- お役立ち記事
- Improving Purchasing Efficiency in Manufacturing with PO Management
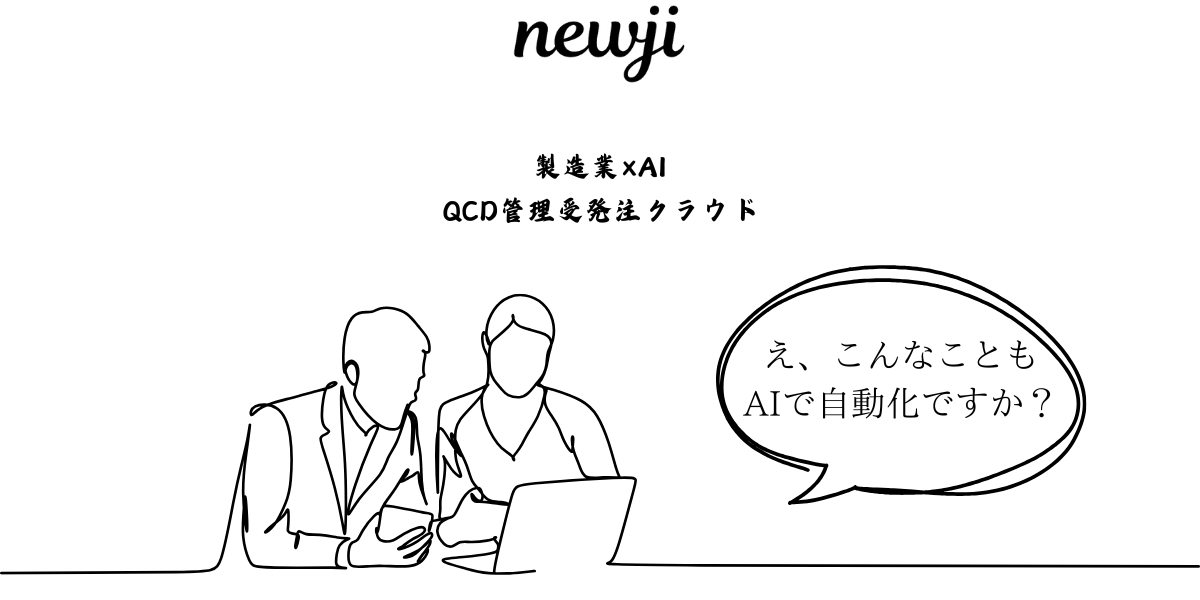
Improving Purchasing Efficiency in Manufacturing with PO Management
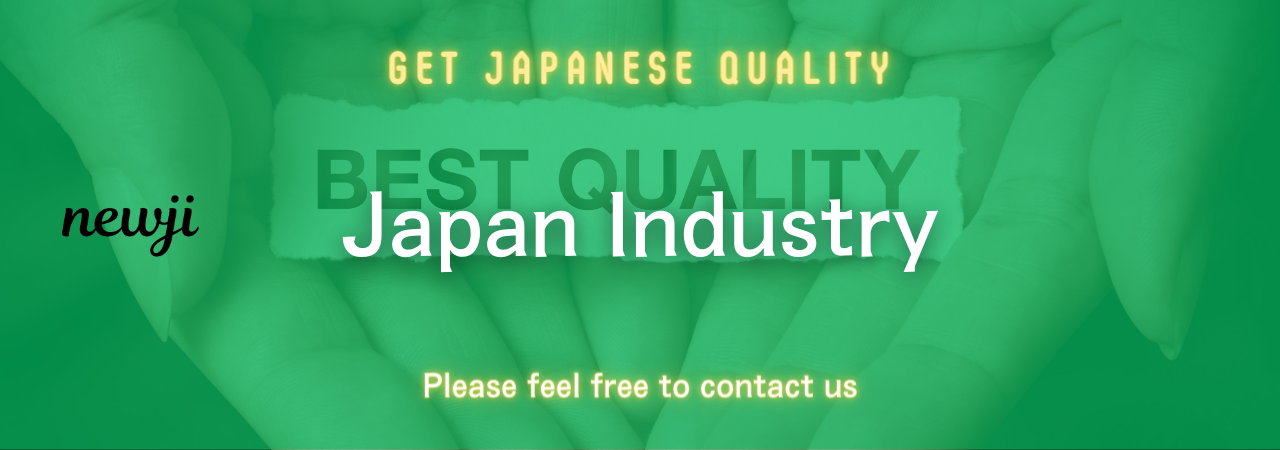
In today’s fast-paced manufacturing world, efficiency is key.
Improving how purchases are managed can significantly boost productivity.
Purchase order (PO) management is a critical component in achieving this efficiency.
目次
What is PO Management?
PO management stands for Purchase Order management.
It involves overseeing the entire process of purchasing goods and services needed in manufacturing.
This includes everything from issuing purchase orders to tracking deliveries and managing payments.
PO management helps ensure that the right materials are acquired at the right time and price.
Why is PO Management Important?
For any manufacturing business, raw materials and components are essential.
Without them, production can come to a halt.
PO management helps streamline the procurement process, ensuring that there are no interruptions in supply.
Proper PO management can lead to cost savings.
By keeping an eye on every purchase and vendor, manufacturers can negotiate better deals and avoid unnecessary expenditures.
It also helps in maintaining good vendor relationships by ensuring timely payments.
Satisfied vendors are more likely to offer favorable terms and quick responses.
Steps Involved in PO Management
Step 1: Identifying Requirements
The first step in PO management involves recognizing what needs to be purchased.
This entails understanding the materials required for production and forecasting demand.
Accurate requirement identification minimizes wastage and ensures only necessary items are ordered.
Step 2: Selecting Vendors
Choosing the right vendors is crucial.
Factors such as cost, quality, reliability, and delivery times need to be considered.
It’s usually beneficial to establish relationships with multiple vendors to create a competitive environment and avoid dependency on a single source.
Step 3: Creating Purchase Orders
Once the vendors are selected, the next step is to create purchase orders.
These documents formally request goods or services from the supplier.
They include details like quantity, specifications, delivery dates, and payment terms.
Detailed POs help prevent misunderstandings between manufacturers and vendors.
Step 4: Tracking and Monitoring Orders
After issuing POs, it’s vital to monitor the order status.
Tracking systems can be employed to provide real-time updates on order progress.
This helps in quickly identifying and resolving any issues that may arise, such as delivery delays or discrepancies in the order.
Step 5: Receiving and Inspecting Goods
Upon arrival, the received goods need to be inspected to ensure they meet the required standards.
This step safeguards against defective materials entering the production process.
Any inconsistencies should be promptly reported to the vendor for resolution.
Step 6: Making Payments
Once goods are received and verified, the next step is to process payments according to the agreed terms.
Timely payments maintain good relationships with vendors and can sometimes lead to favorable payment terms in the future.
Benefits of Effective PO Management
Effective PO management offers numerous benefits to manufacturing businesses:
Cost Savings
By monitoring every purchase and maintaining competition among vendors, manufacturers can obtain better prices and terms.
Bulk purchasing and long-term contracts can also lead to discounts.
Reduced Risk of Stockouts
Properly managed purchase orders help ensure a steady flow of materials.
This reduces the risk of running out of critical supplies, which can halt production and impact customer satisfaction.
Improved Vendor Relationships
Timely and accurate orders strengthen the relationship with vendors.
Reliable suppliers are more likely to provide quality materials and flexible terms.
Long-term partnerships can develop based on mutual trust and benefit.
Enhanced Operational Efficiency
Streamlining the purchasing process reduces administrative workload and operational bottlenecks.
Automated systems can further enhance efficiency, allowing employees to focus on core tasks.
Implementing PO Management Systems
Automation
Many manufacturing firms adopt automated PO management systems to streamline processes.
These systems can handle everything from order creation to tracking and payment processing.
Automation minimizes human error, speeds up processes, and provides real-time data for better decision-making.
Integration with ERP Systems
PO management systems can be integrated with Enterprise Resource Planning (ERP) systems.
ERP systems manage and integrate core business processes.
Integration ensures seamless data transfer and consistency across various departments like finance, supply chain, and production.
Data Analytics
Utilizing data analytics in PO management can provide valuable insights.
Analyzing purchase data helps in identifying trends and improving forecasting accuracy.
Predictive analytics can anticipate shortages and suggest optimal ordering times.
Challenges in PO Management
Despite its advantages, PO management isn’t without challenges:
Human Error
Manual processes are prone to errors.
Incorrect data entry or misplaced documents can cause significant disruptions.
Automation helps but implementing it correctly demands planning and investment.
Vendor Mismanagement
Improperly managed vendor relationships can lead to delays, subpar materials, and strained relations.
Regular communication and feedback help mitigate these issues.
Cost Overruns
Without diligent tracking, costs can quickly escalate due to over-ordering or overpriced purchases.
Regular audits and stringent approval processes are essential to control expenses.
Best Practices for PO Management
To optimize your PO management, consider these best practices:
Standardize Procedures
Develop standardized processes for creating and managing POs.
Clear guidelines ensure consistency and reduce errors.
Use Technology
Invest in PO management software.
Even basic tools can greatly improve efficiency and accuracy.
Maintain Clear Communication
Keep lines of communication open with all stakeholders.
Regular updates ensure everyone is on the same page and can react quickly to any issues.
Conduct Regular Audits
Perform regular audits of purchase orders and vendor contracts.
This helps identify discrepancies and areas for improvement.
In conclusion, improving purchasing efficiency in manufacturing with effective PO management is not just about cost savings but also about enhancing overall operational efficiency.
By adopting best practices and leveraging advanced technologies, manufacturers can ensure a steady supply of quality materials, maintain positive vendor relationships, and drive their business towards greater success.
資料ダウンロード
QCD調達購買管理クラウド「newji」は、調達購買部門で必要なQCD管理全てを備えた、現場特化型兼クラウド型の今世紀最高の購買管理システムとなります。
ユーザー登録
調達購買業務の効率化だけでなく、システムを導入することで、コスト削減や製品・資材のステータス可視化のほか、属人化していた購買情報の共有化による内部不正防止や統制にも役立ちます。
NEWJI DX
製造業に特化したデジタルトランスフォーメーション(DX)の実現を目指す請負開発型のコンサルティングサービスです。AI、iPaaS、および先端の技術を駆使して、製造プロセスの効率化、業務効率化、チームワーク強化、コスト削減、品質向上を実現します。このサービスは、製造業の課題を深く理解し、それに対する最適なデジタルソリューションを提供することで、企業が持続的な成長とイノベーションを達成できるようサポートします。
オンライン講座
製造業、主に購買・調達部門にお勤めの方々に向けた情報を配信しております。
新任の方やベテランの方、管理職を対象とした幅広いコンテンツをご用意しております。
お問い合わせ
コストダウンが利益に直結する術だと理解していても、なかなか前に進めることができない状況。そんな時は、newjiのコストダウン自動化機能で大きく利益貢献しよう!
(Β版非公開)