- お役立ち記事
- Quality Control Secrets to Prevent Issues in Spinning
Quality Control Secrets to Prevent Issues in Spinning
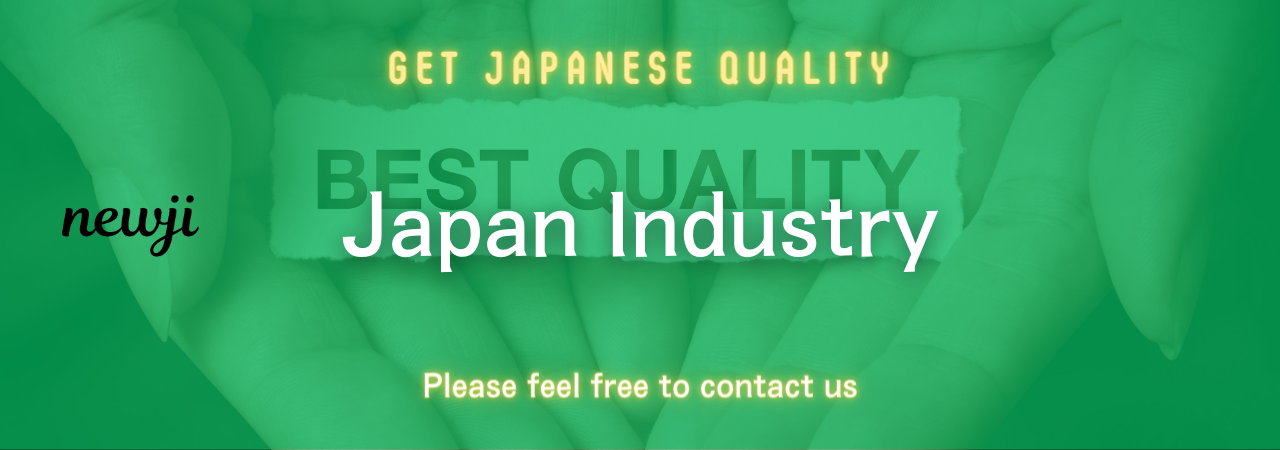
目次
Introduction to Quality Control in Spinning
Quality control is crucial in the spinning industry.
For a business involved in manufacturing yarn and fabrics, poor quality can lead to substantial financial losses.
Moreover, defects in spinning can cause downstream production issues, resulting in further complications.
Therefore, mastering quality control in spinning is essential.
In this article, we explore various quality control secrets to prevent issues in spinning.
Understanding Raw Material Quality
The first step in quality control begins with the raw materials used in spinning.
High-quality raw materials are fundamental for producing superior yarns.
Several factors, such as fiber length, strength, and cleanliness, must be scrutinized.
Conducting thorough inspections and tests on raw materials before they enter the production line can save a lot of trouble.
Visually checking for contaminants and using advanced instruments to measure fiber properties can help identify any deficiencies early.
Importance of Machine Maintenance
Machines play an integral role in the spinning process.
Without regular maintenance, even the best raw materials can fail to produce quality yarn.
Routine checks and servicing of equipment ensure that every part operates efficiently.
This includes proper lubrication, alignment, and calibration.
Scheduled maintenance not only prolongs the lifespan of the machinery but also maintains consistency in production.
Regular training for operators on machine handling can also contribute to reducing machine-related issues.
Calibration and Alignment
Calibration and alignment of spinning machinery are critical.
Inaccurate calibration can lead to uneven yarn thickness and other defects.
Furthermore, alignment issues can cause increased tension and breakage.
Regularly checking and adjusting settings according to manufacturer specifications can mitigate such problems.
Using modern technology to automate these processes can further enhance precision.
Monitoring Environmental Conditions
Environmental conditions, such as temperature, humidity, and dust levels, significantly impact the spinning process.
Spinning facilities should maintain optimal conditions to ensure yarn quality.
High humidity can cause fibers to clump together, while low humidity increases static electricity, making handling difficult.
Temperature fluctuations can also affect fiber properties.
Maintaining Optimal Humidity Levels
Maintaining optimal humidity levels is particularly important.
This can be achieved by using humidifiers and dehumidifiers.
Monitoring systems can alert staff when conditions fall outside the ideal range.
Proper air filtration systems can also control dust levels, preventing contamination of the fibers.
Implementing Standard Operating Procedures (SOPs)
Standard Operating Procedures (SOPs) are standardized guidelines for performing tasks.
Implementing SOPs ensures that all employees follow the same processes, reducing variability and mistakes.
SOPs should be detailed, covering every aspect of the spinning process, including raw material inspection, machine operation, and quality checks.
Regularly reviewing and updating SOPs ensures they remain relevant and incorporate the latest best practices.
Training and Development
The expertise of the workforce significantly impacts product quality.
Continuous training and development programs help employees stay updated with the latest techniques and technologies.
Workers should be trained not only in operating machinery but also in recognizing defects and understanding quality standards.
Effective training programs incorporate practical hands-on sessions and regular assessments to gauge competency.
Knowledge Sharing
Encouraging a culture of knowledge sharing within the organization can also drive quality improvements.
Experienced staff can mentor newer employees, sharing insights and effective practices.
This ensures that the collective knowledge within the organization grows, leading to better overall quality.
Regular Quality Inspections
Regular quality inspections at various stages of the spinning process are critical.
Inspectors should evaluate the yarn during and after production to detect any deviations from quality standards.
Utilizing advanced testing equipment can provide precise measurements of yarn properties such as tensile strength, twist per inch, and moisture content.
Recording and analyzing inspection data helps in identifying recurring issues and determining their root causes.
In-process Checks
In-process checks are carried out while the production is ongoing.
These checks help in catching defects early and taking corrective actions immediately.
Implementing real-time monitoring systems can provide alerts when parameters exceed predefined limits.
Embracing Technology and Automation
Technology and automation play a pivotal role in modern quality control systems.
Adopting advanced software and machinery can significantly enhance precision and efficiency.
Automated systems can monitor various parameters 24/7, eliminate human error, and ensure consistent quality.
For example, spinning mills can use computerized control systems to automate the adjustment of tension and speed in real-time.
Data Analytics
Leveraging data analytics can offer valuable insights.
By analyzing historical production data, mills can identify patterns and predict potential issues before they arise.
Advanced data analytics tools can help in making informed decisions and optimizing the entire production process.
Customer Feedback
While internal quality control measures are essential, customer feedback provides an external perspective on product quality.
Listening to and acting on customer feedback can help in refining the quality control processes.
Surveys, reviews, and direct communication with customers can reveal insights that might not be visible from within the production environment.
Incorporating this feedback into continuous improvement strategies ensures that the final product meets customer expectations.
Conclusion
In conclusion, mastering quality control in spinning involves a comprehensive approach.
From careful selection of raw materials to advanced technological solutions, each step plays a crucial role.
Regular machine maintenance, optimal environmental conditions, stringent SOPs, continuous training, regular inspections, and customer feedback are vital components of an effective quality control system.
By integrating these quality control secrets into daily operations, spinning mills can prevent issues, ensure superior product quality, and maintain a competitive edge.
資料ダウンロード
QCD調達購買管理クラウド「newji」は、調達購買部門で必要なQCD管理全てを備えた、現場特化型兼クラウド型の今世紀最高の購買管理システムとなります。
ユーザー登録
調達購買業務の効率化だけでなく、システムを導入することで、コスト削減や製品・資材のステータス可視化のほか、属人化していた購買情報の共有化による内部不正防止や統制にも役立ちます。
NEWJI DX
製造業に特化したデジタルトランスフォーメーション(DX)の実現を目指す請負開発型のコンサルティングサービスです。AI、iPaaS、および先端の技術を駆使して、製造プロセスの効率化、業務効率化、チームワーク強化、コスト削減、品質向上を実現します。このサービスは、製造業の課題を深く理解し、それに対する最適なデジタルソリューションを提供することで、企業が持続的な成長とイノベーションを達成できるようサポートします。
オンライン講座
製造業、主に購買・調達部門にお勤めの方々に向けた情報を配信しております。
新任の方やベテランの方、管理職を対象とした幅広いコンテンツをご用意しております。
お問い合わせ
コストダウンが利益に直結する術だと理解していても、なかなか前に進めることができない状況。そんな時は、newjiのコストダウン自動化機能で大きく利益貢献しよう!
(Β版非公開)