- お役立ち記事
- Enhancing Manufacturing Communication Networks with CAN Bus Implementation
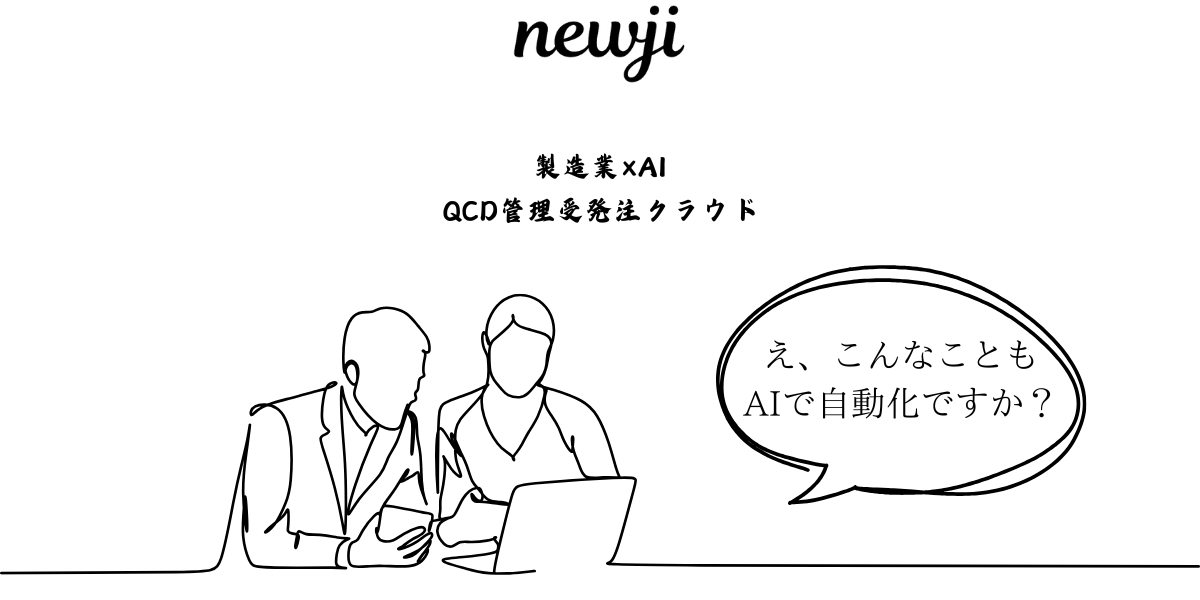
Enhancing Manufacturing Communication Networks with CAN Bus Implementation
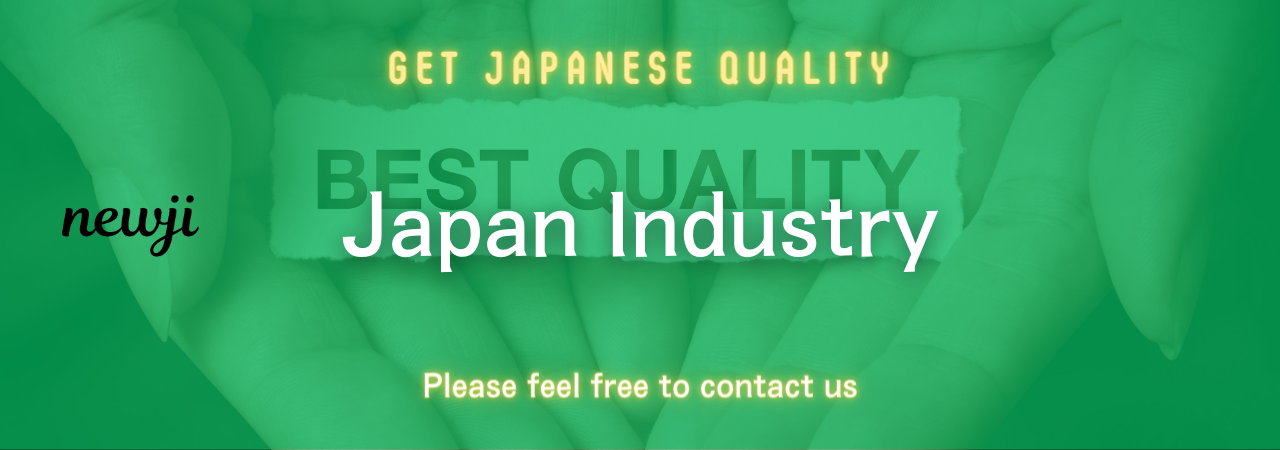
In the ever-evolving world of manufacturing, efficient communication networks are critical for ensuring streamlined operations and minimizing disruptions.
One technology that has come to the forefront in enhancing these communication networks is the Controller Area Network (CAN) bus.
Originally developed for the automotive industry, the CAN bus now finds applications in various sectors, including manufacturing, due to its robustness and reliability.
目次
Understanding CAN Bus Technology
The CAN bus is a high-integrity serial data communication system that operates at high speed.
It was designed to allow microcontrollers and devices to communicate with each other without the need for a host computer.
Each node on the network can send and receive messages, making it a peer-to-peer network.
This setup significantly reduces the wiring needed, compared to traditional methods, which rely on point-to-point wiring.
Advantages of CAN Bus
CAN bus technology offers several advantages over other communication systems.
Firstly, its error detection and handling capabilities are robust, ensuring data integrity.
In a manufacturing setting, where precision and reliability are paramount, these features are invaluable.
Secondly, the simplicity and reliability of the wiring make installation and maintenance both cost-effective and efficient.
Lastly, the CAN bus supports multi-master capabilities, which means that if one node fails, the others can continue to operate, ensuring minimal disruption to the manufacturing process.
Implementing CAN Bus in Manufacturing
Implementing CAN bus technology within a manufacturing environment involves several steps.
Understanding these steps can help your facility transition smoothly and start reaping the benefits of an enhanced communication network.
Assessing System Requirements
Before implementation, it’s essential to assess your current system’s requirements.
Identify the types of devices that need to communicate and the data they will exchange.
This step ensures that you choose the right CAN bus system that fits your needs efficiently.
Designing the Network
Once you understand the requirements, the next step is to design the network.
Consider the layout of your manufacturing plant and the placement of different devices.
Ensure that the CAN bus system covers all the required areas.
This may involve designing the network in a manner that ensures redundancy and minimizes latency, thus leading to more efficient operations.
Benefits of CAN Bus in Manufacturing
The implementation of CAN bus technology in a manufacturing environment brings many benefits.
These advantages revolve around improved communication, enhanced productivity, and reduced operational costs.
Improved Communication
One of the most significant benefits is the improvement in communication between devices.
With CAN bus, devices can share information quickly and efficiently, leading to better-coordinated operations.
For example, in an assembly line, each machine can notify the next in line about the status of its task, ensuring a smooth flow of operations.
Enhanced Productivity
Better communication results in enhanced productivity.
With CAN bus reducing errors and ensuring reliable data transfer, machines operate more efficiently.
This efficiency decreases downtime caused by communication failures and increases the overall output of the manufacturing process.
Reduced Operational Costs
The cost savings from implementing CAN bus technology can be substantial.
The reduction in wiring alone can save significant amounts of money.
Furthermore, the increased reliability decreases maintenance costs and the need for frequent troubleshooting.
The overall result is a more cost-effective manufacturing operation.
Case Study: CAN Bus Implementation Success
Consider a manufacturing plant that produces electronic components.
They faced issues with their traditional communication system, including frequent downtime and high maintenance costs.
By switching to CAN bus technology, they experienced a transformation.
Initial Challenges
Before the implementation, the plant’s production was frequently interrupted by communication failures.
The traditional wiring system was not only cost-intensive but also prone to errors.
Maintenance required significant manual intervention, leading to higher labor costs and production delays.
Implementation Process
The plant began by assessing their system requirements and designing a CAN bus network layout that suited their needs.
They implemented the CAN bus system in phases to ensure that production continued without major disruptions.
Throughout this process, they trained their staff extensively on the new technology, ensuring a smooth transition.
Results
Post-implementation, the plant saw a 30% increase in productivity due to more efficient communication.
Downtime was reduced drastically, and maintenance costs dropped by 25%.
The overall operational costs decreased, showing clear proof of the benefits of CAN bus technology.
Future Trends in CAN Bus Technology
The future of CAN bus technology looks promising, with ongoing advancements expected to further improve its application in manufacturing.
Integration with IoT
One of the most anticipated trends is the integration of CAN bus technology with the Internet of Things (IoT).
This integration will allow for even more efficient data collection and communication between devices.
In a manufacturing context, sensors and devices connected via IoT can provide real-time data, which helps in predictive maintenance and improving overall efficiency.
Enhanced Security Features
With the increasing importance of cybersecurity, future developments in CAN bus technology are likely to focus on enhanced security features.
These will help protect sensitive data and ensure that communication between devices is secure, a critical aspect for maintaining integrity in manufacturing operations.
Higher Data Transfer Rates
Continuous advancements aim to increase the data transfer rates of CAN bus systems.
Higher transfer rates mean quicker communication between devices, further reducing latency and increasing the speed of manufacturing processes.
Incorporating CAN bus technology into manufacturing communication networks provides significant improvements in efficiency, reliability, and cost-effectiveness.
By understanding its benefits and implementation processes, manufacturing facilities can transition smoothly to a more advanced and streamlined communication system.
The future of CAN bus technology holds even more promise, with potential integration into broader technological advancements, ensuring that it remains a vital component of modern manufacturing communication networks.
資料ダウンロード
QCD調達購買管理クラウド「newji」は、調達購買部門で必要なQCD管理全てを備えた、現場特化型兼クラウド型の今世紀最高の購買管理システムとなります。
ユーザー登録
調達購買業務の効率化だけでなく、システムを導入することで、コスト削減や製品・資材のステータス可視化のほか、属人化していた購買情報の共有化による内部不正防止や統制にも役立ちます。
NEWJI DX
製造業に特化したデジタルトランスフォーメーション(DX)の実現を目指す請負開発型のコンサルティングサービスです。AI、iPaaS、および先端の技術を駆使して、製造プロセスの効率化、業務効率化、チームワーク強化、コスト削減、品質向上を実現します。このサービスは、製造業の課題を深く理解し、それに対する最適なデジタルソリューションを提供することで、企業が持続的な成長とイノベーションを達成できるようサポートします。
オンライン講座
製造業、主に購買・調達部門にお勤めの方々に向けた情報を配信しております。
新任の方やベテランの方、管理職を対象とした幅広いコンテンツをご用意しております。
お問い合わせ
コストダウンが利益に直結する術だと理解していても、なかなか前に進めることができない状況。そんな時は、newjiのコストダウン自動化機能で大きく利益貢献しよう!
(Β版非公開)