- お役立ち記事
- Basics and Practical Approaches to Die Clearance Adjustment in Press Processing
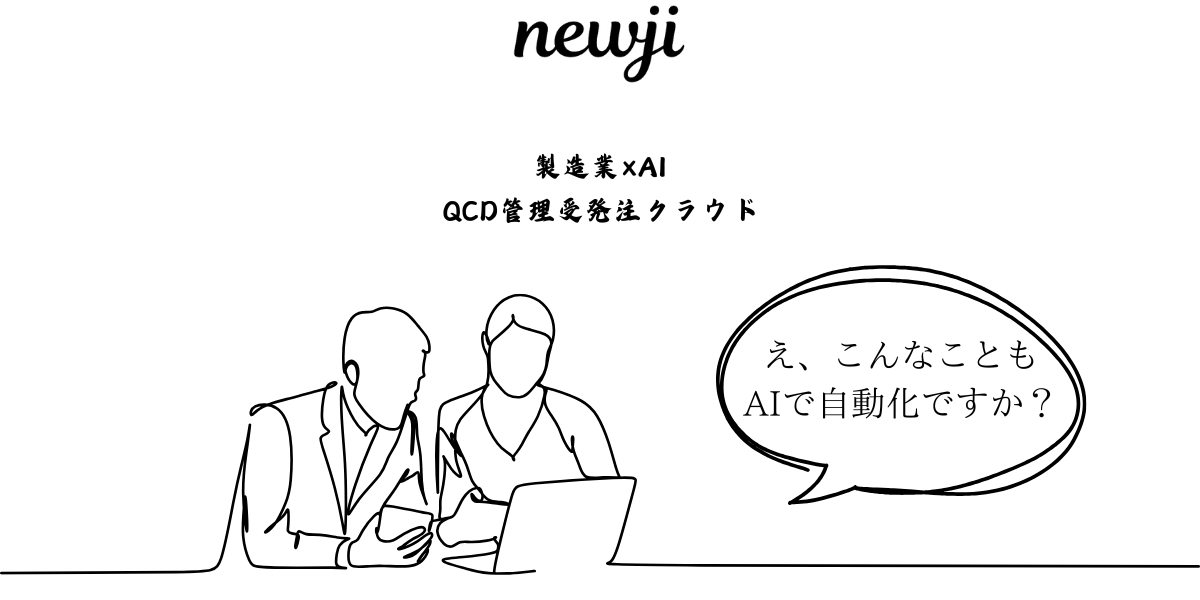
Basics and Practical Approaches to Die Clearance Adjustment in Press Processing
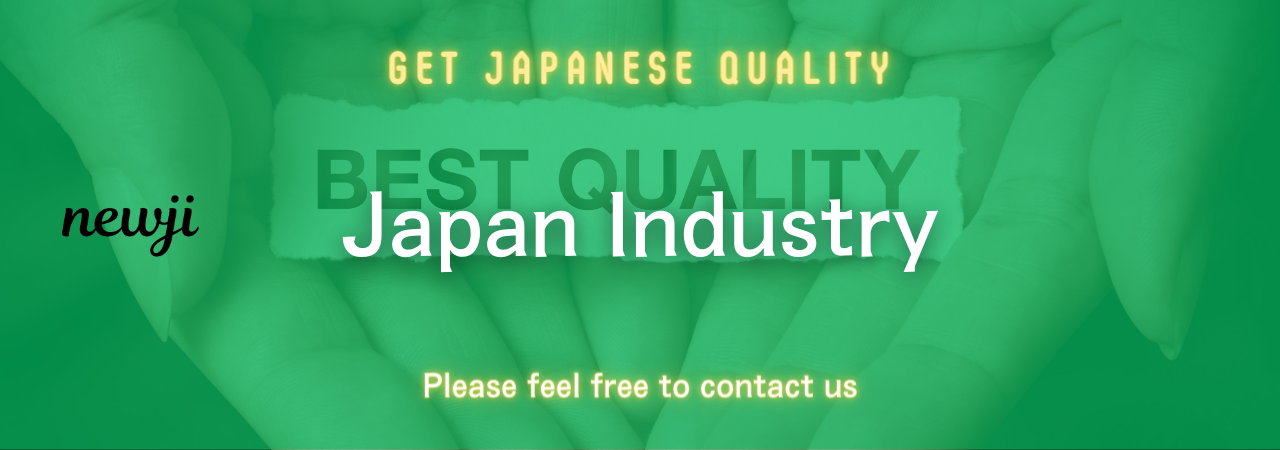
Die clearance adjustment is an essential aspect of press processing, significantly impacting the quality of the final product and the longevity of the machinery. Understanding this concept and its practical application can lead to improved efficiency and reduced waste in manufacturing processes. This article delves into the basics and practical approaches to die clearance adjustment in press processing.
目次
Understanding Die Clearance
Die clearance refers to the gap between the punch and the die in a press machine. This small yet critical distance allows the metal to be sheared efficiently during the punching process. Proper die clearance is crucial for achieving clean cuts, reducing burr formation, and minimizing tool wear.
Importance of Correct Die Clearance
Correct die clearance is vital for several reasons:
It ensures a clean cut, reducing the need for secondary operations like deburring.
Proper clearance helps in maintaining the integrity of the part being produced, reducing the risk of cracks and distortions.
It extends the life of both punches and dies, leading to cost savings in tool maintenance and replacement.
Optimal clearance reduces the overall force needed for the punching process, improving the efficiency of the press machine.
Factors Affecting Die Clearance
Several factors influence the determination of optimal die clearance:
Material Type: Different metals have varying hardness and ductility, affecting how they respond to the shearing process. Softer metals like aluminum may require a different clearance compared to harder metals like stainless steel.
Material Thickness: Thicker materials generally require a larger die clearance to ensure a clean cut.
Punch and Die Condition: Worn or damaged tools can impact the effectiveness of the shearing process. Regular maintenance and timely replacement are crucial.
Type of Cut: The complexity and shape of the cut can also influence the required clearance. Intricate shapes may need more precise adjustments.
Calculating Die Clearance
Determining the correct die clearance involves calculations based on the material properties and thickness. A common method is using a percentage of the material thickness.
Standard Clearance Rates
Different materials have established standard clearance rates.
Mild steel typically requires a clearance of about 10-15% of the material thickness.
Stainless steel usually needs around 15-20%.
Aluminum may need less, often around 5-10%.
Using these standard rates helps in setting a baseline, but adjustments may be necessary based on specific requirements and conditions.
Practical Calculation Example
Consider a mild steel sheet with a thickness of 2mm. Applying the standard clearance rate:
Optimal die clearance = Material thickness * Clearance percentage
= 2mm * 15%
= 0.3mm
So, for a 2mm thick mild steel sheet, the ideal die clearance would be 0.3mm.
Adjusting Die Clearance in Press Machines
Once the optimal die clearance is calculated, the next step is to adjust the press machine accordingly. Proper adjustment involves precise measurements and handling to ensure the desired clearance is achieved.
Steps to Adjust Die Clearance
Here are the general steps to adjust die clearance:
Inspect the Tools: Ensure that both the punch and die are in good condition. Worn-out tools need to be repaired or replaced.
Clean the Setup: Remove any debris, oil, or dirt from the press machine’s working area.
Measure the Current Clearance: Use feeler gauges or a micrometer to measure the existing clearance between the punch and die.
Adjust the Die or Punch: Based on the measured clearance, adjust either the punch or the die using the machine’s adjusting screws or shims.
Re-Measure and Test: After adjusting, re-measure the clearance to ensure accuracy. Conduct a test run to check the quality of the cut and make further adjustments if necessary.
Common Challenges in Die Clearance Adjustment
Several challenges may arise during the die clearance adjustment process:
Tool Wear: Continuous use leads to tool wear, necessitating frequent adjustments to maintain optimal clearance.
Material Variability: Slight differences in material properties between batches can affect the ideal clearance, requiring continuous monitoring and adjustment.
Alignment Issues: Misalignment between the punch and die can lead to inaccurate clears, affecting the quality of the cut.
Best Practices for Die Clearance Adjustment
To ensure optimal die clearance adjustment, it is essential to follow certain best practices:
Regular Maintenance
Conduct regular inspections and maintenance of the press machine and tools. Timely detection of wear and tear ensures that problems are addressed before they affect the production quality.
Consistent Monitoring
Implement a consistent monitoring system to track the performance of the die clearance. Use quality control measures to check the cuts and adjust the clearance as needed regularly.
Training and Skill Development
Ensure that operators and technicians are well-trained in the process of die clearance adjustment. Investing in skill development can lead to better precision and efficiency in adjustments.
Use of Advanced Technology
Incorporate advanced technologies, such as CNC systems and automation, to achieve more precise adjustments. These technologies can help in maintaining optimal clearance with minimal manual intervention.
Material Handling
Proper material handling techniques help in minimizing variability and ensuring consistent material properties—critical factors in maintaining optimal die clearance.
Conclusion
Die clearance adjustment stands as a cornerstone in the realm of press processing. By comprehending its importance, accurately calculating clearance, and following best practices, manufacturers can significantly enhance product quality and operational efficiency.
Regular maintenance, consistent monitoring, skill development, and leveraging advanced technology are pivotal in achieving the optimal die clearance. As industries continue to advance, staying updated with the latest techniques and technologies will be crucial for maintaining a competitive edge in manufacturing processes.
資料ダウンロード
QCD調達購買管理クラウド「newji」は、調達購買部門で必要なQCD管理全てを備えた、現場特化型兼クラウド型の今世紀最高の購買管理システムとなります。
ユーザー登録
調達購買業務の効率化だけでなく、システムを導入することで、コスト削減や製品・資材のステータス可視化のほか、属人化していた購買情報の共有化による内部不正防止や統制にも役立ちます。
NEWJI DX
製造業に特化したデジタルトランスフォーメーション(DX)の実現を目指す請負開発型のコンサルティングサービスです。AI、iPaaS、および先端の技術を駆使して、製造プロセスの効率化、業務効率化、チームワーク強化、コスト削減、品質向上を実現します。このサービスは、製造業の課題を深く理解し、それに対する最適なデジタルソリューションを提供することで、企業が持続的な成長とイノベーションを達成できるようサポートします。
オンライン講座
製造業、主に購買・調達部門にお勤めの方々に向けた情報を配信しております。
新任の方やベテランの方、管理職を対象とした幅広いコンテンツをご用意しております。
お問い合わせ
コストダウンが利益に直結する術だと理解していても、なかなか前に進めることができない状況。そんな時は、newjiのコストダウン自動化機能で大きく利益貢献しよう!
(Β版非公開)