- お役立ち記事
- Approaches to Achieving Zero Human Errors
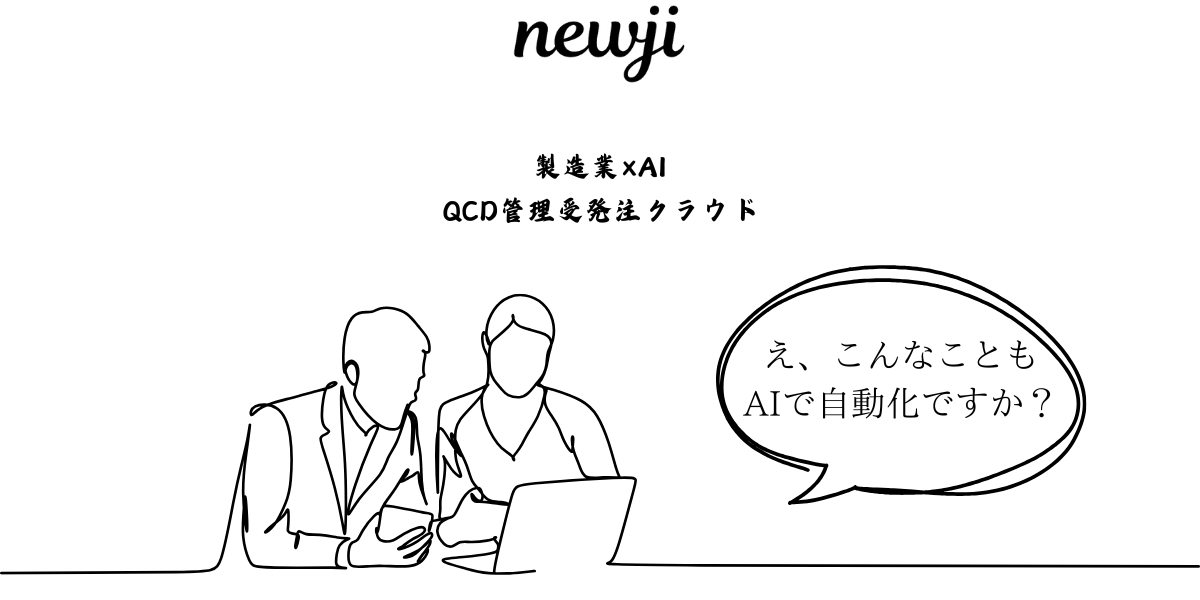
Approaches to Achieving Zero Human Errors
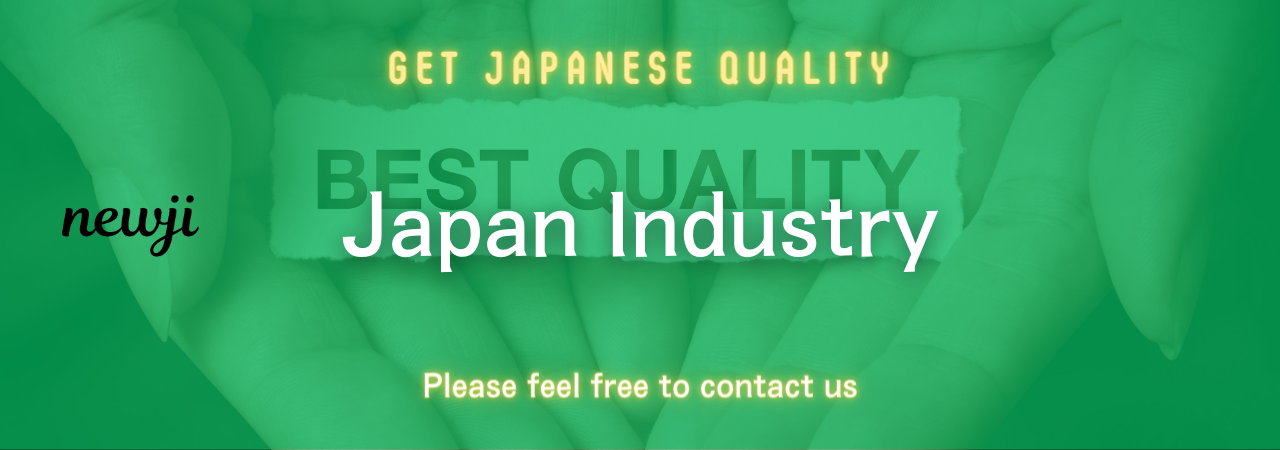
Human error is an unavoidable part of our daily lives, yet in certain environments, such mistakes can have dire consequences. From medical fields to aviation, even minor mistakes can lead to significant repercussions. Achieving zero human errors, though ambitious, is not entirely out of reach. This article offers a detailed exploration of strategies and methods that organizations can adopt to steer closer to this goal.
目次
The Importance of Understanding Human Error
Before diving into strategies to reduce human errors, it is crucial to understand what human error entails. At its core, human error refers to any mistake made by a person that leads to a negative outcome. Errors can stem from various factors, including lack of knowledge, fatigue, or even simple oversight. By identifying the root causes, organizations can begin to develop targeted strategies to mitigate them.
Establishing a Culture of Safety
Leadership and Commitment
The journey toward minimizing human error begins with a strong leadership commitment to safety. Leaders at all levels must prioritize safety and create an environment where it is taken seriously. This commitment should be demonstrated through policies, procedures, and direct actions. When employees see that leadership genuinely values safety, they are more likely to adopt similar attitudes.
Open Communication
A culture of safety thrives on open communication. Employees should feel comfortable reporting potential hazards, near-misses, or actual errors without fear of punishment. Encouraging a no-blame culture can lead to more accurate and timely reporting. This data is invaluable for identifying patterns and implementing corrective measures.
Comprehensive Training and Education
Initial Training Programs
Proper training is the cornerstone of reducing human errors. New employees should undergo comprehensive training programs that cover all aspects of their roles. This training should include hands-on practice, assessments, and regular updates to ensure that knowledge remains current.
Continuous Learning
Learning is an ongoing process, especially in dynamic fields. Organizations should invest in continuous education opportunities for their employees. This could include workshops, seminars, or even online courses. By fostering a culture of continuous improvement, employees are equipped to handle evolving challenges effectively.
Implementing Standardized Procedures
Clear and Concise Protocols
Standardized procedures are vital in reducing variability and minimizing errors. Protocols should be clear, concise, and easy to follow. Visual aids, such as flowcharts and checklists, can enhance understanding and compliance.
Regular Reviews and Updates
Over time, certain procedures may become outdated or less effective. Regularly reviewing and updating protocols ensures that they remain relevant and practical. Incorporating feedback from employees can also provide valuable insights into areas of improvement.
Leveraging Technology
Automation
Technology can play a significant role in reducing human errors. Automation of repetitive or complex tasks can minimize the likelihood of mistakes. For instance, in manufacturing, automated systems can consistently perform tasks with precision that human hands might not achieve.
Decision Support Systems
Decision support systems (DSS) can aid employees in making better-informed decisions. By providing data analysis, predictions, and recommendations, DSS helps reduce the cognitive load on human operators. This, in turn, decreases the risk of errors stemming from mental fatigue or overload.
Designing for Humans
User-Friendly Interfaces
The design of tools and systems plays a crucial role in how easily employees can interact with them. User-friendly interfaces that are intuitive and easy to navigate reduce the chances of operational mistakes. Ergonomics should also be considered to decrease physical strain and discomfort, further lowering error rates.
Feedback Mechanisms
Effective feedback mechanisms provide real-time information on the outcomes of actions. This can help employees quickly identify and correct errors. Immediate feedback loops are essential for maintaining high levels of accuracy and performance.
Monitoring and Continuous Improvement
Performance Metrics
Establishing key performance indicators (KPIs) allows organizations to measure and monitor the effectiveness of their error-reduction strategies. Metrics such as error rates, number of near-misses, and compliance levels can provide valuable data for analysis.
Periodic Audits
Regular audits can identify gaps in procedures and areas where errors are more likely to occur. These audits should be thorough and involve input from various stakeholders within the organization. Findings from audits should be used to refine strategies and enhance overall performance.
Building Resilience
Robust Backup Systems
Despite best efforts, errors can still occur. Implementing robust backup systems ensures that there is a safety net in place to catch and rectify mistakes before they escalate. This could include secondary checks, redundancy systems, or emergency response protocols.
Resilience Training
Training employees to develop resilience can enable them to handle errors more effectively when they do occur. Resilience training helps individuals remain calm, think clearly, and make better decisions under pressure.
Conclusion
While achieving zero human errors is an ambitious goal, it is not unattainable. By understanding the nature of human errors and implementing comprehensive strategies, organizations can significantly reduce the incidence and impact of such mistakes. Fostering a culture of safety, adopting continuous training, leveraging technology, and designing systems with the human user in mind are all critical components of this endeavor.
As organizations continue to strive for excellence, the commitment to minimizing human errors will ultimately lead to safer, more efficient operations and better outcomes for all stakeholders.
資料ダウンロード
QCD調達購買管理クラウド「newji」は、調達購買部門で必要なQCD管理全てを備えた、現場特化型兼クラウド型の今世紀最高の購買管理システムとなります。
ユーザー登録
調達購買業務の効率化だけでなく、システムを導入することで、コスト削減や製品・資材のステータス可視化のほか、属人化していた購買情報の共有化による内部不正防止や統制にも役立ちます。
NEWJI DX
製造業に特化したデジタルトランスフォーメーション(DX)の実現を目指す請負開発型のコンサルティングサービスです。AI、iPaaS、および先端の技術を駆使して、製造プロセスの効率化、業務効率化、チームワーク強化、コスト削減、品質向上を実現します。このサービスは、製造業の課題を深く理解し、それに対する最適なデジタルソリューションを提供することで、企業が持続的な成長とイノベーションを達成できるようサポートします。
オンライン講座
製造業、主に購買・調達部門にお勤めの方々に向けた情報を配信しております。
新任の方やベテランの方、管理職を対象とした幅広いコンテンツをご用意しております。
お問い合わせ
コストダウンが利益に直結する術だと理解していても、なかなか前に進めることができない状況。そんな時は、newjiのコストダウン自動化機能で大きく利益貢献しよう!
(Β版非公開)