- お役立ち記事
- Introduction and effective use of Value Stream Mapping in the manufacturing industry
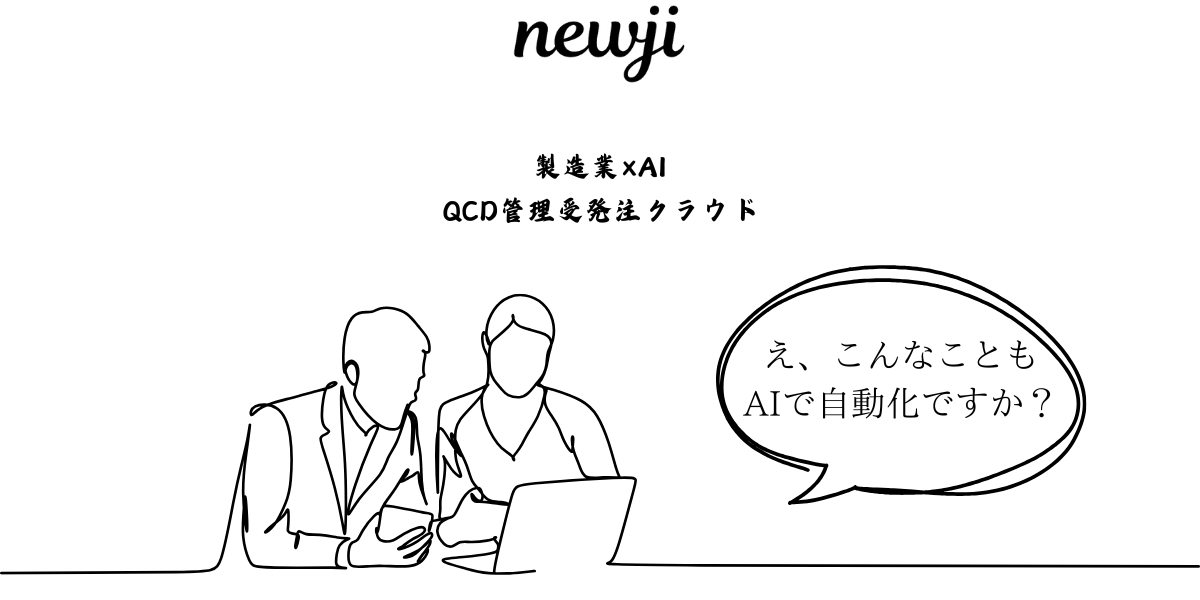
Introduction and effective use of Value Stream Mapping in the manufacturing industry
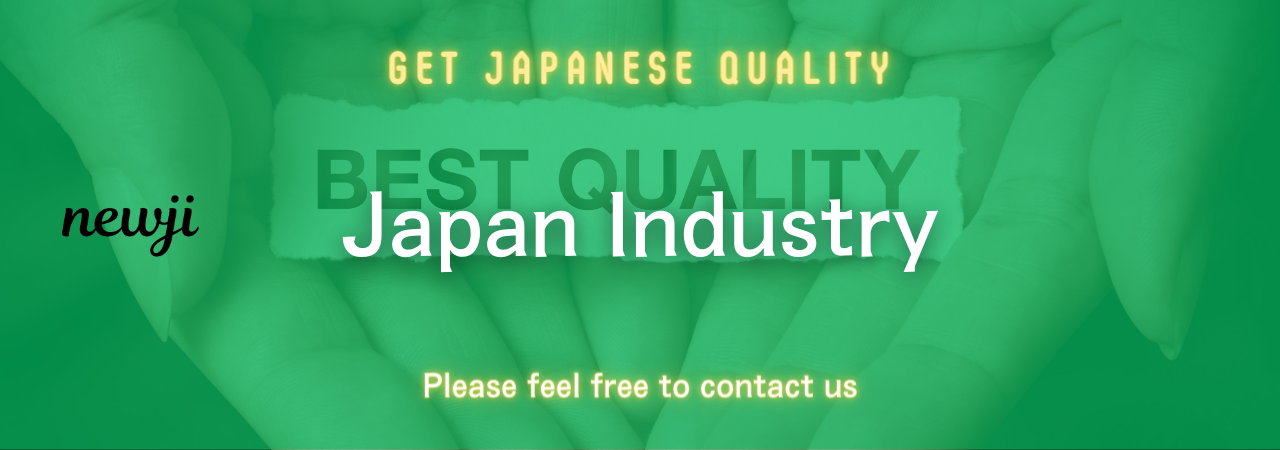
Value Stream Mapping (VSM) is an important tool used in the manufacturing industry to identify waste and improve processes.
It provides a visual representation of the flow of materials and information required to bring a product from start to finish.
This article will introduce Value Stream Mapping, its key components, and how it can be effectively used in the manufacturing industry.
目次
What is Value Stream Mapping?
Value Stream Mapping (VSM) is a lean-management method used to analyze and design the flow of materials and information.
VSM helps identify bottlenecks, reduce waste, and improve efficiency.
Manufacturers can see the steps involved in creating a product and understand how each part of the process interrelates.
In essence, VSM provides a bird’s-eye view of the production system.
This broad perspective is invaluable for making informed decisions and improvements in the manufacturing process.
Components of Value Stream Mapping
Current State Map
The Current State Map represents the existing production process.
It highlights each step from the arrival of raw materials to the completion of the final product.
This map is crucial for identifying areas of waste and inefficiency.
It allows manufacturers to see where time, labor, and resources are being unnecessarily spent.
Future State Map
The Future State Map represents the desired production process after improvements have been made.
This map serves as a goal for the organization to work towards.
It helps visualize the potential benefits of changes and streamlines efforts to achieve these improvements.
Process Box
A Process Box is used to detail each step in the production process.
Each box contains essential information such as cycle time, changeover time, and the number of operators involved.
Understanding these details allows managers to pinpoint where improvements can be made.
Information Flow
Information Flow represents the communication channels within the production process.
This includes instructions, feedback, and other exchanges critical for the flow of materials.
Efficient information flow is key to a smooth production process and helps in minimizing delays and errors.
Material Flow
Material Flow illustrates the movement of raw materials and components through the production process.
This element helps in identifying unnecessary transportation, waiting times, and inventory levels.
A streamlined material flow contributes to reduced costs and helps in delivering products more quickly to customers.
Steps to Create a Value Stream Map
Step 1: Select a Product or Process Family
The first step in creating a Value Stream Map is selecting a product or process family.
This selection should be based on strategic priorities and areas with the most potential for improvement.
By focusing on key products or processes, organizations can achieve more significant benefits.
Step 2: Map the Current State
Next, gather data and map out the Current State of the production process.
This involves documenting each step, measuring cycle times, and recording any delays or bottlenecks.
The Current State Map provides a clear picture of where inefficiencies exist.
Step 3: Identify Waste
Analyze the Current State Map to identify areas of waste.
Common types of waste include overproduction, waiting, unnecessary transportation, excess inventory, and defects.
Clearly highlighting these wastes allows for targeted improvement efforts.
Step 4: Design the Future State
With the waste areas identified, design the Future State Map.
This step involves rethinking the production process to eliminate waste and enhance efficiency.
Consider techniques such as Just-In-Time production, reducing batch sizes, and improving information flow.
Step 5: Create an Implementation Plan
An implementation plan outlines the steps needed to move from the Current State to the Future State.
This plan should include specific actions, timelines, and responsible parties.
Clear communication and regular tracking are important to ensure successful implementation.
Benefits of Value Stream Mapping in Manufacturing
Enhanced Efficiency
VSM helps in identifying and eliminating waste, resulting in a more streamlined production process.
Efficient processes lead to cost savings, faster production times, and higher overall productivity.
Improved Quality
By streamlining processes and reducing waste, VSM can improve the quality of the final product.
Fewer defects mean greater customer satisfaction and potential for repeat business.
Better Inventory Management
A well-designed value stream map shows where inventory levels can be optimized.
By managing inventory more effectively, manufacturers can reduce storage costs and minimize the risk of overstocking or stockouts.
Greater Employee Involvement
VSM encourages a collaborative approach where employees at all levels are involved in identifying and solving problems.
This involvement leads to a more engaged workforce and fosters a culture of continuous improvement.
Enhanced Customer Value
By focusing on reducing waste and improving process efficiencies, VSM enables manufacturers to deliver greater value to their customers.
This can include faster delivery times, better product quality, and lower costs.
Conclusion
Value Stream Mapping is a powerful tool in the manufacturing industry to systematically identify and eliminate waste.
By understanding the flow of materials and information, manufacturers can optimize processes, improve efficiency, and deliver higher quality products to customers.
The implementation of VSM fosters a culture of continuous improvement, engaging employees, and ensuring that the company remains competitive in the ever-evolving market.
Integrating VSM into your manufacturing processes is a strategic step towards achieving operational excellence.
資料ダウンロード
QCD調達購買管理クラウド「newji」は、調達購買部門で必要なQCD管理全てを備えた、現場特化型兼クラウド型の今世紀最高の購買管理システムとなります。
ユーザー登録
調達購買業務の効率化だけでなく、システムを導入することで、コスト削減や製品・資材のステータス可視化のほか、属人化していた購買情報の共有化による内部不正防止や統制にも役立ちます。
NEWJI DX
製造業に特化したデジタルトランスフォーメーション(DX)の実現を目指す請負開発型のコンサルティングサービスです。AI、iPaaS、および先端の技術を駆使して、製造プロセスの効率化、業務効率化、チームワーク強化、コスト削減、品質向上を実現します。このサービスは、製造業の課題を深く理解し、それに対する最適なデジタルソリューションを提供することで、企業が持続的な成長とイノベーションを達成できるようサポートします。
オンライン講座
製造業、主に購買・調達部門にお勤めの方々に向けた情報を配信しております。
新任の方やベテランの方、管理職を対象とした幅広いコンテンツをご用意しております。
お問い合わせ
コストダウンが利益に直結する術だと理解していても、なかなか前に進めることができない状況。そんな時は、newjiのコストダウン自動化機能で大きく利益貢献しよう!
(Β版非公開)