steps, from determining what materials are needed to receiving goods and making payments.
By optimizing these steps, companies can significantly enhance their operational flexibility and responsiveness to market demands.
Benefits of an Optimized Purchasing Workflow
Implementing an optimized purchasing workflow not only reduces waste and improves productivity but also provides several other advantages.
Firstly, a streamlined workflow enhances communication and coordination between departments, minimizing delays and errors in orders.
Secondly, it helps in tracking expenditures and managing budgets more effectively.
Thirdly, businesses can negotiate better terms with suppliers when purchasing volumes and purchasing patterns are transparent and predictable.
Moreover, a good workflow system offers clear visibility into the entire procurement process.
This improves decision-making and ensures compliance with industry standards and regulations.
Ultimately, it leads to enhanced service delivery and customer satisfaction, giving the business a considerable edge in a competitive market.
Steps to Construct a Workflow for Purchasing Processes
Building an efficient purchasing workflow involves several key steps that can transform a disorganized supply chain into a well-oiled machine.
Here’s a step-by-step guide on how to construct one:
Identify and Analyze Current Processes
The first step is to understand the existing purchasing process better.
Map out every stage from requisition to payment and analyze the effectiveness of each step.
Identify bottlenecks and areas prone to errors or delays.
This analysis forms the baseline for implementing improvements.
Define Clear Objectives and Metrics
Establish clear objectives for what you want the new workflow to achieve.
Do you want to reduce procurement times, cut costs, or improve supplier relationships?
Decide on the metrics you will use to measure success, such as average approval times, costs saved, or increased order accuracy.
Map the Ideal Workflow
With objectives set, design the ideal workflow that meets these goals.
Determine which tasks can be automated for greater efficiency, what level of human oversight is required, and how different departments will interact.
Ensure the workflow supports seamless decision-making processes with clearly defined roles and responsibilities.
Select Appropriate Tools and Technologies
Choosing the right tools is crucial to ensuring the success of your new purchasing workflow.
There are numerous procurement software options available that can automate much of the process, providing real-time data and analytics to support business decisions.
Look for tools that offer comprehensive integration with your existing systems to avoid disruptions.
Implement Incremental Changes
Instead of a complete overhaul, consider implementing the new workflow in stages.
This phased approach helps manage transition risks and allows employees to adapt gradually.
Begin with departments that require immediate attention and expand once initial results show positively.
Ensuring Success with Your Workflow
Taking steps to construct a purchasing workflow is vital, but ensuring its success requires diligence and constant monitoring.
Here are a few additional strategies to keep in mind:
Involve the Entire Team
Encourage collaboration across all departments involved in the procurement process.
This guarantees that everyone has a sense of ownership and responsibility, leading to smoother workflow adoption.
Regular Training and Support
Provide regular training sessions to keep employees up-to-date with new tools and practices.
Offer continuous support to help resolve any issues that arise during implementation.
Monitor and Review Performance
Use the metrics established during the construction phase to monitor performance continuously.
Regularly review results and make adjustments as needed to ensure the workflow remains aligned with company goals.
Future Trends in Purchasing Workflows
As the building materials industry continues to evolve, so too will purchasing workflows.
Emerging technologies such as AI and machine learning are playing an increasing role in automating complex procurement tasks.
Additionally, data analytics will become paramount in informing purchasing strategies by offering insights into market trends and customer demands.
Sustainability is also set to become a major focus, with more companies looking to incorporate eco-friendly practices into their procurement processes.
This will include evaluating suppliers based on their environmental practices and prioritizing sustainable materials.
Ultimately, those businesses that embrace these changes and continue to refine their purchasing workflows will be better positioned to drive growth and improve their market position.
Constructing an effective workflow for purchasing processes may require careful planning and strategic implementation, but the long-term benefits are undeniable.
With the right approach, building materials companies can enhance efficiency, reduce costs, and better serve their customers, ensuring success in a rapidly changing industry landscape.
資料ダウンロード
QCD調達購買管理クラウド「newji」は、調達購買部門で必要なQCD管理全てを備えた、現場特化型兼クラウド型の今世紀最高の購買管理システムとなります。
ユーザー登録
調達購買業務の効率化だけでなく、システムを導入することで、コスト削減や製品・資材のステータス可視化のほか、属人化していた購買情報の共有化による内部不正防止や統制にも役立ちます。
NEWJI DX
製造業に特化したデジタルトランスフォーメーション(DX)の実現を目指す請負開発型のコンサルティングサービスです。AI、iPaaS、および先端の技術を駆使して、製造プロセスの効率化、業務効率化、チームワーク強化、コスト削減、品質向上を実現します。このサービスは、製造業の課題を深く理解し、それに対する最適なデジタルソリューションを提供することで、企業が持続的な成長とイノベーションを達成できるようサポートします。
オンライン講座
製造業、主に購買・調達部門にお勤めの方々に向けた情報を配信しております。
新任の方やベテランの方、管理職を対象とした幅広いコンテンツをご用意しております。
お問い合わせ
コストダウンが利益に直結する術だと理解していても、なかなか前に進めることができない状況。そんな時は、newjiのコストダウン自動化機能で大きく利益貢献しよう!
(Β版非公開)