- お役立ち記事
- Optimizing Inventory Management in Manufacturing with PFEP Implementation
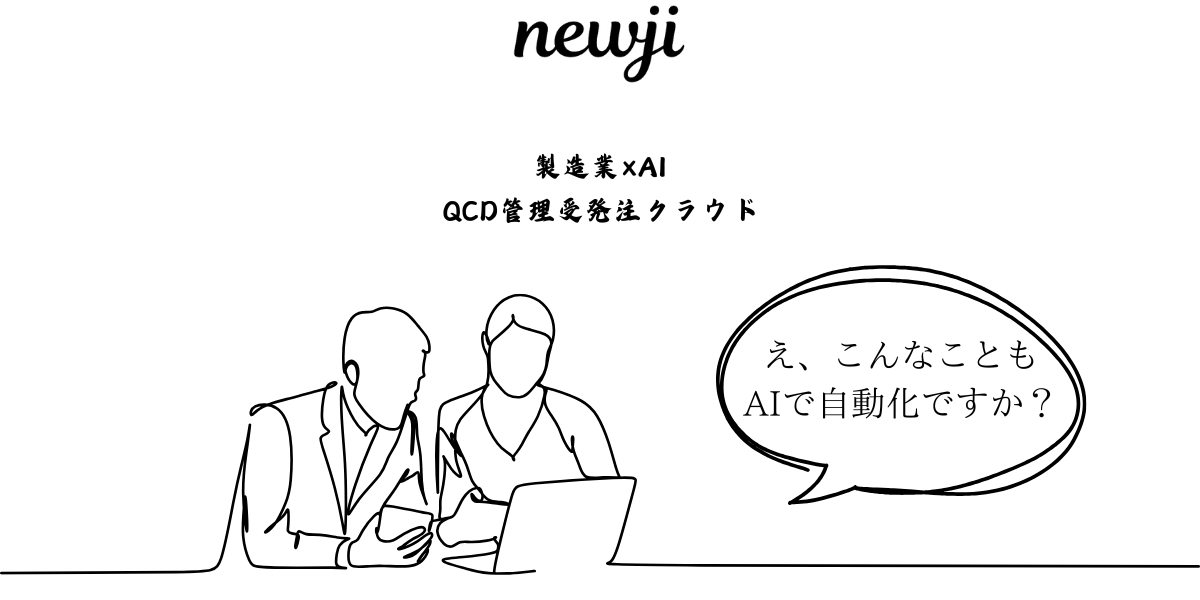
Optimizing Inventory Management in Manufacturing with PFEP Implementation
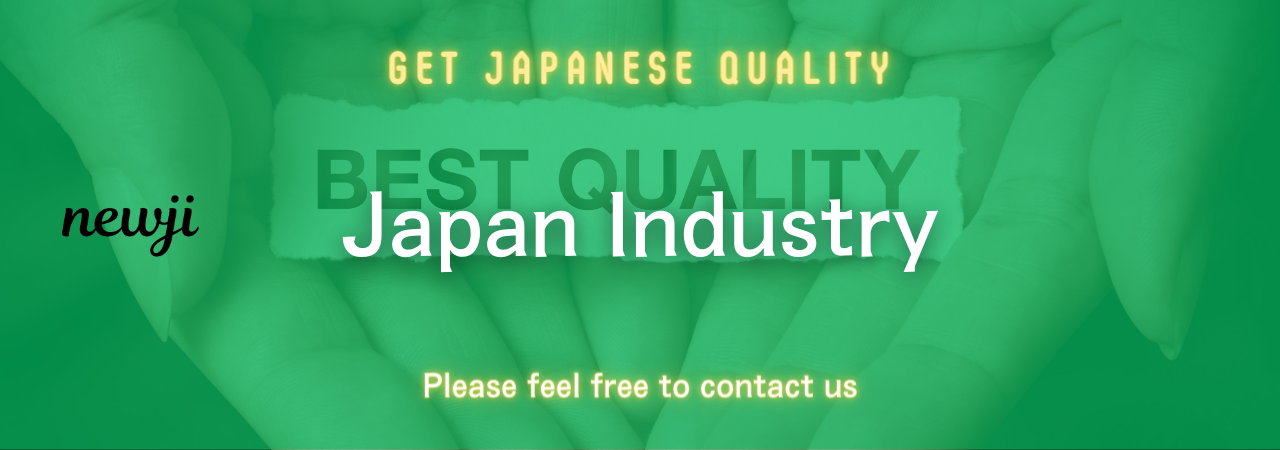
目次
Introduction to PFEP
In the world of manufacturing, managing inventory is one of the most critical tasks.
It can be quite challenging to ensure that the right materials and components are available when needed.
A strategy to tackle this problem is through the implementation of PFEP, which stands for Plan for Every Part.
PFEP is a structured approach to managing inventory better.
It details how each part used in the manufacturing process should be handled, from procurement to delivery.
With a comprehensive PFEP plan in place, manufacturers can streamline their processes, reduce costs, and improve efficiency.
Understanding the Basics of PFEP
PFEP stands for Plan for Every Part.
This means creating a detailed plan for each component used in the manufacturing process.
The main idea behind PFEP is to track and manage each part individually instead of treating them as a bulk lot.
A PFEP plan typically includes details such as:
- Part number and description
- Supplier information
- Packaging specifications
- Storage locations
- Minimum and maximum inventory levels
- Reorder triggers
By having this information readily available, manufacturers can make better decisions about ordering, storing, and using materials.
Benefits of Implementing PFEP
Implementing PFEP in inventory management brings several significant benefits.
Firstly, it helps in reducing stockouts and overstock situations.
When each part has a specific plan, it’s easier to track its availability and need.
Secondly, PFEP improves overall efficiency in the production process.
With well-defined handling instructions, workers can process materials faster and more accurately.
This leads to reduced downtime and fewer production delays.
Thirdly, PFEP can lead to cost savings.
Better-managed inventory often means less money tied up in excess stock and less waste.
Additionally, improved processes can also reduce the need for expensive expedited shipping.
Steps to Implement PFEP in Inventory Management
Implementing PFEP requires a systematic approach.
Here are the essential steps to get started:
Identify All Parts Used in Production
The first step is to identify and list every part used in the production process.
This includes raw materials, components, and any other items necessary for manufacturing.
Be thorough and ensure no part is overlooked.
Once you have a complete list, assign a unique part number and description to each item.
This will help in tracking and managing the parts more efficiently.
Gather Necessary Information
For each part, gather detailed information such as supplier details, packaging specifications, storage locations, and reorder triggers.
This information will form the basis of your PFEP plan.
Ensure that the data collected is accurate and up-to-date.
Create a PFEP Database
Compile all the gathered information into a centralized database.
This could be a simple spreadsheet or a more sophisticated inventory management system.
The key is to have all the data in one place and easily accessible.
Define Inventory Levels
Set minimum and maximum inventory levels for each part.
The minimum level is the point where new stock should be ordered to prevent stockouts.
The maximum level is the upper limit to avoid overstocking and excess inventory.
These levels should be determined based on factors like lead times, usage rates, and storage capacity.
Develop Handling and Storage Procedures
Detail the specific procedures for handling and storing each part.
This includes how parts should be received, inspected, stored, and issued to the production floor.
Clear guidelines will ensure that everyone involved in the process follows the same standards.
Train Employees
Training is crucial for the successful implementation of PFEP.
Ensure that all employees who handle inventory are well-versed in the new procedures.
Conduct training sessions and provide reference materials that employees can use as guides.
Regular Reviews and Updates
Inventory management is a dynamic process, and the PFEP plan should be regularly reviewed and updated.
Conduct periodic audits to ensure the plan is being followed accurately.
Make adjustments as necessary to accommodate changes in production requirements or supplier terms.
Challenges in Implementing PFEP
While PFEP brings numerous benefits, its implementation can also present some challenges.
One common challenge is resistance to change.
Employees who are used to the existing methods might be hesitant to adopt new procedures.
It’s important to communicate the benefits clearly and provide adequate training and support.
Another challenge is the initial time and effort required to collect data and set up the PFEP plan.
However, the long-term benefits far outweigh the initial investment.
Automating the data collection process using inventory management software can also ease the burden.
Case Study: Successful PFEP Implementation
To better understand the impact of PFEP, let’s look at a real-world case study.
A mid-sized manufacturing company faced significant inventory management issues, leading to frequent stockouts and production delays.
The company decided to implement a PFEP plan.
They identified all parts used in their production, gathered detailed information, and established minimum and maximum inventory levels.
They also trained their employees on the new procedures and conducted regular reviews.
Within a few months, the company saw a noticeable improvement.
Stockouts were reduced by 60%, production efficiency increased, and overall inventory costs decreased by 25%.
The success of PFEP implementation significantly contributed to the company’s growth and competitiveness.
Conclusion
Implementing PFEP in inventory management can transform the efficiency and effectiveness of manufacturing operations.
By planning for every part, companies can reduce costs, improve production processes, and ensure timely availability of materials.
Although the initial implementation may require effort, the long-term benefits make it a worthwhile investment.
With a well-structured PFEP plan, manufacturers can achieve better control over their inventory and drive significant improvements in their operations.
資料ダウンロード
QCD調達購買管理クラウド「newji」は、調達購買部門で必要なQCD管理全てを備えた、現場特化型兼クラウド型の今世紀最高の購買管理システムとなります。
ユーザー登録
調達購買業務の効率化だけでなく、システムを導入することで、コスト削減や製品・資材のステータス可視化のほか、属人化していた購買情報の共有化による内部不正防止や統制にも役立ちます。
NEWJI DX
製造業に特化したデジタルトランスフォーメーション(DX)の実現を目指す請負開発型のコンサルティングサービスです。AI、iPaaS、および先端の技術を駆使して、製造プロセスの効率化、業務効率化、チームワーク強化、コスト削減、品質向上を実現します。このサービスは、製造業の課題を深く理解し、それに対する最適なデジタルソリューションを提供することで、企業が持続的な成長とイノベーションを達成できるようサポートします。
オンライン講座
製造業、主に購買・調達部門にお勤めの方々に向けた情報を配信しております。
新任の方やベテランの方、管理職を対象とした幅広いコンテンツをご用意しております。
お問い合わせ
コストダウンが利益に直結する術だと理解していても、なかなか前に進めることができない状況。そんな時は、newjiのコストダウン自動化機能で大きく利益貢献しよう!
(Β版非公開)