- お役立ち記事
- Manufacturing in the Age of Mass Customization: Building Flexible Production Systems
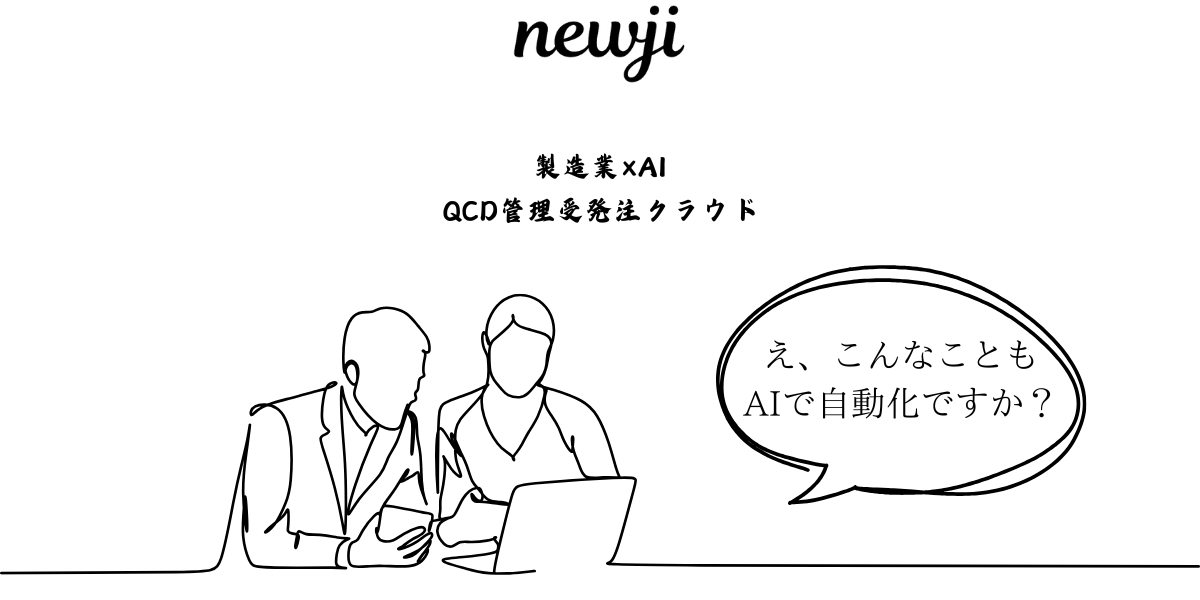
Manufacturing in the Age of Mass Customization: Building Flexible Production Systems
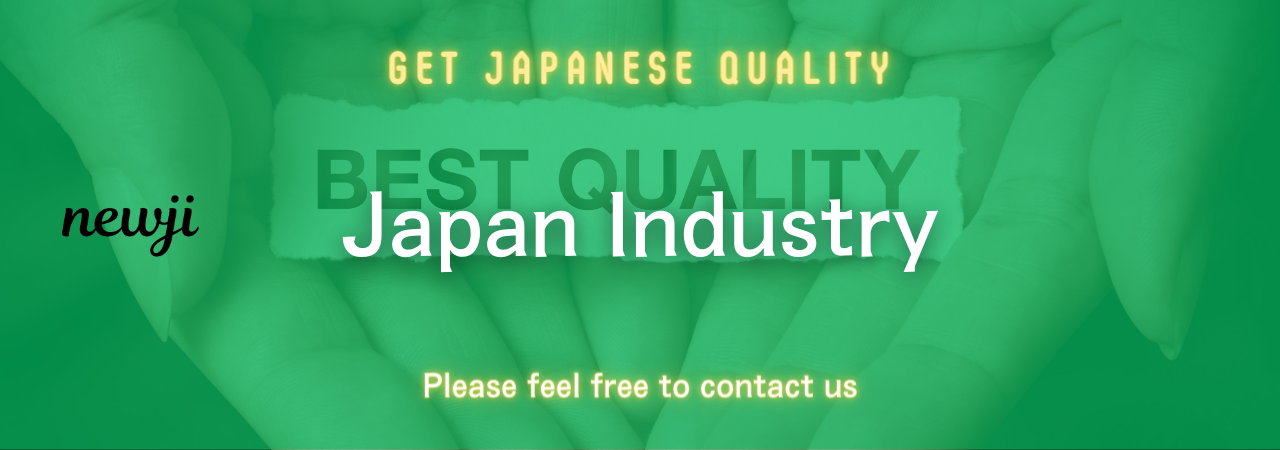
Manufacturing has undergone significant transformations over the years, but none have been as crucial as the shift to mass customization.
Mass customization allows manufacturers to produce goods that meet individual customers’ needs while maintaining the efficiency of mass production.
This evolution in manufacturing places a strong emphasis on building flexible production systems.
目次
What is Mass Customization?
Mass customization is a manufacturing process that combines the best aspects of mass production and custom-made products.
With traditional mass production, companies create large quantities of standardized items.
This method offers cost efficiency but lacks the ability to cater to specific customer preferences. Customization, on the other hand, tailors products to individual needs but is typically more expensive and time-consuming.
Mass customization bridges this gap.
It enables companies to create products that suit individual tastes and requirements while keeping costs in check.
To achieve this, manufacturers must adopt flexible production systems, allowing them to quickly adapt to different demands without significant downtime or expense.
The Importance of Flexible Production Systems
Flexible production systems are the backbone of mass customization.
They allow manufacturers to switch between making different products or product variations rapidly and without extensive retooling.
This flexibility is essential in markets where consumer preferences change frequently, and speed to market is crucial.
A flexible production system typically includes automated machinery, modular equipment, and advanced software that can easily be reprogrammed.
This setup minimizes the transition time between different production runs, ensuring that manufacturers can respond to customer orders promptly and efficiently.
Automation and Robotics
Automation and robotics play a pivotal role in creating flexible production systems.
Automated machinery and robotic arms can be programmed to handle various tasks and processes.
This adaptability is vital for producing customized products on a large scale.
For instance, a robotic arm in a flexible production system can switch from assembling one type of product to another with minimal downtime.
This capability allows manufacturers to meet diverse customer demands without needing multiple specialized machines for each product type.
Advanced Manufacturing Software
Advanced manufacturing software is another critical component of flexible production systems.
Software solutions like Manufacturing Execution Systems (MES) and Enterprise Resource Planning (ERP) software help manage production schedules, track inventory, and ensure quality control.
These software tools enable real-time monitoring and adjustment of production processes.
They provide manufacturers with the data and insights needed to make quick decisions, optimizing production efficiency and ensuring that customized products are delivered on time.
Benefits of Mass Customization
The shift to mass customization offers numerous benefits for both manufacturers and consumers.
For manufacturers, it provides a competitive edge by allowing them to cater to specific customer preferences.
This ability can lead to increased customer satisfaction and loyalty.
From a consumer standpoint, mass customization ensures that products meet their unique needs and tastes.
Whether it’s personalized apparel, customized electronics, or tailor-made furniture, consumers can enjoy products that feel uniquely theirs.
Increased Customer Satisfaction
In today’s market, customers expect more than just generic products.
They want items that reflect their personalities and preferences.
Mass customization allows manufacturers to meet these expectations, enhancing customer satisfaction.
When customers receive products that match their specifications, they are likely to be more content with their purchase.
This satisfaction can lead to repeat business, positive reviews, and word-of-mouth referrals—all of which benefit the manufacturer.
Cost Efficiency
While customization often comes at a premium, mass customization seeks to strike a balance between personalized products and cost efficiency.
Flexible production systems help achieve this balance by reducing the costs associated with switching between different production runs.
By automating processes and using modular equipment, manufacturers can produce customized items without incurring significant additional expenses.
This cost efficiency allows companies to offer customized products at competitive prices, making them accessible to a broader range of consumers.
Challenges and Solutions
While mass customization and flexible production systems offer many advantages, they are not without their challenges.
Implementing these systems can require substantial investment in technology, training, and infrastructure.
One of the main challenges is ensuring consistency and quality in customized products.
Since each item is tailored to individual specifications, maintaining uniformity can be difficult.
However, advanced manufacturing software and quality control measures can help mitigate this issue.
Another challenge is the initial cost of adopting automation and flexible production systems.
While these investments can be significant, they often pay off in the long run through increased efficiency, reduced waste, and improved customer satisfaction.
Implementing Advanced Quality Control Measures
To address the challenge of maintaining consistent quality, manufacturers must implement rigorous quality control measures.
This includes regular inspections, real-time monitoring, and the use of sensors to detect any deviations from the desired specifications.
Advanced quality control software can also play a role in identifying and addressing issues before they become significant problems.
By incorporating these measures, manufacturers can ensure that customized products meet high standards of quality and reliability.
Investing in Training and Development
Transitioning to a flexible production system requires skilled personnel who can operate and maintain the new technology.
Investing in employee training and development is crucial to successful implementation.
Training programs should cover the operation of automated machinery, the use of advanced software, and the principles of quality control.
A well-trained workforce ensures that the production system runs smoothly and efficiently, maximizing the benefits of mass customization.
The Future of Manufacturing
As technology continues to advance, the future of manufacturing will increasingly be driven by mass customization and flexible production systems.
Innovations such as 3D printing, the Internet of Things (IoT), and artificial intelligence are poised to revolutionize the industry even further.
3D printing, for example, offers unparalleled flexibility in producing complex and customized items.
Manufacturers can create intricate designs and prototypes quickly and cost-effectively, opening up new possibilities for customization.
The IoT enables seamless communication between machines and production lines, allowing for real-time adjustments and optimization.
Artificial intelligence can analyze vast amounts of data to identify trends and predict customer preferences, further enhancing the customization process.
In conclusion, manufacturing in the age of mass customization centers around building flexible production systems.
These systems harness the power of automation, robotics, and advanced software to create products that meet individual customers’ needs efficiently and cost-effectively.
By embracing mass customization, manufacturers can stay competitive in a rapidly evolving market while delivering high-quality, personalized products that satisfy customers and drive business success.
資料ダウンロード
QCD調達購買管理クラウド「newji」は、調達購買部門で必要なQCD管理全てを備えた、現場特化型兼クラウド型の今世紀最高の購買管理システムとなります。
ユーザー登録
調達購買業務の効率化だけでなく、システムを導入することで、コスト削減や製品・資材のステータス可視化のほか、属人化していた購買情報の共有化による内部不正防止や統制にも役立ちます。
NEWJI DX
製造業に特化したデジタルトランスフォーメーション(DX)の実現を目指す請負開発型のコンサルティングサービスです。AI、iPaaS、および先端の技術を駆使して、製造プロセスの効率化、業務効率化、チームワーク強化、コスト削減、品質向上を実現します。このサービスは、製造業の課題を深く理解し、それに対する最適なデジタルソリューションを提供することで、企業が持続的な成長とイノベーションを達成できるようサポートします。
オンライン講座
製造業、主に購買・調達部門にお勤めの方々に向けた情報を配信しております。
新任の方やベテランの方、管理職を対象とした幅広いコンテンツをご用意しております。
お問い合わせ
コストダウンが利益に直結する術だと理解していても、なかなか前に進めることができない状況。そんな時は、newjiのコストダウン自動化機能で大きく利益貢献しよう!
(Β版非公開)