- お役立ち記事
- [Zinc-based low melting point alloy casting] Convenient for high-speed prototyping of jigs and inspection models
月間76,176名の
製造業ご担当者様が閲覧しています*
*2025年3月31日現在のGoogle Analyticsのデータより
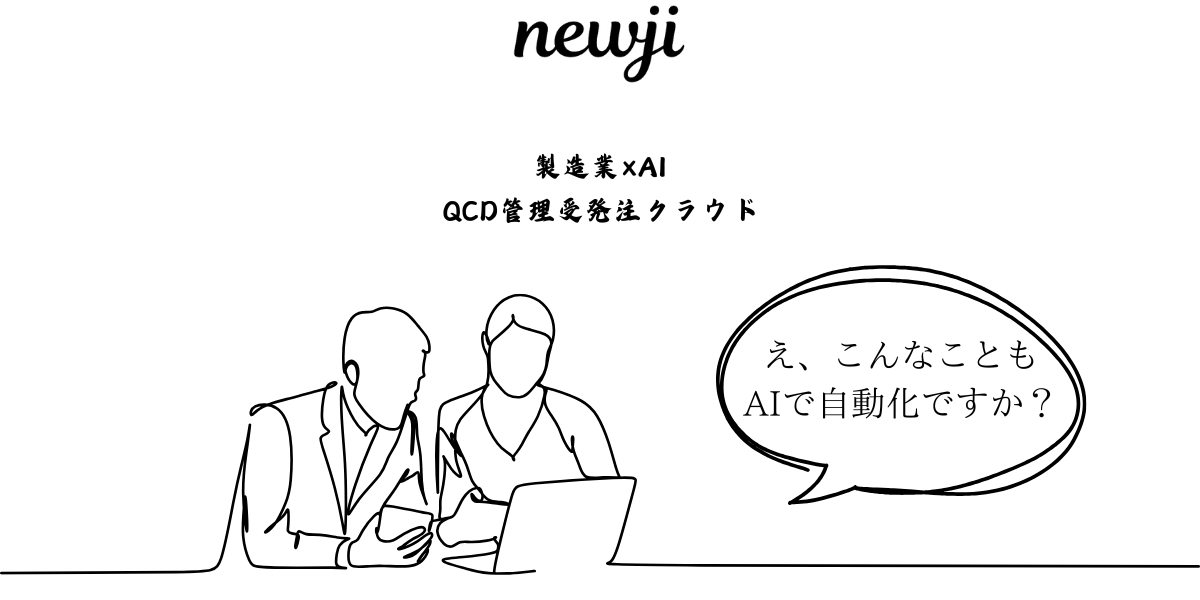
[Zinc-based low melting point alloy casting] Convenient for high-speed prototyping of jigs and inspection models
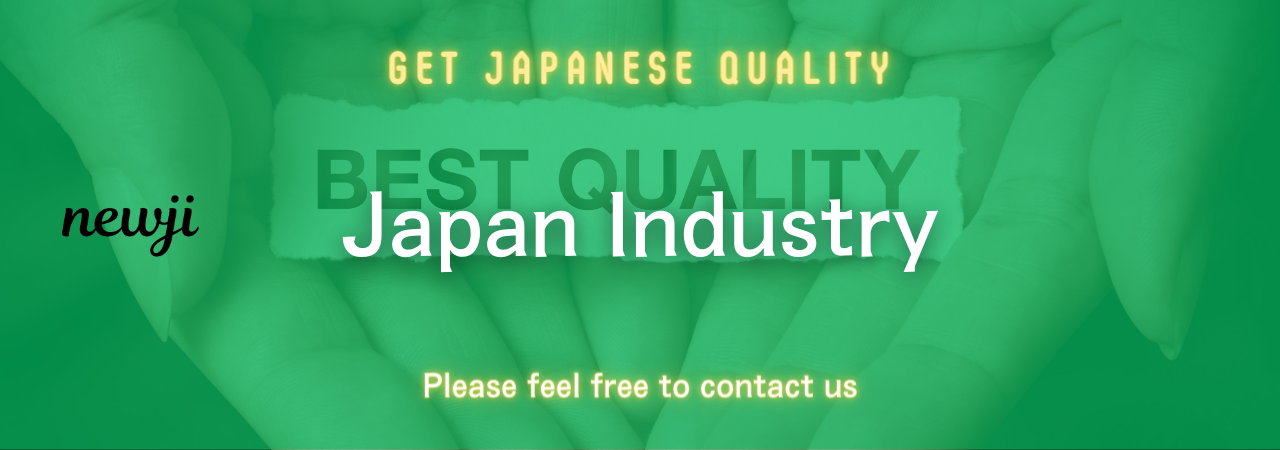
Zinc-based low melting point alloy casting is gaining popularity in various industries due to its convenient properties, especially for high-speed prototyping of jigs and inspection models.
目次
What is Zinc-based Low Melting Point Alloy?
Zinc-based low melting point alloys are materials that contain a high percentage of zinc combined with other elements such as aluminum, magnesium, and copper.
These alloys boast a lower melting point compared to many other metals, which makes them ideal for casting applications. Typically, their melting point ranges from about 200°C to 400°C.
This unique characteristic allows them to be used in situations where rapid prototyping is necessary, saving both time and resources.
Benefits of Using Zinc Alloys for Casting
Zinc-based alloys offer a variety of advantages in casting processes.
1. Cost-Effective
One of the primary benefits is their cost-effectiveness.
These alloys are relatively inexpensive compared to other metals, and their lower melting point can lead to significant energy savings during the casting process.
2. Fine Details
Zinc alloys can produce parts with intricate and precise details, ensuring high-quality outcomes for inspection models and jigs.
Their good fluidity allows them to fill molds with complex geometries, capturing fine features that might be difficult to achieve with other materials.
3. High-Production Efficiency
The quick setting time of zinc-based alloys means that parts can be produced rapidly, improving production efficiency.
The ability to quickly prototype allows manufacturers to test designs and make necessary adjustments in short timeframes.
4. Durability and Strength
Despite their low melting point, zinc alloys provide excellent durability and strength.
They can withstand moderate mechanical stresses while also offering good surface hardness, making them suitable for tools and functional prototypes.
5. Environmentally Friendly
Zinc is highly recyclable, making zinc-based alloys an environmentally friendly option.
Recycling helps reduce the need for new raw materials and minimizes waste, promoting sustainable manufacturing practices.
Applications in Prototyping Jigs and Inspection Models
Prototyping is crucial in modern manufacturing, allowing designers and engineers to bring their concepts to life quickly.
Zinc-based low melting point alloys are particularly useful in prototyping jigs and inspection models for several reasons.
1. Speed in Prototyping
In the fast-paced world of manufacturing, the speed at which prototypes can be made is key.
Zinc alloys allow for the quick turnaround time from design to physical model, enabling rapid iteration and testing of jigs and inspection tools.
2. Dimensional Accuracy
The precision offered by zinc alloys is critical in producing jigs and models that require high dimensional accuracy.
This accuracy aids in ensuring that the prototypes fulfill their intended purposes, down to the minutest detail.
3. Test for Functionality and Fit
Prototyping with zinc-based alloys gives manufacturers the opportunity to test the functionality and fit of their designs before committing to mass production.
This preemptive step can catch potential issues, reducing the likelihood of costly delays or errors in the final production stages.
4. Enhanced Customization
The versatility of zinc alloys allows for enhanced customization in prototyping.
Manufacturers can readily adjust designs based on feedback from prototypes, creating tailored solutions specific to their particular needs.
Process of Zinc Alloy Casting
Zinc alloy casting involves several standard steps, all designed to ensure a high-quality finished product.
1. Mold Preparation
The first step is preparing the mold, which can be made from a variety of materials depending on the complexity and the desired surface finish of the final product.
2. Melting and Pouring
Zinc-based alloys are melted at a controlled temperature, ensuring consistency and preventing potential defects.
Once melted, the alloy is poured into the mold, where it fills the cavity to take the shape of the desired prototype or jig.
3. Cooling and Solidification
After pouring, the alloy begins to cool and solidify.
The quick cooling rate associated with zinc alloys helps to speed up this stage, making it ideal for rapid prototyping needs.
4. Finishing
Finishing processes such as trimming, polishing, or coating are applied to the cast part to achieve the desired surface quality and meet specific application requirements.
The Future of Zinc Alloy Casting in Prototyping
The use of zinc-based low melting point alloys in casting is expected to grow as the demand for rapid and cost-effective prototyping solutions increases.
With advancements in casting technologies and materials science, these alloys continue to provide a practical, efficient solution for producing high-quality prototypes in various industries.
Manufacturers looking for quick, precise, and environmentally sustainable prototyping solutions should consider integrating zinc-based alloy casting into their processes.
The combination of speed, cost savings, and versatility makes zinc alloys an attractive choice for modern production requirements.
資料ダウンロード
QCD管理受発注クラウド「newji」は、受発注部門で必要なQCD管理全てを備えた、現場特化型兼クラウド型の今世紀最高の受発注管理システムとなります。
ユーザー登録
受発注業務の効率化だけでなく、システムを導入することで、コスト削減や製品・資材のステータス可視化のほか、属人化していた受発注情報の共有化による内部不正防止や統制にも役立ちます。
NEWJI DX
製造業に特化したデジタルトランスフォーメーション(DX)の実現を目指す請負開発型のコンサルティングサービスです。AI、iPaaS、および先端の技術を駆使して、製造プロセスの効率化、業務効率化、チームワーク強化、コスト削減、品質向上を実現します。このサービスは、製造業の課題を深く理解し、それに対する最適なデジタルソリューションを提供することで、企業が持続的な成長とイノベーションを達成できるようサポートします。
製造業ニュース解説
製造業、主に購買・調達部門にお勤めの方々に向けた情報を配信しております。
新任の方やベテランの方、管理職を対象とした幅広いコンテンツをご用意しております。
お問い合わせ
コストダウンが利益に直結する術だと理解していても、なかなか前に進めることができない状況。そんな時は、newjiのコストダウン自動化機能で大きく利益貢献しよう!
(β版非公開)