- お役立ち記事
- “Zero Accident Goal” that management and workplaces work together on—An executable safety plan
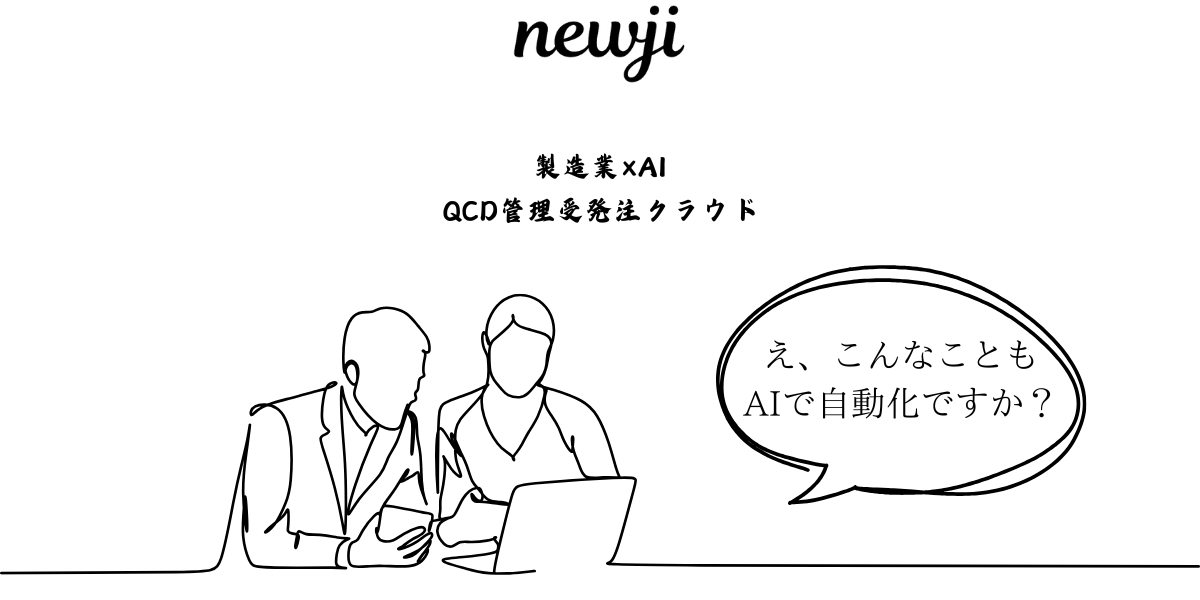
“Zero Accident Goal” that management and workplaces work together on—An executable safety plan
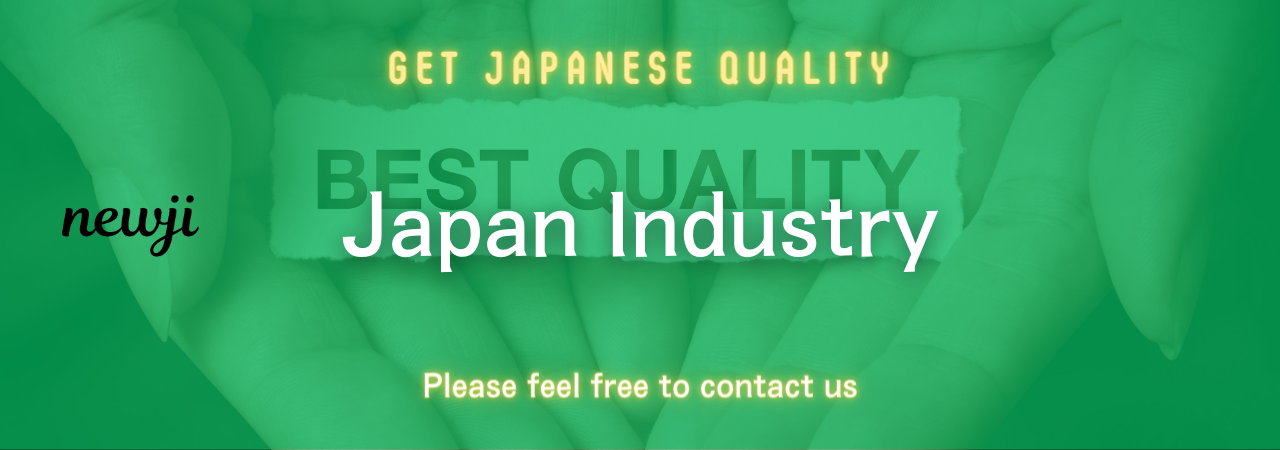
目次
Understanding the Importance of a Zero Accident Goal
Achieving a “Zero Accident Goal” is an aspiration that transcends industries and individual organizations.
It establishes a safety-first mindset, ensuring that all employees return home unharmed at the end of the day.
The idea of zero accidents revolutionizes how companies think about workplace safety.
Rather than accepting that a certain level of accidents are inevitable, it promotes the belief that every accident is preventable.
Management teams and workplaces must collaborate effectively to achieve this ambitious goal.
It’s not a solo endeavor but a joint commitment that requires diligence, commitment, and thorough planning.
Building a Strong Safety Culture
The foundation of a zero-accident goal is a strong safety culture.
This culture is not just about having policies written in manuals, but about embedding safety values into the very ethos of an organization.
Management must lead by example, showing unwavering commitment to safety.
Employees must feel empowered and responsible for their safety and the safety of their colleagues.
This can be achieved through regular safety training, clear communication about safety expectations, and encouraging workers to voice concerns or suggest improvements without fear of retaliation.
Creating an Executable Safety Plan
An executable safety plan is essential to move from the ideal of zero accidents to reality.
The plan should include clear, actionable steps that everyone in the organization understands.
These should be tailored to the specific risks of the workplace but also flexible to accommodate new threats as they arise.
Start by assessing the current safety situation through a thorough audit.
Identify potential hazards and areas that need immediate attention.
Involve employees in this process as they are often the best resource for understanding on-the-ground realities.
Once the risks are identified, prioritize them based on severity and likelihood.
Develop strategies to mitigate these risks, which may include engineering controls, administrative changes, or personal protective equipment (PPE) enhancements.
Regular Training and Education
Regular training sessions are crucial for maintaining awareness and cultivating a safe working environment.
Implement training programs that include not only new employees but also refreshers for veteran staff.
These programs should cover the latest in safety protocols, emergency response plans, and practical skills needed to handle critical situations.
Incorporating real-world scenarios in training helps employees understand and practice how they should react during emergencies.
It also provides an opportunity to identify any gaps in the current procedures and address them promptly.
Fostering Open Communication
Communication is the backbone of any successful safety strategy.
Regular meetings, whether formal safety briefings or informal discussions, provide opportunities for workers to discuss safety concerns and suggestions.
Management must encourage and maintain an open-door policy, ensuring that workers feel comfortable reporting hazards or incidents.
Transparent communication between management and staff aids in building trust, ensuring that everyone is working towards the same objective of zero accidents.
Acknowledging and Analyzing Near Misses
Often overlooked, near misses provide valuable insights into potential safety issues.
A near miss is an event that could have led to an accident but didn’t, either by chance or timely intervention.
Acknowledging and analyzing these incidents are key components of a zero-accident strategy.
Investigation should not aim to place blame but to learn and improve.
These events are opportunities to reassess safety measures and prevent future serious incidents.
Implementing Technology
Technology can play a significant role in driving a zero-accident culture.
From wearable devices that monitor physical strain and environmental conditions to software that tracks incidents and near misses, there are numerous technologies available to enhance workplace safety.
Utilize data analytics to predict potential hazards and auto-generate reports that feed into the continuous improvement cycle.
Technology also improves communication channels between workers and management, making it easier to report and address safety concerns promptly.
Recognizing and Rewarding Safe Practices
Recognizing and rewarding safe behavior reinforces a commitment to the zero-accident goal.
Consider implementing incentive programs that acknowledge employees’ commitment to safety, be it through suggestions for improvements or consistent adherence to safety practices.
These recognitions, whether monetary bonuses or public acknowledgment in meetings, motivate employees to maintain safety-conscious behaviors and demonstrate that management values and supports safety efforts.
Regular Reviews and Updates
Safety plans should not be static documents.
Regularly review and update them in response to changes within the workplace, industry standards, and technological advancements.
Schedule periodic reviews of safety procedures and risk assessments to ensure they remain relevant and effective.
This continuous process of improvement helps maintain momentum towards achieving the zero-accident target.
Conclusion
The zero-accident goal is not merely an option; it’s a moral imperative.
Workplaces where managers and employees collaborate with dedication towards safety can significantly reduce the likelihood of accidents.
By fostering a strong safety culture, creating actionable safety plans, utilizing technology, and maintaining open communication, companies can take definitive steps toward achieving an accident-free environment.
Management and workplace synergy is essential, as the journey to zero accidents requires the commitment, participation, and proactive mindset of everyone involved.
資料ダウンロード
QCD調達購買管理クラウド「newji」は、調達購買部門で必要なQCD管理全てを備えた、現場特化型兼クラウド型の今世紀最高の購買管理システムとなります。
ユーザー登録
調達購買業務の効率化だけでなく、システムを導入することで、コスト削減や製品・資材のステータス可視化のほか、属人化していた購買情報の共有化による内部不正防止や統制にも役立ちます。
NEWJI DX
製造業に特化したデジタルトランスフォーメーション(DX)の実現を目指す請負開発型のコンサルティングサービスです。AI、iPaaS、および先端の技術を駆使して、製造プロセスの効率化、業務効率化、チームワーク強化、コスト削減、品質向上を実現します。このサービスは、製造業の課題を深く理解し、それに対する最適なデジタルソリューションを提供することで、企業が持続的な成長とイノベーションを達成できるようサポートします。
オンライン講座
製造業、主に購買・調達部門にお勤めの方々に向けた情報を配信しております。
新任の方やベテランの方、管理職を対象とした幅広いコンテンツをご用意しております。
お問い合わせ
コストダウンが利益に直結する術だと理解していても、なかなか前に進めることができない状況。そんな時は、newjiのコストダウン自動化機能で大きく利益貢献しよう!
(Β版非公開)