- お役立ち記事
- 非破壊試験で製品の内部欠陥を検出する方法
月間76,176名の
製造業ご担当者様が閲覧しています*
*2025年3月31日現在のGoogle Analyticsのデータより
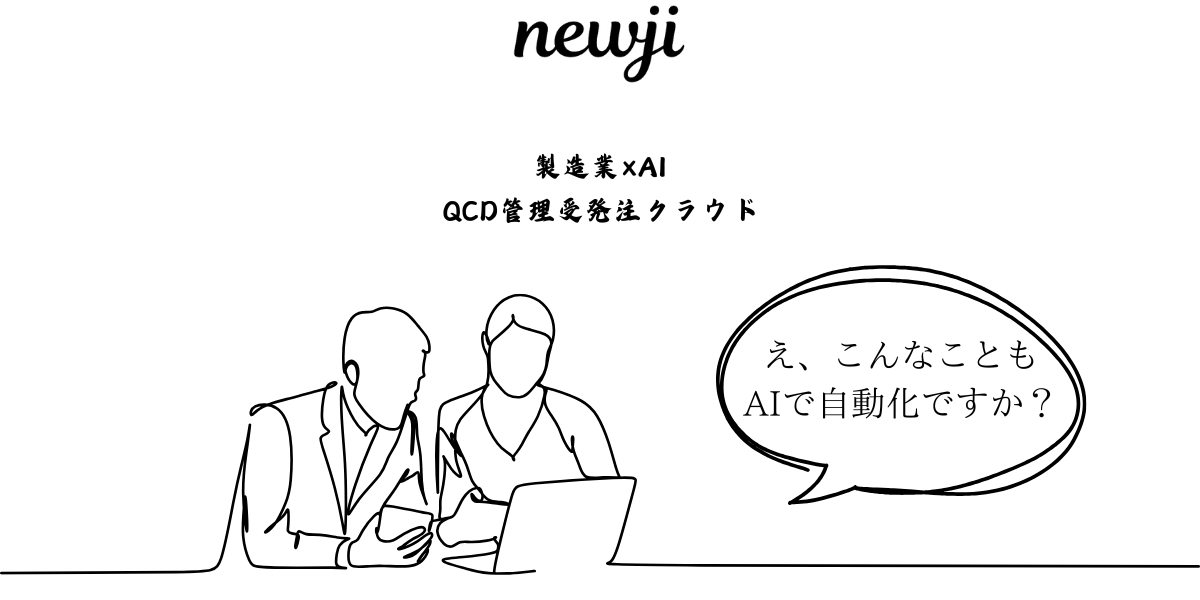
非破壊試験で製品の内部欠陥を検出する方法
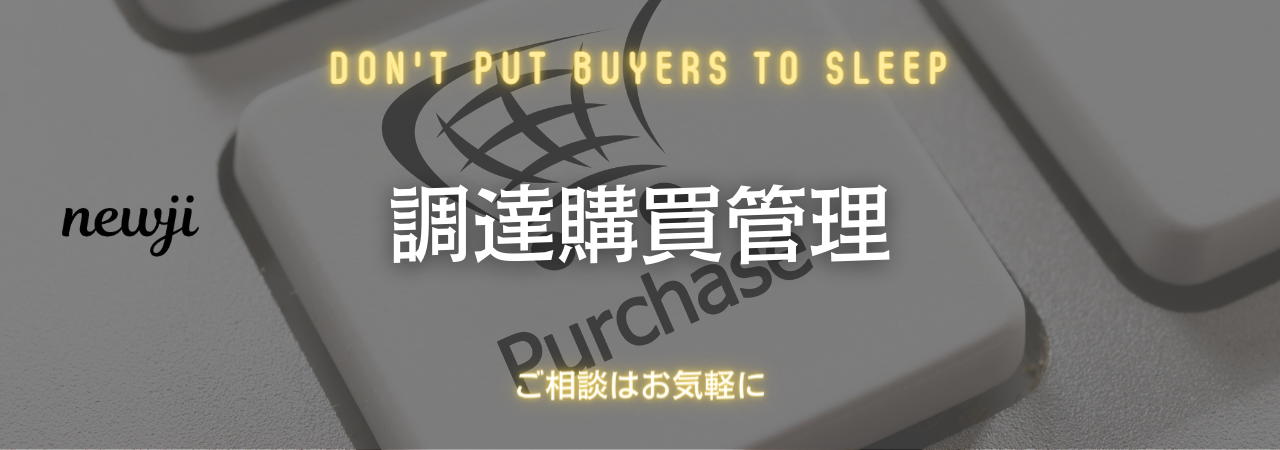
目次
非破壊試験とは?
非破壊試験(Nondestructive Testing, NDT)は、その名の通り、製品や構造物を破壊せずに内部や表面の欠陥を検出する方法です。
これにより、製品の品質や信頼性を確保しながら、コストも抑えることが可能になります。
具体的な手法には、超音波検査、X線検査、磁粉探傷検査、浸透探傷検査などがあります。
主要な非破壊試験の種類とその原理
超音波探傷検査(UT)
超音波探傷検査は、高周波の音波を用いて内部欠陥を検出します。
プローブを用いて音波を材料内部に送信し、反射波を受信することで欠陥箇所を特定します。
超音波探傷検査の大きな利点は、検査深度が深く、非常に細かな欠陥まで検出できることです。
一方で、曲面や複雑な形状の部品には適さない可能性があります。
X線検査(RT)
X線検査は、X線やガンマ線を利用して内部構造を可視化します。
射出された放射線が材料を通過し、フィルムやデジタルセンサーに画像として記録されます。
欠陥がある箇所は放射線の透過率が異なるため、画像として明暗の違いが表現されます。
X線検査は、金属や合金、厚みのある材料の検査に適しています。
その反面、放射線を取り扱うため、安全性や法規制に準拠する必要があります。
磁粉探傷検査(MT)
磁粉探傷検査は、磁性材に磁場をかけて発生する漏れ磁束を検出する方法です。
この漏れ磁束に磁粉を適用することで、表面や浅い内部の欠陥が目視で確認できます。
この手法のメリットは、速やかに大面積を検査できる点です。
しかし、検査対象が磁性材に限られるため、それ以外の材質には適用できません。
浸透探傷検査(PT)
浸透探傷検査は、表面欠陥を検出するために用いられる技法です。
まず、浸透液を対象物に塗布し、欠陥内に染み込ませます。
その後、余剰の浸透液を洗い流し、現像液を塗布することで欠陥部分を浮き上がらせます。
表面の微小なクラックやピンホールを確実に検出できるため、非磁性材にも適用可能です。
一方で、内部の欠陥を検出できない点に注意が必要です。
非破壊試験のメリットとデメリット
メリット
1. **製品や部品の信頼性向上**:
非破壊試験は製品の重大な欠陥を早期に発見することができ、製品の信頼性を確保します。
2. **コスト削減**:
欠陥を事前に発見し、問題のある部品の交換や修理によって最終製品の廃棄を防ぐことができます。
3. **生産効率の向上**:
工程の早い段階で欠陥を見つけることができるため、再作業が少なくなり、全体の生産効率が向上します。
デメリット
1. **専用機器と熟練技術者が必要**:
非破壊試験は高価な機器や熟練した技術者を必要とするため、初期投資が大きくなります。
2. **時間とコストがかかるケースも**:
複雑な製品や大規模な構造物の検査は時間とコストがかかることがあります。
3. **一部の検査手法には法規制がある**:
例えば、X線検査では放射線を取り扱うため、安全管理が不可欠であり、法規制に遵守する必要があります。
最新技術動向: AIと機械学習の導入
近年、AIと機械学習を用いた非破壊試験の研究が進んでいます。
例えば、画像解析技術を利用してX線画像や超音波信号から欠陥を自動的に検出するシステムが開発されています。
従来手法と比較して、AI技術を導入することで検査のスピードと精度の向上が期待できます。
また、人間の主観に依存しないため、客観的かつ再現性のある評価が可能になります。
いくつかの研究では、ディープラーニングを活用したモデルが、熟練検査員と同等の精度で欠陥を検出できることが示されています。
調達購買部門が知っておきたいこと
調達購買部門としては、非破壊試験の理解が必要不可欠です。
部品や原材料の品質を確保するために、適切な非破壊試験を選定し、サプライヤーと連携することが求められます。
検査コストの見積もりと交渉
非破壊試験には異なるコストが伴います。
これを正確に見積もることでサプライヤーとの交渉がスムーズに進みます。
また、必要な検査の種類と頻度を見極めることも重要です。
技術トレンドの理解と導入
AIや機械学習といった新しい技術動向を理解し、必要に応じて導入を検討することが調達購買部門の競争力向上につながります。
最新技術を取り入れることで、検査の精度や効率が向上し、全体の品質管理も強化されます。
具体的な非破壊試験導入事例
ある自動車メーカーでは、エンジン部品の品質向上を目指して、超音波探傷検査を導入しました。
導入前は目視検査が主であったため、微細な欠陥を見逃すことが多かったのですが、超音波探傷検査を導入することで、早期に欠陥を検出し、不具合のリスクを大幅に低減しました。
また、航空機製造業界では、多数の部品に対してX線検査を実施しており、高精度な検査結果に基づいて製品の信頼性を確保しています。
まとめ
非破壊試験は、製品を破壊せずに内部や表面の欠陥を検出するための重要な手法です。
超音波探傷検査、X線検査、磁粉探傷検査、浸透探傷検査といった多くの方法があり、それぞれに利点と制約があります。
これらの手法を効果的に活用することで、製品の信頼性向上、コスト削減、生産効率の向上など多くのメリットが得られます。
特に、AIと機械学習を組み合わせた最新技術の導入は、検査プロセスの更なる進化を促進します。
調達購買部門としては、これらの技術を理解し、適切に選定・導入することで、製品の品質管理に寄与することが求められます。
非破壊試験の知識を深め、サプライチェーン全体の信頼性向上に向けて努力しましょう。
資料ダウンロード
QCD管理受発注クラウド「newji」は、受発注部門で必要なQCD管理全てを備えた、現場特化型兼クラウド型の今世紀最高の受発注管理システムとなります。
ユーザー登録
受発注業務の効率化だけでなく、システムを導入することで、コスト削減や製品・資材のステータス可視化のほか、属人化していた受発注情報の共有化による内部不正防止や統制にも役立ちます。
NEWJI DX
製造業に特化したデジタルトランスフォーメーション(DX)の実現を目指す請負開発型のコンサルティングサービスです。AI、iPaaS、および先端の技術を駆使して、製造プロセスの効率化、業務効率化、チームワーク強化、コスト削減、品質向上を実現します。このサービスは、製造業の課題を深く理解し、それに対する最適なデジタルソリューションを提供することで、企業が持続的な成長とイノベーションを達成できるようサポートします。
製造業ニュース解説
製造業、主に購買・調達部門にお勤めの方々に向けた情報を配信しております。
新任の方やベテランの方、管理職を対象とした幅広いコンテンツをご用意しております。
お問い合わせ
コストダウンが利益に直結する術だと理解していても、なかなか前に進めることができない状況。そんな時は、newjiのコストダウン自動化機能で大きく利益貢献しよう!
(β版非公開)