- お役立ち記事
- Revolutionizing Production: The Role of MG Net in Japanese Manufacturing Innovations
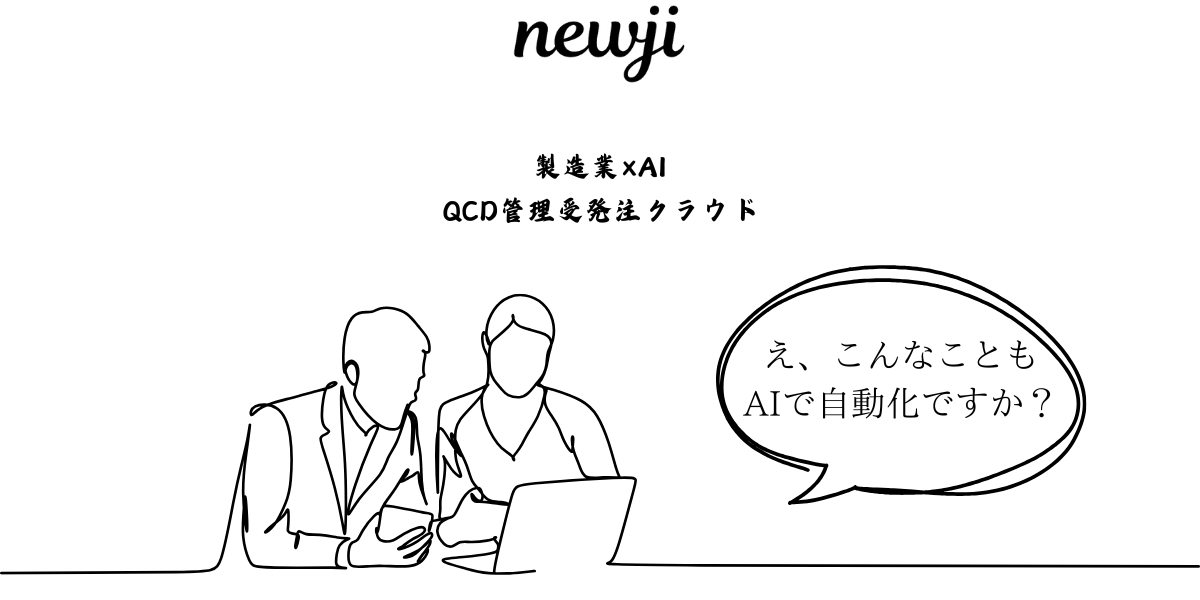
Revolutionizing Production: The Role of MG Net in Japanese Manufacturing Innovations
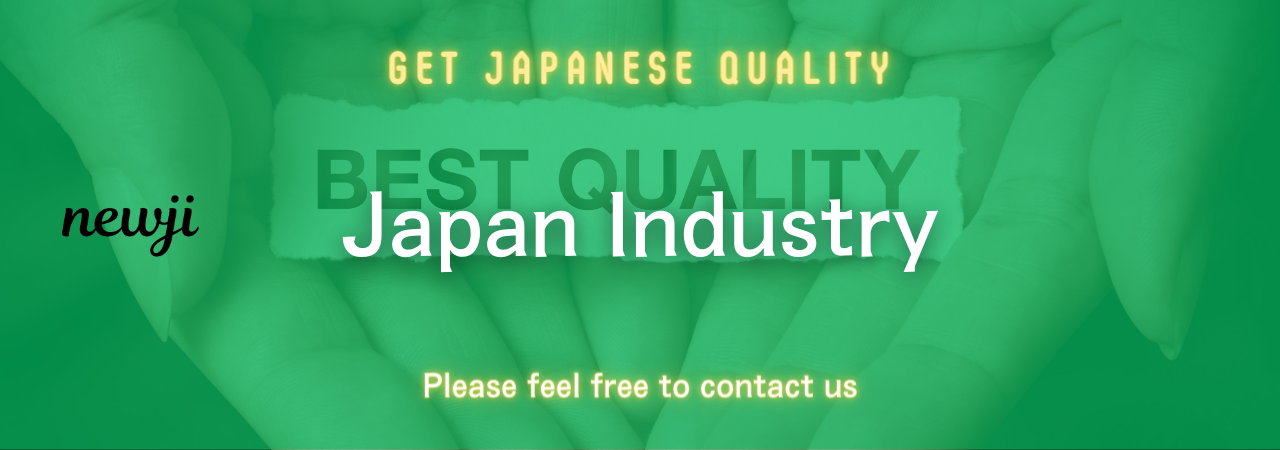
目次
Introduction
The Japanese manufacturing sector has long been a global leader in innovation, efficiency, and quality. With the advent of new technologies and methodologies, the industry continues to push the boundaries of what’s possible in production processes.
One such technological advancement is the MG Net, a revolutionary system designed to enhance various facets of manufacturing. This article delves into the role of MG Net in Japanese manufacturing, exploring its advantages, challenges, practical implementations, and implications for the future.
What is MG Net?
Definition and Background
MG Net, short for “Manufacturing Grid Network,” is an integrated system that leverages IoT (Internet of Things), AI (Artificial Intelligence), and Big Data to streamline manufacturing processes. Initially conceptualized in Japan, MG Net aims to connect different phases of production, from procurement to distribution, in a seamless, efficient, and real-time manner.
Core Components
The core components of MG Net include:
1. **IoT Devices**: These are sensors and actuators that collect and transmit data across the manufacturing floor.
2. **AI Algorithms**: Advanced algorithms that process the collected data, offering predictive analytics and automation.
3. **Big Data Analytics**: This involves analyzing large sets of data to derive actionable insights.
4. **Cloud Computing**: Provides the necessary infrastructure for data storage, processing, and accessibility.
Advantages of MG Net in Japanese Manufacturing
Enhanced Efficiency
MG Net significantly boosts production efficiency by ensuring that all components of the manufacturing process are interconnected and optimally synchronized. The real-time data flow helps identify bottlenecks and inefficiencies, leading to timely interventions and minimized downtime.
Improved Quality Control
Quality control is paramount in Japanese manufacturing. MG Net’s real-time monitoring allows for immediate identification of defects, ensuring that corrective measures are implemented swiftly. This reduces waste and enhances the overall quality of the final product.
Cost Reduction
By streamlining operations and reducing inefficiencies, MG Net helps in cutting down overall production costs. Real-time data analytics can identify areas where resources are being underutilized or wasted, allowing for better allocation and cost-saving strategies.
Sustainability
MG Net contributes to sustainability by optimizing resource usage and minimizing waste. It also supports predictive maintenance, thereby reducing the need for frequent replacements and repairs, which in turn lowers the environmental impact.
Disadvantages and Challenges
High Initial Investment
Implementing MG Net requires a substantial initial investment. This includes the cost of IoT devices, AI software, cloud infrastructure, and skilled personnel to manage and maintain the system. Small and medium-sized enterprises may find this financial hurdle challenging to overcome.
Data Security Concerns
With increased connectivity comes the risk of cyber-attacks. Ensuring the security of data is crucial, as any breach could lead to significant financial and reputational damage.
Complex Integration
Integrating MG Net into existing manufacturing processes can be complex and time-consuming. It requires a thorough understanding of both the legacy systems and the new technology, making it necessary to train staff and possibly hire new talent with specialized skills.
Resistance to Change
Human factors play a significant role in the adoption of new technologies. There may be resistance from employees who are accustomed to traditional methods and are wary of automation and digitalization.
Supplier Negotiation Techniques
Understanding Market Conditions
Before entering into negotiations with suppliers, it’s crucial to understand the current market conditions. Knowing the supply and demand dynamics, price trends, and competitive landscape can provide valuable leverage during negotiations.
Building Strong Relationships
Japanese business culture places a strong emphasis on relationships. Building trust and establishing long-term partnerships with suppliers can lead to more favorable terms and conditions. Regular communication and showing appreciation for their efforts can go a long way in strengthening these ties.
Focus on Total Cost of Ownership (TCO)
Rather than just focusing on the initial price, consider the total cost of ownership. This includes costs associated with maintenance, quality, and reliability. A higher upfront cost might be justified if it leads to lower operational expenses and higher quality in the long run.
Leverage Technology
Use technology to your advantage during negotiations. Real-time data from the MG Net system can provide insights into supplier performance, delivery timelines, and quality metrics. This information can be used to argue for better terms or to identify areas where the supplier needs to improve.
Market Conditions
Current Trends
The global manufacturing landscape is constantly evolving, influenced by factors such as technological advancements, geopolitical tensions, and economic conditions. In Japan, there is a growing emphasis on digital transformation and sustainability, driven by both government policies and market demands.
Impact of Global Supply Chain Disruptions
Recent global events, such as the COVID-19 pandemic, have highlighted the vulnerabilities in the supply chain. Japanese manufacturers are increasingly looking to diversify their supplier base and invest in technologies like MG Net to enhance supply chain resilience.
Regulatory Environment
Japan has stringent regulations when it comes to manufacturing and quality control. Staying compliant with these regulations is crucial for maintaining market credibility. MG Net can assist in ensuring that all processes adhere to the necessary standards.
Best Practices for Implementing MG Net
Conduct a Thorough Needs Assessment
Before implementing MG Net, conduct a thorough needs assessment to understand the specific requirements and challenges of your manufacturing process. Identify the key areas where MG Net can add value.
Phased Implementation
Implementing MG Net in phases can help manage the complexities and challenges associated with integration. Start with a pilot project in a specific area of the manufacturing process, evaluate its performance, and then gradually roll it out across other areas.
Invest in Training
Ensure that your staff is well-trained in using the new system. This includes not only technical training but also educating them about the benefits and potential challenges of MG Net. A well-informed team is critical for the successful implementation and utilization of the system.
Continuous Monitoring and Improvement
The implementation of MG Net is not a one-time activity. Continuous monitoring and improvement are essential to ensure that the system continues to deliver value. Regularly review performance metrics, gather feedback from staff, and make necessary adjustments.
Case Studies: Successful Implementations of MG Net in Japan
Automotive Manufacturing
One of the leading automotive manufacturers in Japan implemented MG Net to enhance its production efficiency and quality control. By integrating IoT sensors across its assembly line, the company was able to monitor real-time data, identify bottlenecks, and implement corrective actions swiftly. This resulted in a 20% increase in production efficiency and a significant reduction in defects.
Electronics Manufacturing
A Japanese electronics manufacturer leveraged MG Net to optimize its supply chain and production processes. By utilizing AI algorithms for predictive analytics, the company could forecast demand accurately and adjust its production schedules accordingly. This minimized inventory costs and ensured timely delivery of products, giving the company a competitive edge in the market.
The Future of MG Net in Japanese Manufacturing
Integration with Industry 4.0
MG Net is poised to play a crucial role in the broader context of Industry 4.0, which emphasizes the digital transformation of manufacturing processes. By integrating MG Net with other Industry 4.0 technologies such as robotics and 3D printing, Japanese manufacturers can achieve unprecedented levels of efficiency and innovation.
Expansion to Other Sectors
While MG Net has primarily been implemented in traditional manufacturing sectors such as automotive and electronics, its potential extends to other industries. Sectors such as pharmaceuticals, food and beverage, and textiles can also benefit from the real-time data analytics and automation capabilities of MG Net.
Global Adoption
The success of MG Net in Japan has garnered international attention, with manufacturers worldwide looking to adopt similar systems. As global supply chains become increasingly interconnected, the adoption of MG Net could facilitate more resilient and efficient production processes on a global scale.
Conclusion
MG Net represents a significant leap forward in the realm of manufacturing innovation. By leveraging the power of IoT, AI, and Big Data, it offers a comprehensive solution to the challenges faced by modern manufacturers.
While the initial investment and integration complexities present certain challenges, the long-term benefits in terms of efficiency, quality, and sustainability are undeniable.
Japanese manufacturers, known for their commitment to excellence, are at the forefront of this technological revolution. By adopting best practices, understanding market conditions, and building strong supplier relationships, they can fully realize the potential of MG Net.
As the manufacturing landscape continues to evolve, MG Net stands as a testament to the enduring spirit of innovation and the relentless pursuit of perfection that defines Japanese manufacturing.
資料ダウンロード
QCD調達購買管理クラウド「newji」は、調達購買部門で必要なQCD管理全てを備えた、現場特化型兼クラウド型の今世紀最高の購買管理システムとなります。
ユーザー登録
調達購買業務の効率化だけでなく、システムを導入することで、コスト削減や製品・資材のステータス可視化のほか、属人化していた購買情報の共有化による内部不正防止や統制にも役立ちます。
NEWJI DX
製造業に特化したデジタルトランスフォーメーション(DX)の実現を目指す請負開発型のコンサルティングサービスです。AI、iPaaS、および先端の技術を駆使して、製造プロセスの効率化、業務効率化、チームワーク強化、コスト削減、品質向上を実現します。このサービスは、製造業の課題を深く理解し、それに対する最適なデジタルソリューションを提供することで、企業が持続的な成長とイノベーションを達成できるようサポートします。
オンライン講座
製造業、主に購買・調達部門にお勤めの方々に向けた情報を配信しております。
新任の方やベテランの方、管理職を対象とした幅広いコンテンツをご用意しております。
お問い合わせ
コストダウンが利益に直結する術だと理解していても、なかなか前に進めることができない状況。そんな時は、newjiのコストダウン自動化機能で大きく利益貢献しよう!
(Β版非公開)