- お役立ち記事
- 製造現場の7つの無駄を排除する徹底した改善活動
月間76,176名の
製造業ご担当者様が閲覧しています*
*2025年3月31日現在のGoogle Analyticsのデータより
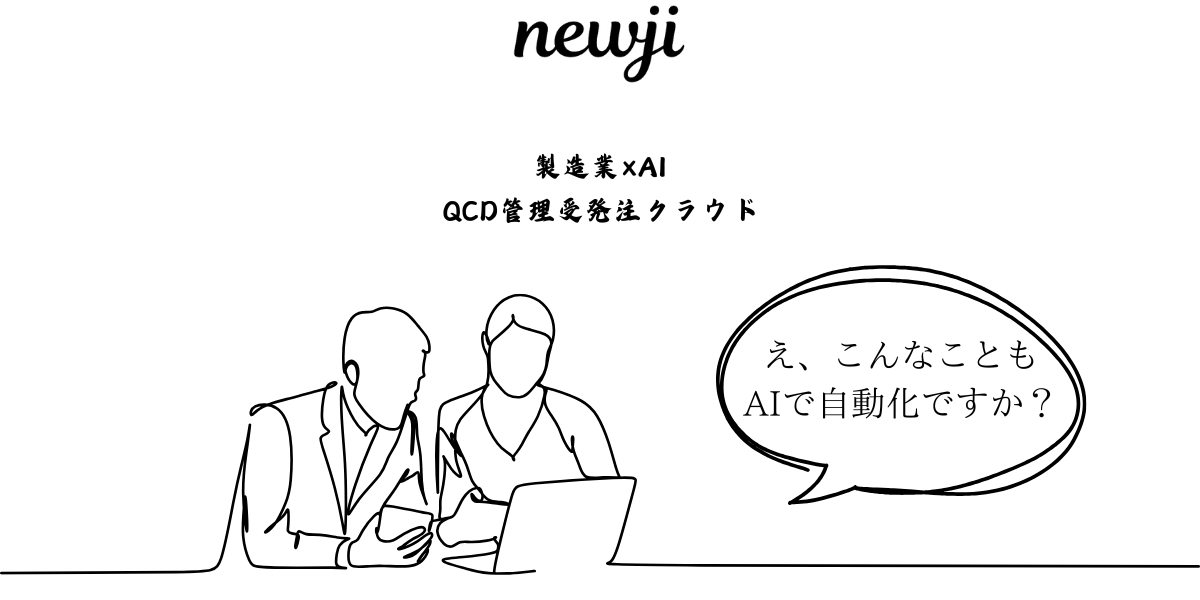
製造現場の7つの無駄を排除する徹底した改善活動
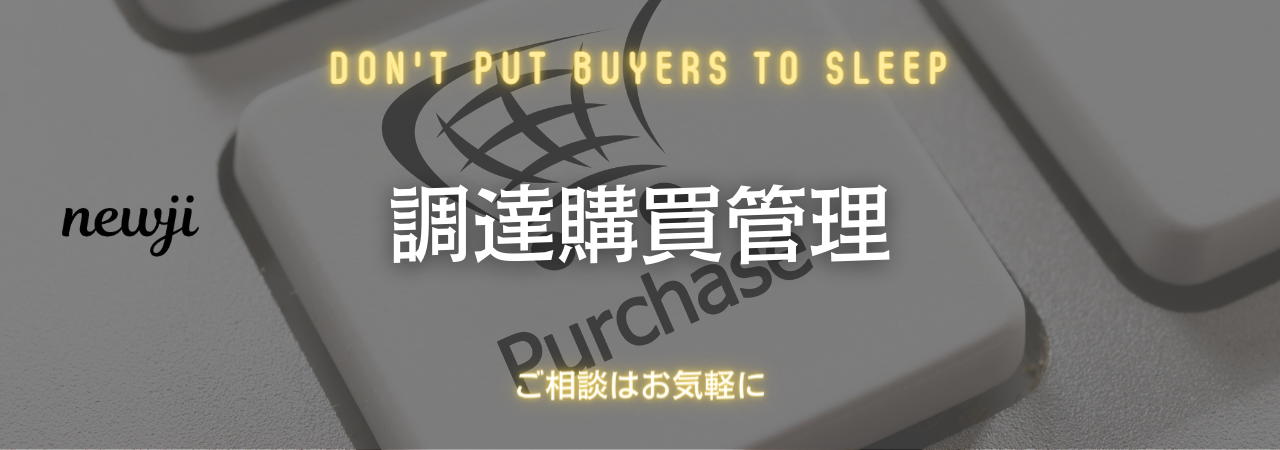
製造業における効率化とコスト削減は、永続的な課題です。
その中でも「7つの無駄」を認識し、それを排除することは極めて重要です。
「7つの無駄」とは、トヨタ生産方式(TPS)で定義された概念であり、「過剰生産」「手待ち」「不良品」「加工ミス」「在庫過多」「動作の無駄」「運搬の無駄」を指します。
この記事では、それぞれの無駄の定義と、具体的な排除方法、さらに最新の技術動向について解説します。
目次
1. 過剰生産の無駄
過剰生産は、必要以上に製品を作ることです。
これは在庫コストを増加させ、生産システム全体に悪影響を与えます。
原因と影響
過剰生産は、顧客の需要を無視した生産計画や、保守的なリスク管理(「もしも」のための過剰安全在庫)が原因となります。
これにより、不良在庫が増え、保管スペースが必要になり、資金が無駄になります。
排除方法
過剰生産を排除するためには、以下の方法があります。
1. 需要予測の精度を向上
顧客の需要を正確に予測し、生産計画に反映します。
2. ジャストインタイム(JIT)生産方式の導入
必要な物を、必要な時に、必要な量だけ生産することで、過剰生産を防ぎます。
3. 柔軟な生産システムの構築
需要の変動に対応できる柔軟な生産システムを構築することが有効です。
2. 手待ちの無駄
手待ちは、作業員や機械が作業を待っている状態です。
これも生産効率を低下させる大きな要因となります。
原因と影響
手待ちの無駄を引き起こす要因には、機械の故障、材料不足、作業指示の遅れなどがあります。
これにより、生産ラインの停滞や納期遅延が発生し、顧客満足度の低下を招きます。
排除方法
手待ちの無駄を排除するためには以下の方法があります。
1. 予防保全の徹底
機械の故障を未然に防ぐため、定期的なメンテナンスを行います。
2. 材料管理システムの強化
原材料の在庫を適切に管理し、欠品を防ぎます。
3. リアルタイムの作業指示
生産スケジュールをリアルタイムで把握し、適時に作業指示を行います。
3. 不良品の無駄
不良品は、顧客に提供できない製品を指します。
これによって再作業や廃棄コストが増加します。
原因と影響
設計ミス、素材の品質不良、作業の誤りなどが不良品の主な原因です。
これにより、顧客の信頼を失い、最悪の場合、リコールが発生することもあります。
排除方法
不良品の無駄を排除するためには以下の方法があります。
1. 品質管理の徹底
作業マニュアルの整備や品質チェックを強化します。
2. トレーニングの充実
作業者のスキルを向上させるための教育訓練を行います。
3. 品質データの活用
生産プロセスのデータを収集・分析し、問題点を早期に発見します。
4. 加工ミスの無駄
加工ミスとは、不要な加工や不適切な加工を指します。
これにより、時間と材料が無駄になります。
原因と影響
加工ミスは、設計図面の誤解、作業指示の不備、機械の設定ミスなどが原因です。
これによって、再加工や廃棄が必要になり、コストが増加します。
排除方法
加工ミスを排除するためには以下の方法があります。
1. 設計レビューの実施
設計段階でのレビューを徹底し、ミスを未然に防ぎます。
2. 作業指示の明確化
明確な作業手順書や標準作業を設定し、誤操作を防ぎます。
3. 機械の精度向上
定期的なキャリブレーションや精度維持を行います。
5. 在庫過多の無駄
在庫過多は、必要以上に材料や部品を保管することです。
これにより、保管コストやスペースが無駄になります。
原因と影響
在庫過多は、過剰生産や需要予測の誤りによって発生します。
これにより、保管費用が増加し、資金が滞留します。
排除方法
在庫過多を排除するためには以下の方法があります。
1. 需要予測精度の向上
精度の高い需要予測を行い、適正な在庫管理を実施します。
2. ジャストインタイム(JIT)方式の導入
必要なときに必要な量だけ供給することで、在庫を最小限に抑えます。
3. サプライチェーンの最適化
供給業者との連携を強化し、在庫の過不足を防ぎます。
6. 動作の無駄
動作の無駄とは、作業における不要な動きを指します。
これにより、作業効率が低下します。
原因と影響
動作の無駄は、不適切な作業環境や不明瞭な作業手順から発生します。
これにより、作業時間が延び、疲労が増大します。
排除方法
動作の無駄を排除するためには以下の方法があります。
1. 動作分析の実施
作業の流れを分析し、不要な動作を排除します。
2. 作業環境の整備
作業台や工具の配置を見直し、作業環境を最適化します。
3. 5S活動の推進
整理、整頓、清掃、清潔、しつけを徹底し、効率的な作業を行います。
7. 運搬の無駄
運搬の無駄とは、材料や製品の不要な移動を指します。
これにより、時間とコストが無駄になります。
原因と影響
運搬の無駄は、設備や作業場のレイアウトが不適切であることから発生します。
これにより、移動時間が増え、作業効率が低下します。
排除方法
運搬の無駄を排除するためには以下の方法があります。
1. レイアウトの見直し
最適な作業場のレイアウトを設計し、運搬距離を短縮します。
2. コンベアシステムの導入
自動化された運搬システムを導入し、人手による運搬を削減します。
3. 生産フローの最適化
作業の流れを見直し、効率的な運搬ルートを設定します。
最新の技術動向
製造現場の7つの無駄を排除するためには、最新の技術を活用することが不可欠です。
IoTとAIの活用
IoT(モノのインターネット)とAI(人工知能)は、製造現場の無駄を大幅に削減する技術です。
リアルタイムでデータを収集し、AIを用いて分析することで、問題点を早期に発見し、改善策を講じることが可能です。
自動化技術
ロボティクスや自動搬送システム(AGV)は、運搬や単純作業を自動化し、人手による作業を削減します。
これにより、効率的な生産が実現します。
生産管理システム(MES)
製造実行システム(MES)を導入することで、生産の全プロセスをリアルタイムで監視・管理します。
これにより、無駄を早期に発見し、迅速な対応が可能となります。
製造現場の7つの無駄を排除することは、効率的な生産とコスト削減を実現する上で極めて重要です。
過剰生産、手待ち、不良品、加工ミス、在庫過多、動作の無駄、運搬の無駄を認識し、それぞれの無駄を排除する具体的な方法を実践することで、製造現場は大きく改善されます。
さらに、最新の技術を積極的に活用することで、一層の効率化を図ることが可能です。
製造現場の改善活動は一朝一夕には成し得ませんが、継続的な努力と工夫によって無駄のない、効率的な生産体制を築くことができます。
これからも、製造業の発展に寄与するために、一層の改善活動を続けて参りましょう。
資料ダウンロード
QCD管理受発注クラウド「newji」は、受発注部門で必要なQCD管理全てを備えた、現場特化型兼クラウド型の今世紀最高の受発注管理システムとなります。
ユーザー登録
受発注業務の効率化だけでなく、システムを導入することで、コスト削減や製品・資材のステータス可視化のほか、属人化していた受発注情報の共有化による内部不正防止や統制にも役立ちます。
NEWJI DX
製造業に特化したデジタルトランスフォーメーション(DX)の実現を目指す請負開発型のコンサルティングサービスです。AI、iPaaS、および先端の技術を駆使して、製造プロセスの効率化、業務効率化、チームワーク強化、コスト削減、品質向上を実現します。このサービスは、製造業の課題を深く理解し、それに対する最適なデジタルソリューションを提供することで、企業が持続的な成長とイノベーションを達成できるようサポートします。
製造業ニュース解説
製造業、主に購買・調達部門にお勤めの方々に向けた情報を配信しております。
新任の方やベテランの方、管理職を対象とした幅広いコンテンツをご用意しております。
お問い合わせ
コストダウンが利益に直結する術だと理解していても、なかなか前に進めることができない状況。そんな時は、newjiのコストダウン自動化機能で大きく利益貢献しよう!
(β版非公開)