- お役立ち記事
- FMEA(Failure Modes and Effects Analysis)で製造プロセスのリスクを低減する手法
FMEA(Failure Modes and Effects Analysis)で製造プロセスのリスクを低減する手法
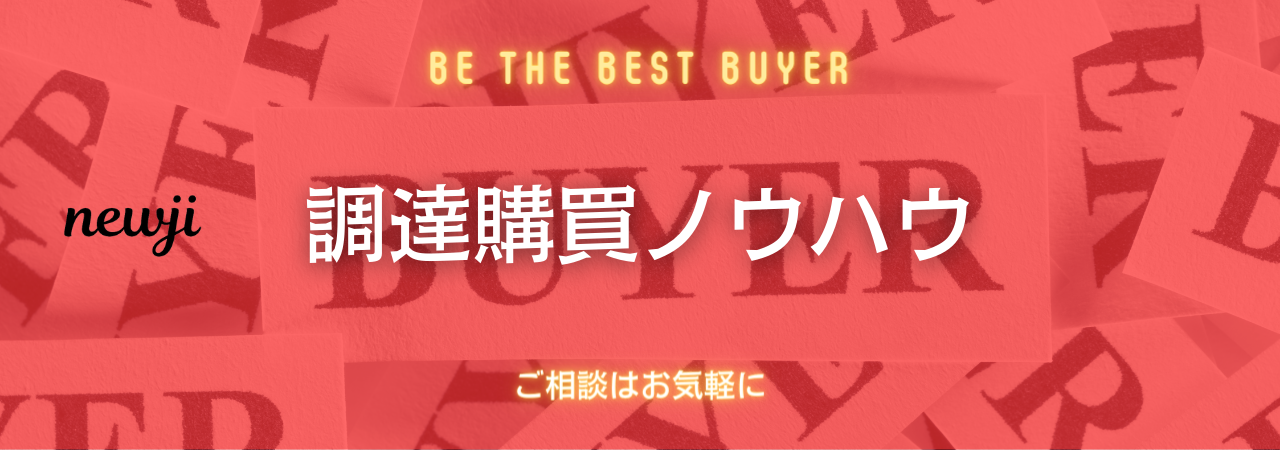
目次
FMEA(Failure Modes and Effects Analysis)とは?
FMEA(Failure Modes and Effects Analysis)とは、製品やプロセスの潜在的な不具合や失敗のモード(方式)を洗い出し、それが及ぼす影響を評価し、予防策や軽減策を講じるための分析手法です。
製造業においては、製品の品質を保証するため、そして生産コストを削減するために利用されることが多いです。
FMEAを実施することで、製造プロセスのリスクを体系的に低減することが可能となります。
FMEAの基本プロセス
FMEAの基本プロセスは、大きく以下のステップに分けられます。
ステップ1: システムの理解
まず最初に、分析対象の製品やプロセスを詳細に理解する必要があります。
これには、設計図や過去のデータ、製造プロセスの詳細なフローチャートなどが含まれます。
情報を収集し、関係者と共有することで、共通の理解を持つことが重要です。
ステップ2: 潜在的な失敗モードの特定
次に、潜在的な失敗モードを洗い出します。
失敗モードとは、製品やプロセスが期待通りに機能しない場合の事象を指します。
これには、不良品の発生、機械の故障、手順の誤りなどが含まれます。
チームメンバーとブレインストーミングを行い、あらゆる可能性を検討します。
ステップ3: 失敗モードの影響の評価
洗い出した失敗モードが製品やプロセスに与える影響を評価します。
影響の評価には、製品品質の劣化、製造コストの増加、納期の遅延などが含まれます。
これにより、各失敗モードの深刻度(Severity)を数値化してランク付けします。
ステップ4: 失敗モードの発生確率と検出確率の評価
次に、失敗モードの発生確率(Occurrence)と、それを検出する確率(Detection)を評価します。
発生確率は、過去のデータや専門家の意見を基に見積もります。
検出確率は、現行の検査プロセスやモニタリングシステムがどれだけ効果的かを評価します。
ステップ5: リスクの計算と優先順位付け
上記の評価を基に、各失敗モードのリスクを計算します。
その際、一般的には「RPN(Risk Priority Number)」という数値が用いられます。
RPNは、深刻度、発生確率、検出確率の積として計算されます。
RPNが高い項目から優先的に改善策を講じるべきです。
ステップ6: 改善策の策定と実施
最終ステップとして、リスクを低減するための具体的な改善策を策定し、実施します。
改善策には、設計の変更、プロセスの最適化、新しい検査手法の導入などが考えられます。
実施後は、その効果を評価し、必要に応じてさらに改善を行います。
FMEAがもたらすメリット
FMEAを実施することで、製造プロセスに多くのメリットがもたらされます。
リスクの可視化と低減
FMEAはリスクを体系的に洗い出し、評価することで、それを可視化します。
これにより、潜在的な問題を事前に発見し、早期に対応することが可能となります。
具体的な対策を講じることで、リスクを大幅に低減できます。
品質向上とコスト削減
製品の不良発生率を低減することで、品質の向上が図れます。
また、不良品が市場に流出するリスクを低減することで、顧客満足度を向上させるだけでなく、保証や返品にかかるコストも削減できます。
プロセスの効率化
FMEAを通じて製造プロセスの無駄や非効率を改善することができます。
これは、作業手順の改善や設備の最適化、新しい技術の導入などを通じて実現されます。
その結果、生産性が向上し、リードタイムの短縮にも寄与します。
実際の事例: FMEAを活用した製造プロセス改善
ここで、実際の製造現場でFMEAを活用した事例を紹介します。
事例: 自動車部品製造会社
ある自動車部品製造会社では、製品の不良発生率が高く、納期遅延が頻繁に発生していました。
そこでFMEAを導入し、製造プロセスの徹底的な見直しを行いました。
プロセスと結果
まず、製造ラインごとにチームを編成し、詳細なプロセスフローチャートを作成しました。
次に、各工程での潜在的な失敗モードを洗い出し、それが製品品質や納期に与える影響を評価しました。
その結果、高リスクと判定された失敗モードに対して、具体的な改善策を講じました。
例えば、ある工程では機械の故障が頻発していたため、定期的なメンテナンスと予防保全策を強化しました。
また、検査工程も見直し、新しい検査機器を導入して検出確率を大幅に向上させました。
これにより、不良発生率が50%削減され、納期遅延も大幅に改善されました。
FMEAの導入により、製造プロセスのリスクが体系的に低減され、全体の効率が向上しました。
最新技術を活用したFMEAの進化
近年、FMEAも最新の技術を活用することでさらに進化しています。
デジタルトランスフォーメーション(DX)
製造業のデジタルトランスフォーメーション(DX)が進む中、FMEAもデジタルツールを活用して実施することが増えています。
例えば、クラウドベースのFMEAソフトウェアは、リアルタイムでのデータ共有やチーム間のコラボレーションを可能にし、分析の効率性を向上させます。
ビッグデータと機械学習
ビッグデータと機械学習を組み合わせることで、過去のデータを基にした高精度なリスク予測が可能になります。
これにより、より正確な発生確率や検出確率の評価が行え、リスク低減策の効果も事前にシミュレーションすることが可能となります。
まとめ: FMEAの重要性と今後の展望
FMEAは、製造プロセスのリスクを低減するための非常に有効な手法です。
潜在的な問題を事前に洗い出し、具体的な対策を講じることで、製品の品質向上、コスト削減、プロセスの効率化を実現します。
また、最新技術の導入により、FMEAはさらに進化を遂げています。
製造業の現場において、FMEAは不可欠なツールとして位置づけられています。
今後もその重要性は増していくことでしょう。
ぜひ、自社の製造プロセス改善にFMEAを活用し、さらなる発展を目指してください。
資料ダウンロード
QCD調達購買管理クラウド「newji」は、調達購買部門で必要なQCD管理全てを備えた、現場特化型兼クラウド型の今世紀最高の購買管理システムとなります。
ユーザー登録
調達購買業務の効率化だけでなく、システムを導入することで、コスト削減や製品・資材のステータス可視化のほか、属人化していた購買情報の共有化による内部不正防止や統制にも役立ちます。
NEWJI DX
製造業に特化したデジタルトランスフォーメーション(DX)の実現を目指す請負開発型のコンサルティングサービスです。AI、iPaaS、および先端の技術を駆使して、製造プロセスの効率化、業務効率化、チームワーク強化、コスト削減、品質向上を実現します。このサービスは、製造業の課題を深く理解し、それに対する最適なデジタルソリューションを提供することで、企業が持続的な成長とイノベーションを達成できるようサポートします。
オンライン講座
製造業、主に購買・調達部門にお勤めの方々に向けた情報を配信しております。
新任の方やベテランの方、管理職を対象とした幅広いコンテンツをご用意しております。
お問い合わせ
コストダウンが利益に直結する術だと理解していても、なかなか前に進めることができない状況。そんな時は、newjiのコストダウン自動化機能で大きく利益貢献しよう!
(Β版非公開)