- お役立ち記事
- PDCAサイクルの運用と活用: 品質改善と業務効率化のためのサイクルマネジメント
月間76,176名の
製造業ご担当者様が閲覧しています*
*2025年3月31日現在のGoogle Analyticsのデータより
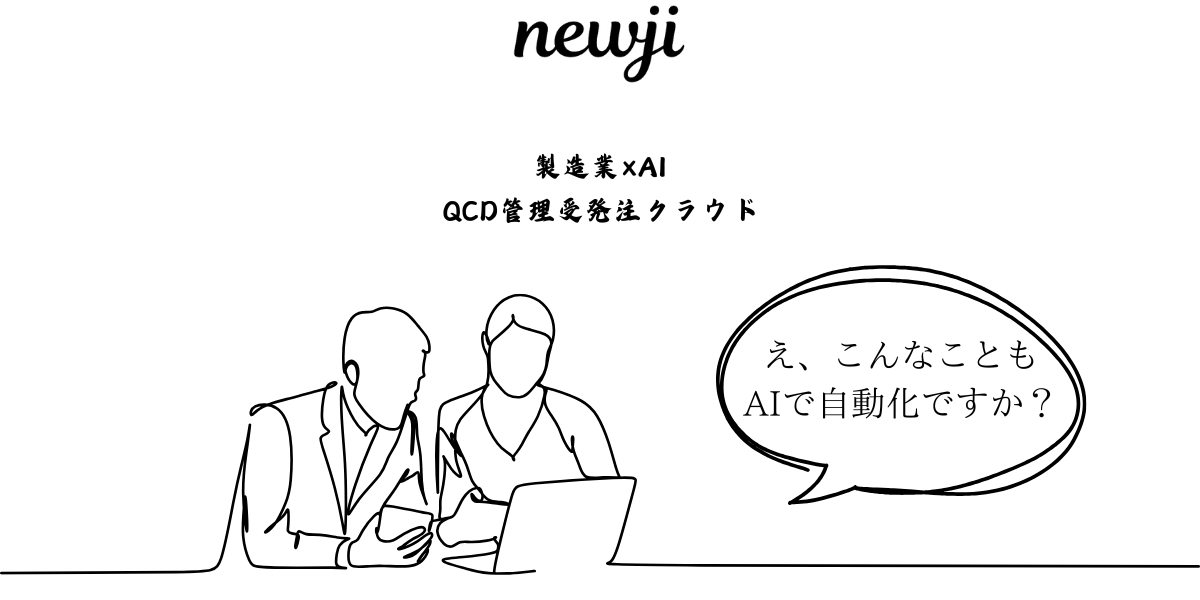
PDCAサイクルの運用と活用: 品質改善と業務効率化のためのサイクルマネジメント
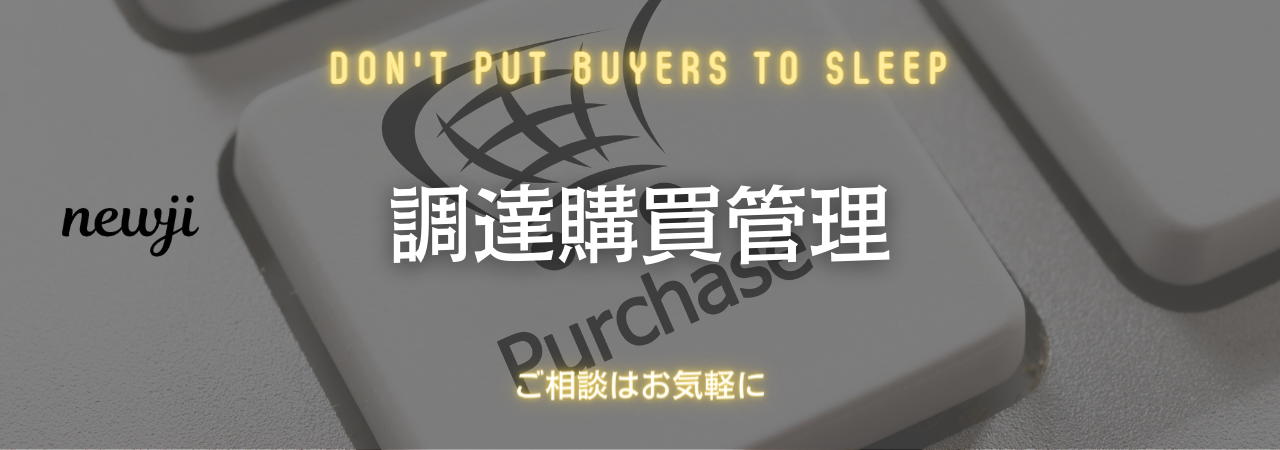
目次
はじめに: PDCAサイクルとは何か
製造業における品質改善と業務効率化は、企業の競争力を保つために極めて重要です。
その中で、PDCAサイクルの運用と活用は欠かせない要素と言えます。
PDCAサイクルとは、「Plan(計画)」「Do(実行)」「Check(評価)」「Act(改善)」の4つのステップを繰り返すことで、継続的な改善を図るためのマネジメント手法です。
これにより、製造プロセスや業務フローを最適化し、品質向上とコストダウンを実現することが可能です。
PDCAサイクルの基本構造
Plan(計画)
最初のステップである「Plan」では、目標設定とそれを達成するための具体的な計画を立てます。
例えば、新しい材料の採用によるコスト削減や、不良品率の低減を目指す計画などが考えられます。
この段階で大切なのは、達成可能で具体的な目標を設定し、どのような手順で進めるかを詳細に決めることです。
Do(実行)
「Plan」で立てた計画に基づき、実際に行動を起こすのが「Do」のステップです。
新しい材料を試用する、製造プロセスの一部を変更する、スタッフへのトレーニングを実施するなどの具体的な活動を行います。
また、この段階では記録を取ることが重要です。
どのような手順で、どの程度の期間でどのような結果が得られたかを詳しく記録することで、次の「Check」ステップでの評価に役立ちます。
Check(評価)
「Do」で実行した活動が計画通りに進んでいるか、目標が達成されたかを評価するのが「Check」のステップです。
得られたデータを基に、計画の効果を客観的に評価します。
この評価によって、実行内容が効果的だったのか、あるいは改善が必要かを分析します。
Act(改善)
最後のステップである「Act」では、「Check」での評価を基に次のアクションを決定します。
もし計画がうまくいった場合は、その手法を標準として確立し、さらに他のプロセスにも応用することが考えられます。
逆に、目標に達しなかった場合は、原因を分析し、新たな計画を立てる必要があります。
こうしてPDCAサイクルを繰り返すことで、継続的な改善を達成することができます。
PDCAサイクルが製造業で特に重要な理由
継続的な品質改善
製造業では品質が最も重要な要素の一つです。
PDCAサイクルを導入することで、製品の品質を継続的に改善することができます。
例えば、不良品率の低減、加工精度の向上、顧客満足度の向上など、様々な品質改善につながります。
業務効率の向上
PDCAサイクルにより業務プロセスを継続的に見直すことで、無駄を削減し、効率を向上させることが可能です。
例えば、製造ラインのレイアウト変更や作業手順の見直し、スタッフのスキルアップなどが挙げられます。
コストダウンの実現
品質改善と業務効率化が進むことで、結果的に製造コストの削減が図れます。
新しい材料や部品の採用、在庫管理の最適化、エネルギー使用の見直しなどもコストダウンに直結します。
PDCAサイクルを効果的に運用するためのポイント
明確な目標設定
PDCAサイクルを成功させるためには、最初の「Plan」の段階で明確な目標を設定することが重要です。
具体的かつ達成可能な目標を設定することで、全てのステップがスムーズに進行します。
データの収集と活用
「Do」ステップでの活動記録や、「Check」ステップでの評価では、データの収集と分析が欠かせません。
具体的な数値やデータを基に評価することで、客観的な判断が可能になります。
柔軟な対応能力
「Act」ステップでは、評価結果に基づき柔軟に対応することが求められます。
計画がうまくいかなかった場合には、その原因を速やかに分析し、新たなアプローチを試みることが重要です。
実際の現場でのPDCAサイクル運用の事例
事例1: 製造ラインのレイアウト変更
ある製造工場では、製造ラインのレイアウトを変更することで業務効率を向上させる計画を立てました。
「Plan」の段階では、現状の問題点を洗い出し、最適なレイアウトを設計しました。
「Do」では、新しいレイアウトを試行的に導入し、その効果を観察しました。
結果的に、作業フローがスムーズになり、製品の生産速度が向上しました。
「Check」の段階では、明らかな改善が見られたため、そのレイアウトを正式に採用しました。
「Act」では、更なる最適化のために細部の調整を行い、PDCAサイクルを継続しました。
事例2: 不良品率の低減
別の工場では、不良品率の低減を目指してPDCAサイクルを導入しました。
「Plan」の段階で、過去のデータを基に不良品の発生原因を特定し、改善のための具体的な計画を立てました。
「Do」では、特定の製造工程の見直しや、品質検査の強化などを実行しました。
「Check」での評価では、一時的には改善が見られたものの、完全に目標を達成しませんでした。
そのため、「Act」での改善策として、さらに詳細な原因分析を行い、新たな対策を講じることにしました。
最新の技術動向とPDCAサイクルの融合
デジタルツールの活用
最近では、IoT(Internet of Things)やAI(人工知能)などのデジタルツールを活用したPDCAサイクルの運用が注目されています。
これにより、データの収集や分析が自動化され、より迅速かつ正確な評価が可能になります。
リアルタイムモニタリング
IoTを活用することで、製造ラインの状態をリアルタイムでモニタリングし、即座に問題を検知することができます。
これにより、「Check」や「Act」のステップが迅速に行え、サイクルのスピードも向上します。
まとめ
PDCAサイクルは、製造業における品質改善と業務効率化を図るための強力なツールです。
「Plan」「Do」「Check」「Act」の4つのステップを繰り返すことで、継続的な改善が可能になります。
明確な目標設定やデータの収集・分析、柔軟な対応能力が求められます。
また、最新のデジタル技術を取り入れることで、PDCAサイクルの効果をさらに高めることができます。
製造業の現場でこのサイクルを活用し、競争力を向上させるための一助となれば幸いです。
資料ダウンロード
QCD管理受発注クラウド「newji」は、受発注部門で必要なQCD管理全てを備えた、現場特化型兼クラウド型の今世紀最高の受発注管理システムとなります。
ユーザー登録
受発注業務の効率化だけでなく、システムを導入することで、コスト削減や製品・資材のステータス可視化のほか、属人化していた受発注情報の共有化による内部不正防止や統制にも役立ちます。
NEWJI DX
製造業に特化したデジタルトランスフォーメーション(DX)の実現を目指す請負開発型のコンサルティングサービスです。AI、iPaaS、および先端の技術を駆使して、製造プロセスの効率化、業務効率化、チームワーク強化、コスト削減、品質向上を実現します。このサービスは、製造業の課題を深く理解し、それに対する最適なデジタルソリューションを提供することで、企業が持続的な成長とイノベーションを達成できるようサポートします。
製造業ニュース解説
製造業、主に購買・調達部門にお勤めの方々に向けた情報を配信しております。
新任の方やベテランの方、管理職を対象とした幅広いコンテンツをご用意しております。
お問い合わせ
コストダウンが利益に直結する術だと理解していても、なかなか前に進めることができない状況。そんな時は、newjiのコストダウン自動化機能で大きく利益貢献しよう!
(β版非公開)