- お役立ち記事
- 高品質な製品を実現するための設計指針
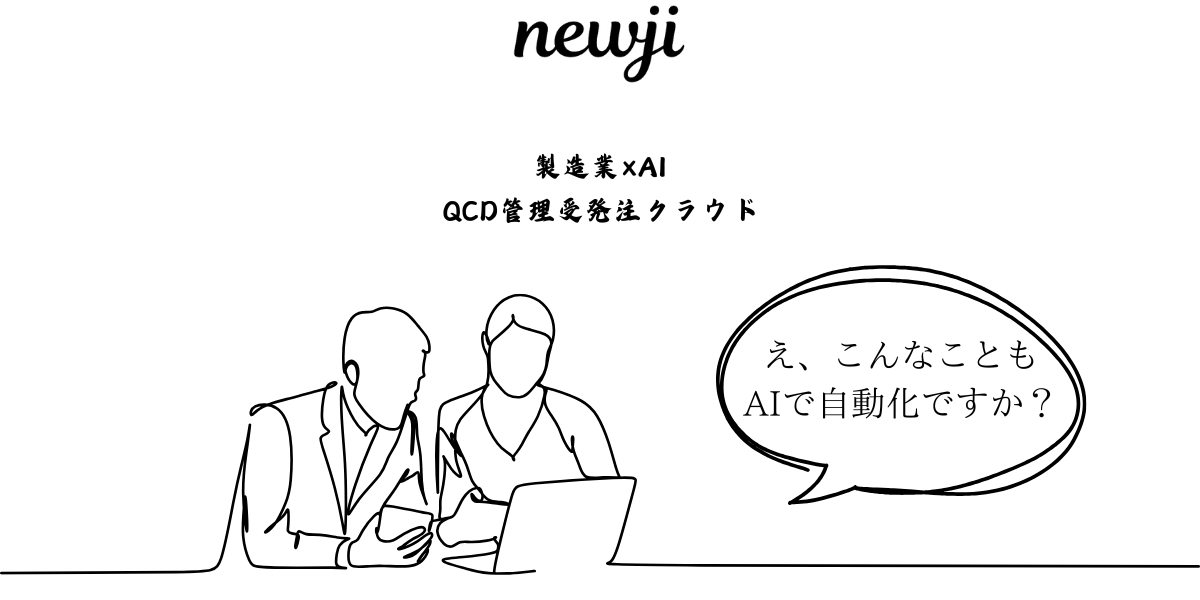
高品質な製品を実現するための設計指針
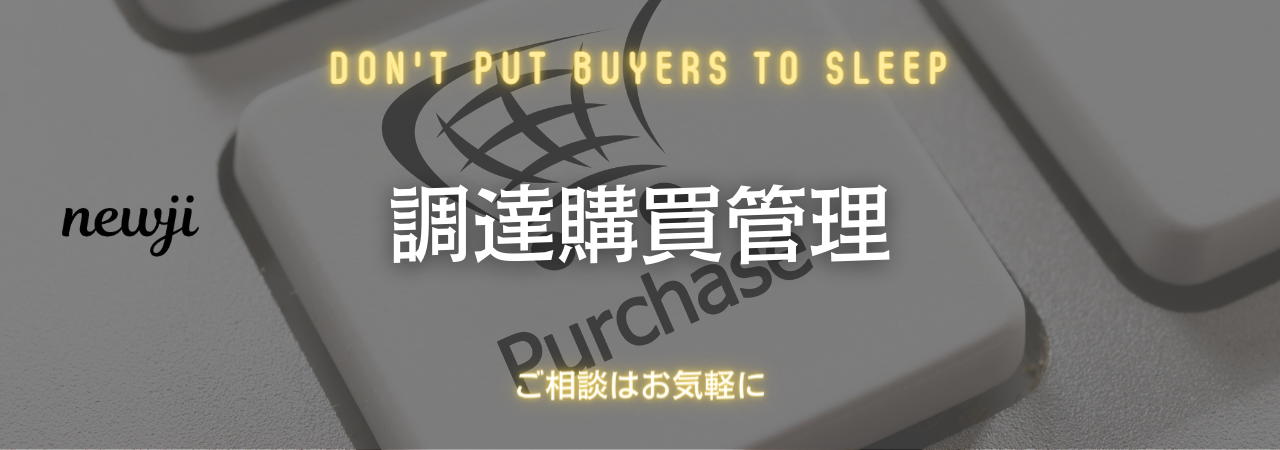
目次
高品質な製品を実現するための設計指針
製造業において、高品質な製品を実現するためには、設計段階からしっかりとした指針を持つことが必須です。
設計が製品の品質を左右する最も重要な要素だからです。
以下では、設計指針に関するいくつかの重要なポイントと具体的な実践方法について解説します。
設計指針の基本要素
機能要件の明確化
製品設計の第一歩は、何よりも機能要件の明確化です。
どのような機能を持たせるべきか、ターゲットユーザーがどのように使うのかを徹底して洗い出します。
具体的な要件を設計図に反映させることで、高い完成度と信頼性を持つ製品が生まれます。
製造プロセスの連携
設計段階で製造プロセスを無視してはなりません。
製造部門との緊密な連携が求められます。
例えば、部品の供給元や生産スケジュールを考慮した設計を行うことで、無駄のない製造プロセスを実現できます。
材料選定の重要性
使用する材料も製品の品質に大きく影響します。
耐久性、可加工性、コストなどを考慮した材料選定は、高品質な製品の基礎となります。
最新の材料技術や市場動向を把握し、最適な材料を選定することが重要です。
高品質を追求するための具体的戦略
DFM(Design for Manufacturing)の導入
DFMとは、製造を容易にするための設計手法です。
この手法を導入することで、設計と製造の整合性を高めることができます。
例えば、部品の標準化や組立ての簡便化を行うことで、製造現場での効率向上と不良率低減が期待できます。
FMEA(Failure Mode and Effects Analysis)の実施
FMEAは、設計の段階であらゆる故障モードを洗い出し、その影響と対策を検討する手法です。
これにより、リスクを事前に把握し対策を講じることができます。
FMEAは品質管理の強力なツールとして広く利用されています。
プロトタイピングと反復テスト
プロトタイプを制作し、実際の使用環境で試験を行うことは、設計の不具合や改善点を早期に発見するために非常に有効です。
特に、反復テストによって設計の問題点を繰り返し修正することで、高品質な製品を実現します。
サプライチェーンの最適化
サプライチェーンの管理も高品質な製品を実現するためには欠かせません。
部品供給元の品質管理や納期の確認を厳格に行い、必要な材料や部品が適時に供給される体制を確立します。
多くの企業が導入しているSRM(Supplier Relationship Management)システムを活用して、サプライチェーン全体の効率と透明性を向上させることが効果的です。
最新技術の活用
IoT技術の導入
IoT(Internet of Things)技術を活用したスマートファクトリーでは、製造ラインのリアルタイム監視やデータ分析が可能です。
これにより、異常を早期に検知し、迅速な対応が可能になります。
また、製品自体にもIoTを組み込むことで、ユーザーの使用状況をリアルタイムでモニタリングし、フィードバックを得ることができます。
AIと機械学習の応用
AI(人工知能)と機械学習を活用することで、設計の最適化や不良品の予測が可能になります。
例えば、大量の設計データを解析し、最適な設計パターンを見つけ出すことができます。
また、製造データを用いた予測モデルにより、不良品の発生を事前に予測し対策を講じることができます。
人材の育成とチームワーク
専門知識の研修と継続教育
高品質な製品を実現するためには、設計者や技術者の専門知識とスキルが重要です。
定期的な研修や継続的な教育プログラムを実施することで、最新の技術動向や設計手法を学ばせることが必要です。
クロスファンクショナルチームの編成
製品の設計から製造、品質管理に至るまで、多くの部門が関わります。
クロスファンクショナルチームを編成し、部門間の連携を強化することで、問題点を早期に特定し解決することができます。
特に、設計者、製造担当者、品質管理担当者が一体となって取り組むことで、全体の効率と品質を向上させることができます。
品質管理と改善策の実施
品質管理システムの導入
ISO9001などの品質管理システムを導入し、標準化された手順に基づいて製品を製造することが不可欠です。
このシステムにより、不良品やトラブル発生時の迅速な対応が可能となります。
フィードバックループの確立
ユーザーからのフィードバックを収集し、製品改善に反映させるプロセスも重要です。
特に、製品使用後の問題点や要望を設計に反映することで、次世代製品の品質向上につながります。
これは、顧客満足度を向上させるための重要なステップです。
まとめ
高品質な製品を実現するためには、設計指針の確立が鍵となります。
機能要件の明確化、製造プロセスとの連携、材料選定、DFMやFMEAなどの手法、そして最新技術の活用が挙げられます。
また、人材の育成やチームワーク、品質管理システムの導入、フィードバックループの確立も、すべてが一体となって取り組むべき要素です。
これらを包括的に実践することで、高品質な製品を安定して提供することができ、ひいては企業全体の競争力向上につながります。
資料ダウンロード
QCD調達購買管理クラウド「newji」は、調達購買部門で必要なQCD管理全てを備えた、現場特化型兼クラウド型の今世紀最高の購買管理システムとなります。
ユーザー登録
調達購買業務の効率化だけでなく、システムを導入することで、コスト削減や製品・資材のステータス可視化のほか、属人化していた購買情報の共有化による内部不正防止や統制にも役立ちます。
NEWJI DX
製造業に特化したデジタルトランスフォーメーション(DX)の実現を目指す請負開発型のコンサルティングサービスです。AI、iPaaS、および先端の技術を駆使して、製造プロセスの効率化、業務効率化、チームワーク強化、コスト削減、品質向上を実現します。このサービスは、製造業の課題を深く理解し、それに対する最適なデジタルソリューションを提供することで、企業が持続的な成長とイノベーションを達成できるようサポートします。
オンライン講座
製造業、主に購買・調達部門にお勤めの方々に向けた情報を配信しております。
新任の方やベテランの方、管理職を対象とした幅広いコンテンツをご用意しております。
お問い合わせ
コストダウンが利益に直結する術だと理解していても、なかなか前に進めることができない状況。そんな時は、newjiのコストダウン自動化機能で大きく利益貢献しよう!
(Β版非公開)