- お役立ち記事
- Strengthening Risk Management in Purchasing for SMEs
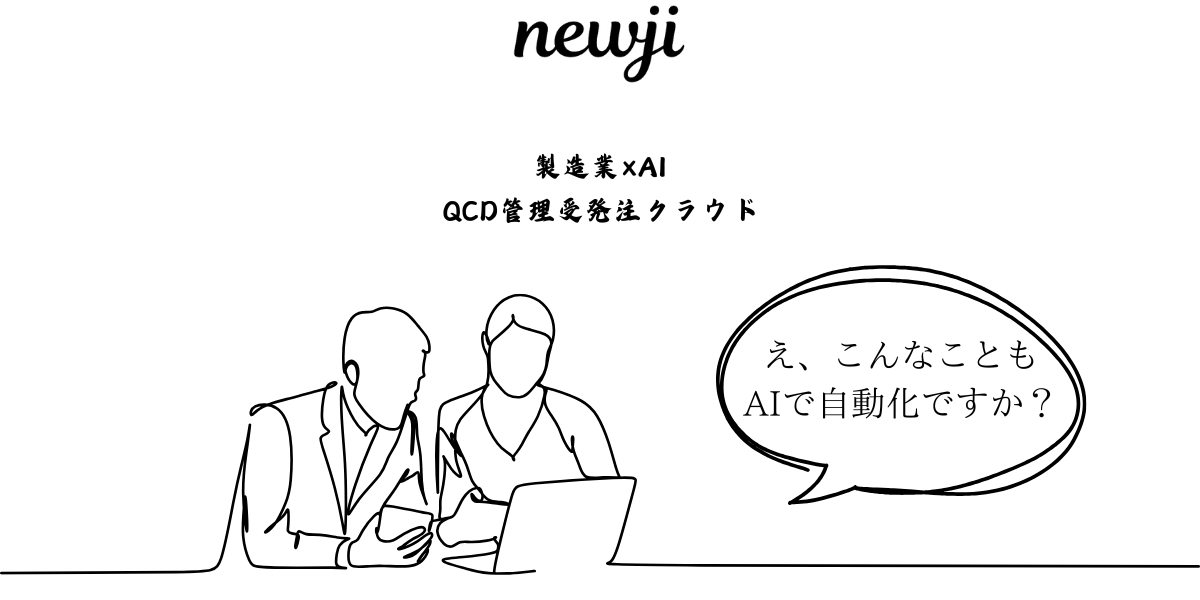
Strengthening Risk Management in Purchasing for SMEs
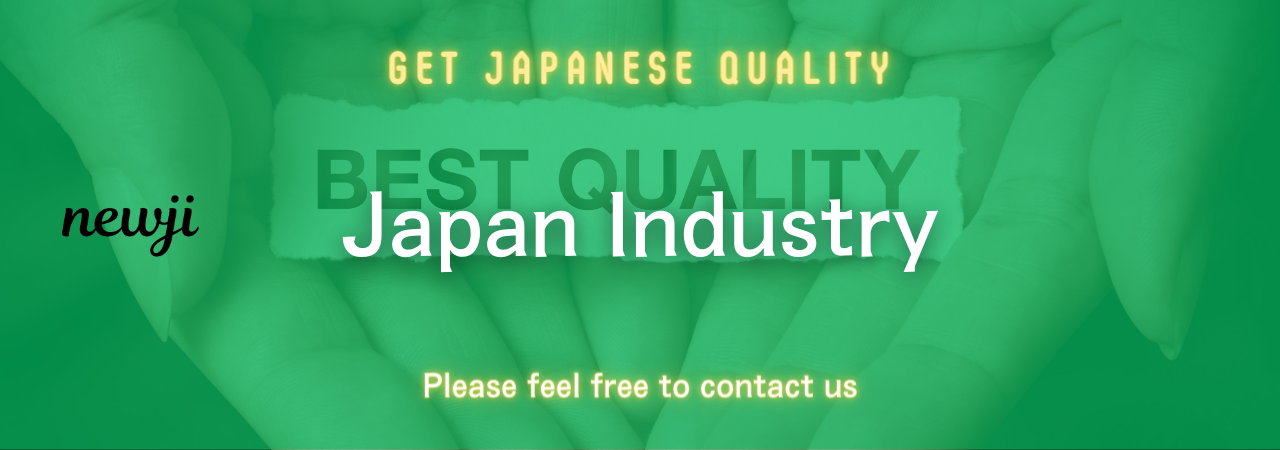
目次
Understanding Risk Management in Purchasing
Purchasing is a critical component for any company, especially for small and medium-sized enterprises (SMEs).
But, with every purchase comes an inherent level of risk.
Understanding risk management in purchasing can help SMEs navigate these challenges more effectively.
Risk management involves identifying, assessing, and prioritizing risks to minimize their potential impact.
In the context of purchasing, these risks can range from supplier reliability to changes in market conditions.
Identifying Risks in Purchasing
Before implementing any risk management strategy, it is vital to identify potential risks associated with purchasing.
Common risks include supplier uncertainty, lead-time variability, and quality concerns.
For SMEs, the impact of these risks can be significant due to limited resources.
Supplier risks can manifest if a supplier fails to deliver goods on time or at the agreed quality.
Lead-time variability can cause delays in production, affecting customer satisfaction.
Quality concerns may result in products that do not meet customer expectations, leading to returns and loss of reputation.
Supplier Risks
Supplier risks are among the most critical areas to focus on in purchasing.
The reliability and performance of your suppliers directly impact your operations.
For SMEs, having a single supplier dependency can be particularly risky.
Building long-term relationships with multiple suppliers can mitigate this risk.
Also, regularly evaluating suppliers’ performance through audits and feedback can help maintain consistent quality and reliability.
Market Risks
Market risks refer to the fluctuations in price and availability of goods in the market.
Economic changes, political instability, and natural disasters can all affect market conditions.
For SMEs, sudden price increases can significantly strain finances.
Effective market research, including trends and forecasts, can provide valuable insights.
Additionally, maintaining a buffer stock can protect against sudden supply disruptions.
Assessing the Impact of Risks
Once risks are identified, assessing their potential impact is crucial for effective risk management.
Quantifying the potential damage from each risk can help SMEs prioritize their focus.
For instance, supplier failure might be more detrimental compared to a slight market shift.
Risk assessment tools such as SWOT analysis (Strengths, Weaknesses, Opportunities, Threats) can be invaluable.
Another method is the FMEA (Failure Mode and Effects Analysis), which helps in understanding the severity, occurrence, and detection of risks.
Implementing Risk Mitigation Strategies
After assessing the risks, implementing strategies to mitigate their impact is the next step.
For SMEs, cost-effective measures are often necessary due to budget constraints.
Building Strong Supplier Relationships
Building strong, reliable relationships with suppliers is an effective way to manage supplier risks.
Regular communication, performance reviews, and mutual understanding can foster better cooperation.
Offering fair terms and timely payments can encourage suppliers to prioritize your business.
Additionally, having contracts that outline terms clearly can help in mitigating disputes.
Diversifying Supplier Base
Relying on a single supplier is risky for any business.
SMEs should aim to diversify their supplier base to ensure continuity in times of crisis.
Having multiple suppliers can reduce the impact of any single supplier’s failure.
Also, it offers competitive pricing and better negotiation power.
Adopting Technology
Technology can play a crucial role in risk management.
Adopting procurement software can streamline purchasing processes and improve efficiency.
These tools offer real-time tracking, automated order processing, and enhanced reporting capabilities.
They also facilitate better supplier evaluation and market trend analysis.
For SMEs, investing in technology could be a game-changer in managing purchasing risks effectively.
Continuous Monitoring and Improvement
Risk management is an ongoing process that requires continuous monitoring and improvement.
Regular reviews of your risk management strategies help identify areas of improvement.
Staying updated with market trends, economic conditions, and supplier performance is essential.
Encouraging a culture of risk awareness within the organization can also be beneficial.
Employees should be trained to recognize potential risks and contribute to mitigation efforts.
Conclusion
Strengthening risk management in purchasing is crucial for SMEs to ensure operational efficiency and profitability.
Understanding and identifying potential risks, assessing their impacts, and implementing effective mitigation strategies are essential steps.
Building strong supplier relationships, diversifying suppliers, and adopting technology can significantly reduce purchasing risks.
Continuous monitoring and improvement can help SMEs stay ahead of potential challenges.
By focusing on these areas, SMEs can enhance their purchasing processes and ultimately achieve better business outcomes.
資料ダウンロード
QCD調達購買管理クラウド「newji」は、調達購買部門で必要なQCD管理全てを備えた、現場特化型兼クラウド型の今世紀最高の購買管理システムとなります。
ユーザー登録
調達購買業務の効率化だけでなく、システムを導入することで、コスト削減や製品・資材のステータス可視化のほか、属人化していた購買情報の共有化による内部不正防止や統制にも役立ちます。
NEWJI DX
製造業に特化したデジタルトランスフォーメーション(DX)の実現を目指す請負開発型のコンサルティングサービスです。AI、iPaaS、および先端の技術を駆使して、製造プロセスの効率化、業務効率化、チームワーク強化、コスト削減、品質向上を実現します。このサービスは、製造業の課題を深く理解し、それに対する最適なデジタルソリューションを提供することで、企業が持続的な成長とイノベーションを達成できるようサポートします。
オンライン講座
製造業、主に購買・調達部門にお勤めの方々に向けた情報を配信しております。
新任の方やベテランの方、管理職を対象とした幅広いコンテンツをご用意しております。
お問い合わせ
コストダウンが利益に直結する術だと理解していても、なかなか前に進めることができない状況。そんな時は、newjiのコストダウン自動化機能で大きく利益貢献しよう!
(Β版非公開)