- お役立ち記事
- Technology of Current Sensors and Their Applications in Manufacturing
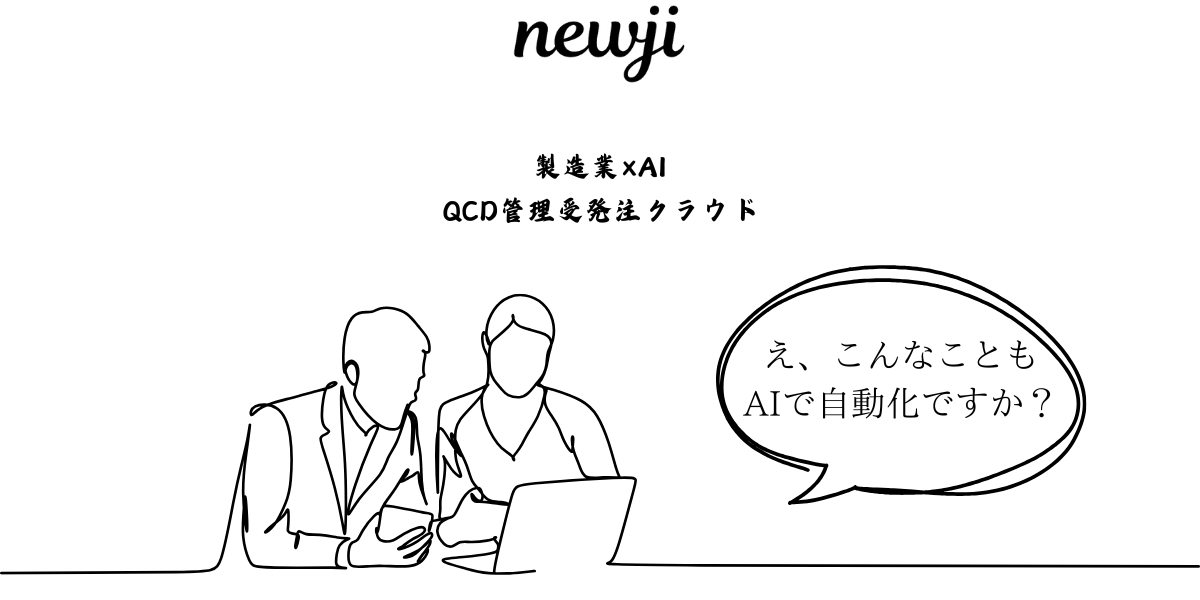
Technology of Current Sensors and Their Applications in Manufacturing
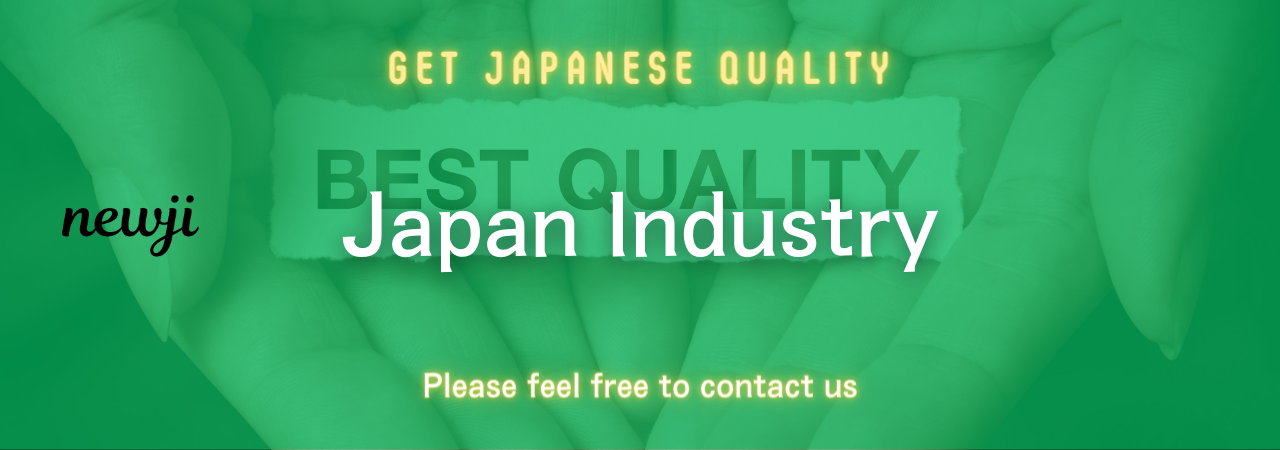
Current sensors play a vital role in modern manufacturing processes.
These sensors help monitor and measure the flow of electrical current in various machines and equipment, ensuring smooth operation and safety.
Understanding the technology behind current sensors and their applications in manufacturing can provide significant advantages for businesses.
In this article, we will explore the various types of current sensors, the technology that drives them, and their crucial applications in the manufacturing sector.
目次
Types of Current Sensors
Current sensors come in different types based on their design and application needs.
Each type has unique characteristics, making them suitable for specific situations.
Resistive Current Sensors
Resistive current sensors, also known as shunt resistors, are simple and cost-effective.
They measure current by detecting the voltage drop across a resistor placed in the current path.
This method provides accurate readings but may introduce resistance into the circuit, which could affect high-precision applications.
Magnetic Current Sensors
Magnetic current sensors use the magnetic field generated by the current to measure its intensity.
They are further divided into Hall Effect sensors, Rogowski coils, and magnetic transformers.
– **Hall Effect Sensors**: These sensors use the Hall Effect principle, where a magnetic field induces a voltage in a conductor. They are non-intrusive and can handle both AC and DC currents.
– **Rogowski Coils**: These are flexible and easy to install around conductors. They are ideal for measuring high-frequency currents and do not saturate at high current levels.
– **Magnetic Transformers**: These sensors use a magnetic core and secondary winding to measure AC currents. They offer high accuracy and are commonly used in power monitoring applications.
Optical Current Sensors
Optical current sensors use light to measure the electrical current.
They employ the Faraday effect, where the polarization of light changes in response to a magnetic field.
Optical sensors offer high accuracy and immunity to electromagnetic interference, making them suitable for high-voltage applications and harsh environments.
Technology Behind Current Sensors
The technology behind current sensors has evolved significantly, enhancing their accuracy, reliability, and range of applications.
Analog and Digital Circuits
Current sensors can output signals in analog or digital formats.
Analog sensors provide continuous voltage or current signals proportional to the measured current.
Digital sensors, on the other hand, convert analog signals into digital data, which can be easily processed by microcontrollers and computer systems.
Digital sensors offer better noise immunity and are easier to integrate with modern electronics.
Microcontroller Integration
Modern current sensors often incorporate microcontrollers to enhance functionality.
Microcontrollers can process sensor data in real-time, apply calibration algorithms, and communicate with other devices via interfaces like I2C, SPI, or UART.
This integration enables advanced features such as self-diagnosis, data logging, and remote monitoring.
Wireless Connectivity
With the advent of the Industrial Internet of Things (IIoT), wireless connectivity has become a key feature of current sensors.
Wireless communication protocols like Bluetooth, Zigbee, and Wi-Fi enable sensors to transmit data to central monitoring systems without the need for extensive wiring.
This improves installation flexibility and reduces maintenance costs.
Applications in Manufacturing
Current sensors have a wide range of applications in the manufacturing industry.
They help improve efficiency, safety, and reliability across various processes and machinery.
Motor Control
Current sensors are crucial in monitoring and controlling electric motors used in manufacturing.
By measuring motor current, sensors help detect issues like overloads, short circuits, and inefficiencies.
This allows for timely maintenance, preventing downtime and extending the lifespan of motors.
Additionally, current sensors enable precise control of motor speed and torque, enhancing process accuracy.
Energy Management
Effective energy management is essential for cost reduction and sustainability in manufacturing.
Current sensors contribute to energy management by monitoring power consumption of machinery and lighting systems.
This data helps identify energy-hungry equipment, optimize production schedules, and implement energy-saving measures.
As a result, manufacturers can reduce energy costs and minimize their environmental footprint.
Predictive Maintenance
Predictive maintenance relies on real-time data to forecast equipment failures and schedule maintenance activities proactively.
Current sensors are integral to this approach, as they provide insights into the operational health of machinery.
By analyzing current patterns, sensors can detect anomalies that may indicate potential failures.
This enables manufacturers to address issues before they escalate, reducing unplanned downtime and maintenance costs.
Quality Control
Maintaining high-quality standards is vital in manufacturing.
Current sensors assist in quality control by ensuring equipment operates within specified parameters.
For instance, in welding processes, sensors can monitor welding current to ensure consistent weld quality.
Deviations from standard current profiles can indicate defects, prompting immediate corrective actions.
Thus, current sensors contribute to maintaining product quality and reducing waste.
Safety Systems
Ensuring the safety of workers and equipment in manufacturing environments is paramount.
Current sensors play a role in various safety systems, such as circuit protection and fault detection.
They help identify hazardous conditions like ground faults, short circuits, and overcurrent scenarios, triggering protective mechanisms to isolate faults.
This prevents damage to equipment, reduces fire risk, and safeguards personnel.
Future Trends and Developments
The field of current sensors is continuously evolving, driven by advancements in technology and changing industry needs.
Miniaturization
As electronic devices and machinery become more compact, the demand for smaller current sensors increases.
Miniaturization efforts focus on developing sensors that occupy less space without compromising performance.
Achieving this involves advancements in materials, fabrication techniques, and integration methods.
Enhanced Accuracy and Precision
Improving the accuracy and precision of current sensors remains a priority.
Researchers are exploring new materials and sensing principles to achieve finer measurements.
Enhanced accuracy is particularly critical in applications like medical devices, aerospace, and high-precision manufacturing, where even slight deviations can have significant consequences.
Greater Integration with Smart Systems
The integration of current sensors with smart systems and artificial intelligence (AI) will unlock new possibilities.
AI algorithms can analyze sensor data more effectively, identifying complex patterns and making data-driven decisions.
This will further enhance applications like predictive maintenance, energy management, and process optimization.
Conclusion
Current sensors are indispensable in the modern manufacturing landscape.
They support a wide range of applications, from motor control and energy management to predictive maintenance and quality control.
The technology behind current sensors continues to advance, offering improved accuracy, reliability, and integration capabilities.
As industries evolve and adopt smarter manufacturing practices, current sensors will play an increasingly critical role in driving efficiency, safety, and sustainability.
資料ダウンロード
QCD調達購買管理クラウド「newji」は、調達購買部門で必要なQCD管理全てを備えた、現場特化型兼クラウド型の今世紀最高の購買管理システムとなります。
ユーザー登録
調達購買業務の効率化だけでなく、システムを導入することで、コスト削減や製品・資材のステータス可視化のほか、属人化していた購買情報の共有化による内部不正防止や統制にも役立ちます。
NEWJI DX
製造業に特化したデジタルトランスフォーメーション(DX)の実現を目指す請負開発型のコンサルティングサービスです。AI、iPaaS、および先端の技術を駆使して、製造プロセスの効率化、業務効率化、チームワーク強化、コスト削減、品質向上を実現します。このサービスは、製造業の課題を深く理解し、それに対する最適なデジタルソリューションを提供することで、企業が持続的な成長とイノベーションを達成できるようサポートします。
オンライン講座
製造業、主に購買・調達部門にお勤めの方々に向けた情報を配信しております。
新任の方やベテランの方、管理職を対象とした幅広いコンテンツをご用意しております。
お問い合わせ
コストダウンが利益に直結する術だと理解していても、なかなか前に進めることができない状況。そんな時は、newjiのコストダウン自動化機能で大きく利益貢献しよう!
(Β版非公開)