- お役立ち記事
- The Importance of Inventory Management in Optimizing Procurement for SMEs
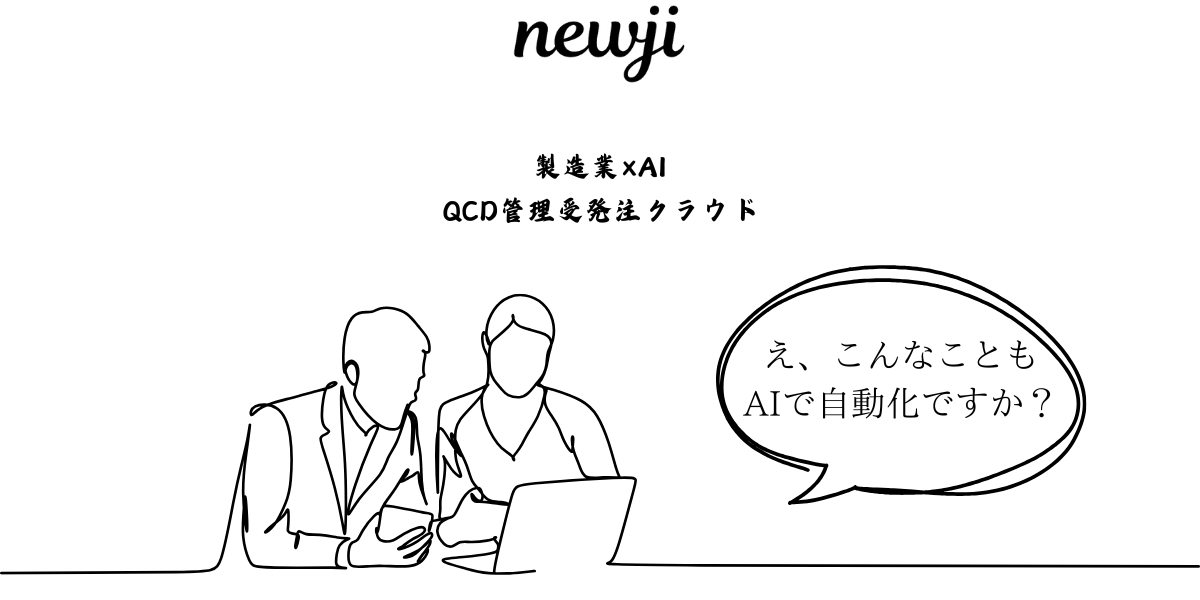
The Importance of Inventory Management in Optimizing Procurement for SMEs
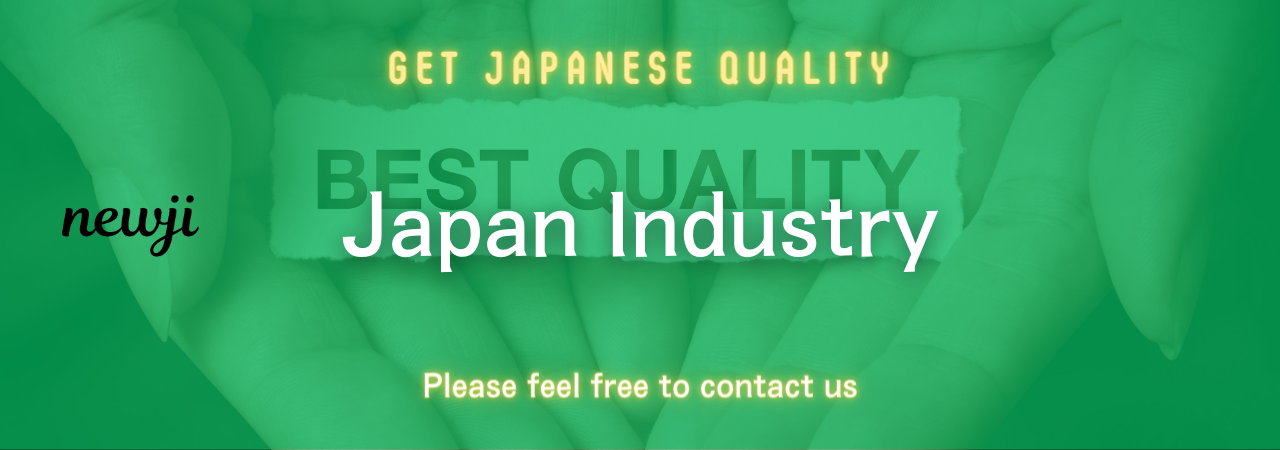
In today’s fast-paced business environment, managing inventory efficiently can make a substantial difference in the success of small and medium-sized enterprises (SMEs).
Effective inventory management is crucial in optimizing procurement processes and ensuring that businesses run smoothly.
目次
What is Inventory Management?
Inventory management is the process of overseeing the flow of goods from manufacturers to warehouses and from these facilities to points of sale.
It involves the coordination of various tasks such as ordering, storing, and utilizing a company’s inventory items.
For SMEs, effective inventory management means keeping the right balance of stock at all times to meet customer demand without unnecessary overspending or waste.
Why is Inventory Management Important for SMEs?
Good inventory management can significantly impact the efficiency and profitability of SMEs.
There are several reasons why it is particularly important:
Cost Control
By keeping track of inventory, businesses can avoid overstocking or understocking.
Both scenarios can lead to increased costs.
Overstocking ties up capital that could be used elsewhere, while understocking can result in lost sales and customer dissatisfaction.
Improved Cash Flow
Efficient inventory management helps to improve cash flow.
When you manage your inventory correctly, you only stock what you need, freeing up cash that can be used for other critical business operations or investments.
Better Customer Service
Maintaining optimal inventory levels ensures that customer needs are met promptly.
Consistently having the products customers want, when they want them, leads to better customer satisfaction and loyalty.
Enhanced Efficiency and Productivity
Accurate inventory management systems streamline procurement processes and reduce the time spent on manual inventory counts and order processing.
This leads to increased efficiency and productivity, allowing staff to focus on more strategic tasks.
Optimizing Procurement through Inventory Management
Procurement is the process of sourcing and acquiring the goods and services that a company needs to conduct its operations.
Optimizing procurement processes through efficient inventory management can lead to significant benefits for SMEs.
Demand Forecasting
One of the critical aspects of inventory management is accurate demand forecasting.
By analyzing sales data and market trends, businesses can predict future demand for products.
This helps in placing accurate orders, minimizing the risk of overstocking or stockouts.
Supplier Relationships
Effective inventory management involves building strong relationships with suppliers.
Reliable suppliers ensure timely delivery of goods, which helps maintain optimal inventory levels.
Additionally, good supplier relationships can lead to better pricing, discounts, and favorable payment terms.
Automated Reordering
Many modern inventory management systems come with automated reordering features.
These systems can monitor inventory levels in real-time and place orders automatically when stock levels reach a predefined threshold.
This ensures that the business never runs out of essential items and reduces the need for manual intervention.
Minimizing Lead Time
Another advantage of effective inventory management is the ability to minimize lead time.
Lead time is the period between placing an order and receiving the goods.
Efficient procurement processes help in reducing lead times, allowing businesses to respond quickly to customer demands.
Tools and Techniques for Effective Inventory Management
There are several tools and techniques that SMEs can use to manage their inventory effectively:
Inventory Management Software
Investing in good inventory management software can make a significant difference.
These programs offer features such as real-time tracking, automated reordering, and advanced reporting capabilities.
They help in maintaining accurate inventory records and making data-driven decisions.
Just-In-Time (JIT) Inventory
The JIT inventory system aims to reduce holding costs by receiving goods only as they are needed in the production process.
This technique minimizes inventory levels and reduces waste, but it requires precise demand forecasting and reliable suppliers.
ABC Analysis
ABC analysis is a technique that divides inventory items into three categories:
– Category A: Highly valuable items with low sales frequency.
– Category B: Moderately valuable items with moderate sales frequency.
– Category C: Lower value items with high sales frequency.
By focusing on managing Category A items more closely, businesses can optimize their inventory investments.
First-In, First-Out (FIFO)
The FIFO method ensures that older inventory items are sold before newer ones.
This technique is particularly useful for perishable goods or items with a limited shelf life, helping prevent obsolescence and reducing waste.
The Impact of Poor Inventory Management
Ineffective inventory management can have several negative consequences for SMEs:
Lost Sales
Stockouts can lead to lost sales opportunities and frustrated customers.
Consistently failing to meet customer demand can damage the business’s reputation and result in diminished customer loyalty.
Increased Costs
Overstocking introduces additional holding costs, such as storage fees, insurance, and potentially spoilage or obsolescence costs.
Poor inventory management can lead to an unnecessary increase in operational expenses, affecting the bottom line.
Operational Inefficiencies
Manual inventory tracking and ordering processes can be time-consuming and error-prone.
This leads to inefficiencies that can hinder overall operational performance and productivity.
Conclusion
For SMEs, effective inventory management is not just about keeping track of stock.
It is a strategic component that influences various aspects of the business, including procurement, customer satisfaction, and overall financial performance.
By adopting modern inventory management tools and techniques, SMEs can optimize their procurement processes, improve cash flow, and ensure customer satisfaction.
By prioritizing inventory management, SMEs position themselves for sustainable growth and long-term success.
Implementing best practices in inventory management not only streamlines operations but also provides a competitive edge in the market.
資料ダウンロード
QCD調達購買管理クラウド「newji」は、調達購買部門で必要なQCD管理全てを備えた、現場特化型兼クラウド型の今世紀最高の購買管理システムとなります。
ユーザー登録
調達購買業務の効率化だけでなく、システムを導入することで、コスト削減や製品・資材のステータス可視化のほか、属人化していた購買情報の共有化による内部不正防止や統制にも役立ちます。
NEWJI DX
製造業に特化したデジタルトランスフォーメーション(DX)の実現を目指す請負開発型のコンサルティングサービスです。AI、iPaaS、および先端の技術を駆使して、製造プロセスの効率化、業務効率化、チームワーク強化、コスト削減、品質向上を実現します。このサービスは、製造業の課題を深く理解し、それに対する最適なデジタルソリューションを提供することで、企業が持続的な成長とイノベーションを達成できるようサポートします。
オンライン講座
製造業、主に購買・調達部門にお勤めの方々に向けた情報を配信しております。
新任の方やベテランの方、管理職を対象とした幅広いコンテンツをご用意しております。
お問い合わせ
コストダウンが利益に直結する術だと理解していても、なかなか前に進めることができない状況。そんな時は、newjiのコストダウン自動化機能で大きく利益貢献しよう!
(Β版非公開)