- お役立ち記事
- The Manufacturing Process for Wooden Rocking Chairs and Strengthening Durability
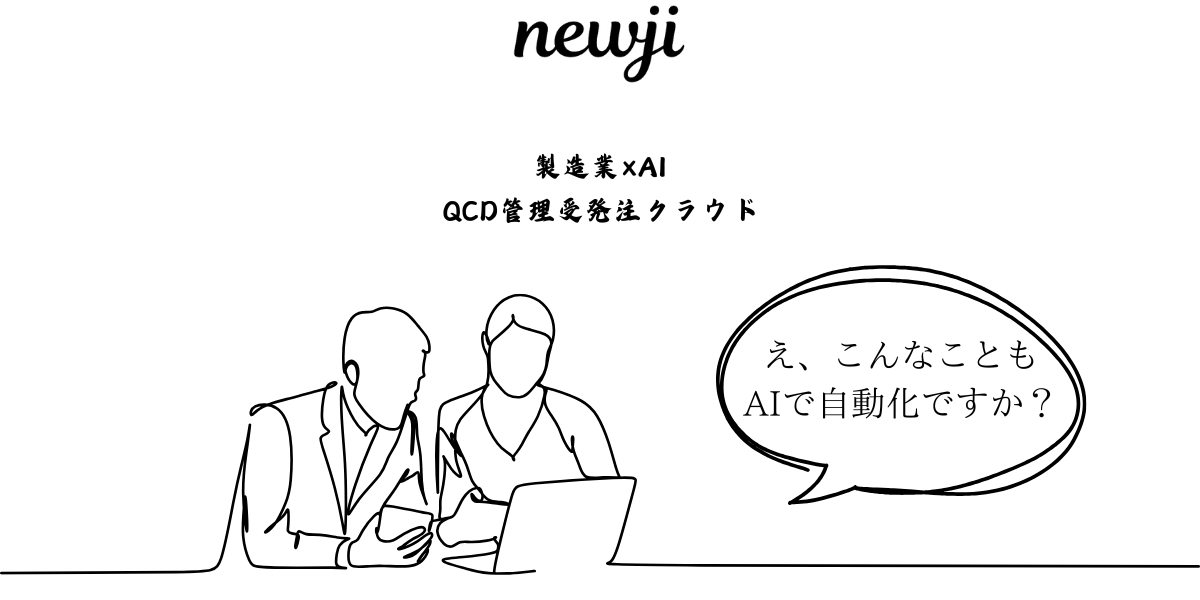
The Manufacturing Process for Wooden Rocking Chairs and Strengthening Durability
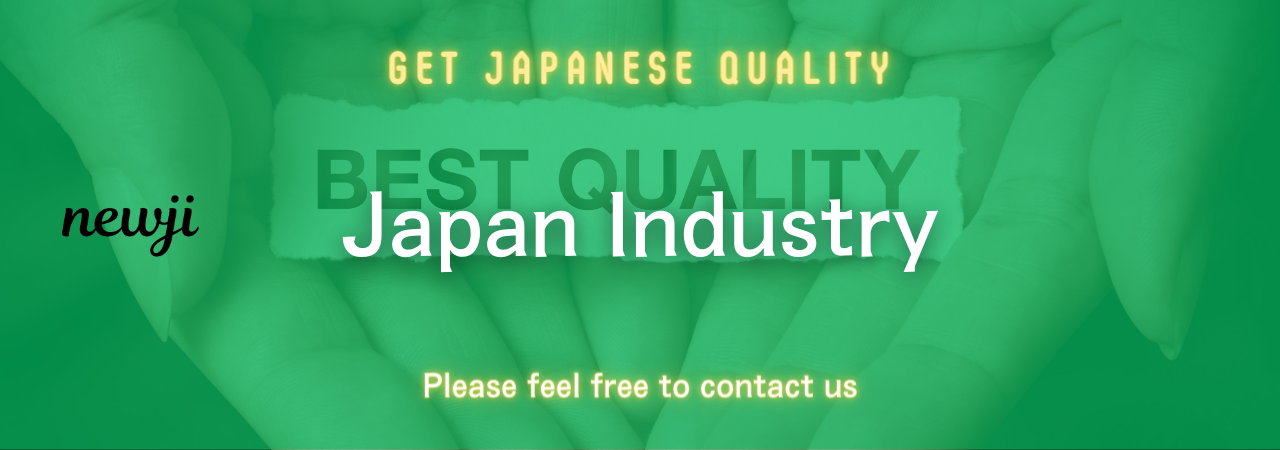
Wooden rocking chairs have been cherished for generations, providing both comfort and a timeless aesthetic.
Understanding the manufacturing process behind these beloved pieces is crucial to appreciating their craftsmanship and ensuring their durability.
This article will detail the process of creating wooden rocking chairs and explore various ways to enhance their longevity.
目次
Choosing the Right Wood
The first step in manufacturing a wooden rocking chair is selecting the right type of wood.
The wood chosen must balance aesthetics, durability, and workability.
Common wood types used include oak, maple, cherry, and walnut.
Oak
Oak is popular for its strength and durability.
Its distinct grain pattern adds a classic look to the rocking chair.
These qualities make oak rocking chairs both visually appealing and long-lasting.
Maple
Maple is known for its smooth grain and fine texture.
It is also quite durable, making it an excellent choice for rocking chairs.
The close-grain structure of maple means it holds up well to wear over time.
Cherry
Cherry wood has a rich, warm color that deepens with age.
It is also easy to work with, allowing intricate designs to be carved into the rocking chair.
While slightly softer than oak, cherry is still a durable option.
Walnut
Walnut is famed for its dark, luxurious color and straight grain.
It is strong yet easy to work with, making it another excellent choice for a quality rocking chair.
Shaping the Wood
Once the wood is selected, the next step involves cutting and shaping it to form the various parts of the rocking chair.
Cutting
Precision is key during the cutting phase.
Modern woodworking shops use advanced machinery like table saws and band saws to ensure each piece is cut to exact specifications.
Templates and jigs often guide these cuts to improve consistency.
Shaping
Shaping involves refining the cut pieces into the desired forms for the chair’s arms, seat, backrest, and rockers.
Hand tools like chisels and planes, along with powered sanders and routers, help smooth and shape the pieces.
Attention to detail is crucial here to ensure all parts fit together seamlessly.
Assembly
With all the parts cut and shaped, the next step is assembling the rocking chair.
Joinery
Joinery techniques are vital to the chair’s strength and durability.
Common methods include mortise and tenon joints, dowels, and screws.
These methods create strong connections between the different wood pieces.
Gluing and Clamping
Wood glue adds an extra layer of strength to the joints.
Once glued, the parts are clamped together to ensure a tight bond.
Clamp pressure is applied uniformly to avoid any gaps in the joints as the glue dries.
Adding the Rockers
Finally, the rockers are attached.
These curved pieces determine the chair’s rocking motion.
Careful alignment is crucial to ensure a smooth and balanced rock.
Finishing Touches
Once the chair is assembled, the finishing touches are applied to enhance its appearance and longevity.
Sanding
The assembled chair is sanded to remove any rough edges and create a smooth surface.
This step is essential for both comfort and aesthetics.
Various grades of sandpaper are used, starting with coarse and finishing with fine.
Staining and Sealing
Staining the wood enhances its natural color and adds a layer of protection.
Multiple coats may be applied to achieve the desired depth of color.
After staining, a sealant like polyurethane or varnish is applied to protect the wood from moisture, scratches, and wear.
Upholstery
Some rocking chairs feature upholstered seats and backrests for added comfort.
High-quality foam and durable fabrics are chosen to ensure comfort and longevity.
The upholstery is securely fastened to the wood frame to prevent any shifting or wear over time.
Strengthening Durability
Durability is a vital aspect of any wooden rocking chair.
Several additional steps can be taken to strengthen the chair’s longevity.
Quality Control
Quality control is essential in every step of the manufacturing process.
Inspecting each piece of wood for defects and ensuring precise cuts and tight joints can prevent future issues.
Regular quality checks during assembly and finishing also help maintain high standards.
Reinforcement
Additional reinforcement can be added to high-stress areas.
Metal brackets or additional wood supports can be used to strengthen joints and connections.
These reinforcements can significantly extend the chair’s lifespan, especially with heavy use.
Regular Maintenance
Routine maintenance is crucial for prolonging the life of a wooden rocking chair.
This includes regular cleaning, checking for loose joints, and applying wood conditioner or wax to maintain the finish.
Addressing minor issues promptly can prevent them from becoming significant problems.
Environmental Considerations
Sustainability is increasingly important in furniture manufacturing.
Selecting responsibly sourced wood and using eco-friendly finishes can contribute to the environmental sustainability of wooden rocking chairs.
Responsible Sourcing
Choosing wood from sustainably managed forests helps preserve ecosystems and reduce deforestation.
Certifications from organizations like the Forest Stewardship Council (FSC) can guide responsible wood purchasing decisions.
Eco-Friendly Finishes
Eco-friendly finishes, such as water-based stains and sealants, reduce the environmental impact of manufacturing.
These products emit fewer volatile organic compounds (VOCs), making them safer for both the environment and indoor air quality.
Crafting a wooden rocking chair is a detailed process that requires skill, precision, and careful material selection.
By understanding this process and implementing steps to enhance durability, manufacturers can create rocking chairs that are both beautiful and long-lasting.
Respect for quality craftsmanship and sustainable practices ensures these cherished pieces can be enjoyed for generations to come.
資料ダウンロード
QCD調達購買管理クラウド「newji」は、調達購買部門で必要なQCD管理全てを備えた、現場特化型兼クラウド型の今世紀最高の購買管理システムとなります。
ユーザー登録
調達購買業務の効率化だけでなく、システムを導入することで、コスト削減や製品・資材のステータス可視化のほか、属人化していた購買情報の共有化による内部不正防止や統制にも役立ちます。
NEWJI DX
製造業に特化したデジタルトランスフォーメーション(DX)の実現を目指す請負開発型のコンサルティングサービスです。AI、iPaaS、および先端の技術を駆使して、製造プロセスの効率化、業務効率化、チームワーク強化、コスト削減、品質向上を実現します。このサービスは、製造業の課題を深く理解し、それに対する最適なデジタルソリューションを提供することで、企業が持続的な成長とイノベーションを達成できるようサポートします。
オンライン講座
製造業、主に購買・調達部門にお勤めの方々に向けた情報を配信しております。
新任の方やベテランの方、管理職を対象とした幅広いコンテンツをご用意しております。
お問い合わせ
コストダウンが利益に直結する術だと理解していても、なかなか前に進めることができない状況。そんな時は、newjiのコストダウン自動化機能で大きく利益貢献しよう!
(Β版非公開)