- お役立ち記事
- Fundamentals of etching technology and practical procedures in manufacturing
Fundamentals of etching technology and practical procedures in manufacturing
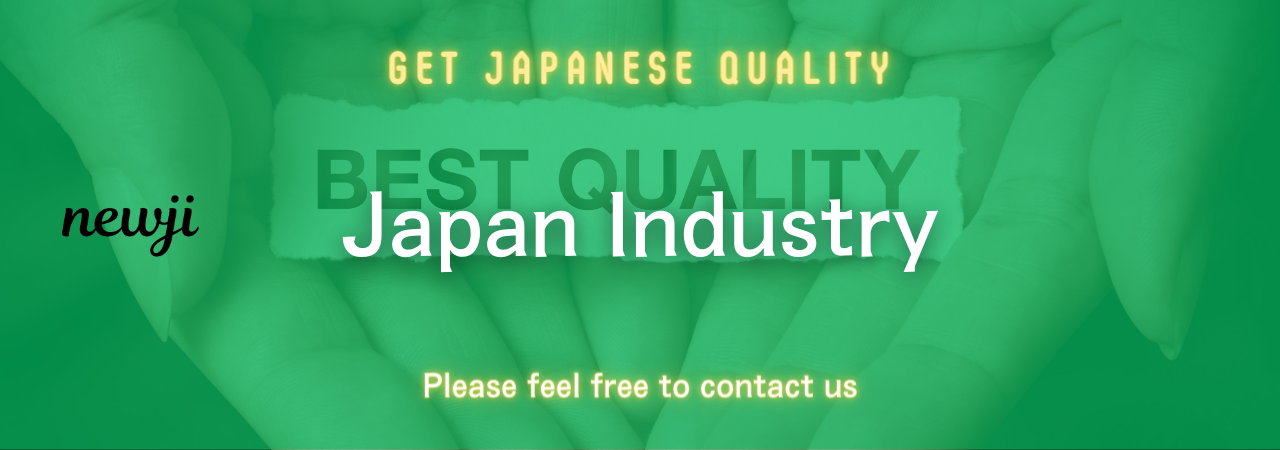
Etching technology is crucial in various manufacturing processes, especially in industries like electronics, semiconductors, and automotive.
By understanding its fundamentals, you can appreciate its application in making intricate designs and components that drive modern technology.
This article will present the basics of etching technology, its techniques, and practical procedures in manufacturing.
目次
What is Etching Technology?
Etching technology involves removing material from a surface to create a specific design or shape.
It is commonly used in manufacturing industries to fabricate fine patterns on metals, silicon wafers, and other substrates.
Etching is essential in developing printed circuit boards (PCBs), microelectromechanical systems (MEMS), and semiconductor devices.
Types of Etching
There are two primary types of etching: wet etching and dry etching.
Wet Etching
Wet etching involves using liquid chemicals to dissolve materials selectively.
This method is typically simple and cost-effective, making it suitable for large-scale production.
Common chemicals used in wet etching include acids and bases.
Process of Wet Etching
1. **Masking:** A protective layer, known as a mask, is applied to the parts of the substrate that should not be etched.
2. **Immersion:** The substrate is immersed in a chemical solution that reacts with the exposed areas.
3. **Rinsing:** After the desired material is etched, the substrate is rinsed to remove any residual chemicals.
4. **Drying:** The substrate is dried to reveal the etched pattern.
While wet etching is relatively simple, it has limitations, such as undercutting, where the chemical spreads horizontally, compromising precision.
Dry Etching
Dry etching, on the other hand, uses gases or plasmas to remove material.
This method provides higher precision and control, making it ideal for applications requiring detailed patterns.
Dry etching is more complex and expensive than wet etching, but it offers better resolution and uniformity.
Process of Dry Etching
1. **Masking:** Similar to wet etching, a mask is applied to protect specific areas.
2. **Ion Bombardment:** In a vacuum chamber, gases are ionized to create plasma.
Positively charged ions accelerate towards the substrate, breaking bonds and removing material.
3. **Chemical Reaction:** Reactive ions interact with the exposed material, creating volatile by-products that are easily removed.
4. **Cleaning:** The etched substrate is cleaned to remove any residues.
Dry etching includes several techniques such as Reactive Ion Etching (RIE), Plasma Etching, and Ion Beam Etching, each offering unique benefits.
Practical Procedures in Manufacturing
Etching technology plays a pivotal role in manufacturing processes.
Understanding practical procedures can ensure efficient and high-quality production.
Step-by-Step Guide to Etching
1. **Designing the Pattern:**
Before etching, a precise design is created using computer-aided design (CAD) software.
This digital blueprint guides the etching process, ensuring the correct pattern and dimensions.
2. **Preparing the Substrate:**
The substrate must be clean and free of contaminants.
This is often achieved through a series of cleaning steps involving solvents and ultrasonic baths.
3. **Applying the Mask:**
The designed pattern is transferred onto the substrate using a mask.
In photolithography, for instance, a light-sensitive photoresist is applied to the substrate and exposed to ultraviolet light through a mask.
The light hardens the exposed areas, while unexposed areas remain soft and are removed.
4. **Etching:**
Depending on the chosen method (wet or dry), the substrate is subjected to the etching process.
For wet etching, it’s immersed in a chemical bath.
In dry etching, it’s placed in a vacuum chamber with ionized gases.
5. **Removing the Mask:**
After etching, the protective mask is removed, revealing the etched pattern.
This step may involve solvents, plasma, or mechanical means.
6. **Inspecting and Testing:**
The final product is carefully inspected for defects and tested for functionality.
High-power microscopes, scanning electron microscopes (SEM), and other analytical tools ensure the product meets specifications.
7. **Finishing:**
Additional steps, such as plating, polishing, or coating, may be applied to finalize the product.
These processes enhance durability, conductivity, or other desired properties.
Applications of Etching Technology
Etching technology is versatile, impacting numerous industries:
Electronics:
In the electronics sector, etching forms complex circuits and components on silicon wafers and PCBs. It allows for miniaturization, leading to the development of compact and efficient electronic devices.
Automotive:
The automotive industry utilizes etching for precision parts and sensors. It ensures the reliable performance of safety systems and electronic controls.
Aerospace:
In aerospace, etching creates lightweight components without sacrificing strength. This is crucial for reducing fuel consumption and improving aircraft performance.
Jewelry and Art:
Etching is also employed in crafting intricate designs on metal, glass, and other materials. Artists and jewelers use etching to create detailed and personalized pieces.
Future Trends in Etching Technology
As technology advances, etching processes are evolving to meet new demands:
Smaller Features:
The continuous push for miniaturization in electronics requires etching techniques that can create even smaller features with high precision.
New Materials:
The development of new materials, such as graphene and other nanomaterials, demands innovative etching processes that can handle their unique properties.
Eco-Friendly Methods:
With increasing environmental concerns, there’s a growing focus on developing eco-friendly etching techniques that minimize waste and reduce hazardous chemicals.
Understanding the fundamentals and practical procedures of etching technology provides insight into its critical role in modern manufacturing.
By leveraging this technology, industries can manufacture highly complex and precise components, driving innovation and technological advancement.
As we move forward, the continued evolution of etching processes promises to unlock new possibilities in various fields, making it a cornerstone of future manufacturing endeavors.
資料ダウンロード
QCD調達購買管理クラウド「newji」は、調達購買部門で必要なQCD管理全てを備えた、現場特化型兼クラウド型の今世紀最高の購買管理システムとなります。
ユーザー登録
調達購買業務の効率化だけでなく、システムを導入することで、コスト削減や製品・資材のステータス可視化のほか、属人化していた購買情報の共有化による内部不正防止や統制にも役立ちます。
NEWJI DX
製造業に特化したデジタルトランスフォーメーション(DX)の実現を目指す請負開発型のコンサルティングサービスです。AI、iPaaS、および先端の技術を駆使して、製造プロセスの効率化、業務効率化、チームワーク強化、コスト削減、品質向上を実現します。このサービスは、製造業の課題を深く理解し、それに対する最適なデジタルソリューションを提供することで、企業が持続的な成長とイノベーションを達成できるようサポートします。
オンライン講座
製造業、主に購買・調達部門にお勤めの方々に向けた情報を配信しております。
新任の方やベテランの方、管理職を対象とした幅広いコンテンツをご用意しております。
お問い合わせ
コストダウンが利益に直結する術だと理解していても、なかなか前に進めることができない状況。そんな時は、newjiのコストダウン自動化機能で大きく利益貢献しよう!
(Β版非公開)