- お役立ち記事
- Yield improvement strategies for continuous casting processes that managers of production technology departments in the steel industry should keep in mind
Yield improvement strategies for continuous casting processes that managers of production technology departments in the steel industry should keep in mind
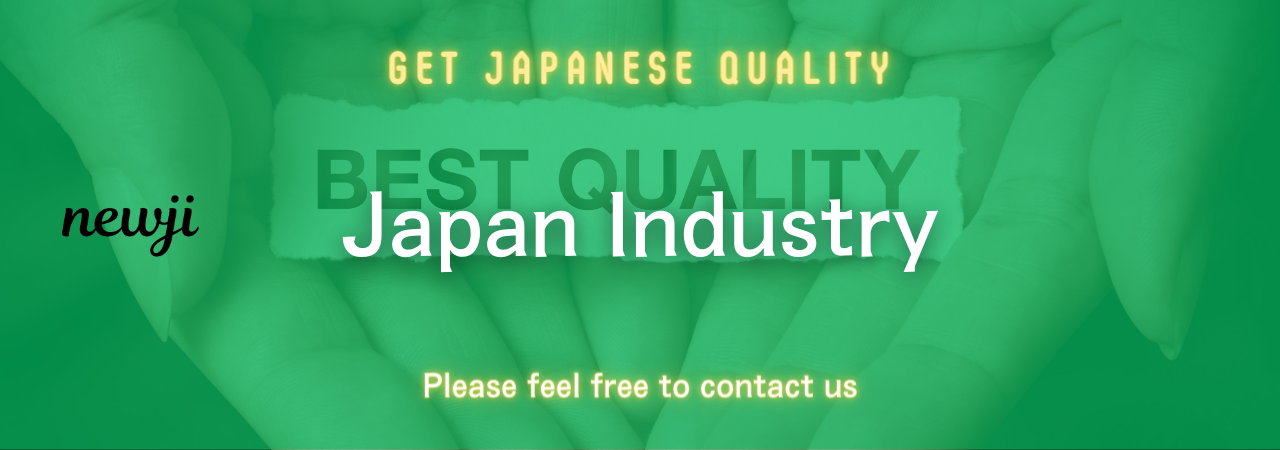
目次
Understanding Continuous Casting in the Steel Industry
Continuous casting is a pivotal process in the steel industry, serving as a bridge between the production of liquid steel and solid finished products like slabs, billets, and blooms.
This process offers numerous efficiency advantages over traditional ingot casting, providing improved yield, quality, and energy savings.
However, like any manufacturing process, continuous casting isn’t free from challenges.
For managers of production technology departments in the steel industry, understanding and implementing yield improvement strategies can lead to substantial cost savings and efficiency gains.
Importance of Yield in Continuous Casting
Yield in continuous casting refers to the percentage of liquid steel that is successfully transformed into a solid, usable product.
Higher yield means more of the produced steel reaches the market, translating into increased revenue and reduced waste.
Poor yield results in more scrap, which not only represents a direct financial loss but also requires additional processing and energy to melt down and recycle.
Thus, optimizing yield is a top priority for plant managers aiming to maximize efficiency and competitiveness.
Key Factors Influencing Yield
Before delving into strategies for yield improvement, it’s crucial to understand the factors that influence yield in continuous casting:
1. Quality of Raw Materials
The quality of raw steel significantly impacts the yield.
Impurities and variations in composition can lead to defects and inconsistencies, requiring rework or resulting in scrap.
Therefore, sourcing high-quality raw materials and conducting rigorous quality checks can aid in maintaining the yield.
2. Temperature Control
Maintaining the correct temperature of the molten steel is critical.
If the temperature is too high or too low, it can lead to surface defects or even cause the casting to break.
Accurate temperature monitoring and control are essential for reducing waste and improving yield.
3. Casting Speed
Casting speed is another vital parameter.
If the process is too slow, production efficiency decreases.
Conversely, if it’s too fast, it can introduce defects or cause cracking.
Thus, optimizing casting speed is essential for balancing productivity with quality.
4. Mold Design and Maintenance
The mold, which shapes the steel, must be designed for optimal performance and regularly maintained.
Any wear or damage to the mold can result in product defects and yield losses.
This makes regular inspection and maintenance a necessity.
Strategies for Improving Yield
To enhance yield in continuous casting, managers should consider the following strategies:
1. Implement Advanced Sensors and Automation
Investing in advanced sensors and automation technologies can provide precise control over the continuous casting process.
These technologies offer real-time monitoring of critical parameters such as temperature, speed, and pressure.
Automated systems can detect anomalies and adjust the process promptly, reducing downtime and minimizing defects.
2. Conduct Regular Training Programs
Employees operating the casting equipment play a critical role in yield improvement.
Regular training programs can ensure they are well-versed in the latest technologies and best practices.
Training can help operators identify potential issues early and respond effectively, preventing yield losses down the line.
3. Optimize Maintenance Schedule
Predictive maintenance technologies can help minimize unexpected equipment failures.
By analyzing historical data and monitoring equipment health, managers can schedule maintenance at the optimal time, thereby reducing downtime and maintaining consistent quality.
4. Improve Quality Inspection Protocols
Enhanced quality control protocols ensure that only the best material reaches the end of the line.
Implementing better inspection techniques can help catch defects early, preventing a compromised batch from proceeding.
Advanced imaging and analytics tools can aid in identifying potential problems earlier than traditional methods.
5. Feedback Loop for Continuous Improvement
Creating a feedback loop whereby operators and managers record observations and outcomes can facilitate continuous improvement.
By analyzing this data, production teams can identify patterns and implement systemic changes that further improve yield.
Conclusion
Maximizing yield in continuous casting processes is essential for enhancing profitability, efficiency, and sustainability in the steel industry.
By understanding the key factors that influence yield and implementing strategic improvements, managers of production technology departments can drive significant operational improvements.
Investing in technology, training, and robust quality control measures can lead to more consistent, high-quality outputs and a substantial reduction in waste.
Ultimately, these efforts not only improve the financial bottom line but also contribute to more sustainable industrial practices.
資料ダウンロード
QCD調達購買管理クラウド「newji」は、調達購買部門で必要なQCD管理全てを備えた、現場特化型兼クラウド型の今世紀最高の購買管理システムとなります。
ユーザー登録
調達購買業務の効率化だけでなく、システムを導入することで、コスト削減や製品・資材のステータス可視化のほか、属人化していた購買情報の共有化による内部不正防止や統制にも役立ちます。
NEWJI DX
製造業に特化したデジタルトランスフォーメーション(DX)の実現を目指す請負開発型のコンサルティングサービスです。AI、iPaaS、および先端の技術を駆使して、製造プロセスの効率化、業務効率化、チームワーク強化、コスト削減、品質向上を実現します。このサービスは、製造業の課題を深く理解し、それに対する最適なデジタルソリューションを提供することで、企業が持続的な成長とイノベーションを達成できるようサポートします。
オンライン講座
製造業、主に購買・調達部門にお勤めの方々に向けた情報を配信しております。
新任の方やベテランの方、管理職を対象とした幅広いコンテンツをご用意しております。
お問い合わせ
コストダウンが利益に直結する術だと理解していても、なかなか前に進めることができない状況。そんな時は、newjiのコストダウン自動化機能で大きく利益貢献しよう!
(Β版非公開)