- お役立ち記事
- Optimizing Manufacturing Processes with Inline Inspection Devices
Optimizing Manufacturing Processes with Inline Inspection Devices
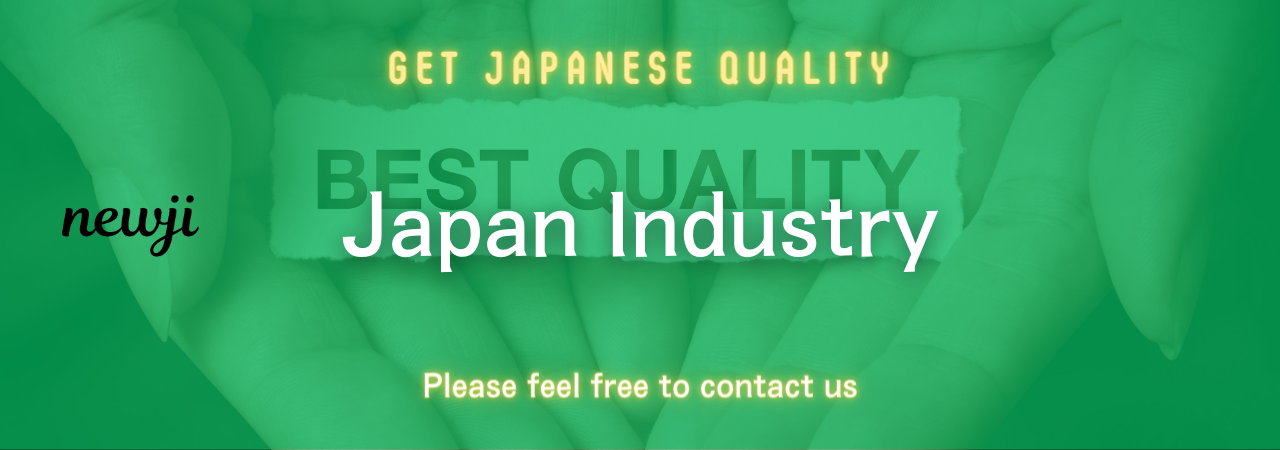
Inline inspection devices have revolutionized the manufacturing industry, enhancing quality control and efficiency.
These smart devices are integrated into the production line, providing real-time data and insights.
By optimizing manufacturing processes with these tools, businesses can reduce costs, increase productivity, and improve product quality.
Let’s delve deeper into how these devices prove invaluable in manufacturing.
目次
Understanding Inline Inspection Devices
Inline inspection devices are machines or tools installed directly within a production line to monitor and inspect products in real-time.
They detect defects, measure dimensions, and ensure that products meet required specifications before they proceed further in the production process.
This continuous monitoring helps in maintaining high-quality standards and minimizing waste.
Types of Inline Inspection Devices
There are several types of inline inspection devices, each serving a specific purpose in the production line:
1. **Vision Systems**: These use cameras and imaging software to detect visual defects such as scratches, dents, or missing parts.
2. **Laser Measurement Systems**: These systems employ lasers to measure dimensions with high precision, ensuring components are within the required tolerances.
3. **X-ray Inspection Systems**: These devices inspect the internal structure of products, identifying issues like voids, cracks, or misalignments.
4. **Ultrasonic Testing**: This technology uses sound waves to detect internal flaws in materials, such as cracks or inclusions.
Each of these systems contributes uniquely to maintaining product quality and consistency.
Benefits of Using Inline Inspection Devices
Implementing inline inspection devices offers numerous benefits, which include:
Real-time Quality Control
One of the most significant advantages is real-time quality control.
As products are inspected immediately after or during production, any defects can be detected and addressed instantly.
This reduces the risk of defective products reaching customers and improves overall product quality.
Increased Efficiency
With inline inspection, there’s no need to stop the production line for separate quality checks.
This leads to a smoother and faster production process.
Efficient operations translate to higher throughput and lower production costs.
Reduced Waste
Early detection of defects helps in reducing waste.
By catching flaws early in the process, manufacturers can prevent a defective product from progressing further down the line, where it might incur additional costs and resources.
This not only saves money but also promotes sustainable practices.
Data-Driven Decisions
Inline inspection devices collect vast amounts of data during the production process.
Manufacturers can analyze this data to identify trends, make informed decisions, and continuously improve processes.
Data-driven insights help in predicting potential issues and making proactive adjustments.
How to Integrate Inline Inspection Devices
Implementing these devices requires careful planning and consideration:
Assessing Production Needs
First, evaluate the specific needs of your production line.
Identify the critical points in the process where inspections are most needed.
Understanding these requirements will help you choose the right type of inline inspection devices.
Choosing the Right Technology
Select the technology that best fits your production needs.
For instance, if you need high-precision measurements, laser systems might be ideal.
For internal defect detection, X-ray or ultrasonic systems would be more suitable.
Integrating with Existing Systems
Ensure that the chosen devices can seamlessly integrate with your existing production line.
Compatibility with current machinery and software is crucial for smooth operations.
Consider working with a professional to install and configure the devices correctly.
Training Staff
Train your staff to operate and maintain the new inspection devices.
Proper training ensures that your team can effectively use the technology, minimizing downtime and maximizing efficiency.
Case Studies: Success with Inline Inspection Devices
Several manufacturers have successfully integrated inline inspection devices, yielding impressive results.
Automotive Industry
In the automotive sector, inline inspection devices are used to monitor the assembly of various components, from engines to chassis.
One notable case is a car manufacturer that implemented vision systems to inspect welds in real-time.
This led to a significant reduction in defective welds and improved overall vehicle quality.
Electronics Manufacturing
Electronics manufacturers use X-ray inspection systems to inspect solder joints on circuit boards.
A major electronics company reported a 30% reduction in defects and an increase in production speed after integrating these devices.
Pharmaceutical Industry
In the pharmaceutical industry, inline inspection ensures that each pill or tablet meets stringent quality standards.
A pharmaceutical company using laser measurement systems saw a marked improvement in product consistency and compliance with regulatory standards.
Future Trends in Inline Inspection
The future of inline inspection devices looks promising, with several trends shaping the industry:
Artificial Intelligence and Machine Learning
AI and machine learning are anticipated to play a significant role in enhancing inline inspection systems.
These technologies can improve defect detection accuracy, predict maintenance needs, and optimize inspection processes.
IoT Integration
The Internet of Things (IoT) will enable better connectivity between inspection devices and other machinery in the production line.
This interconnectedness will facilitate real-time data sharing and more efficient process management.
Advanced Imaging Technologies
The development of more advanced imaging technologies, including hyperspectral imaging, will enhance the capabilities of vision systems.
These technologies will provide more detailed and accurate inspections, further improving quality control.
In conclusion, inline inspection devices are invaluable tools for optimizing manufacturing processes.
They enhance quality control, increase efficiency, reduce waste, and provide valuable data for continuous improvement.
By integrating these devices, manufacturers can stay ahead in a competitive market, delivering high-quality products to their customers.
資料ダウンロード
QCD調達購買管理クラウド「newji」は、調達購買部門で必要なQCD管理全てを備えた、現場特化型兼クラウド型の今世紀最高の購買管理システムとなります。
ユーザー登録
調達購買業務の効率化だけでなく、システムを導入することで、コスト削減や製品・資材のステータス可視化のほか、属人化していた購買情報の共有化による内部不正防止や統制にも役立ちます。
NEWJI DX
製造業に特化したデジタルトランスフォーメーション(DX)の実現を目指す請負開発型のコンサルティングサービスです。AI、iPaaS、および先端の技術を駆使して、製造プロセスの効率化、業務効率化、チームワーク強化、コスト削減、品質向上を実現します。このサービスは、製造業の課題を深く理解し、それに対する最適なデジタルソリューションを提供することで、企業が持続的な成長とイノベーションを達成できるようサポートします。
オンライン講座
製造業、主に購買・調達部門にお勤めの方々に向けた情報を配信しております。
新任の方やベテランの方、管理職を対象とした幅広いコンテンツをご用意しております。
お問い合わせ
コストダウンが利益に直結する術だと理解していても、なかなか前に進めることができない状況。そんな時は、newjiのコストダウン自動化機能で大きく利益貢献しよう!
(Β版非公開)