- お役立ち記事
- 自社工場と外注の最適バランスで製造原価の最小化を図る
月間77,185名の
製造業ご担当者様が閲覧しています*
*2025年2月28日現在のGoogle Analyticsのデータより
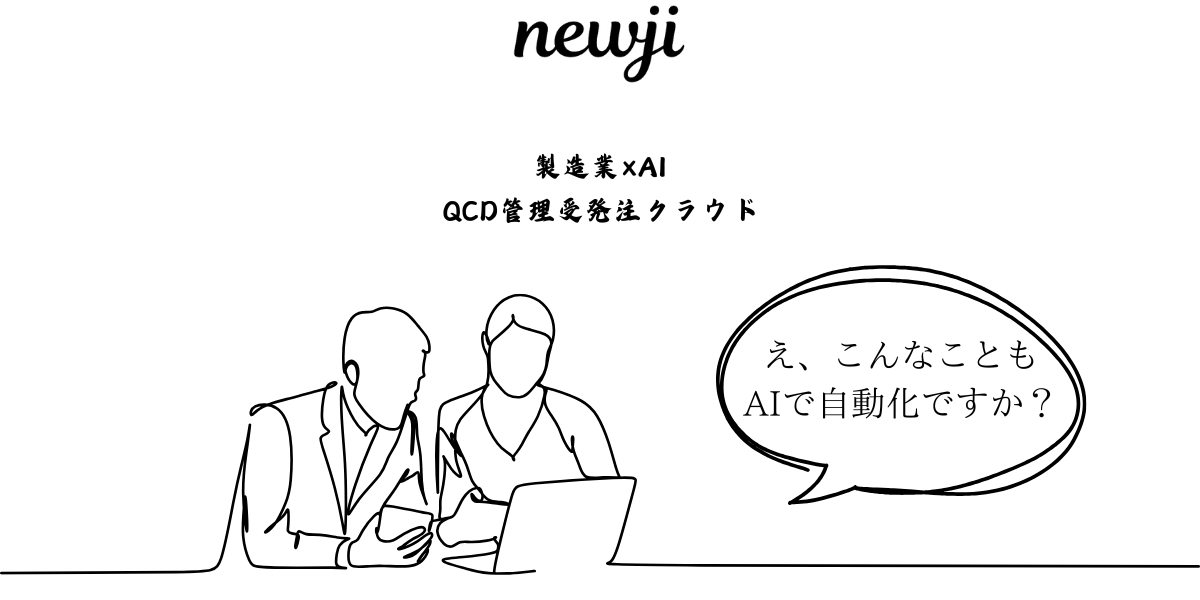
自社工場と外注の最適バランスで製造原価の最小化を図る
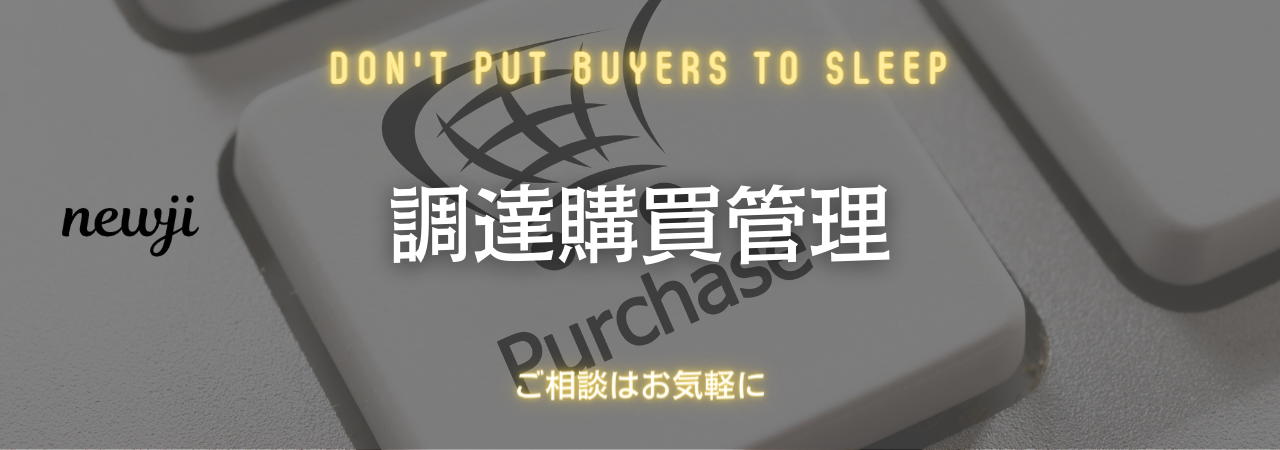
製造業において、製品の製造原価を最小限に抑えることは、企業の利益を最大化するための重要な課題です。
特に、自社工場での製造と外注(アウトソーシング)との最適なバランスを見極めることは、コスト削減のための鍵となります。
この記事では、自社工場と外注の最適バランスを見つけ出し、製造原価の最小化を図るための実践的な方法を解説します。
目次
自社工場と外注のメリットとデメリット
自社工場のメリット
1. 品質管理のしやすさ:
自社工場で製造することで、品質管理がしやすくなります。
品質基準を直接監視でき、その標準を維持するための迅速な対応が可能です。
2. 機密保持:
自社工場での製造は、機密情報を外部に出さないという点でも非常に優れています。
特に技術力やデザインが競争優位の源泉である場合、自社工場はその秘密を守る強力な手段となります。
3. 柔軟な生産対応:
市場の需要変動や新製品の導入に対して、柔軟に対応できるのも自社工場の強みです。
自社工場のデメリット
1. 固定費が高い:
設備投資や人件費、維持費といった固定費が高くつくため、生産量が少ないとコストが重くのしかかります。
2. 需要変動に対するリスク:
需要が急減した場合でも、生産能力を減らすことは容易ではなく、過剰な在庫や遊休設備が発生するリスクがあります。
外注のメリット
1. 固定費の抑制:
外注を利用することで、自社の生産設備や人員にかかる固定費を抑えることができます。
2. 専門技術の利用:
専門的な技術や設備を持つ外注先に依頼することで、製品の品質や性能を向上させることができます。
3. フレキシビリティ:
生産量や製品ラインナップの変動に対して、柔軟に対応可能な外注先を選ぶことで、需要に合わせた生産が可能です。
外注のデメリット
1. 品質管理の難しさ:
外注先での品質管理が十分でない場合、製品の品質にばらつきが生じるリスクがあります。
2. 納期遅延のリスク:
外注先の都合で納期が遅れる、といったリスクは常に存在します。
特に外注先の管理が不十分だと、自社の生産計画全体に支障をきたす可能性があります。
3. 追加コスト:
輸送費や契約管理費などの追加コストがかかる場合があります。
最適バランスを探るための要点
1. コスト分析
まず、自社製造と外注それぞれのコストを詳細に分析することが重要です。
これには、材料費、人件費、設備維持費などの直接コストに加え、管理費や輸送費などの間接コストも含まれます。
2. 製品ごとの特性を考慮
全ての製品を同じ戦略で扱うのではなく、各製品の特性に応じた最適な製造方法を考えることが重要です。
例えば、高度な技術を要する部品は自社製造し、標準化された部品は外注する、といった具合です。
3. サプライチェーンの透明性
外注先の選定にあたっては、サプライチェーンの透明性を確保することが重要です。
品質管理体制、労働環境、コンプライアンス状況などを事前に確認し、信頼できるパートナーを選ぶことが不可欠です。
4. 柔軟な契約とリレーションシップ
外注契約は柔軟であることが望ましいです。
例えば、需要変動に応じて生産量を調整できる契約を結ぶことで、リスクを軽減できます。
また、信頼関係を構築するために、定期的なコミュニケーションを図り、問題発生時には迅速に対応する姿勢が求められます。
最新技術動向とその活用
IoTとスマートマニュファクチャリング
インターネット・オブ・シングズ(IoT)の技術を活用することで、自社工場と外注先の生産状況をリアルタイムで把握することができます。
これにより、生産効率の最適化や品質管理の向上が図れます。
AIとデータ解析
人工知能(AI)とデータ解析の技術を用いることで、コスト最小化のための最適バランスをより正確にシミュレーションすることが可能です。
生産データをもとに、需要予測や供給計画を精緻化することで、効率的な生産体制を確立できます。
実践例:成功事例と失敗事例
成功事例
ある大手製造業メーカーでは、高度な技術を要する部品は自社工場で製造し、標準化された部分はコストの低い地域の外注先に委託することで、全体の製造コストを大幅に削減しました。
これにより、企業は約10%のコスト削減を達成し、その分を新技術開発や市場拡大に投資することができました。
失敗事例
一方、外注先の品質管理が不十分であったために、製品に重大な不良が発生したケースもあります。
ある企業は、外注先の選定時にコスト削減を重視しすぎた結果、品質トラブルが多発し、結果的にリコール費用やブランドイメージの低下につながりました。
自社工場と外注の最適バランスを見極めることは、製造業におけるコスト最小化の鍵となります。
それぞれのメリット・デメリットを把握し、コスト分析や製品特性の考慮、サプライチェーンの透明性の確保などを行うことで、効率的な生産体制を構築することが可能です。
また、最新の技術動向を活用することで、さらに効率的な運営が期待できます。
成功事例や失敗事例から学び、現実的な戦略を立てることで、企業の競争力を一層高めることができるでしょう。
資料ダウンロード
QCD管理受発注クラウド「newji」は、受発注部門で必要なQCD管理全てを備えた、現場特化型兼クラウド型の今世紀最高の受発注管理システムとなります。
ユーザー登録
受発注業務の効率化だけでなく、システムを導入することで、コスト削減や製品・資材のステータス可視化のほか、属人化していた受発注情報の共有化による内部不正防止や統制にも役立ちます。
NEWJI DX
製造業に特化したデジタルトランスフォーメーション(DX)の実現を目指す請負開発型のコンサルティングサービスです。AI、iPaaS、および先端の技術を駆使して、製造プロセスの効率化、業務効率化、チームワーク強化、コスト削減、品質向上を実現します。このサービスは、製造業の課題を深く理解し、それに対する最適なデジタルソリューションを提供することで、企業が持続的な成長とイノベーションを達成できるようサポートします。
製造業ニュース解説
製造業、主に購買・調達部門にお勤めの方々に向けた情報を配信しております。
新任の方やベテランの方、管理職を対象とした幅広いコンテンツをご用意しております。
お問い合わせ
コストダウンが利益に直結する術だと理解していても、なかなか前に進めることができない状況。そんな時は、newjiのコストダウン自動化機能で大きく利益貢献しよう!
(β版非公開)