- お役立ち記事
- Causes and Solutions for Short Shots in Manufacturing
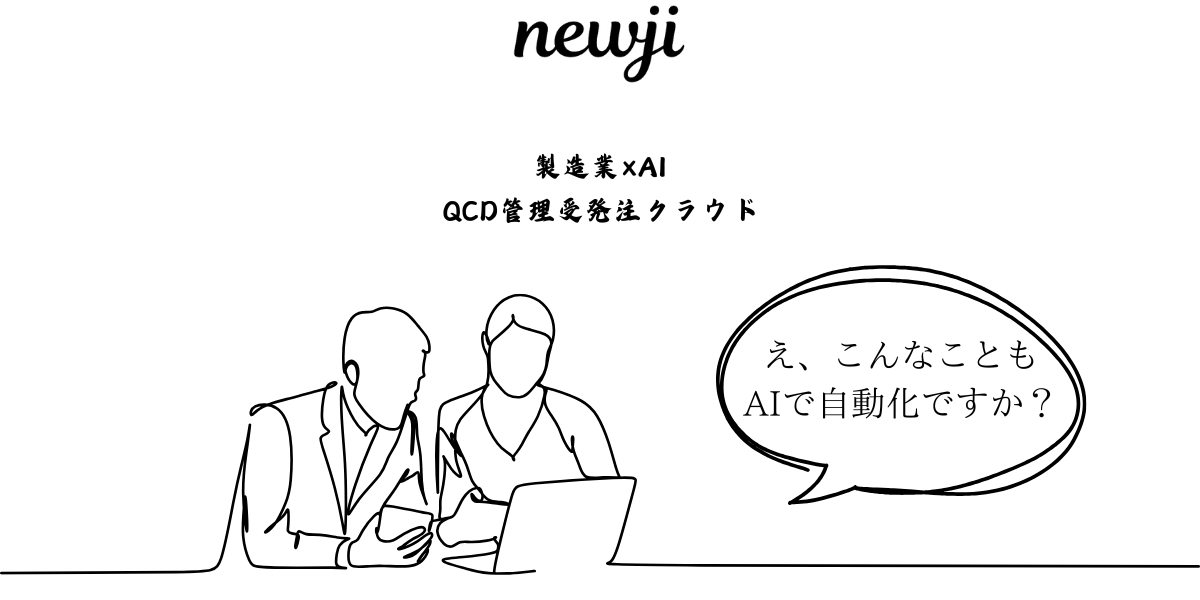
Causes and Solutions for Short Shots in Manufacturing
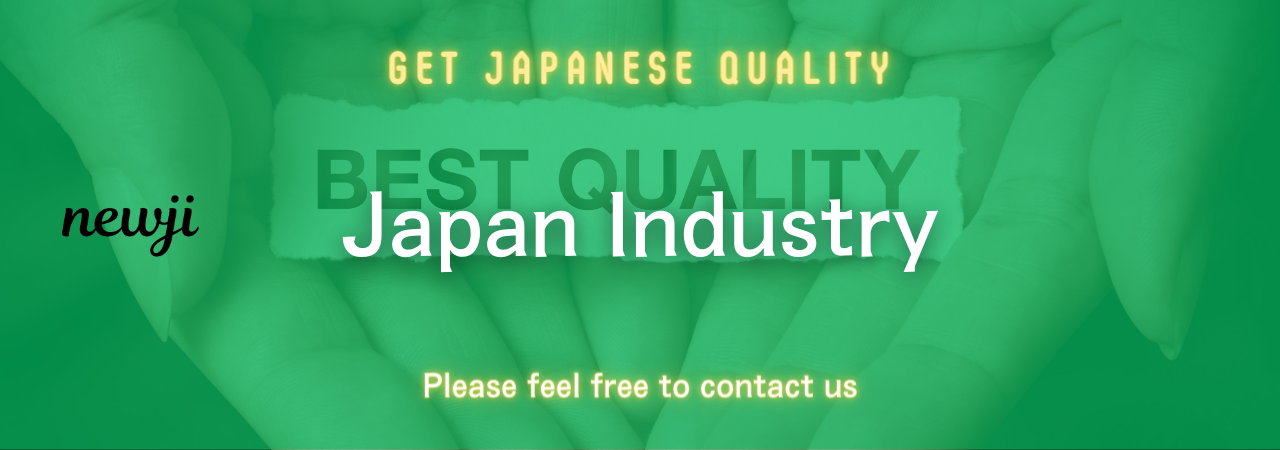
In manufacturing, short shots are a common issue that can affect the final quality of products. Short shots occur when a mold or cavity is not completely filled with material, leading to incomplete or defective products. Understanding the causes and solutions for short shots is crucial for maintaining high production standards. This article delves into the common reasons behind short shots and offers practical solutions to mitigate this problem in manufacturing processes.
目次
Common Causes of Short Shots
Insufficient Material Supply
One of the primary causes of short shots is an insufficient supply of material in the injection mold. When the material supply is too low, it cannot completely fill the mold, resulting in incomplete parts. Various factors can contribute to insufficient material supply, including improper material handling, blockages in the supply system, or incorrect material settings in the machinery.
Improper Mold Design
Mold design plays a significant role in ensuring the effective and complete filling of cavities. If the design is flawed or not well-suited for the type of material being used, it can lead to short shots. Common design issues include inadequate venting, poorly placed gates, or sharp corners that impede material flow.
Machine Settings and Parameters
Inappropriate machine settings can also result in short shots. Factors such as injection pressure, temperature, and injection speed need to be carefully calibrated. If these settings are not optimized, the material may not flow properly into the mold. For example, low injection pressure may not be enough to push the material into intricate areas of the mold.
Flow Restrictions
Flow restrictions within the mold can hinder the material from properly filling the cavity. These restrictions can be due to narrow gates, thin sections within the mold, or even blockages caused by contaminants. When the material flow is restricted, it can lead to gaps and short shots.
Material Properties
Different materials have varying flow characteristics. Some materials might have higher viscosity, making them harder to flow into tight spaces within the mold. If the material selected is inappropriate for the mold design, it could lead to short shots. Additionally, recycled or low-quality materials often come with inconsistencies that affect the flow and filling of the mold.
Solutions to Address Short Shots
Ensuring Adequate Material Supply
Monitoring and ensuring an adequate supply of material is essential to prevent short shots. Regular checks and maintenance of the material supply system can help in identifying and rectifying discrepancies. Implementing automated material filling systems can also enhance consistency and reduce human error.
Optimizing Mold Design
Reviewing and optimizing the mold design can significantly reduce the occurrence of short shots. Working with experienced mold designers who understand the nuances of material behavior can lead to improved mold efficiency. Incorporating adequate venting systems, optimizing gate locations, and smoothening sharp corners can facilitate better material flow.
Adjusting Machine Settings
Fine-tuning machine settings to match the material’s characteristics and mold design is crucial. Conducting thorough trials and setting the optimal injection pressure, temperature, and speed can ensure the material fills the mold adequately. Regular monitoring and adjustment of these settings based on the material batch and production conditions can maintain consistent quality.
Addressing Flow Restrictions
Properly designed molds should minimize flow restrictions, but they can still occur. Regular inspections and maintenance of the mold can help in identifying and clearing any blockages. Implementing flow simulation software during the design phase can also predict potential problem areas and allow for preemptive adjustments.
Choosing the Right Material
Selecting the appropriate material for the mold design is vital. Working with suppliers to understand the material’s flow characteristics and conducting trials can help in making informed decisions. Using high-quality materials and minimizing the use of recycled components can also reduce inconsistencies and improve flow within the mold.
Preventive Measures and Best Practices
Regular Maintenance and Cleaning
Regular maintenance and cleaning of the injection molding machinery and molds can prevent blockages and contamination. Scheduled maintenance checks should include a thorough inspection of the material handling system, mold vents, and gates. Keeping the equipment in top condition ensures smooth operation and reduces the likelihood of short shots.
Training and Skill Development
Investing in the training and skill development of personnel involved in the manufacturing process is crucial. Workers should be educated about the importance of correct machine settings, material handling, and mold maintenance. Skilled operators are more likely to identify and address potential issues before they lead to short shots.
Data Monitoring and Analysis
Implementing data monitoring and analysis systems can provide valuable insights into the manufacturing process. By collecting and analyzing data on machine performance, material flow, and product quality, manufacturers can identify patterns and pinpoint the root causes of short shots. This data-driven approach enables proactive measures to be taken, leading to continuous improvement in the manufacturing process.
Collaborating with Experts
Collaborating with experts, such as mold designers, material scientists, and process engineers, can bring additional expertise to tackle short shots. Engaging with professionals who have extensive experience in the field can help in diagnosing complex issues and implementing advanced solutions.
Implementing Quality Control Measures
Robust quality control measures should be in place to identify and address short shots early in the production process. Visual inspections, automated quality checks, and sample testing can help in detecting incomplete parts before they reach the end of the production line. Early identification allows for prompt corrective actions, reducing waste and ensuring product quality.
Short shots in manufacturing can pose significant challenges, but understanding their causes and implementing effective solutions can mitigate their impact. By focusing on adequate material supply, optimizing mold design, adjusting machine settings, addressing flow restrictions, and selecting the right material, manufacturers can reduce the occurrence of short shots. Additionally, adopting preventive measures and best practices, such as regular maintenance, training, data monitoring, collaboration with experts, and quality control, can enhance overall manufacturing quality and efficiency. By addressing short shots proactively, manufacturers can ensure the production of high-quality products and maintain a competitive edge in the market.
資料ダウンロード
QCD調達購買管理クラウド「newji」は、調達購買部門で必要なQCD管理全てを備えた、現場特化型兼クラウド型の今世紀最高の購買管理システムとなります。
ユーザー登録
調達購買業務の効率化だけでなく、システムを導入することで、コスト削減や製品・資材のステータス可視化のほか、属人化していた購買情報の共有化による内部不正防止や統制にも役立ちます。
NEWJI DX
製造業に特化したデジタルトランスフォーメーション(DX)の実現を目指す請負開発型のコンサルティングサービスです。AI、iPaaS、および先端の技術を駆使して、製造プロセスの効率化、業務効率化、チームワーク強化、コスト削減、品質向上を実現します。このサービスは、製造業の課題を深く理解し、それに対する最適なデジタルソリューションを提供することで、企業が持続的な成長とイノベーションを達成できるようサポートします。
オンライン講座
製造業、主に購買・調達部門にお勤めの方々に向けた情報を配信しております。
新任の方やベテランの方、管理職を対象とした幅広いコンテンツをご用意しております。
お問い合わせ
コストダウンが利益に直結する術だと理解していても、なかなか前に進めることができない状況。そんな時は、newjiのコストダウン自動化機能で大きく利益貢献しよう!
(Β版非公開)