- お役立ち記事
- Manufacturing Innovation Techniques that Balance Quality and Cost: Expert-Led Productivity Improvement Strategies
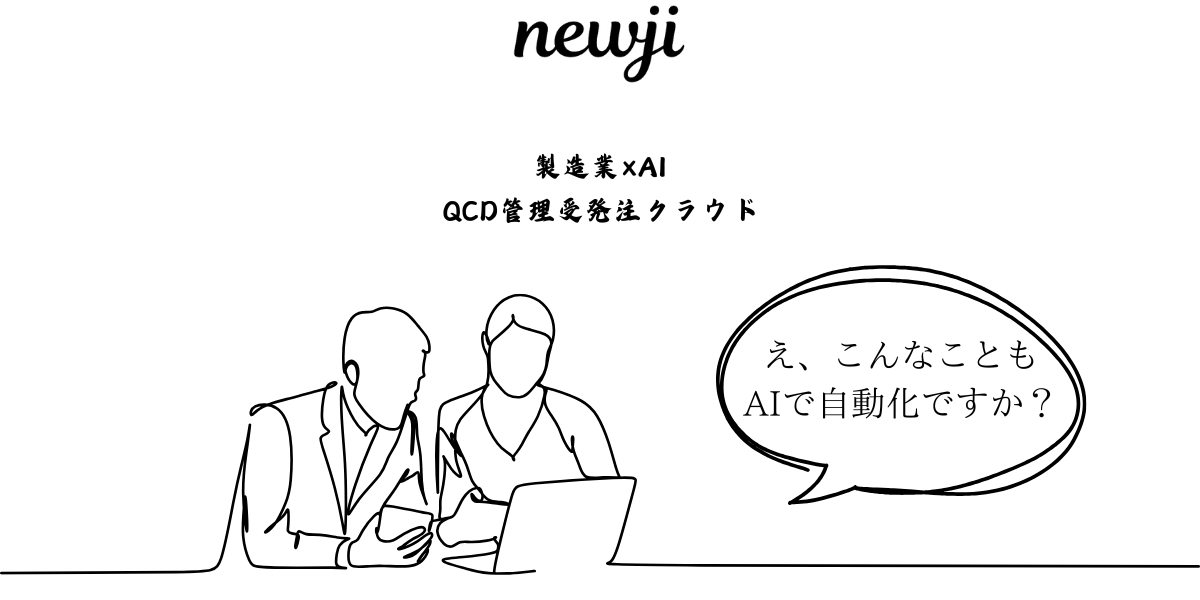
Manufacturing Innovation Techniques that Balance Quality and Cost: Expert-Led Productivity Improvement Strategies
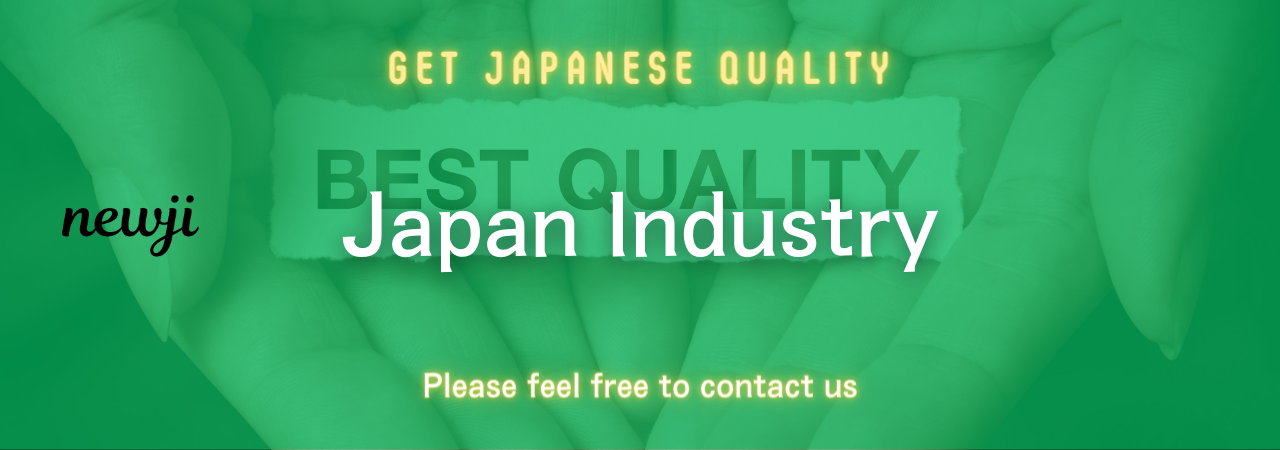
In today’s rapidly evolving industrial landscape, manufacturing firms face the dual pressures of maintaining high quality while controlling costs.
Achieving this delicate balance requires innovative techniques and expert-led productivity improvement strategies.
The goal is to streamline operations, enhance efficiency, and foster a culture of continuous improvement.
In this article, we will explore various methods to strike this balance effectively.
目次
Lean Manufacturing: The Foundation of Efficiency
Understanding Lean Principles
Lean Manufacturing is a systematic approach aimed at minimizing waste without compromising productivity.
The key principles of lean manufacturing focus on streamlining workflows, reducing production costs, and improving overall quality.
These principles include value stream mapping, continuous improvement (Kaizen), and just-in-time production.
Implementing Lean Methods
To implement lean manufacturing techniques, firms must begin with a thorough assessment of their current processes.
This involves identifying areas where waste occurs—be it through excess inventory, overproduction, or operational bottlenecks.
Once identified, teams can employ various lean tools like 5S (sort, set in order, shine, standardize, sustain) and Kanban to enhance workflow and reduce inefficiencies.
Advanced Automation and Robotics
Embracing Industry 4.0
Industry 4.0 represents the fourth industrial revolution, characterized by the integration of digital technologies into manufacturing processes.
This includes the use of advanced automation and robotics to maximize efficiency and minimize human error.
Robots can handle repetitive tasks with precision, freeing up human workers for more complex activities that require creativity and problem-solving skills.
Smart Manufacturing Systems
Intelligent manufacturing systems, incorporating Internet of Things (IoT) devices, sensors, and machine learning algorithms, enable real-time monitoring and optimization of production lines.
These systems can predict maintenance needs, thereby reducing downtime and extending the lifespan of equipment.
Investing in smart systems ensures that manufacturers can maintain both high quality and cost control.
Evolving Quality Management Systems (QMS)
Importance of Quality Management
A robust Quality Management System (QMS) is essential for any manufacturing operation.
It ensures that products meet customer expectations and comply with industry standards.
A comprehensive QMS includes regular inspections, audits, and adherence to ISO standards.
Adopting Total Quality Management (TQM)
Total Quality Management (TQM) is a holistic approach that involves all employees in the quest for continuous quality improvement.
This strategy emphasizes close collaboration between departments and the use of statistical quality control techniques.
By embedding quality into every stage of the production process, firms can reduce defects and rework, thereby lowering costs.
Agile Manufacturing: Adapting to Change
Flexibility and Responsiveness
Agile manufacturing focuses on creating flexible production systems that can quickly respond to changes in market demand or customer requirements.
This agility allows firms to offer customized products without incurring prohibitive costs.
It involves using modular production systems, cross-trained workers, and flexible supply chains.
Rapid Prototyping and Iteration
With the help of 3D printing and computer-aided design (CAD) software, manufacturers can rapidly develop and test product prototypes.
This capability enables quick iteration and refinement before full-scale production, reducing time-to-market and ensuring products meet quality standards.
Sustainable Manufacturing Practices
Environmental Responsibility
Sustainability is increasingly a priority for manufacturing firms, driven by both regulatory requirements and consumer preference.
Sustainable manufacturing practices include reducing waste, recycling materials, and utilizing renewable energy sources.
Cost Benefits of Sustainability
While there is an initial investment associated with sustainable practices, the long-term benefits include lower operational costs and improved brand reputation.
Energy-efficient equipment, for example, reduces utility bills.
Furthermore, waste reduction through recycling can lead to significant cost savings.
Employee Training and Development
Investment in Human Capital
An often-overlooked aspect of manufacturing innovation is the development of the workforce.
Continuous training ensures employees are well-versed in the latest technologies and methodologies.
Skilled workers are more efficient and can operate complex machinery with fewer errors.
Fostering a Culture of Innovation
Encouraging a culture of innovation involves more than just providing training.
It requires creating an environment where employees feel empowered to suggest improvements and experiment with new ideas.
This collaborative atmosphere can lead to breakthroughs in both quality and efficiency.
Data-Driven Decision Making
Utilizing Big Data Analytics
The proliferation of data in modern manufacturing environments offers immense potential for improvement.
By leveraging big data analytics, firms can gain insights into every aspect of their operations.
Predictive analytics can forecast demand, optimize supply chains, and identify potential issues before they escalate.
Continuous Monitoring and Feedback
Real-time data monitoring allows for immediate feedback and corrective actions.
Implementing a robust feedback loop ensures that any deviations from the desired quality or productivity levels are quickly addressed.
This proactive approach reduces waste and maintains high standards.
Conclusion
Balancing quality and cost in manufacturing is not an easy task, but it is achievable through the adoption of innovative techniques and expert-led strategies.
From lean manufacturing methods to smart systems and sustainable practices, there are numerous ways to enhance productivity while maintaining high standards.
Investing in employee training, fostering a culture of continuous improvement, and leveraging data analytics are also crucial components.
By embracing these approaches, manufacturing firms can position themselves for success in an increasingly competitive market.
資料ダウンロード
QCD調達購買管理クラウド「newji」は、調達購買部門で必要なQCD管理全てを備えた、現場特化型兼クラウド型の今世紀最高の購買管理システムとなります。
ユーザー登録
調達購買業務の効率化だけでなく、システムを導入することで、コスト削減や製品・資材のステータス可視化のほか、属人化していた購買情報の共有化による内部不正防止や統制にも役立ちます。
NEWJI DX
製造業に特化したデジタルトランスフォーメーション(DX)の実現を目指す請負開発型のコンサルティングサービスです。AI、iPaaS、および先端の技術を駆使して、製造プロセスの効率化、業務効率化、チームワーク強化、コスト削減、品質向上を実現します。このサービスは、製造業の課題を深く理解し、それに対する最適なデジタルソリューションを提供することで、企業が持続的な成長とイノベーションを達成できるようサポートします。
オンライン講座
製造業、主に購買・調達部門にお勤めの方々に向けた情報を配信しております。
新任の方やベテランの方、管理職を対象とした幅広いコンテンツをご用意しております。
お問い合わせ
コストダウンが利益に直結する術だと理解していても、なかなか前に進めることができない状況。そんな時は、newjiのコストダウン自動化機能で大きく利益貢献しよう!
(Β版非公開)