- お役立ち記事
- Practical Inventory Optimization Course
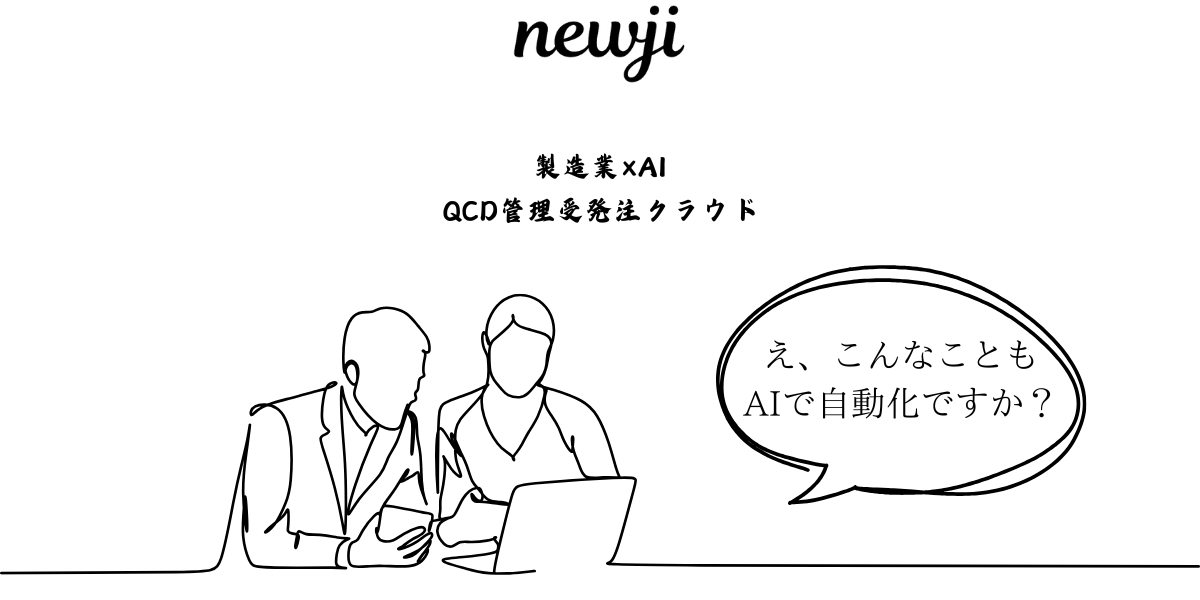
Practical Inventory Optimization Course
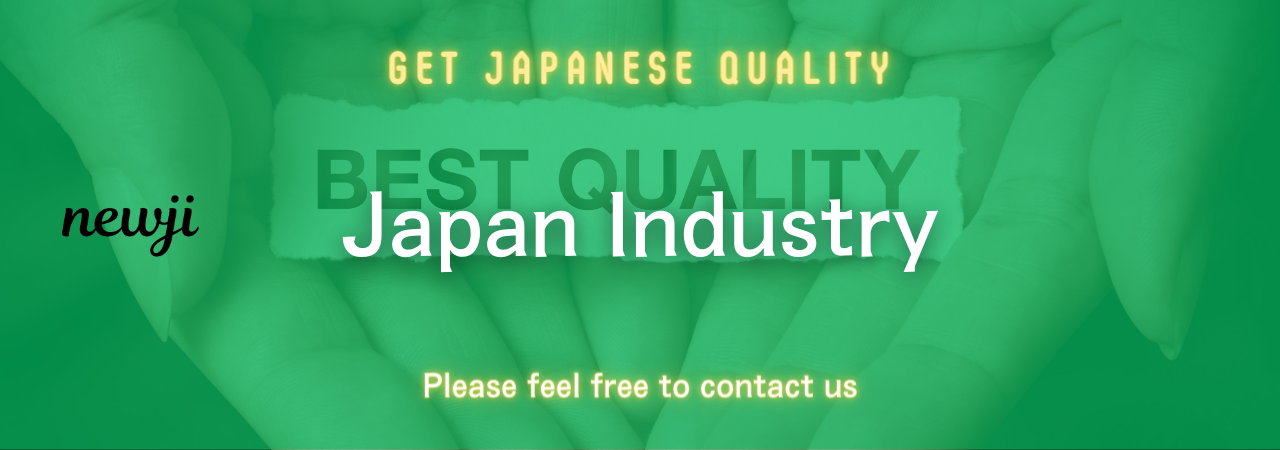
Inventory optimization is a crucial aspect of successful business management.
When done right, it helps companies reduce costs, improve cash flow, and ensure that products are available when customers need them.
In this practical course, we will explore various strategies and techniques to optimize inventory effectively.
目次
Why Inventory Optimization Matters
Efficient inventory management is vital for any business dealing with physical products.
Poor inventory management can lead to overstocking or stockouts, both of which can negatively impact a company’s bottom line.
Overstocking ties up capital in unsold goods while also incurring storage costs.
On the other hand, stockouts can result in lost sales and dissatisfied customers.
Key Concepts in Inventory Optimization
Understanding several critical concepts can significantly enhance your ability to manage inventory effectively.
Let’s delve into some of the most important areas.
Economic Order Quantity (EOQ)
EOQ is the optimal number of units you should order to minimize total inventory costs, including ordering and holding costs.
This formula helps businesses ensure they’re not overordering or underordering, thus keeping costs in check.
It’s particularly useful for companies with consistent and predictable demand.
Safety Stock
Safety stock is additional inventory held to prevent stockouts caused by demand variability or supply chain disruptions.
Calculating the right amount of safety stock is essential for maintaining service levels and customer satisfaction.
Companies often use statistical methods to estimate the optimal safety stock level accurately.
ABC Analysis
ABC analysis classifies inventory into three categories: A, B, and C.
‘A’ items are high-value products with low sales frequency, ‘B’ items are moderate in both value and sales frequency, and ‘C’ items are low-value but high-frequency sellers.
Prioritizing management efforts on ‘A’ items can yield significant benefits.
Inventory Optimization Techniques
Just-In-Time (JIT) Inventory
JIT inventory management aims to reduce carrying costs by receiving goods only as they are needed in the production process.
While this method can significantly cut costs, it also requires excellent communication and coordination with suppliers.
It’s crucial to have reliable suppliers and efficient logistics to make JIT work effectively.
Demand Forecasting
Accurate demand forecasting is essential for effective inventory optimization.
By analyzing historical sales data and market trends, businesses can predict future demand more accurately.
Techniques like time-series analysis, regression models, and machine learning algorithms are commonly used for this purpose.
With reliable forecasts, companies can maintain optimal inventory levels and minimize both overstocking and stockouts.
Automated Inventory Management Systems
Utilizing automated inventory management systems can streamline the entire inventory process.
These systems track inventory in real-time, generate reorder alerts, and provide valuable insights into sales trends.
Modern solutions often integrate with other business systems, such as ERP or CRM platforms, offering a comprehensive view of the business operations.
Automation minimizes human errors and saves time, allowing staff to focus on more strategic tasks.
Best Practices for Inventory Optimization
Regular Audits
Conduct regular inventory audits to ensure that the records align with the physical stock.
Discrepancies can indicate issues such as theft, spoilage, or administrative errors.
Regular audits help maintain accurate inventory data, which is crucial for effective decision-making.
Employee Training
Properly trained staff are essential for successful inventory management.
Educate employees on best practices, the importance of accurate data entry, and how to use inventory management software.
Well-informed employees can spot potential issues early and take corrective actions, ensuring smooth operations.
Supplier Relationships
Cultivate strong relationships with your suppliers.
Reliable suppliers who can deliver quality products on time are critical for inventory optimization.
A good relationship allows for better negotiation of terms and fosters collaboration on strategies like JIT inventory management.
Challenges in Inventory Optimization
Handling Seasonal Demand
Seasonal fluctuations can pose significant challenges.
Effective demand forecasting becomes even more critical during peak seasons.
Stocking up on inventory well in advance and negotiating flexible terms with suppliers can help manage seasonal demands efficiently.
Dealing with Supply Chain Disruptions
Unexpected supply chain disruptions can result in stockouts and lost sales.
Developing a robust risk management strategy that includes alternative suppliers, safety stock, and contingency plans can help mitigate the impact of such disruptions.
Technology Integration
Integrating new technology into existing systems can be a daunting task.
However, the long-term benefits far outweigh the initial challenges.
Investing in cutting-edge inventory management solutions and ensuring seamless integration can significantly enhance overall efficiency.
Conclusion
Inventory optimization is a multifaceted process requiring a blend of strategic planning, accurate forecasting, and efficient execution.
By understanding key concepts like EOQ, safety stock, and ABC analysis, and employing techniques like JIT inventory and automated systems, businesses can dramatically improve their inventory management.
Regular audits, employee training, and strong supplier relationships further bolster these efforts, helping companies navigate challenges and maintain optimal inventory levels.
With diligent application of these practices, businesses can enjoy reduced costs, improved cash flow, and enhanced customer satisfaction.
資料ダウンロード
QCD調達購買管理クラウド「newji」は、調達購買部門で必要なQCD管理全てを備えた、現場特化型兼クラウド型の今世紀最高の購買管理システムとなります。
ユーザー登録
調達購買業務の効率化だけでなく、システムを導入することで、コスト削減や製品・資材のステータス可視化のほか、属人化していた購買情報の共有化による内部不正防止や統制にも役立ちます。
NEWJI DX
製造業に特化したデジタルトランスフォーメーション(DX)の実現を目指す請負開発型のコンサルティングサービスです。AI、iPaaS、および先端の技術を駆使して、製造プロセスの効率化、業務効率化、チームワーク強化、コスト削減、品質向上を実現します。このサービスは、製造業の課題を深く理解し、それに対する最適なデジタルソリューションを提供することで、企業が持続的な成長とイノベーションを達成できるようサポートします。
オンライン講座
製造業、主に購買・調達部門にお勤めの方々に向けた情報を配信しております。
新任の方やベテランの方、管理職を対象とした幅広いコンテンツをご用意しております。
お問い合わせ
コストダウンが利益に直結する術だと理解していても、なかなか前に進めることができない状況。そんな時は、newjiのコストダウン自動化機能で大きく利益貢献しよう!
(Β版非公開)